渐开线圆柱齿轮承载能力计算方法
1 范围
本标准适用于钢、铸铁制造的,基本齿廓符合GB 1356—87 的内、外啮合直齿、斜齿和人字齿(双斜齿)圆柱齿轮传动。基本齿廓与GB 1356—87 相类似,但个别齿形参数值略有差异的齿轮,亦可参照本标准计算其承载能力。
本标准包括齿面接触强度和轮齿弯曲强度两种校核计算方法。
本标准规定相对应的齿轮精度标准为GB 10095—88 。对于采用其它精度标准的齿轮,当采用本标准的简化方法计算有关载荷系数时,应折算成规定标准的相应精度等级。
本标准是各部门和行业制定齿轮承载能力计算标准和规范的基础。
2 引用标准
下列标准所包含的条文,通过在本标准中引用而构成为本标准的条文。本标准出版时,所示版本均为有效。所有标准都会被修订,使用本标准的各方应探讨使用下列标准最新版本的可能性。
GB 1356—87 渐开线圆柱齿轮 基本齿廓
GB/T 3374—92 齿轮基本术语
GB 8539—87 齿轮材料热处理质量检验的一般规定
GB10095—88 渐开线圆柱齿轮精度
3 概述
3.1 可靠性与安全系数
不同的使用场合对齿轮有不同的可靠度要求。齿轮工作的可靠性要求是根据其重要程度、工作要求和维修易等方面的因素综合考虑决定的。一般可分为下述几类情况:
a) 低可靠度要求 齿轮设计寿命不长,对可靠度要求不高的易于更换的不重要齿轮,或齿轮设计寿命虽不短,但对可靠性要求不高。这类齿轮可靠度可取为90%。
b) 一般可靠度要求 通用齿轮和多数的工业应用齿轮,其设计寿命和可靠性均有一定要求。这类齿轮工作可靠度一般不大于99%。
c) 较高可靠度要求 要求长期连续运转和较长的维修间隔,或设计寿命虽不很长时间但可靠性要求较高的高参数齿轮,一旦失效可能造成较严重的经济损失或安全事故,其可靠要求甚至高达99.9%。
d) 高可靠度要求 特殊工作条件下要求可靠度很高的齿轮,其可靠度要求甚至高达99.99%以上。
目前,可靠性理论虽已开始用于一些机械设计,且已表明只用强度安全系数并不能完全反映可靠性水平,但是在齿轮设计中将各参数作为随机变量处理尚缺乏足够数据。所以,本标准仍将设计参数作为确定值处理,仍然用强度安全系数或许用应力作为判据,而通过选取适当的安全系数来近似控制传动装置的工作可靠度要求。考虑到计算结果和实际情况有一定偏差,为保证所要求的可靠性,必须使计算允许的承载能力有必要的安全裕量。显然,所取的原始数据越准确,计算方法越精确,计算结果与实际情况偏差就越小,所需的安全裕量就可以越小,经济性和可靠性就更加统一。
具体选择安全系数时,需注意以下几点:
a) 本标准所推荐的齿轮材料疲劳极限(见8.1)是在失效概率为1%时得到的。可靠度要求高时,安全系数应取大些;反之,则可取小些。
b) 一般情况下弯曲安全系数应大于接触安全系数,同时断齿比点蚀的后果更为严重,也要求弯曲强度的安全裕量应大于接触强度安全裕量。
c) 不同的设计方法推荐的最小安全系数不尽相同,设计者应根据实际使用经验或适合的数据选定。无可用数据时,可参考附录A(标准的附录)选取。
d) 对特定工作条件下可靠度要求较高的齿轮安全系数取值,设计者应作详细分析,并且通常应由设计制造部门与用户商定。
3.2 主要代号
本标准的主要代号及其意义和单位见表1 。
表1 主要代号
代 号 |
意 义 |
单 位 |
a
a′ |
中心距,标准齿轮及高度变位齿轮的中心距
角度变位齿轮的中心距 |
mm
mm |
b
bcal |
齿宽
计算齿宽 |
mm
mm |
C
Ca
Cay
cγ
c′ |
节点:系数
齿顶修缘量
由跑合产生的齿顶修缘量
轮齿单位齿宽总刚度平均值(啮合刚度)
一对轮齿的单位齿宽的最大刚度(单对齿刚度) |
μm
μm
N/(mm·μm)
N/(mm·μm) |
d
d1,d2
da1,da2
db1,db2
df1,df2 |
直径
小轮、大轮的分度圆直径
小轮、大轮的齿顶圆直径
小轮、大轮的基圆直径
小轮、大轮的齿根直径 |
mm
