6 齿厚、公法线长度和跨球(圆柱)尺寸的测量
测得的齿厚常被用来评价整个齿的尺寸或一个给定齿轮的全部齿尺寸。它可根据测头接触点间或两条很短的接触线间距离的少数几次测量来计值,这些接触点的状诚和位置是由测量法的类型(公法线、球、圆柱或轮齿卡尺)以及单个要素偏差的影响来确定的。习惯上常假设整个齿轮依靠一次或两次测量来表明其特性。
控制相配齿轮的齿厚是十分重要的,以保证它们在规定的侧隙下运行。有些情况下,由于齿顶高的变位,要在分度圆直径d处测量齿厚不太容易,故而用一个计算式给出在任何直径dy处齿厚s,见图16,推荐选取dy=d+2mnx。
图16 齿顶高和弦齿厚
6.1齿厚的测量
用齿厚游标卡尺测齿厚
齿厚游标卡尺不能用于测量内齿轮。
侧隙的允许偏差没有包括在sync齿厚的公称值内,应从公称值减去上上偏差Esyns和下Esyni。
Esyni和Esyns应有正负号。
用齿厚游标卡尺测齿的弦齿厚的优点,是可以用一个手持的量具进行测量,携带方便和使用简便是其主要优点,见图17。
图17 用齿厚游标卡尺测量弦齿厚
测量弦齿厚也有其局限性,由于齿厚卡尺寸的两个测量腿与齿面只是在其顶尖角处接触而不是在其平面接触,故测量必须要由有经验的操作者进行。另一点是,由于齿顶圆柱面的精确度和同心度的不确定性,以及测量标尺分辨率很差,使测量不甚可靠。如果可能的话,应采用更可靠的公法线长度、圆柱销或球测量法来代替此法。
6.2 公法线长度的测量
公法线WK的长度是在基圆柱切平面(公法线平面)上跨K个齿(对外齿轮)或k个齿槽(对内齿轮)在接触到一个齿的右齿面和另一个齿的左齿面的两个平行平面之间测得的距离。这个距离在两个齿廓间沿所有法线都是常数(见图18和图19)。
图18 斜齿轮公法线测量
图19 在基圆柱切平面上的公法线测量的极限尺寸
在外齿轮的实际测量时,按规定作出的两内侧平行平面就是度量表面,以测量它们之间的距离。
度量表面间所跨的齿数k应这样来选择,即其接触线大体上位于齿高的中间,可按下面方法来计算(圆整到最近的整数):
式中αytt αt见式9和式10。
公法线长度尺寸由下列公式给出:
Wk=mncosαn[(k-0.5)π+zinvαt+2tanαnx]……………………(29)
或 Wk=(k-1)pbn+sbn……………………(30)
测隙的允许没有包括在Wk的公称值内,应从公称值减去公法线长度的上Ebns和下偏差Ebni的值(见图1),而对内齿轮则应增大。
a) 对外齿轮:
Wk+Ebni≤Wkactual≤Wk+Ebns……………………(32)
b) 对内齿轮:
Wk-Ebni≤Wkactual≤Wk-Ebns……………………(33)
Ebni和Ebns应有适当的正负号。
公法线测量对内斜齿轮是不适当的。另外对斜齿轮而言,公法线测量受齿轮齿宽的限制,只有满足下式条件时才可能:
或使
b>1.015Wksinβb……………………(35)
如果有齿廓或螺旋线修开,公法线测量应该在未经修形的齿面部分进行。对斜齿鼓形齿,斜齿公法线中的公称齿厚应予以修正。对直齿鼓形齿,应在鼓形的顶点测量。
6.3 用测定跨球(圆柱)尺寸来控制齿厚
当斜齿轮的齿宽太窄,不允许作公法线测量时,可以用间接地检测齿厚的方法,即把两个球或圆柱(销子)置于尽可能在直径上相对的齿槽内(图20),然后测量跨球(圆柱)尺寸。
图20 直齿轮的跨球(圆柱)尺寸Md
6.3.1 球或圆柱的尺寸DM
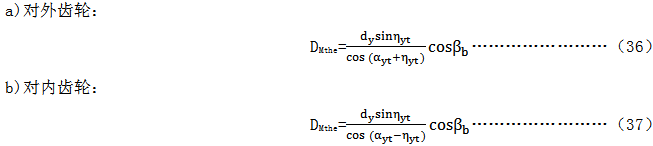
关于αyt,dyηyt和βb见式9,11,12和20。
DM应根据优先数系R40选择较计算值大一点的直径,或选自可提供给齿轮制造商的标准圆柱销尺寸表,例如表1。参见图21。
表1 标准圆柱销的直径 mm
2 |
2.25 |
2.5 |
2.75 |
3 |
3.25 |
3.5 |
3.75 |
4 |
4.25 |
4.5 |
5 |
5.25 |
5.5 |
6 |
6.5 |
7 |
7.5 |
8 |
9 |
10 |
10.5 |
11 |
12 |
14 |
15 |
16 |
18 |
