3 载荷、有关系数及疲劳极限
3.1 名义切向力Ft
名义切向力作用于端面内并切于分度圆,且由齿轮副传递的名义功率确定。名义切向力可按下式计算:
式中:d——齿轮分度圆直径,mm;
T——名义转矩,N·m。
当传递的名义功率P以kw计时,


n——齿轮传递,r/min。
在变动载荷下工作的齿轮载荷、应力及其强度安全系数的核算,当缺乏更精确和更可靠的方法及数据可用时,可参考附录B进行核算。
3.2使用系数KA
使用系数KA是考虑由于齿轮啮合外部因素引起附加动载荷影响的系数。这种外部附加动载荷取决于原动机和从动机的特征,轴和联轴器系统的质量和刚度以及运行状态。
如有可能,使用系数应通过精密测量或对传动系统的全面分析来确定。当上述方法不能实现时,可参考表2查取。
表2 减速齿轮装置的使用系数KA
原动机工作特性及其示例 |
从动机械工作特性及其示例 |
均匀平稳
如发电机,皮带输送机
、板式输送机、螺旋输送
机、轻型升降机、电葫芦
、机床进给机构、通风机、
透平鼓风机、透平压缩机、
均匀密度材料搅拌机 |
中等振动
如机床传动、重型升降机、
起重机回转机构、矿山通风
机、非均匀密度材料搅拌机、 多缸柱塞泵、进泵 |
严重冲击
如冲床、剪床、橡胶压轧机、
轧机、挖掘机、重型离心机、
重型进料泵、旋转钻机、压
坯机、挖泥机 |
均匀平稳
如电动机、
蒸汽轮机 |
1.00 |
1.25 |
1.75或更大 |
轻微振动
如多缸内
燃机 |
1.25 |
1.50 |
2.00或更大 |
中等振动
如单缸内
燃机 |
1.50 |
1.75 |
2.25或更大 |
注:① 表中数值仅适用于在非共振速度区运转的齿轮装置。
② 对于增速传动,根据经验建议取L 表值的1.1 倍。
③ 当外部机械与齿轮装置之间有挠性连接时,通常K 人值可适当减小。
3.3动载系数KV
动载系数Kv 是考虑大、小齿轮啮合振动产生的内部附加动载荷影响的系数。Kv 定义为实际齿轮副啮合时的最大作用力和纯由外加载荷所产生的相应作用力之比值。
影响动载系数的主要因素有:
a.由基节和齿形误差产生的传动误差;
b.大、小齿轮的质量(转动惯量),
c.啮合刚度,特别是在轮齿啮合循环中的刚度变化,
d.考虑了KA 后的切向力的大小。
其他的影响因素还有:
e.润滑情况;
f.齿轮系统的阻尼特性;
g.轴及轴承的刚度,
h.承载齿面上的接触情况。
如能通过实测或对所有影响因素作全面的动力学分析来确定包括内部动载荷在内的最大切向载荷,则可取Kv 等于l ;但此时需对所采用方法的精度和可靠性加以论证,并明确给出前提条件。
在上述的要求难以实现时,可用本标准提供的下述方法计算动载系数。该方法的力学模型为:将大、小齿轮的质量转化到啮合线上,并由弹簧联结所形成的弹性振动系统。弹簧的刚度即为轮齿啮合刚度。啮合中的阻尼取为一个名义平均值,忽略滞后现象和轴承、联轴器等附加阻尼因素。也忽略了轴、轴承和箱体变形的影响。由于未考虑上述各种附加阻尼,除在主共振区外,按本法求得的Kv 值通常比实际的略大一些。
3.3.1 一般方法
确定KV的计算式列于6.2.1.2中,为了使用这些公式,需首先确定临界转速比N。
3.3.1.1 临界转速比N
简化了的齿轮啮合振动模型存在一个临界转速nE1 ,小齿轮的运行转速n1与临界转速nE1的比值N称为临界转速比,即

式中: z1——小齿轮齿数;
Cγ——轮齿啮合刚度,N/(mm·μm),见3.6条;
mred——诱导质量,kg/mm。
其中m1 ,m2分别表示小轮及大轮化到啮合线上的单位齿宽当量质量,kg/mm。
式中:b——齿宽,mm,这里应取各自的实际尺寸;
rb1、rb2——小轮及大轮基圆半径,mm;
Θ1、Θ2——小轮及大轮的转动惯量,kg,mm2。
对一般外啮合传动,齿轮副的诱导质量可近似按下式计算:
式中:ρ——材料密度,kg/mm3;
db——基圆直径,mm;
dm——平均直径,mm,dm=1/2(dn+df);…………………………………………………(23)

