加工误差的分类
各种加工误差按其在一批工件中出现规律的不同可分为:
(1)系统误差,在顺序加工一批工件中,其加工误差的大小和方向都保持不变,或者按一定规律变化,统称为系统误差。前者称常值系统误差,后者称变值系统误差。
(2)随机误差,在顺序加工一批工件中,其加工误差的大小和方向的变化是属于随机性的,称为随机误差。
造成各类加工误差的原始误差见表3-5。
2. 加工误差的分析计算法
3. 该法适用于分析计算各系统误差对加工精度的影响。分析计算时可按如下步骤进行:
1)查明对某项加工误差有影响的各原始误差。
2)通过分析计算或测试、实验、建立加工误差与每一原始误差间的数学关系试。
3)测量或计算出各原始误差的数值,代入数学关系试,计算出各单项加工误差。
4)将各单项加工误差代数相加即得总加工误差。
3、加工误差的统计分析法
该法仅适用于采用调整法加工的成批、大量生产。在机械加工中,经常采用的统计分析法主要有分布 图分析法和点图(x-R图)分析法两种。
系统误差 |
随机误差 |
常值系统误差 |
变值系统误差 |
1) 原理误差
2) 工艺系统的调整误差(对一次调整而言)
3) 夹紧误差(对于机动夹紧
4) 测量误差(又量仪制造、对零不准、设计原理、磨损等产生)
5) 夹具的制造误差与磨损
6) 刀具的制造误差
7) 机床的制造、安装误差及磨损
8) 工艺系统受力变形(加工余量、材料硬度均匀时)
9) 工艺系统热变形(系统达到热平衡状态后 |
1) 刀具的尺寸磨损(砂轮、车刀、端铣刀、单刃镗刀等)
2) 工艺系统热变形(系统大大派热平衡状态前)
3) 多工位机床回转工作台的分度误差和其上夹具的安装误差 |
1) 工件定位误差
2) 夹紧误差(对于手动夹紧)
3) 测量误差(由量仪传动链间隙测量条件不稳定、读数不准等造成)
4) 工艺系统的调整误差(多台机床加工同批工件、一台机床多次调整加工大批工件)
5) 工艺系统受力变形(加工余量、材质硬度不均匀时)
6) 残余应力引起变形 |
(2) 分布图分析法
1)分布图的绘制步骤
a采集数据,成批加工某种零件,随机抽取数量为n的零件进行测量。抽取的这批零件称为样本,n称为样本容量,通常取n=50~200件。
表3-5 早成各类加工误差的原始误差
B确定分组数k、组距d、各组组界和组中值 分组数k应根据样本容量n来选取(见表3-6)
表3-6 分组数k的选取
n |
25~40 |
40~60 |
60~100 |
100 |
100~160 |
160~250 |
k |
6 |
7 |
8 |
10 |
11 |
12 |
组距为
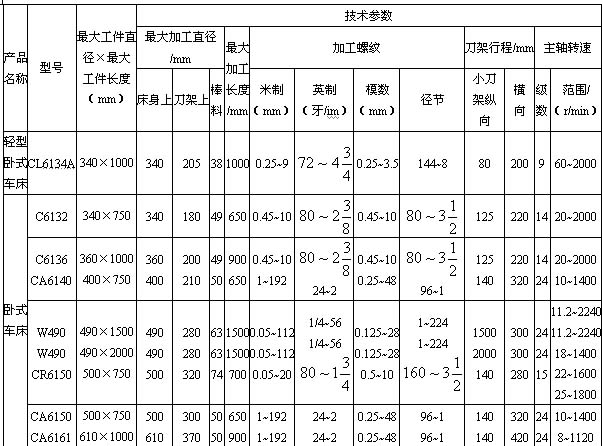
式中R—样本尺寸的最大值Xmax与在小值Xmin之差,称为极差,即R=Xmax--Xmin.
表2组组界为Xmin+(j-1)d± (j=1.2.3……k)
各组组中值为
Xmin+(j-1)d
c.以工件尺寸(组中值)为横坐标,以频数(同一尺寸组中零件的数量)m为纵坐标作(频数)分布图
d在分布图上标出该工序的公差带位置。
e.计算样本的算术平均值 和标准差s。
式中Xi—工件尺寸。
2)分布图分析法的应用
a. 判别加工误差性质,如果分布曲线形状与正态分布曲线基本相符,说明加工过程中没有变值系统误差(或影响很小),此时可进一步根据样本算术平均值 是否与公差带中心重合老判断是否存在常值系统误差(不重合则表明存在常值系统误差);如分布图曲线形状与正态分布曲线有较大出入,则可根据分布图曲线形状初步判断变值系统误差的性质;
b. 计算工序能力系数CP(CP= ,T为零件公差)如CP>1,说明该工序能力足够,
但加工中是否会出废品,还要看工艺系统调整是否正确;如CP<1,那么不论怎样调整,不合格品总是不可避免,此时应采取精化机床、提高毛坯制造精度或改用更精密的加工方法等措施来减少随机误差。
分布图分析法可看出各种随机因素对加工精度的综合影响;可把常值系统误差与随机误差区别开来,确知它的大小和方向,分布图分析法的不足在于,没有考虑一批工件加工的先后顺序,战不能反映误差变化的趋势,难以区别变值系统误差与随机误差的影响;必须等到一批工件加工完毕后才能绘制分布图,因此不能在加工过程中及时提供控制精度的信息。
(3)点图(x—R图)分析法
1)—R图的绘制步骤
a.在一批工件的加工过程中,每隔一定时间抽取容量n=2~10件的一个小样本,并计算出小样本的算术平均值 和极差Ri。经过若干时间后就可德到k个小样本(常取k=25)。
b.以小样本的组序号为横坐标,小样本的算术平均值 和极差R为纵坐标,分别作出 点图和R点图。
C.在 点图和R点图上作出中线和上、下、控制线:
式中 A2、D1、D2—常数,可由表3-7查得。
2) —R图的作用 在一定程度上代表了瞬时的分散中心,故 点图主要反映系统误差及其变化趋势;R在一定程度上代表了瞬时的尺寸分散范围,故R点图可反映出随机误差及其变化趋势,两种点图必须结合起来应用,根据图中点的分布情况可判别工艺过程是否稳定(波动是否属于正常),判别的标志见表3-8。
表3-7 A2、D1、D2
N件 |
A2 |
D1 |
D2 |
4 |
0.73 |
2.28 |
0 |
5 |
0.58 |
2.11 |
0 |
6 |
0.48 |
2.00 |
0 |
表3-8 正常波动与异常波动标志
正常波动 |
异常波动 |
1) 没有点子超出控制线
2) 大部分点子在中线上下波动,小部分在控制线附近
3) 点子分布没有明显的规律性 |
1) 有点子超出控制线
2) 点子密集在中线上下附近
3) 点子密集在控制线附近
4) 连续7个点以上出现在中线一侧
5) 连续11点中有10点出现在中线一侧
6) 连续14点中有12点以上出现在中线一侧
7) 连续17点中有14点以上出现在中线一侧
8) 连续20点中有16点以上出现在中线一侧
9) 电子有上升或下降倾向
10) 点子呈周期性波动 |