在滚切大直径齿轮时其理论计算的长度将成倍地超过上述规定的长度,同时按其计算长度来设计制造滚刀将存在一系列的难题。如毛坯的锻打,热处理,磨削精度等都不易达到设计要求。为了减轻切入端第一个刀齿的切削负荷,在不增加滚刀长度的前提下,通过生产实践,我们采用了“端剖面阿基米德螺旋不等高齿”的设计法,制造了新结构参数的滚刀,即根据首次进给量,将其分解成若干等分,每等分相等,从切入端第一完整齿起向啮合节点数若干点逐步升高。滚刀长度仍按国标数值,该刀具切削负荷均匀,切削轻快,振动极小。
软齿面齿轮加工示例
表8-5中列出23000KW燃气轮发电机组增速箱中的R005、13、01、37大齿轮加工工艺。
表8-5 R005、13、01、37大齿轮加工工艺
已知条件 |
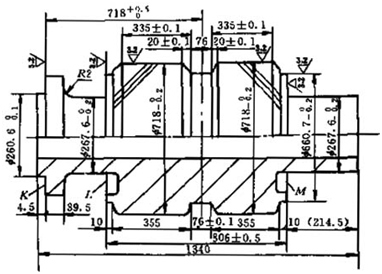
|
齿数z=83,螺旋角β=34°24′41.43″
旋向:如图示,中心距a=560mm。
精度:4级GB10095-88。
热处理:调质200~240HBS
齿距累积公差:Fp=0.036mm
齿形公差ff=0.0095mm
基节极限偏差fpb±0.0055mm
接触斑点:按高度≥60%
按高度≥90% |
序号 |
工序 |
加工或检验内容 |
设备 |
1 |
锻 |
|
|
2 |
热 |
锻后正火 |
|
3 |
粗车 |
按粗加工图进行(粗加工图省略) |
C61125 |
4 |
热 |
调质:200~240HBS |
|
5 |
检 |
割取试料,进行化学成分分析、力学性能试验 |
|
6 |
粗车、镗 |
夹住外圆、粗镗孔 |
C61100 |
7 |
半精车 |
|
C61125 |
8 |
检 |
超声波探伤 |
|
9 |
热 |
去应力 |
|
10 |
精车、镗 |
精镗孔 |
C61100 |
11 |
精车 |
按精车图加工(精车简图省略) |
C6125 |
12 |
磨 |
磨外圆至要求 |
|
13 |
滚齿 |
|
RFK-10S |
14 |
计量 |
测量齿形误差,螺旋线误差、齿面波度误差,公法线长度,齿距的相邻误差和累积误差、齿面的表面精度、人字对中误差等,并作记录,其各项误差按5级精度 |
齿形仪、齿向仪、齿距仪、波度仪、公法线卡尺 |
15 |
剃齿 |
|
RFW-10S |
16 |
计量 |
测量项目同工序14,并增加齿面接触精度检查,各项允差应符合图样要求 |
|
17 |
钳 |
齿部去毛、倒棱 |
|
18 |
检查 |
磁力探伤仪检查,不允许有裂纹及非金属夹杂物、检查后去磁 |
磁力探伤仪 |
19 |
动平衡 |
按技术条件做动平衡试验 |
动平衡机 |
中硬齿面(300~350HBS)齿轮的加工
硬齿面剃齿精加工工艺是于80年代中期在国外发展起来的。它既有剃齿的效率,又具有磨齿才能达到的精度,因此,中硬齿面的工艺流程为滚齿—剃齿—珩齿。
中硬齿面齿轮加工的滚刀目前主要有镀TiN滚刀和钴高速钢滚刀两种。
镀TiN滚刀成本较低,一般镀层费为滚刀价格的1倍左右,在常规切削用量下,对于齿数多、齿宽大的中硬度齿轮,进行滚削加工,能得到很好的齿轮精度,精度可达7级,齿面的表面粗糙度值Ra≥3.2μm。
钴高速钢滚刀的价格较贵,约是普通高速钢滚刀的5倍左右,由于它耐磨。寿命长,综合性能好(尤其是高温硬度)。琴滚切质量又较好,使用AA级的钴高速钢滚刀能够滚切出7级精度及Ra<3.2μm的硬齿面齿轮,经济效益仍然显著。
硬齿面齿轮的加工
渗氮齿轮的加工
渗氮齿轮的加工
渗氮齿轮的工艺路线如下:
锻造—正火—粗车—调质—半精车—去应力—精车—超声波探伤—钳—精磨—滚齿—钳工齿顶及齿端面倒棱—磨齿—齿面渗氮处理
对于精度在4~5级的高速齿轮,粗磨齿及齿面渗氮处理后再加一道精磨工序。齿面渗氮深度应为:设计渗氮层深+单边精磨余量。
齿轮的磨齿余量见表8-6。
表8-6 磨齿的加工余量(齿厚)
模数 |
2 |
3 |
4 |
5 |
6 |
7 |
余量 |
0.15 |
0.2 |
0.23 |
0.26 |
0.29 |
0.32 |
模数 |
8 |
9 |
10 |
11 |
12 |
余量 |
0.35 |
0.38 |
0.4 |
0.45 |
0.5 |