(对整体结构的齿轮,q=0);……………………………………………………(24)
Di——轮缘内腔直径,mm。
式(22)各代号的脚标1,2分别表示小轮和大轮。
上述各直径的含义参见图2。
对于行星传动和其他较特殊的齿轮,如小齿轮的平均直径接近其轴径,两刚性联接的同轴齿轮,两个小轮驱动一个大轮等,其诱导质量可分别按表3和表4的分式近似计算。
表 3 行星传动齿轮的诱导质量mred
齿轮组合 |
mred计算公式或提示 |
备注 |
太阳轮(S)-
行星轮(P) |

|
np——轮系的行星轮数;
ms,mp——太阳轮,行星轮的
当量质量,可用式(20)
及(21)计算 |
行星轮(P)-
固定内齿圈 |
|
把内齿圈质量视为无穷
大处理。
ρp——行星轮材料密度;
dm,db,q定义及计算参见
式(23)(24)说明及图2 |
行星轮(P)-
转动内齿圈 |
mred按式(22)计算,有若干个行
星轮时可按单个行星轮分别计算 |
内齿圈的当量质量可当
作外齿轮处理 |
表4 较特殊结构型式的齿轮的诱导质量mred
齿轮结构型式 |
计 算 公 式 或 提 示 |
备注 |
1 |
小轮的平均直径与轴颈相近 |
采用一般的计算公式,见式(22)。
因为结构引起的小轮当量质量增大和扭转刚度增大(使实际啮合刚度cy增大)对计算临界转速nE1的影响大体上相互抵消 |
|
2 |
两刚性联接的同轴齿轮 |
较大的齿轮质量必须计人,而较小的齿轮质量可以略去 |
若两个齿轮直径无显著差别时,一起计入 |
3 |
两个小轮驱动一个大轮 |
可分别按小轮1-大轮
小轮2-大轮
两个独立齿轮副分别计算 |
此时的大轮质量总是比小轮质量大得多 |
4 |
中间轮 |
|
m1,m2,m3为主动轮、中间轮、从动轮的当量质量;
cy1-2——主动轮、中间轮啮合刚度;
cy2-3——中间轮、从动轮啮合刚度 |
3.2.1.2 KV的计算式
临界转速比N对齿轮装置的动载系数有着极其重要的影响,N=1时,运行转速n等于临界转速,此时KV达最大值。在不同的N值区间,即不同的运行转速区间,啮合振动对KV的影响是不同的。考虑到振动模型的简化和次要影响因素的忽略而带来的计算结果与实际情况的偏差,将运行转速N值划分为4个区间,其相应的KV计算公式见表5。
表5 运行转速区间及其动载系数KV的计算公式
运行转速区间 |
临界转速比N |
对运行的齿轮装置的要求 |
KV计算公式 |
备注 |
亚临界区 |
N≤NS |
多数通用齿轮在此区工作 |
KV=NK+1=N(CV1Bp+CV2Bf+CV3BK)+1 (29) |
在N=1/2或2/3时可能出现共振现象,KV大大超过计算值,直齿轮尤甚。此时应修改设计,在N=1/4或1/5时共振影响很小 |
主共振区 |
NS<N≤1.5 |
一般精度不高的齿轮(尤其是未修缘的直齿轮)不宜在此区运行。εy>2的高精度斜齿轮可在此区工作 |
KV=CV1Bp+CV2Bf+CV4BK+1 (30) |
在此区内KV受阻尼影响术大,实际动载与按式(30)计算所得值相差可达40%,尤其是对未修缘的直齿轮 |
过渡区 |
1.15<N<1.5 |
|
|
KV(N=1.5)按式(32)计算。
KV(N=1.5)按式(30)计算 |
超临界区 |
N≥1.5 |
绝大多数透平齿轮及其他高速齿轮在此区工作 |
KV=CV5Bp+CV6Bf+CV7 ……………… (32) |
1.可能在N=2或3时出现共振,但影响不大。
2.当轴齿轮系统的横向振动固有频率与运行的啮合频率接近或相等时,实际动载与按式(32)计算所得值可相差100%,应避免此情况 |
注:1 表中各式将每一齿轮副按单级传动处理,略去多级传动的其他各级的影响。非刚性联结的同轴齿轮,可以这样简化,否则应按表4中第二类型情况处理。
在表5各式中
Cv1——考虑基节偏差的影响系数,
Cv2——考虑齿形误差的影响系数.