mm
mm
mm
mm |
E
e |
弹性模量(杨氏模量)
辅助量 |
N/mm2 |
Fbn
Fbt
Ft
Fβ
Fβx
Fβy
ff
fpb |
法面内基圆周上的名义切向力
端面内基圆周上的名义切向力
端面内分度圆周上的名义切向力
齿向公差
初始啮合齿向误差
跑合后的啮合齿向误差
齿形公差
基节极限偏差 |
N
N
N
μm
μm
μm
μm
μm |
G |
切变模量 |
N/mm2 |
HB
HRC
HV1
HV10
h
hFa
hFe
ha
haP,hfP |
布氏硬度
洛氏硬度
F=9.8N时的维氏硬度
F=98.1N时的维氏硬度
齿高
载荷作用于齿顶时的弯曲力臂
载荷作用于单对齿啮合区外界点时的弯曲力臂
齿顶高
刀具基本齿廓齿顶高和齿根高 |
mm
mm
mm
mm
mm |
KA
KFα
KFβ
KHα
KHβ
KV |
使用系数
弯曲强度计算的齿间载荷分配系数
弯曲强度计算的齿间载荷分配系数
接触强度计算的齿间载荷分配系数
接触强度计算的齿间载荷分配系数
动载系数 |
|
L |
长度 |
mm |
M
m
mn
mred
mt |
弯矩
模数;当量品质
法向模数
诱导品质
端面模数 |
N·m
mm; kg/mm
mm
kg/mm
mm |
K
NL
n1,n2
nE1 |
临界转速比;指数
应力循环次数
小轮、大轮的转速
小轮的临界转速 |
r/min
r/min |
P
Pbn
Pbt |
功率
法向基节
端面基节 |
kW
mm
mm |
q
qs |
辅助系数
单位齿宽柔度
齿根圆角参数 |
μm·mm/N |
Ra
Rz
r |
轮廓表面算术平均偏差
表面微观不平度10点高度
半径,分度圆半径 |
μm
μm
mm |
SF
SF min
SH
SH min
s
sFn |
弯曲强度的计算安全系数
弯曲强度的最小安全系数
接触强度的计算安全系数
接触强度的最小安全系数
齿厚;尺寸
危险截面上的齿厚 |
mm
mm |
T1,T2 |
小轮、大轮的名义转矩 |
N·m |
u |
齿数比u=z2/z1>1 |
|
v
wm
wmax
x1,x2 |
线速度,分度圆圆周速度
单位齿宽平均载荷
单位齿宽最大载荷
小轮、大轮的法向变位系数 |
m/s
N/mm
N/mm
|
YF
YFa
YNT
YR rel T
YS
YSa
YST
YX
Yβ
Yδ rel T
Yε
yα
yβ |
载荷作用于单对齿啮合区外界点时的齿形系数
载荷作用于齿顶时齿表系数
弯曲强度计算的寿命系数
相对齿根表面状况系数
载荷作用于单对齿啮合区外界点时的应力修正系数
载荷作用于齿顶时的应力修正系数
试验齿轮的应力修正系数
弯曲强度计算的尺寸系数
弯曲强度计算的螺旋角系数
相对齿根圆角敏感系数
弯曲强度计算的重合度系数
齿廓跑合量
齿向跑合量 |
μm
μm |
ZB,ZD
ZE
ZR
ZL
ZNT
ZR
ZV
ZW
ZX
Zβ
Zε
z1,z2
zn |
小轮,大轮单对齿啮合系数
弹性系数
节点区域系数
润滑剂系数
接触强度计算的寿命系数
粗糙度系数
速度系数
齿面工作硬化系数
接触强度计算的尺寸系数
接触强度计算的螺旋角系数
接触强度计算的重合度系数
小轮、大轮的齿数
斜齿轮的当量齿数 |
|
αFan
αFat
αFen
αFet
αan
αat
αen
αet
αn
αt
αt′ |
齿顶法向载荷作用角
齿顶端面载荷作用角
单对齿啮合区外界点处法向载荷作用角
单对齿啮合区外界点处端面载荷作用角
齿顶法向压力角
齿顶端面压力角
单对齿啮合外界点处的法向压力角
单对齿啮合外界点处的端面压力角
法向分度圆压力角
端面分度圆压力角
端面分度圆啮合角 |
°,rad
°,rad
°,rad
°,rad
°,rad
°,rad
°,rad
°,rad
°,rad
°,rad
°,rad |
β
βb
βe |
分度圆螺旋角
基圆螺旋角
单对齿啮合区外界点处螺旋角 |
°,rad
°,rad
°,rad |
