提高磨效率的途径有两条: 是缩短辅助时间:如自动装卸工件、自动测量及数字显示尺寸、砂轮自动修整及补偿,采用新的磨料提高砂轮的耐用度 以减少修整次数;二是改变磨削用量以及增大磨削面积,例如高速磨削、强力磨削、恒压力磨削、宽砂轮磨削及多片砂轮磨削等。以下是改变磨削用量以及增大磨削面积的方法。
1、 高速磨削指砂轮线速度高于45m/s的磨削加工。它是提高磨削和产率和加质量的重要途径之一。其特点是:
1) 生产率高,砂轮子速度提高后,单位时间进入磨削区的磨粒数成比例地增加,如果还保持每颗磨粒切屑厚度与普通磨削相同,则时给量可以成比例加大,磨削时间相应地缩短。
2) 提高砂轮耐用度和使用寿命,砂轮速度提高后,若进给仍通磨削相同,则每颗磨粒切去的切屑厚度减速小,每颗磨粒承受的切削负荷下降,磨粒切削能力相对提高,每次修整后砂轮可以磨去更多的金属。
3) 能减少工件表面粗糙度值,提高加工精度。因为每颗磨粒切削厚度变小,表面切痕深度浅,表面粗糙度值小,另外作用在工件上的向磨削力也相应减小,所以又可提高加工精度。
应当指出,高速磨削对砂轮和机床有如下特殊要求:
1) 必须注意提高砂轮的强度,按切削速度规范选用砂轮,以免砂轮因离心力而破裂。
2) 砂轮主轴的轴承间隙适当加大,冷测为0.04-0.05mm,热态间隙为0.03mm左右。砂轮 主轴润滑油采用粘度小的油
3) 砂轮电动机功率应提高1.5-3倍,防止振动,高速旋转部件需经仔细平衡,机床静刚度和动刚度要好。
4) 砂轮的防护罩就加厚,开口角度减少,以确保安全。
5) 改善切削液供给方式。高速磨削时,磨削温度极高,面砂轮周围高速回转形成一股强大的气流,切削液不易注入磨削区,为避免工件表面烧伤,应增加切削液的流量和压力,并采用特殊喷嘴,如图1所示,另外还可采用多孔性砂轮,冷却液不是直执着注入磨削区,而是从砂轮内部在离心力作用下送入磨削区,如图2
2、 强力磨削
强力磨削就是以大的磨削度和较小的进给量进行磨削。常规磨削时磨削深度小于0.02mm,而进给量极大为0.05-5m/s,强力磨削与此相反,采用极大的切深,而进给量极小为0.002-0.005m/s。采用强力磨削加工钢制工件时金属切除率达3kg/min,磨铸铁时达405-5kg/min,可直接从毛坯或实体材料上磨出加工表面,适用于磨削各种成形表面沟槽,对耐热合金等难加工材料与淬硬金属的成形加工特别合适它可代替车削、铣削,且效率比车削铣削高,可节给特殊高速钢制造的复杂的成形刀具。强力磨削有一系列特点,但对砂轮及机床也提出了多主面的要求。
3、 宽砂轮和多片砂轮磨削
宽砂轮与多片砂轮磨削,都是增加砂轮宽度的磨削方法,适用于加工阶梯轴、曲轴、凸轮轴、螺纹、锥等工件。图3a、2b分别表示其加工方法。
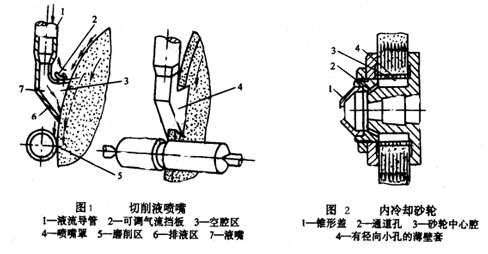
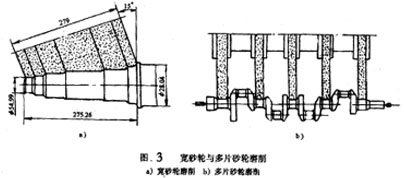