Cv3——考虑啮合刚度周期变化的影响系数,
Cv4——考虑啮合刚度周期性变化引起齿轮副扭转共振的影响系数.
Cv5——考虑在超临界速度区内基节偏差的影响系数,
Cv6——考虑在超临界速度区内齿形误差的影响系数,
Cv7——考虑实际齿轮在超临界速度区内最大外加载荷与理想精密齿轮的最大载荷的关系系数。
上述Cv1~Cv7的值可按表6 中相应公式计算或由图3 查取。
Bp、Bf、Bk——分别考虑基节偏差、齿形误差和轮齿修缘对动载荷影响的无量纲参数。
式中:Ft,FA——定义同前;
b——对齿轮的较小齿宽,mm;
C′——单对齿刚度,N/(mm·μm),见3.6条;
Ca——设计修复量,μm,沿齿廓法线方向计量。对无修缘齿轮,可用由跑合产生的齿顶磨合量Cay(μm)值代替。Cay可按下述公式计算。
当大、小轮材料相同时:
当大、小轮材料不同时:
Cay=0.5(Cay1+ Cay2) …………………………(37)
Cay1 ,Cay2分别按式(36)计算。
fpbeff,ffeff——分别为有效基节偏差和有效齿形公差,μm,与相应的跑合量Tp,Yf有关。
fpbeff =fpb-yp …………………………(38)
ffeff =ff-yf …………………………(39)
如无yp ,yt的可靠数据,可近似取
yp= yf = ya
ya可按表13中的公式计算,或由图20,图21查取,见3.5.3款。
fpb,ft通常按大齿轮查取。
表6 CV系数值
图3 系数Cv…… Cv7的数值(相应公式见表6)
3.3.2 简化方法
凡满足下列限制条件的齿轮,Kv 可由图5*或图6查取。
限制条件:
a.厚轮缘的钢质齿轮;
b.单位齿宽载荷Ft/b>150N/mm;
c.小轮齿数较少(z1<50);
d.在亚临界速度区工作,即
对斜齿轮
v·z1/100<14
对直齿
v·z1/100<10
对于v·z1/100 小于3m/s的所有齿轮也可按图查取。
*当由图5 查斜齿轮的Kv 时,若纵向重合度εβ<1 ,这时
Kv=Kva-εβ(Kva-Kvβ)
式中εβ——纵向重合度;
Kvα——由图6按直齿查得的Kv;
Kvβ—— 由图5按斜齿查得的Kv。
3.4齿向载荷分布系数KHβ,KFβ
3.4.1KHβ的定义及影响因素
齿向载荷分布系数是考虑沿齿宽方向载荷分布不均匀影响的系数。在接触强度计算中记为KHβ在弯曲强度计算中记为KFβ。它取决于承载齿轮副的啮合齿向误差Fβγ(见图7 )及啮合刚度Cγ。
接触强度计算的齿向载荷分布系数的定义可由下式表示:
式中:Wmax——单位齿宽最大载荷,N/mm;
Wm——单位齿宽平均载荷,N/mm;
式中: Ft——名义切向力,N;
KA——使用系数。
Kv——动载系数;
b——齿宽,mm。对人字齿轮或双斜齿轮,应取两个斜齿宽度之和。
影响载荷分布系数的主要因素有:
a.齿轮加工误差;
b.箱体幢孔偏差引起的安装误差,大小轮轴的平行度;
c.由几何尺寸和结构形式确定的轮齿、轮缘、轴、箱体以及机座的刚度;
d.热膨胀及热变形,这对高速宽齿轮尤其重要;
e.轴承间隙及变形;
f.轮齿接触变形;
g.切向、轴向载荷及轴上的附加载荷(例如带或链传动);
h.跑合效果;
i.设计中有无元件变形补偿措施。
由于影响因素较多,确切的载荷分布系数应通过实际的精密测量和全面分析已知的各影响因素的量值综合确定,这时,要论证所用方法的精确度和可靠性,并明确其前提条件。
