选择毛坯种类和制造方法时应全面考虑机械加工成本和毛坯制造成本,以达到降低零件生产总成本的目的。影响毛坯选择的因素是:
1)零件生产纲领的大小;
2)工件结构形状和尺寸;
3)零件的机械性能要求;
4)本厂现有生产条件。
拟订工艺过程
1. 定位基准的选择及定位、夹紧符号
工件加工的第一道工序或最初几道工序中,只能用毛坯上未经加工的表面作为定位基准,这种定位基准称为粗基准。在以后的工序中,则应使用经过加工的表面作为定位基准,这种基准称为精基准。
在制订零件机械加工工艺规程时,总是首先考虑选择怎样的精基准把各个主要表面加工出来,然后再考虑选择怎样的粗基准把作为精基准的表面先加工出来。
(1) 精基准的选择,精基准的选择应从保证零件的加工精度,特别是加工表面的相互位置精度来考虑,同时也要照顾到装夹方便,夹具结构简单。因此,选择精基准应遵循下列原则:
1)“基准重合”原则,即应尽可能选用设计基准作为精基准,这样可以避免由于基准不重合而引起的误差。
2)“基准统”原则,即应尽可能选择加工工件的多个方面时都能使用的一组定位基准作为精基准。这样就便于保证各加工表面的相互位置精度,避免基准变换所产生的误差,并能简化夹具的设计和制造。
3):“相互基准”原则,当两个表面相互位置精度以及它们自身的尺寸与形状精度都要求很高时,可以采用互为基准原则,反复多次进行加工。
4)“自身基准”原则,有些精加工或光整加工工序要求加工余量小而均匀,在加工时就应尽量选择加工表面本身作为精基准,而该表面与其他表面之间的位置精度则由先行工序保证。
(2)粗基准的选择,粗基准的选择主要影响不加工表面与加工表面间的相互位置精度,以及加工表面的余量分配。因此,选择粗基准时,一般应注意以下几个问题:
1)如果必须首先保证工件上加工表面与不加工表面之间的位置精度要求,应以不加工表面作为粗基准。如果工件上有很多不需要加工的表面,则应以其中与加工表面的位置精度要求较高的表面作为粗基准。
2)若必须首先保证二件上某重要表面的加工余量均匀,则应选择该表面作为粗基准。
3)选作粗基准的表面的表面应尽量平整光洁,不应有飞边、浇口、冒口等缺陷。
4)粗基准一般只使用一次。
(3)定位与夹紧符号(见表4-9)
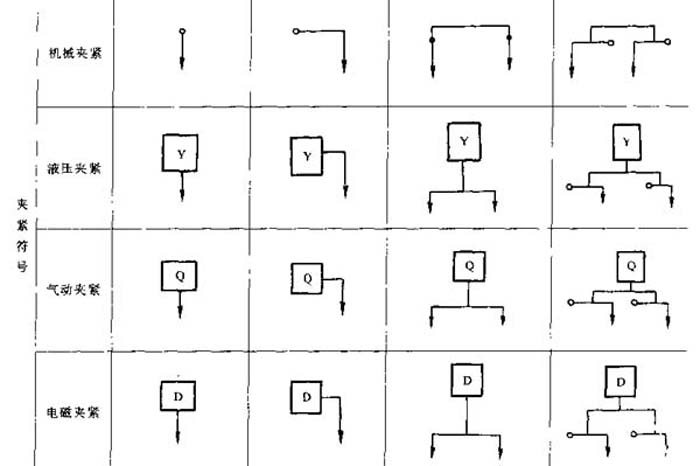