一、直接减少误差法
这种方法是生产中应用较广的一种基本方法。它是在查明影响加工精度的主要原始误差因素后,设法对其直接进行消除或减少。
例如
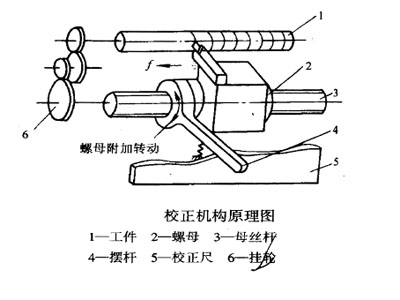
细长轴的车削,由于受力和热的影响,使工件产生弯曲变形,采用“大走刀反向切削法”再辅之以弹簧后顶尖,可以消除轴向切削力和受热伸长引起的弯曲变形。
又如薄片工件两端而的磨削,可先采用环氧树脂粘强剂或厚没脂将薄片工件在自由状态下粘结到一块平板上,平板连同工件一起放到磁力吸盘上,磨平工件的上端面,再将工件从平板上取下来,以上端面为基准磨平另一端面。这样,就可以消除薄片的夹紧变形,增强片纲度,从而解决两端面磨削的平行度问题。
二、误差补偿法
这种方法就是人为地造出一种新的原始误差,去补偿或抵消原来工艺系统中固有的原始误差,从而达到减少加工误差,提高加工精度的目的。
例如图精密丝杆车床就采用校正尺5来螺母2得到一个附加运动去补偿母丝杆3的螺距误差。显然,此例若仅靠提高传动链中各个远件的制造的精度是难以达到母丝杆传动要求的。
又如数控机床上的滚珠丝杆,制造时,有意地将丝杆累距比标准值磨得小一些,装配时预加拉伸力使丝杆螺距拉长至标准螺距,补偿了制造误差,且同时产生了压应力。工作时,丝杆受热晒台恰 好抵消了存在于丝杆内的压应力而保持了标准螺距,从而消除了热变形引起的原始误差。
三、误差分组法
在生产中会遇到这种情况:本工序的加工精度是稳定的,工艺能力也足够,但毛坯或上工序加工的半成品粗度发生了变化(精度太低),引起定位误差或复映误差过大,不能保证工序精度,如果要求的的提高毛坯精度或上工序加工精度,往往是不经济的。这时可采用误差分组示,把毛坯(或半成品)的尺寸按误差大小分为 n组,每组毛坯的误差就缩小为原来的1/n,然后按各组尺寸分别调整刀具与工件的相对位置或调整定位元件,就可大大缩小整批工件的尺寸分布范围。这种方法比起直接提高本工序的加工精度要简便易行一些。