γ |
辅助角 |
°,rad |
εα
εβ
εγ |
端面重合度
纵向重合度
总重合度 |
|
1,2 |
小轮、大轮的转动惯量 |
kg·mm2 |
υ |
润滑油运动粘度
泊桑比 |
mm2/s(eSt)
|
ρ
ρfP
ρF |
密度
基本齿条齿根过渡圆角半径
危险截面处齿根圆角半径 |
kg/mm2
mm
mm |
σb
σF
σFo
σFP
σF lim
σH
σHo
σHP
σH lim |
抗拉伸强度
计算齿根应力
计算齿根应力基本值
许用齿根应力
试验齿轮的弯曲疲劳极限
计算接触应力
计算接触应力基本负
许用接触应力
试验齿轮的接触疲劳极限 |
N/mm2
N/mm2
N/mm2
N/mm2
N/mm2
N/mm2
N/mm2
N/mm2
N/mm2 |
3.3 系数的分类和计算顺序
本标准中涉及的影响系数就其对象来说有修正载荷、修正计算应力和修正许用应力三大部分。这些系数可分为两类:
a)由几何关系或常规方法确定的系数,如修正计算应力的系数。这些系数按标准提供的公式计算确定。
b)受多种因素影响但被独立处理的系数。这些因素虽然在一定程度上是相关的,但目前尚难作精确的定量计算。例如,修正载荷的系数KA,KV,KHβ(KFβ),KHα,(KFα)以及修正许用应力的诸系数。
对于修正载荷的诸系数,最理想的方法是通过精密实测或对传动系统作全面的力学分析得到,也可从大量的现场经验确定。这时,应对所采用方法的精确度和可靠性加以认证,并要明确其前提条件。
当由于技术或经济上的原因使上述方法难以实现时,可选取本标准提供的两种方法(即一般方法和简化方法)之一来确定KV,KHβ(KFβ)和KHα,(KFα)。简化方法主要用于总体方案设计和非重要齿轮的核算。在对计算结果有争议时,以一般方法为准。对于要求计算精确度较高的齿轮,各系数应优先采用一般方法或更精确的其它方法计算。
各修正载荷的系数与其相应的端面内分度圆上切向力有关,需按以下顺序计算:
a)用FtKA求KV;
b)用FtKAKV求KHβ(KFβ);
c)用FtKAKVKHβ求KHα(KFα);
对于修正许用应力的诸系数,本标准对每个系数的诸影响因素均按独立变量处理;在取值上除个别某些系数(如三个润滑油膜影响系数ZL,ZV,ZR)外,均只提供一个公式或经验数据。
4 某计算公式
4.1 齿面接触强度核算
本标准把赫兹应力作为齿面接触应力的计算基础,并用来评价接触强度。赫兹应力是齿面间应力的主要指标,但不是产生点蚀的唯一原因。例如在应力计算中未考虑滑动的大小和方向、摩擦系数及润滑状态等,这些都会影响齿面的实际接触应力。
齿面接触强度核算时,取节点和单对齿啮合区内界点接触应力中的较大值,小轮和大轮的许用接触应力σHP 要分别计算。下列公式适用于端面重合度εα<2.5的齿轮副。
在任何啮合瞬间,大、小齿轮的接触应力总是相等的。分析计算表明,齿面最大接触应力一般出现在小轮单对齿啮合区内界点B、节点C及大轮单对齿啮合区内界点D这三个特征点之一处上(B、C、D三点可参见图12)。实际使用和实验均表明,由于上述除赫兹应力外的其它因素影响,产生点蚀的危险的实际接触应力通常出现在C、D点或其间(对大齿轮),或在C、B点或其间(对小齿轮)1]。式(5)是基于节点区域系数ZH计算得节点C处接触应力基本值σHO,当单对齿啮合区内界点处的应力超过节点处的应力时,即ZB或ZD大于1.0时,在确定大、小齿轮计算应力σH时应乘以ZD,ZB予以修正;当ZB或ZD不大于1.0时,取其值为1.0。
对于斜齿轮,当纵向重合度εβ≥1时,一般地节点接触应力较大;当纵向重合度εβ<1时,接触应力由与斜齿轮齿数相同的直齿轮的σH和εβ=1的斜齿轮的σH按εβ作线性插值确定。
4.1.1 强度条件
大、小轮在节点和单对齿啮合区内界点处的计算接触应力中的较大值σH,均应不大于其相应的许用接触应力σHP ,即:
σH≤σHP………………………………………………(1)