上述方法特别适用于重要的高速或大型齿轮传动的校核计算,特别是小轮宽径比6/d1大于1.5 的齿轮。这时,啮合齿向误差实际上已可知道,实际的啮合齿向误差值可根据运转试验或对各影响因素及齿面接触情况的完整分析确定。
在无法得到实际运转试验、接触斑点等影响因素的全面分析资料时,建议用较为详细的分析法求得啮合齿向误差,然后再按式(49)至(52)求得齿向载荷分布系数KHβ。
对于图纸上已限定齿向载荷分布系数值的齿轮,如条件允许,可实测运转中的齿根应力分布或测得各种载荷下的齿面接触情况,进而通过调整的办法来控制齿向载荷分布系数。
一般情况下,影响因素的数值未能确切知道,而运转中的应力测量又难以实现时,可用本标准提供的下述两种方法―一般方法和简化方法来近似地计算齿向载荷分布系数。
3.4.2 一般方法
3.4.2.1 基本假定
a.沿齿宽将轮齿视为许多彼此独立,互不影响的弹簧(具有刚度值为Cγ)。齿上的载荷完全是该处弹簧压缩变形的单值函数(参见图7)。
c.忽略轮齿的接触变形。
3.4.2.2 KHβ的计算公式
KHβ可用式(49)或式(52)计算
a.当bca1/b≤1时
上述各式中:bca1——计算齿宽,见图8;
Cy——轮齿啮合刚度,见3.6条。
Fβγ=FβX-yβ…………………………………………(53)
式中:Fβx——初始啮合齿向误差,是轮齿跑合前的啮合齿向误差,μm;
Fβγ——跑合后的啮合齿向误差,μm ,
yβ——齿向跑合量,见3.4.2.5项。
初始啮合齿向误差Fβx主要是考虑轮齿沿齿宽的综合变形和制造(包括装配)误差的合成量。应通过实测或考查确定,并在装配图上标明。若上述方法难于实现时,可根据下式计算确定。
*应先由式(49)计算bca1/b,如果计算值大于l 时,再按式(51)及式(52)计算。
Fβχ=|fsh+λfma|……………………(54)
式中:fsh——综合变形产生的啮合齿向误差分量,μm ,参见3.4.2.3 ;
fma——加工、安装误差产生的啮合齿向误差分量,μm,参见3.4.2.4 项。
补偿系数λ按表7 选取。
表7补偿系数λ
结构或设计条件 |
λ |
高精度的齿轮,并经精细安装调整 |
0 |
鼓形齿 |
0.5 |
齿端修薄 |
0.7 |
可确定fsh和fma的影响相互补偿时 |
-1 |
一般情况 |
1 |
综合变形应包括受载和工作时的小齿轮及其轴的弹性变形(弯曲变形和扭转变形),以及热变形,轴承、箱体和大齿轮的变形。在一般情况下后四种变形可以忽略。但在很高的线速度下工作的齿轮装置应考虑热变形。
3.4.2.3 综合变形产生的啮合齿向误差分量fsh
无齿向修形时,fsh 是考虑齿轮在载荷作用下,轮体和轴作为一个整体沿齿宽的弯曲变形和扭转变形所造成的齿向误差。
当无法用精密实测或全面分析方法得到KHβ值,可按下式近似求得综合变形的啮合齿向误差分量fsh*:
fsh=Wm·fsho……………………(55)
式中:Wm=Ft·KA·KV/b
对于人字齿或双斜齿轮的情况,除图9 中的e栏外,上式中Ft为两个斜齿轮切向力的总和,而b 则取为单个斜齿的宽度。
fsho——单位载荷(Wm=1N/mm )作用下的相对变形,μm· mm / N ,可按表8 中的公式计算或由图10 查取。