20 |
22 |
25 |
28 |
30 |
35 |
40 |
45 |
50 |
- |
- |
图21 球的尺寸
6.3.2 跨球(圆柱)尺寸Md
6.3.3 计入侧隙允许偏差的跨球(圆柱)尺寸测量
Md的公称值中不包括侧隙的允许偏差,应从公称值减去上偏差Eyns和下偏差Eyns,Eyns和Eyni由下列方程式转换(见7.2)。
因而,跨球(圆柱)尺寸应为:
a)对外齿轮:
Md+Eyni≤Mdactual≤Md+Eyns……………………(46)
b)对内齿轮:
Md-Eyns≤Mdactual≤Md -Eyni……………………(47)
Eyni和Eyns应有正负号。
对于内斜齿轮,只能用球测量。常用球形测头内径千分表来测量,测得端平面上两个置于直径两端的齿槽中球之间的最小尺寸,这是真实的尺寸,当测量奇数齿的斜齿轮时,需要考虑用适当的方法使球定位于端平面上。
6.4 用径向综合检测作齿厚测量
用径向综合检测测量齿厚有其优点,测得的是功充齿厚,包括齿的所有偏差的影响。如果工件的尺寸允许,所需工装也适用,则径向综合检测,即半径方向的测量,是检测齿厚的最好的方法。径向综合检测在一次操作中对产品齿轮的每一个齿都进行了检测,比用其他方法进行多次测量要快得多。
然而,这个方法仅适用于中型和小型齿轮,因为中心距大于500mm的测试仪器是很稀少的,在特定情况下,可以在切削机床上进行测度。
应特别注意被测齿轮的安装面,以保证所进行的测试,能代表齿轮实际运行时的安装情况。对内齿轮需要用专用的仪器或附件。
测量仪器必须经过仔细标定,特别是对小模数和高精度的齿轮。
6.5 径向综合啮合测试的计算
下面的方法适用于外齿轮。
必须校核测量齿轮的尺寸,以使其与产品齿轮作正确的啮合,并保证其接触能达到齿顶附近及真实的渐开线的直径处而不产生干涉。
测量齿轮通常在其上标记着检测半径,所谓检测半径,是指在此半径处测量齿轮与标准齿轮相啮合,该标准齿轮在分度圆直径d2处的齿厚为:
对非标准尺寸的直齿轮,常常需要特殊的测量齿轮。斜齿轮通常需要特殊的测量齿轮。
测量齿轮应该做的非常精确,因为测量齿轮的任何偏差,将在检测结果中添加到产品齿轮的偏差上去。
6.5.1 最大检测半径
最大检测半径是以最大实效齿厚为基础计算的。计算方法中假设测量齿轮的误差是极小的,不会影响检测的结果。这就需要一个十分精确的测量齿轮,特别是在测量精密齿轮时。
如果两个齿轮是紧密相啮合,它们在工作节圆上齿厚之和等于在此圆上的齿距(圆弧上度量的),另外,两个齿轮的工作节圆直径与其齿数成正比。这些关系加上齿厚基本方程式就得联立方程式,从它们可得到工作端面压力角。
式中:sbt2——产品齿轮的最大端面基圆齿厚,mm;
sbt3——测量齿轮的端面基圆齿厚,mm;
db2——产品齿轮的基圆直径,mm;
db3——测量齿轮的基圆直径,mm;
αwt3——紧密啮合时端面工作压力角,°;
pbt——端面基圆齿距,mm。
αwt3也可用下式计算:
式中:Sn2——产品齿轮在分度圆直径蓰的法向齿厚,mm;
Sn3——测量齿轮在分度圆直径处的法向齿厚, mm;
z2——产品齿轮的齿数;
z3——测量齿轮的齿数。
产品齿轮在分度圆上的最大齿厚的尺寸,等于公称齿厚减去齿厚上偏差。
所有的测量均在端平面上进行。
最大中心距值αmax(mm)可由下式计算
最大检测半径r2max是:
r2max=αmax-r3……………………(52)
式中:r3——测量齿轮检测半径,mm。
6.5.2 最小检测半径
图22表明一个典型的径向综合啮合检测的图,“最大齿轮迹线”表示一个齿轮,它有一个最大实效齿厚swtmax的齿,对于径向综合啮合测试或检测中心距的公差带,必须包括由径向综合总公差加上齿厚公差的全部偏差。两个组成部分都随产品齿轮的尺寸和精度不同而变化。
图22 径向综合啮合检测测量齿厚
在下面求αmin的公式中,用αwt3作为最小压力角是一个近似的方法,如时需要更为精确的结果,可用式49或工50和αmin重新计算,取得最后的数值。
式中:αmin——最小中心距;
Tswt——与测量齿轮啮合的工作节圆直径处的端面齿厚公差。