或接触强度的计算安全系数SH均应不大于其相应的最小安全系数SH min ,即
SH≥SH min………………………………………………(2)
上述两式中:σH——齿轮的计算接触应力,N/min2,见4.1.2;
σHP——齿轮的许用接触应力,N/min2,见4.1.3;
SH——接触强度的计算安全系数,见4.1.4;
SH min——接触强度的最小安全系数,见3.1及附录A。
4.1.2 计算接触应力σH
小轮和大轮的计算接触应力σH1,σH2分别按下述两式确定:
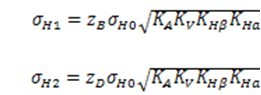
上述两式中:K
A——使用系数,见6.1;
KV——动载系数,见6.2;
KHβ——接触强度计算的齿向载荷分布系数,见6.3;
KHα——接触强度计算的齿间载荷分配系数,见6.4;
ZB,ZD——小轮及大轮单对啮合系数,见7.1.5;
σH0——节点处计算接触应力的基本值,N/min2,用下式计算:
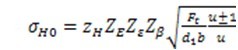
……………………………………(5)
式中:Ft——端面内分度圆上的名义切向力,N,见第5章;
B——工作齿宽,mm,指一对齿轮中的较小齿宽;
d1——小齿轮分度圆直径,mm;
u——齿数比,u=z2/z1,z1,z2分别为小轮和大轮的齿数;
ZH——节点区域系数,见7.1.1;
Z
E——弹性系数,
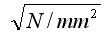
,见7.1.2;
Zε——重合度系数,见7.1.3;
Zβ——螺旋角系数,见7.1.4。
式(5)中的“+”号用于外啮合传动;“-”号用于内啮合传动。
4.1.3 许用接触应力σHP
4.1.3.1 一般方法
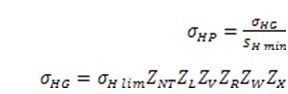
式中:σ
HP——计算齿轮的接触极限应力,N/mm
2;
σH lim——试验齿轮的接触疲劳极限,N/mm2,见8.1;
ZNT——接触强度计算的寿命系数,见8.2.1;
ZL——润滑剂系数,见8.3.1;
ZV——速度系数,见8.3.1;
ZR——粗糙度系数,见8.3.1;
ZW——工作硬化系数,见8.4;
ZX——接触强度计算的尺寸系数,见8.5.1 。
4.1.3.2 简化方法
由式(7)计算σHG时,系数ZL,ZV,ZW按简化方式确定。
4.1.4 接触强度的计算安全系数SH

……………………………………..(8)
式中的各参数对一般方法和简化方法应分别确定。大、小轮的SH应分别计算。不同使用场合对安全系数的考虑参见3.1,σHG和σH计算分别按式(7)和式(3)。
4.2 轮齿弯曲强度核算
作为判断的齿根应力,原则上可用任何适宜的方法(如有限元法、积分法、保角变换法)或实际测量(如光弹测量、应变测量)来确定。在考虑了同时啮合的各对轮齿间载荷分配后,用上述方法之一来确定产生最大齿根应力的载荷作用位置及其相应的最大齿根应力是较理想的方法。
本标准以载荷作用侧的齿廓根部的最大拉应力作为名义弯曲应力,并经相应的系数修正后作为计算齿根应力。
考虑到使用条件、要求及尺寸的不同,本标准将修正后的试件弯曲疲劳极限作为齿根应力。
本标准的轮齿弯曲强度计算式适用于齿根以内轮缘厚度不小于3.5mn的圆柱齿轮。对于不符合前述条件的薄轮缘齿轮,应作进一步应力分析、实验或根据经验资料确定其齿根应力的增大率。在无法采用上述方法时,可参考附录C近似确定2] 。
4.2.1 强度条件
计算齿根应力σF 应不大于许用齿根应力σFP,即:
σF≤σFP……………………………………..(9)
或弯曲强度的计算安全系数SF应不小于弯曲强度的最小安全系数SF min ,即
SF≥SF min……………………………………(10)
上述两式中:σF——齿轮的计算齿根应力,N/mm2,见4.2.2;
σFP——齿轮的许用齿根应力,N/mm2,见4.2.3;
SF——弯曲强度的计算安全系数,见4.2.4;