表8 fsho计算公式
齿型结构 |
计算公式 |
值齿轮 |
无齿向修形 |
fsho=(31r+5)×10-3…………(56) |
齿向修形 |
fsho=5×10-3………………(57) |
鼓形齿 |
fsho=(15.5r+5)×10-3…………(58) |
齿端修薄 |
fsho=(23r+5)×10-3…………(59) |
斜齿轮 |
无齿向修形 |
fsho=(36r+13)×10-3…………(60) |
齿向修形 |
fsho=13×10-3…………(61) |
鼓形齿 |
fsho=(18r+13)×10-3…………(62) |
齿端修薄 |
fsho=(27r+13)×10-3…………(63) |
注:①字母A至H是图10中相应曲线的代号。
②表8各式中所含的r为小齿轮结构尺寸系数,可根据结构布局由图9选取系数K值,然后按表9中相应的各式计算。
*当结构不符合图9 时,fsh的确定应另行分析。作为近似计算,可取fsh=1.0Fβ。
表9 小齿轮结构尺寸系数r 的计算式
齿型结构 |
计算公式 |
直齿轮及单斜齿轮 |
|
人字齿轮或双斜齿轮 |
不对称于轴承跨距中心线 |
|
对称于轴承跨距中心线 |
近似用式(65)确定 |
注:①对人字齿轮及双斜齿轮,以图9中实线表示的半人字齿位置按式(65)计算,此时b是单个斜齿的宽度。
②表中公式限制条件详见图9。
③上式中:l一轴承跨距,mm ,s-距离,mm,见图9;d1-小齿轮分度圆直径,mm;K-系数,从图9 查。
注:图中虚线表示人字齿轮或双斜齿轮的另一半斜齿,其综合变形小于实线表示的一半斜齿轮的变形。
齿轮型式:A.直齿轮未修形(56 式)
B.齿轮未修形(60 式)
C.齿轮经齿向修形(57 式)
D.齿轮经齿向修形(61 式)
E.齿轮鼓形齿(58 式)
F.齿轮鼓形齿(62 式)
G.齿轮齿端部修薄(59 式)
H.齿轮齿端部修薄(63 式)
3.42.加工、安装误差产生的啮合齿向误差分量fma
fma的大小取决于齿轮副加工的齿向误差与轴线间平行度的组合(彼此叠加或互相补偿)以及是否进行装配调整。
如无实测数据,fma可按表10中方法之一确定。
表10加工、安装误差的啮合齿向误差分量fma
类别 |
确定方法或公式 |
精密高速齿轮某些类型齿轮 |
fma=0
fma=10μm |
给定精度等级 |
装配时无检验调整 |
fma=1.0Fβ |
|
装配时进行检验调整 |
fma=0.5 Fβ |
给定空载下接触斑点长度bco |
sc——涂色层厚度,一般为2~20μm,
计算时建议取SC=5μm |
注:表中的Fβ为齿向公差,μm。
3.4.2.5齿向跑合量yβ
齿向跑合最yβ是考虑跑合后使啮合齿向误差减小的量。如无实测数据,yβ可用表11中各式计算或由图11、12查取。
表11齿向跑合量yβ
齿轮材料 |
齿向跑合量yβ,μm, |
适用范围及限制条件 |
调质钢 |
|
V>10m/s时,
yβ≤12800/σHlimμm;
5<v≤10m/s时,
yβ≤25600/σHlim
v≤5m/s时,
yβ无限制 |
灰铸铁、铁体球墨铸铁 |
yβ=0.55FβX……………… (68) |
V>10m/s时,
yβ≤22μm,;
5<v≤10m/s时,
yβ≤45μm;
v≤5m/s时,
yβ无限制 |
