数控加工柔性好,自动化程度高,特别适宜加工轮廓形状复杂的曲线,曲面零件,以及具有大量孔、槽加工的复杂箱体,棱体零件,在多品种、小批量生产情况下,使用数控机床加工能获得较高的经济效益。
数控加工工艺问题的处理与普通加工基本相同,但又有其特点。因此,在设计零件的数控加工工艺时,既要遵循普通加工工艺的基本原则和方法,又要考虑数控加工本身的特点和零件编程要求。
(1)零件装夹方法的确与夹具选择,数控机床上被加工零件的装夹方法与一般机床上一样,也要合理选择定位基准和夹紧方案。在选择精基准时,也要遵循“基准统一”和“基准重合”等原则,除此之外,还应考虑一几点:
1) 听尽量在一次定位夹紧中完成所有能加工的各表面的加工,为此要选择便于各个表面都可被加工的定位方式。如对箱体零件,宜采用一面两销的定位方式,也可采用以某侧面为导向基准,带工件夹紧后将导向元件拆去的定位方式。
2)对于工件一次装夹可完成工件上各个表面的加工,也可直接选用毛面作定位基准,只是这时毛坯的制造精度要求要高一些。
3)对于加工中心,工件在工作台上的安放位置的确定要兼顾各个工位的加工,要考虑刀具长度及其刚度对加工质量的影响。如进行单工位单面加工,应将工件靠工作台一侧放置在工作台的正中位置。这样可减少刀杆伸出长度,提高具刚度。
4)数控加工中使用的夹具,其结构大多比较简单,并应尽可能选用由通用元件拼装的组合可调节夹具,以缩短生产准备周期。为了简化定位、编程和对刀,保证工件能在正确的位置上按程序加工,必须协调工件、夹具与机床坐标系之间的尺寸关系。
(2)加工顺序的安排,除了因按照“先面后孔”“先粗后精”等基本原则安排加工顺序外,还应注意遵循以下原则:
1)为了件少换刀次数和时间,通常应按刀具集中工序。即在一次装夹中,用同一把刀具加工完工件上所有需要压该刀具加工的各个部位后,在换下一把刀具进行加工。对于加工中心,若换刀时间较工作台转位时间,则应采用相同工位集中加工完毕所有可以加工的待加工表面,然后在转动工作台去加工其他表面。
2)对于同轴度要求很高的孔系,应在一次定位后(同一工位下),通过顺序连续换刀,顺序连续加工完该孔系的全部孔后,在加工其他坐标位置的孔,以消除重复定位误差的影响,提高孔系的同轴度。
(3) 对刀点和换刀点的确定,对刀点是数控加工时刀具相对于工件运动的起点。由于程序也是从这一点开始执行,所以对刀点也称作程序起点或起刀点。编程时应首先考虑对刀点位置的选择。
加工精度要求不高时,可直接用工件上或夹具上的某些表面作对刀面;加工精度要求较高时,对刀点应尽量选在零件的设计基准或工艺基准上,如以孔定位的零件,取孔的轴心作为对刀点就比较合适。
对刀点必须与工件的定位基准有一定坐标关系,这样才能确定机床标系与工件坐标系之间的关系。对刀点的选择应便于坐标值的计算,并使对刀方便。
对刀时,应是使对刀点与刀位点重合。所谓刀位点,对于平底立铣刀是指刀具轴线与刀具底面的交点;对于球头铣刀是指球头部分的球心;对于车刀是指刀尖;对于钻头是指钻尖;对于线电极切割机床,则是指线电极轴心与零件面的焦点。
加工过程中需换刀时,应规定换刀点,换刀点的位置应根据换刀时不得碰伤工件、夹具以及机床的原则而设定。