SF min——弯曲强度的最小安全系数,见3.1及附录A。
4.2.2 计算齿根应力σF
计算齿根应力σF由下式确定:
σF=σF0 KAKV KFβKFα……………………………………(11)
式中:KA,KV——见4.1.2说明;
KFβ——弯曲强度计算的齿向载荷分布系数,见6.3.4;
KFα——弯曲强度计算的齿间载荷分配系数,见6.4;
σF0——齿根应力的基本值,N/mm2,对于大、小齿轮应分别确定。
本标准提供下列两种确定齿根应力基本值σF0的计算方法。对于计算精度要求较高的齿轮,应优先采用方法一。在对计算结果有争议时,以方法一为准。
a)方法一:本法是以载荷作用于单对齿啮合区外界点为基础进行计算的1)。齿根应力基本值可按下式确定:
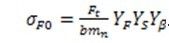
…………………………………..(12)
式中:Ft——端面内分度圆上的名义切向力,N;
b——工作齿宽(齿根圆处),mm。若大、小齿轮宽度不同时,最多把窄齿轮的齿宽加上一个模数作为宽齿轮的工作齿宽;对于双斜齿或人字齿轮b=bB×2,bB为单个斜齿轮宽度;轮齿如有齿端修薄或鼓形修整,b应取比实际齿宽较小的值;
mn——法向模数,mm;
YF——载荷作用于单对齿啮合区外界点时的齿形系数,见7.2.1;
YS——载荷作用于单对齿啮合区外界点时的应力修正系数,见7.2.2;
Yβ——螺旋角系数,见7.2.4 。
b)方法二:本法是以载荷作用于齿顶为基础进行计算的,仅适用于εα<2的齿轮传动。齿根应力基本值按下式确定:
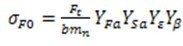
…………………………………..(13)
式中:YFα——载荷作用于齿顶时的齿形系数,见7.2.1;
YSα——载荷作用于齿顶时的应力修正系数,见7.2.2;
Yε——弯曲强度计算的重合度系数,见7.2.3。
Ft,b,mn和Yβ的意义同式(12)的说明。
4.2.3 许用齿根应力σFP
大、小齿轮的许用齿根应力要分别确定。在采用以试验齿轮的强度为依据所得到的数据时,其许用齿根应力可按下式确定2):
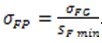
…………………………………..(14)

………………………………..(15)
式中:σFG ——计算齿轮的弯曲极限应力,N/mm2;
σF lim——试验齿轮的齿根弯曲疲劳极限,N/mm2,见8.1.3;
YST—— 试验齿轮的应力修正系数,如用本标准所给σF lim值计算时,取
YST=2.0…………………………(16)
YNT——弯曲强度计算的寿命系数,见8.2.2;
SF min——弯曲强度的最小安全系数,见3.1及附录A;
Yδrel T——相对齿根圆角敏感系数,见8.6;
YRrel T——相对齿根表面状况系数,见8.7;
YX——弯曲强度计算的尺寸系数,见8.5.2 。
4.2.4 弯曲强度的计算安全系数SF

………….………………………..(17)
式中符号的说明见4.2.2及4.2.3 , 大小齿轮的安全系数应分别计算。不同使用场合对安全系数的考虑参见3.1,σFG和σF计算分别按式(15)和式(11)。
5 名义切向力Ft
一般齿轮传动的名义切向力由齿轮传递的名义功率或转矩确定。名义切向力作用于端面内并切于分度圆,可按下式计算:

………….………………………..(18)
式中:Ft——名义切向力,N;
d——齿轮分度圆直径,mm;
T——名义转矩,N·m。
当传递的名义功率P以kw计时,
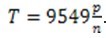
………….………………………..(19)
当传递的名义功率P以PS计时,
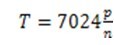
………….………………………..(20)
n——齿轮传递,r/min.
