1. 加工表面层的冷作硬化
(1)加工硬化产生的原因,机械加工后,工件已加工表面表层金属的硬度常常高于基体材料的硬度,这一现象称为加工硬化。
加工硬化通常以硬化层深度hd及硬化程度N表示,hd是已加工表面至未硬化处的垂直距离,单位为微米;N是已加工表面显微硬度的增加值对原始显微硬度H0比值的百分数,即
式中H—以加工表面的显微硬度(GPa)。
一般樱花层深度hd可达几十到几百微米,而樱花程度N可达120%~200%。
切削和磨削过程中,由于切削力的作用,工件表层金属产生了很大的塑性变形,使金属的晶格扭曲,晶力拉长、破碎、并阻碍金属的进一步变形,使材料强化,硬度提高;同时、切削(磨削)温度将使材料弱化,更高的温度将引起相变。已加工表面的硬度变化就是这种强化、弱化和相变作用的综合结果。当塑性变形引起的强化起主导作用时,已加工表面就硬化;当切削温度引起的弱化去主导作用时,已加工表面就软化;当相变起主导作用时,则由相变的具体情况而定,例如在磨削淬火钢时,如果发生退火,则表面硬度降低,但在充分冷却的条件下,却可能引起二次淬火而使表面硬度提高。
(2)响加工硬化的因素
1)刀具方面,刀具的前角越大,切削层金属的塑性变形越小,故硬化层深度hd越小。
切削刃钝圆半径rn越大,已加工表面在形成过程中受挤压的程度越大,故加工硬化也越大(见图3-3)
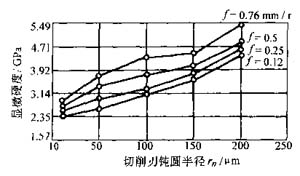
图3-3 切削刃钝圆半径rn对加工硬化的影响
工件:45钢
随着刀具后刀面磨损量VB的增加,后刀面与加工表面的摩擦随之增大,从而加工硬化层深度亦增大。
2)工件方面,工件材料的塑性越大,强化指数越大,熔点越高,则硬化越严重。对于碳素结构钢,含碳量越少,则塑性越大,硬化越严重。有色金属由于熔点较低,容易弱化,故加工硬化比钢小得多。
3) 切削条件方面,切削速度对冷度程度的影响是力因素和热因素综合作用的结果,通常表现出加工硬化先是随着切削速度的增加而减小。
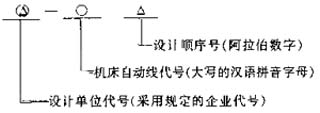
图 3-4 切削速度对硬化层深度的影响
刀具:硬质合金 工件:45钢
切削用量:车削时ap=0.5mm,
F=0.14mm/r铣削时 ap=3mm,af=0.04mm/z
到较高的切削速度后,又随着切削速度的增加而增加(见图3-4)。
增加进给量,将使切削力及塑性变形区范围增大,因此硬化程度随之增加(见图3-3),而切削深度改变时,对硬化层深度的影响则不显著。
采用有效的冷却润滑措施也可以使加工硬化层深度减小。