齿轮的渗氮比渗碳耐磨性好,而且变形小,但硬度层深度比渗碳小,处理时间长,成本高。因此,渗氮用于无强烈冲击载荷的高速齿轮。也可用于耐磨性有特殊要求的齿轮。深层离子深氮在高速齿轮制造中的应用,使齿轮的综合强度提高的同时,加工精度无明显下降,常用的7~6级(GB10095—88)齿轮渗氮后不必磨齿就可装机使用,从而使一部分高精度齿轮找到了既经济又方便的强化技术。
渗碳淬火齿轮的加工
渗碳淬火齿轮的工艺路线如下:
锻造—正火—粗车—超声波探伤滚齿—渗碳—非渗碳部位去碳层—淬火—精车—精磨—超硬滚—磨齿—磁粉探伤。
对于模数大、尺寸大的齿轮,各企业根据自己的具体情况,可增加调质等工序。
1.齿轮非渗碳部位无碳层厚度,渗碳前粗车时,非渗碳部位最小余量按表8-7选取,渗碳后车去非渗碳部位的渗碳层,再进行淬火。
表8-7 齿轮非渗碳部位最小余量
渗碳层深 |
0.3~0.8 |
0.9~1.4 |
1.5~2.0 |
2.1`2.5 |
2.6~3.0 |
3.1~4.0 |
4.1~5.0 |
5.1~6.0 |
单边余量 |
1~1.8 |
2~2.5 |
2.6~3 |
3~3.5 |
3.5~4 |
4~5 |
5~6 |
6~7 |
2.渗碳淬火齿轮的磨齿余量,由于渗碳淬火会产生齿部变形,所以渗碳前粗切齿时,齿厚要留足够的余量,以便精切齿时消除变形。齿部变形的大小取于渗碳层深度、齿部长度和模数,并与齿轮的材质和渗碳淬火的工艺方法,各企业的技术水平等因素有关,渗碳淬火齿轮的磨齿余量见表8-8。
表8-8 渗碳淬火齿轮的磨齿余量
模数mn |
mn≤3 |
>3~7 |
>7~10 |
>10~15 |
mn>15 |
公法线放磨量 |
2×0.06mn |
2×0.05mn |
2×0.045mn |
2×0.04mn |
2×0.038mn |
公差 |
0.05 |
渗碳淬火齿轮加工示例。
表8-9为渗碳淬火大齿轮的加工工艺。
表8-9 渗碳淬火大齿轮的加工工艺
技术要求 |
材料:20Cr2Ni4
齿形:渐开线,齿数z=111 模数mn=6mm
螺旋角β=27°,螺旋方向见下图
压力角an=20°,齿顶高系数h*an=1mm
顶隙系数c*n=0.4,径向变为系数x=0.406
中心距a=482.6mm,精度等级:5(-0.24 -0.25)GB10095-88 |
|
齿距累积公差Fp=0.063mm
齿形公差ff=0.013mm
接触斑点:沿齿高≥45%,沿齿长≥80%
公法线平均长度极限偏差,WEws Ewl=324.587-0.23 -0.48mm
跨齿数k=18
齿面渗碳淬火:层深2.2~2.7mm。硬度56~62HRC
动平衡:允许最大不平衡量770g·cm
人字对中线对中偏差±0.3mm |
序号 |
工序 |
加工或检验内容 |
设备 |
|
锻 |
|
|
|
热 |
锻后正火 |
|
1 |
车 |
粗加工至简图(粗加工图略) |
CW61100 |
2 |
检 |
超声波探伤
试样做化学成分分析,力学性能试验 |
超声波探伤仪 |
3 |
热 |
调质230~270HBS |
|
4 |
车 |
按简图车外圆、内孔及端面打印编号 |
C512A |
5 |
检 |
超声波探伤 |
|
6 |
滚齿 |
校正外圆跳动≤0.05mm。滚齿、公法线放磨量0.60~0.65mm |
Y31125E |
7 |
热 |
渗碳层深2.5~3.0mm |
|
8 |
车 |
按简图车去渗碳层(简图略) |
C512 |
9 |
钳 |
划钻攻两端面各4-M24×43均布螺孔,齿廓倒角R1.5 |
Z35 |
10 |
热 |
淬硬56~62HRC(螺孔保护) |
|
11 |
车 |
校正两端轮齿节圆跳动≤0.03mm。车去φ720mm台阶,车准内孔,倒角为8×20°,在另一端面光一刀作校调用
工作调面校内孔,端面圆跳动≤0.02mm。车去φ720mm台阶,保持工件总厚400+0.2 +0.1mm,孔口倒角8×20°,端面打印原标记 |
C512 |
12 |
装配 |
领出大齿轮轴、复测配合尺寸,修光配合处毛刺,将大齿轮按图上技术要求加热、热套 |
|
13 |
磨 |
夹住大齿轮轴φ345mm一端,另一端顶住、校正两轴颈处圆跳动≤0.01mm。磨齿顶圆,在齿的两端面擦一刀。磨出即可。宽度>50mm(工艺要求) |
|
14 |
磨齿 |
按图样要求磨齿 |
HSS-90S |
15 |
检 |
齿面进行磁力探伤,并退磁 |
|
16 |
检 |
按技术要求动平衡 |
|