在变动载荷下工作的齿轮载荷、应力及其强度安全系数的核算,当缺乏更精确和更可靠的方法及数据可用时,可参考附录B进行核算。
6 修正载荷的系数和轮齿刚度
6.1 使用系数KA
使用系数KA是考虑由于齿轮啮合外部因素引起附加动载荷影响的系数。这种外部附加动载荷取决于原动机和从动机的特征,轴和联轴器系统的质量和刚度以及运行状态。
如有可能,使用系数应通过精密测量或对传动系统的全面分析来确定。当上述方法不有实现时,可参考表2查收,但需注意以下几点:
a)表2主要适用于在非共振区运行的工业齿轮和高速齿轮,采用表荐值时至少应取最小弯曲强度安全系数3]SF min=1.25
b)某些应用场合的使用系数KA值可能远高于表2中示值(甚至高达10),选用时应认真并尽可能全面地分析工况和联接结构。如在运行中存在非正常的重载、大的起动转矩、重复的中等或严重冲击,应当核算其有限寿命下承载能力和静强度。
表2 使用系数KA
原动机工作特性 |
工 作 机 工 作 特 性 |
均匀平稳 |
轻微冲击 |
中等冲击 |
严重冲击 |
均匀平稳 |
1.00 |
1.25 |
1.50 |
1.75 |
轻微冲击 |
1.00 |
1.35 |
1.60 |
1.85 |
中等冲击 |
1.25 |
1.50 |
1.75 |
2.0 |
严重冲击 |
1.50 |
1.75 |
2.0 |
2.25或更大 |
注
1 对于增速传动,根据经验建议取上表值的1.1倍。
2 当外部机械与齿轮装置之间挠性联接时,通常KA值可适当减小。 |
6.2 动载系数KV
动载系数KV是考虑齿轮制造精度、运转速度对轮齿内部附加动载荷影响的系数,定义为:
K
V=

影响动载系数的主要因素有:
a)由基节和齿形误差产生的传动误差;
b)节线速度;
c)转动件的惯量和刚度;
d)轮齿载荷;
e)轮齿啮合刚度在啮合循环中的变化。
其他的影响因素还有:跑合效果、润滑油特性、轴承及箱体支承刚度以及动平衡精度等。
如能通过实测或对所有影响因素作全面的动力学分析来确定包括内部动载荷在内的最大切向载荷,则可取KV等于1;但此时需对所采用方法的精度和可靠性加以论证,并明确给出前提条件。
在上述的要求难以实现时,可用本标准提供的下述方法之一计算动载系数。该方法的力学模型为:将大小齿轮的质量转化到啮合线上,并由弹簧联结所形成的弹性振动系统。弹簧的刚度即为轮齿啮合刚度。啮合中的阻尼取为一个名义平均值,忽略滞后现象和轴承、联轴器等附加阻尼因素。也忽略了轴、轴承和箱体变形的影响。由于未考虑上述各种附加阻尼,除在主共振区外,按本法求得的KV值通常比实际的略大一些。
6.2.1 一般方法
确定KV的计算式列于6.2.1.2中,为了使用这些公式,需首先确定临界转速比N。
6.2.1.1 临界转速比N
简化了的齿轮啮合振动模型存在一个临界转速nE1 ,小齿轮的运行转速n1与临界转速nE1的比值N称为临界转速比,即

………….………………………..(21)
临界转速nE1可按(22)计算
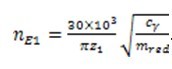
………….………………………..(22)
式中:nE1——小齿轮临界转速,r/min;
z1——小齿轮齿数;
Cγ——轮齿啮合刚度,N/(mm·μm),见6.5.2;
mred——诱导质量,kg/mm。
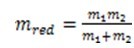
………….………………………..(23)
其中m1 ,m2分别表示小轮及大轮化到啮合线上的单位齿宽当量质量,kg/mm。

式中:b——齿宽,mm,这里应取各自的实际尺寸;
rb1、rb2——小轮及大轮基圆半径,mm;
Θ1、Θ2——小轮及大轮的转动惯量,kg,mm2。
对一般外啮合传动,齿轮副的诱导质量可近似按下式计算:
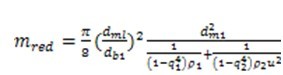
………….………………………..(26)
式中:ρ——材料密度,kg/mm3;
db——基圆直径,mm;
dm——平均直径,mm,dm=1/2(dn+df);

(对整体结构的齿轮,q=0);
Di——轮缘内腔直径,mm。
式(26)各代号的脚标1,2分别表示小轮和大轮。
上述各直径的含义参见图1。
图1 齿轮各直径
对于行星传动和其他较特殊的齿轮,如小齿轮的平均直径接近其轴径,两刚性联接的同轴齿轮,两个小轮驱动一个大轮等,其诱导质量可分别按表3和表4的分式近似计算。
表 3 行星传动齿轮的诱导质量mred
齿轮组合 |
mred计算公式或提示 |
备注 |