(4)刀具进给路线的规划,进给路线是指数控加工过程中刀具(刀位点)想对于被加工零件的运动轨迹,规划进给路线时应遵循的原则是:
1)保证被加工零件获得良好的加工精度和表面质量。
2)使数值计算工作简单。
3)使进给路线最短。
铣削平面零件轮廓时,一般采用立铣刀的侧刃切削,为了保证工件的外形光滑,铣刀的切入和切出点应沿零件周边外延布置(见图4-3)如果铣刀沿零件轮廓法想直接切如零件,将在零件外形上留下明显刀痕。
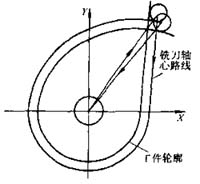
图4-3 加工外轮廓的走刀路线
铣削平面零件内槽的封闭轮廓时,切入切出不能有外延部分。这时可沿零件轮廓的法线切入或切出,可能时其切入和切出点做好选在零件轮廓两几何元素的交点处。
轮廓加工中应避免进给停顿,因为加工过程中,工件、刀具、夹具以及机床等都有少量的弹性变形,进给停顿会使切削力减小,刀具将在工件表面留下凹痕。
对于孔的位置精度要求高的零件,在精镗孔系时,安排镗孔路线一定要注意做到各孔的定位方向一致,避免反向间隙的影响。例如图4-4a所示的进给路线,在加工孔Ⅳ时,X的反向间隙将影响Ⅲ-Ⅳ孔的孔距精度。若按图b的进给路线,可使各孔的定位方向一致,故可提高孔距精度。
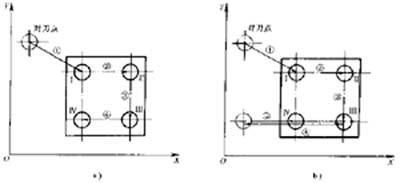
图4-4 孔系加工的两种走刀路线
(5) 刀具选择,数控加工台时费用高,为提高效益,数控加工对刀具提出了更高要求,不仅要刚性好,精度高,而且要尺寸稳定、耐用度高。调整方便。因此凡加工情况允许选用硬质合金刀具时,就不应选用高速钢具刀。应尽量选用可转位刀片以减少刀具磨损后的更换和预调时间,选用涂层刀具以提高耐磨性。精密镗孔应选用性能更好更耐磨的金刚石和立方氧化硼刀具。
数控加工一般不采用钻模,钻孔刚度差,因此钻孔前应选用大直径钻头或中心先锪一个被锥坑或钻一中心孔,作为钻头切入时的定心锥面,然后在用钻头钻孔。
铰孔采用浮动铰刀,铰前孔口要倒角,铰刀两刀刃对称度要控制在0.02~0.05mm之内。
由于镗孔是悬臂加工,为平衡径向力,减轻镗削振动,应采用对称的两刃或多刃镗刀头进行切削。精镗应采用微调镗刀。
(6)切削用量的确定,数控加工的切削用量选择原则与普通加工相同。由金属切削原理可知,在选择切削用量时,应首先采用最大的切削深度,再选用大的进给量,然后根据确定的刀具耐用度选择切削速度。对于数控加工,刀具耐用度至少应大雨加工完一个零件,或最少不低于半个工作班。
在轮廓加工中,应注意克服由于惯性或伺服系统的随动误差而造成轮廓拐角处的“超程”或“欠程”现象。为此,要选择变化的进给量,即在接近拐角处应适当降低进给量,过拐角后在逐渐升高,以保证加工精度(见图4-5)。
(7)程编误差及其控制,程序编制中的误差由逼近误差、插补误差和尺寸圆整误差三部分组成。在点位数控加工中,编程误差只包含尺寸圆整误差,在轮廓加工中,程编误差主要是插补误差,尺寸圆整误差所占的比例较小。
一般应控制尺寸圆整误差不超过脉冲当量的一半。减小插补误差的最简单方法是密化补点,但这会增加程序段数目,增加计算、编程工作量、通常程编误差应小于零件公碴的10%~20%。
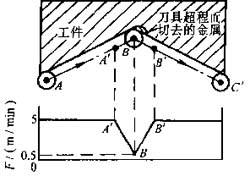
4-5 超程误差及控制