渗碳淬火钢、表面硬化钢、氮化钢、
氮碳共渗钢、表面硬化球墨铸铁 |
yβ=0.15FβX………………(69) |
yβ≤6um |
注:①σhlim——齿轮接触疲劳限值,N/mm2,见3.13条。
②FβX——初始啮合齿向误差,μm,见3.4.2.2项。
③当大小齿轮材料及热处理不同时,其齿向跑合量可取为相应两种材料齿轮副跑合量的算术平均值。
3.4.3 简化计算
3.4.3.1 适用范围
a.中等载荷,当载荷范围在400≤Wm≤1000N/mm 时,此法求得的KHβ误差不超过15%。
b.轮齿啮合刚度范围15≤Cr≤25N/mm·μm。
c.齿宽50≤b≤400mm,且齿宽与齿高比为3<b/h<12,小齿轮宽径比b/dl小于2.0,满载时齿宽全长或接近全长接触。
d.大、小轮材料的疲劳极限范围在400≤σHLim≤1000N/mm2的调质钢,矿物油润滑。
e.无齿向修形,齿向跑合量Yβ等于0.5FβX,初始啮合齿向误差FβX不大于40μm。
f.假定啮合齿向误差分量fma约等于齿向公差Fβ;进行研齿跑合或装配中作调整时fma等于0.5Fβ。
g.刚性箱体,受载时两轴承变形量相差很小,可以略去不计。
3.4.3.2 计算公式及线图
齿轮精度为5~9 级(第111 公差组精度)的KHβ简化计算公式及相应的结构布局限制条件见表12。其中,对称支承情况下的齿轮副的齿向跑合量yβ可由图13 至图17 查取(图中实线为未经调整或对研跑合的,虚线为经调整或对研跑合的)。
3.4.4KFβ的计算公式
齿向载荷分布系数KFβ是考虑沿齿宽载荷分布对齿根弯曲应力的影响。对于所有的实际应用范围,KFβ可按下式计算:
KFβ=(KHβ)N……………………………………………(100)
式中:KHβ——接触强度计算的齿向载荷分布系数,见3.4.2或3.4.3;
N——幂指数。
其中:b——齿宽,mm。对人字齿或双斜齿齿轮,用单个斜齿轮的齿宽;
H——齿高,mm。
b/h应取大小齿轮中的小值。
图18给了按式(100)、(101)确定的近似解。对于3<(b/h)<12范围内的对称布置齿轮,KFβ也可用图13至图17的相应精度级别的KHβ线图的右纵坐标查得其近似值。
图18弯曲强度计算的齿向载荷分布系数KFβ
3.5齿间载荷分配系数KHa,KFa
齿间载荷分配系数是考虑同时啮合的各对轮齿间载荷分配不均匀影响的系数。齿间载荷分配系数的定义为:在无任何动载荷的情况下,一对齿轮在啮合区内轮齿上的最大载荷与相同的一对精确齿轮轮齿的相应最大载荷之比。
影响齿间载荷分配系数的主要因素有:
a)受载后轮齿变形;
b)轮齿制造误差,特别是基节偏差;
c)齿廓修形;
d)跑合效果。
齿间载荷分配系数如能通过精密实测或对所有影响因素的精确分析得到,则应优先采用;但此时应对其测量或分析方法的精度和可靠性进行论证。在一般情况下,可按下述方法确定KHa,KFa。
3.5.1 一般方法
齿间载荷分配系数一般可按下式确定:
但对于斜齿轮,如计算得的KHa值过大,则应调整设计参数,使得KHa及KFa不大于εao同时,式(102)和(103)仅适用于齿轮基节偏差在圆周方向呈正常分布的情况。
上述各式中:εγ——总重合度;
εγ=εa+εβ………………………………………(104)
cγ——啮合刚度,见3.6条