太阳轮(S)-行星轮(P) |
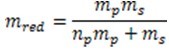 (27) |
np——轮系的行星轮数;
ms,mp——太阳轮,行星轮的当量质量,可用式(24)及(25)计算 |
行星轮(P)-固定内齿圈 |
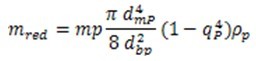 (28) |
把内齿圈质量视为无穷大处理。
ρp——行星轮材料密度;
dm,db,q定义及计算参见式(26)说明及图1 |
行星轮(P)-转动内齿圈 |
mred按式(26)计算,有若干个行星轮时可按单个行星轮分别计算 |
内齿圈的当量质量可当作外齿轮处理 |
表4 较特殊结构型式的齿轮的诱导质量mred
齿轮结构型式 |
计 算 公 式 或 提 示 |
备注 |
1 |
小轮的平均直径与轴颈相近 |
采用一般的计算公式,见式(26)。
因为结构引起的小轮当量质量增大和扭转刚度增大(使实际啮合刚度cy增大)对计算临界转速nE1的影响大体上相互抵消 |
|
2 |
两刚性联接的同轴齿轮 |
较大的齿轮质量必须计人,而较小的齿轮质量可以略去 |
若两个齿轮直径无显著差别时,一起计入 |
3 |
两个小轮驱动一个大轮 |
可分别按小轮1-大轮
小轮2-大轮
两个独立齿轮副分别计算 |
此时的大轮质量总是比小轮质量大得多 |
4 |
中间轮 |
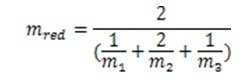 (29)
等效刚度
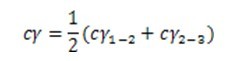 (30) |
m1,m2,m3为主动轮、中间轮、从动轮的当量质量;
cy1-2——主动轮、中间轮啮合刚度;
cy2-3——中间轮、从动轮啮合刚度 |
6.2.1.2 KV的计算式
临界转速比N对齿轮装置的动载系数有着极其重要的影响,N=1时,运行转速n等于临界转速,此时KV达最大值。在不同的N值区间,即不同的运行转速区间,啮合振动对KV的影响是不同的。考虑到振动模型的简化和次要影响因素的忽略而带来的计算结果与实际情况的偏差,将运行转速N值划分为4个区间,其相应的KV计算公式见表5。
表5 运行转速区间及其动载系数KV的计算公式
运行转速区间 |
临界转速比N |
对运行的齿轮装置的要求 |
KV计算公式 |
备注 |
亚临界区 |
N≤NSNS |
多数通用齿轮在此区工作 |
KV=NK+1=N(CV1Bp+CV2Bf+CV3BK)+1 (31) |
在N=1/2或2/3时可能出现共振现象,KV大大超过计算值,直齿轮尤甚。此时应修改设计,在N=1/4或1/5时共振影响很小 |
主共振区 |
NS<N≤1.5 |
一般精度不高的齿轮(尤其是未修缘的直齿轮)不宜在此区运行。εy>2的高精度斜齿轮可在此区工作 |
KV=CV1Bp+CV2Bf+CV4BK+1 (32) |
在此区内KV受阻尼影响术大,实际动载与按式(32)计算所得值相差可达40%,尤其是对未修缘的直齿轮 |
过渡区 |
1.15<N<1.5 |
|
 (33) |
KV(N=1.5)按式(34)计算。
KV(N=1.5)按式(32)计算 |
超临界区 |
N≥1.5 |
绝大多数透平齿轮及其他高速齿轮在此区工作 |
KV=CV5Bp+CV6Bf+CV7 (34) |
1.可能在N=2或3时出现共振,但影响不大。
2.当轴齿轮系统的横向振动固有频率与运行的啮合频率接近或相等时,实际动载与按式(34)计算所得值可相差100%,应避免此情况 |
注:
1 表中各式均每一齿轮副按单级传动处理,略去多级传动的其他各级的影响。非刚性联结的同轴齿轮,可以这样简化,否则应按表4中第二类型情况处理。
2 亚临界区中当(F tK A)/b<100N/mm时,N S=0.5+  ;其他情况时,N S=0.85。 |
表5各式中:Cv1——考虑齿距偏差的影响系数;
Cv2——考虑齿形误差的影响系数;
Cv3——考虑啮合刚度周期变化的影响系数;
Cv4——考虑啮合刚度周期性变化引起齿轮副扭转共振的影响系数;
Cv5——在超临界区内考虑齿距偏差的影响系数;
Cv6——在超临界区内考虑齿形误差的影响系数;
Cv7——考虑因啮合刚度的变动,在恒速运行时与轮齿弯曲变形产生的分力有关的系数。
上述Cv1,…Cv7的值可按表6中相应公式计算或由图查取。
表6 CV系数值
总重合度
系数代号 |
1<εγ≤2 |
εγ>2 |
CV1 |
0.32 |
0.32 |
CV2 |
0.34 |
|
CV3 |
0.23 |
|
CV4 |
0.90 |
