刀具耐用度与切削用量的关系
刀具磨损到一定限度就不在继续使用,这个磨损限度称为磨钝标准。国际标准ISO统一规定以后带面上测定的磨损带宽度VB作为刀具磨损钝标准。在生产实际中,为可更方便、快速、准确地判断刀具的磨损情况,一般是以刀具耐用度来间接地反映刀具的磨钝标准。
刃磨后的刀具自开始切削直到磨损量达到磨钝标准所经历的总切削时间称为刀具耐用度,以T表示。刀具耐用度与刀具重磨次数的乘积就是刀具寿命,即一把新刀具从开始投入使用直到报废为止的总切削时间。
切削用量对刀具耐用度的影响十分显著。目前刀具磨损耐用度与切削用量之间的数学关系式还只能用实验的方法得到:
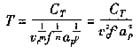
(2-1)
式中CT—耐用度系数;
M、n、p—指数。指数M、n、p随切削条件而变,而且0<M<n<p。这表明切削速度对刀具耐用度影响最大,进给量次之,切削深度影响最小。这与二者对切削温度的影响顺序一致,同时也说明切削温度是影响刀具耐用度的主要因素。
由式(2-1)可得
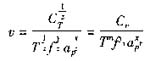
(2-2)
式中的系数Cυ及指数m、yυ、xυ、亦随切削条件而变。用该式可以计算出在指定的f、ap、与T的情况下所允许的切削速度。
刀具耐用度的确定原则
确定刀具合理耐用度的方法有三种:第一种方法是根据单工件时最小的原则来制定耐用度,称为最高生产率耐用度Tp:第二种反复法是根据每个工件工序成本最低原则来制定耐用度,称为最低成本耐用度Tc:第三种方法是根据单位时间内获得的盈利最大来制定耐用度,称为最大利润耐用度Tpr。
分析可知,这三种耐用度之间存在如下关系,即TP<TPR<TC。生产中一般多采用最低成本耐用度,只有当生产任务紧迫,或生产中出现不平衡的薄弱环节时,才选用最高生产率耐用度。
实际确定刀具耐用度时通常应考虑如下因素:
1)对于制造、刃磨比较简单,成本不高的刀具,例如车刀、钻头等,耐用度可定低一点,反之则耐用度应选高一点,如铣刀、拉刀及齿轮刀具。
2)对于装刀、换刀和调刀比较复杂的多刀机床、组合机床与自动化加工刀具,耐用度应取得高一些。机夹可转位车到和陶瓷刀具,其换刀时间短,耐用度可选得低些。
3)对不满足生产节拍的关键工序,为使车间生产达到平衡,该工序的耐用度应选得低一些。当某工序单位时间内所分担到的全厂开支较大时,刀具耐用度也应选低些。
4)大件精加工时,为避免在加工同一表面时中途换刀,耐用度应规定得高一些,至少应该完成一次走刀。
5) 生产线上的刀具耐用度应规定为一个班或二个班,以便能在换班时换刀。
表2-10列举了常用刀具的合理耐用度数值,可供选用时参考。
刀具类型 |
耐用度参考值 |
高速钢车刀、刨刀、镗刀
硬质合金可转位车刀、陶瓷刀具
硬质合金焊接车刀
硬质合金端铣刀
高速钢钻头
加工有色金属的金钢石车刀
加工淬火钢的立方氧化棚车刀
仿形车刀
多轴钻床上高速钢钻头
多轴铣床上硬质合金端铣刀
齿轮刀具
数控机床加工用刀具 |
30~60
15~45
15~60
120~180
80~120
600~1200
120~150
120~180
200~300
400~800
200~300
按班次安排 |
表2-10 常用刀具合理耐用参考数值