fpb——基节极限偏差,通常以大轮的基节极限偏差计算;当有适宜的修缘时,按此值的一半计算;若齿形公差ff大于fpb时,应以ff代替fpb。
FtH=FtKAKVKHβ………………………………………(105)
Ft,KA,KV,KHβ的定义及计算分别见3.1至3.4条。
yα——齿廓跑合最,见3.5.3款。
3.5.2简化方法
对于载荷在200N/mm≤Ft/b≤450N/mm范围内的常规齿轮,齿间载荷分配系数可近似地按总重合度εγ和齿轮精度等级(第Ⅱ公差组精度)由图19查取。在上述载荷范围内,图示值的偏差不大于15%。
对于有适宜修缘的齿传输线,KHα(KFα)可取图示值的80%,但不应小于1。
3.5.3齿廓跑合最ya
齿廓距合量ya沿齿廓法线方向计量。若无经验数据,ya可按表13中的公式近似计算或按图20或图21查取。
表13齿廓跑合量ya
注:①fpb一齿轮基节极限偏差,μm;σHLim一齿轮接触疲劳极限,N/mm2,见3.13条。
②当大、小齿轮的材料和热处理不同时,其齿廓跑合量可取为相应两种材料齿轮副跑合量的算术平均值。
3.6轮齿刚性系数C′,Cγ
轮齿刚性系数(或刚度)定义为使一对或几对同时啮合的轮齿在1mm齿宽上产生1μm挠度所需的载荷。
直齿轮的C′是一对轮齿的最大刚度,简称“单对齿刚度”,它大致等于单齿啮合状态下一对轮齿扔刚度。斜齿轮的C′是指一对轮齿在法截面内的最大刚度。C′是端截面内轮齿总刚度的平均值,简称“啮合刚度”。
影响轮齿刚度的主要地因素有:
a.齿形参数:齿厚、齿高、齿形及其曲率半径;
b.设计参数:螺旋角、重合度、齿圈截面;
c.齿轮制造误差及其啮合齿向误差;
d.齿轮材料的弹性模量。
轮齿刚度的精确值应以实测的结果为依据,然后进行全面分析而确定(这时必须考虑上述所有影响因素)。由于理论上和技术上的困难上述方法难以实现时,可按下述方法之一确定轮齿刚度。
3.6.2一般方法
3.6.2.1单对齿刚度C′
对基本齿廓符合GB1356-78,齿圈和轮辐刚性较大的外啮合刚性齿轮,在中等载荷作用下时,其单对齿刚度可按下述公式近似计算*。
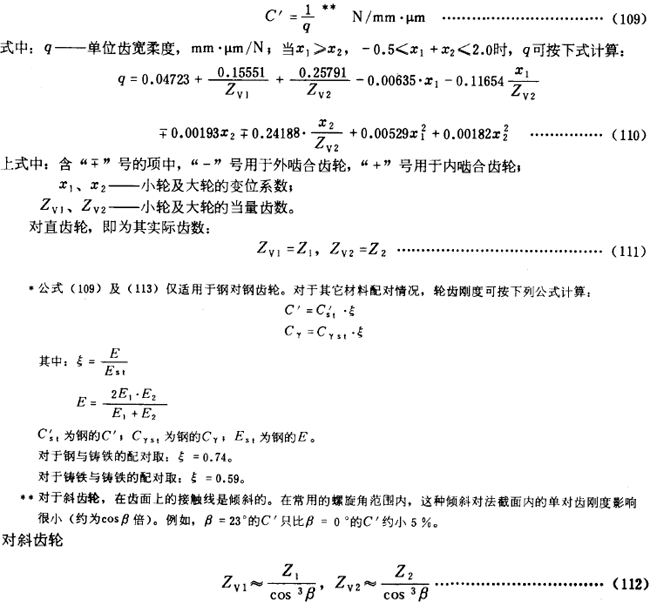
对内齿轮,可将ZV=∞代入式(110)近似计算。
当齿圈及轮辐很薄时,C′可较刚性齿轮降低50%。在端面重合度εα>1.2时,可近似取单对齿啮合区上界点处的C′作为最大刚度,也可将公式(109)的计算结果约降低10%使用。
式(109)(110)
是按Ft/b=300N/mm的条件求得的。在100N/mm≤ ≤1600N/mm范围内,按式(109)(110)求得的C′的误差在+5%到-8%之间。
3.6.2简化方法
在满足3.6.2.1 项的限制条件时,轮齿刚度可近似取为:
单对齿刚度C′=14N/mm·μm……………………(114)
啮合刚度Cγ=20N/ mm·μm……………………(115)
在1.2<εα<1.9范围内,由式(114)和(115)确定的轮齿刚度与一般方法相比,其误差不超过±25%。
3.7节点区域系数ZH
节点区域系数ZH是考虑节点处齿离曲率对接触应力的影响,并将分度圆上切向力折算为节圆上法向力的系数。
ZH数值可由式(116)计算得出。对于具有法面齿形角αn为20°,22.5°,25°的内、外啮合齿轮,ZH也可由图22,图23和图24根据比值(x2±x1)/(z2±z1)及螺旋角β查得。