|
CV5 |
0.47 |
0.47 |
CV6 |
0.47 |
|
总重合度
系数代号 |
1<εγ≤1.5 |
1.5<εγ≤2.5 |
εγ>2.5 |
CV7 |
0.75 |
0.125sin〔π(εγ-2)〕+0.875 (41) |
1.0 |
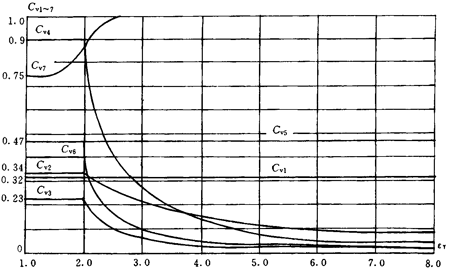
图2 系数C
V1,…,C
V7的数值(相应公式见表6)
Bp、Bt、Bk——分别考虑齿距偏差、齿形偏差和轮齿修缘对动载荷影响的无量纲参数。
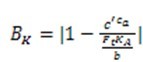
(对于齿轮精度低于5级者,应取B
K=1)…………………………..(44)
式中:Ft,FA——定义同前;
b——一对齿轮的较小齿宽,mm;
c′——单对齿刚度,N/(mm·μm),见6.5;
Ca——设计修复量,μm,沿齿廓法线方向计量。对无修缘齿轮,可用由跑合产生的齿顶磨合量Cay(μm)值代替。Cay可按下述公式计算。
当大、小轮材料相同时:

…………………………..(45)
当大、小轮材料不同时:
Cay=0.5(Cay1+ Cay2) …………………………..(46)
Cay1 ,Cay2分别按式(45)计算。
fpbeff,ffeff——分别为有效基节偏差和有效齿形公差,μm,与相应的跑合量Tp,Yf有关。
fpbeff =fpb-yp …………………………..(47)
ffeff =ff-yf …………………………..(48)
如无yp ,yt的可靠数据,可近似取
yp= yf = ya
ya可按6.4.3中表17的公式计算。
fpb,ft通常按大齿轮查取相应的基节极限偏差和齿形公差.
6.2.2 简化方法
KV的简化法基于经验数据,主要考虑齿轮制造精度和节线速度的影响。根据经验,在图3所示的曲线范围内没有考虑共振区的影响。本方法尤其适用于缺乏详细资料的初步设计阶段时KV的取值。
6.2.2.1 高精度齿轮
传动精度系数C≤5的高精度齿轮,在良好的安装和对中精度以及合适的润滑条件下,KV值可按图3取为1.0~1.1。C值根据6.2.2.2的条件按式(53)计算。
注:6~12为齿轮传动精度系数
图3 动载系数KV
6.2.2.2 其他齿轮
其他齿轮在符合下述条件时,KV值可按图3查取或由式(50)计算。适用的条件是:
a)法向模数mn=1.25~50mm;
b)齿数z=6~1200(当mn>8.33mm时,用 取代1200);
c)传动精度系数C=6~12,C的计算见式(53);
d)齿轮节线速度v不超过vmax
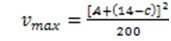
………………………..(49)
A与C的计算分别见式(51)和式(53)
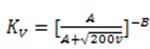
………………………..(50)
式中:
A=50+56(1.0-B)……………………………………(51)
B=0.25(c-5.0)0.667……………………………………(52)
C=-0.504 8ln(Z)-1.144ln(mn)+2.852ln(fpt)+3.32………………………(53)
式(53)计算的C值应作圆整,C=6~12;
z——大、小轮中计算得C值大者的齿数;
mn——法向模数的值;
fpt——大、小轮中最大的单个齿距偏差的值。
6.3 齿向载荷分布系数KHβ,KFβ
6.3.1 KHβ的定义及影响因素
齿向载荷分布系数KHβ是考虑沿齿宽方向载荷分布不均匀对齿面接触应力影响的系数,其定义为:
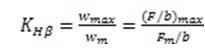
………………………..(54)
式中:ωmax——单位齿宽最大载荷,N/mm;
ωm——单位齿宽平均载荷,N/mm;
Fm——分度圆上平均计算切向力,N;Fm=FtKAKV。
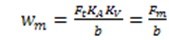
……………………..…..(55)
式中:b——齿宽,mm;对人字齿轮或双斜齿轮,应取两个斜齿轮宽度之和。影响齿向载荷分布的主要因素有:
a)齿轮副的接触精度(GB 10095–88 第Ⅲ公差组精度),它主要取决于齿轮加工误差、箱体镗孔偏差、轴承的间隙和误差、大小轮轴的平行度、跑合情况等;
b)轮齿啮合刚度、齿轮的尺寸结构及支承型式及轮缘、轴、箱体及机座的刚度;
c)轮齿、轴、轴承的变形,热膨胀和热变形(这对高速宽齿轮尤其重要);
d)切向、轴向载荷及轴上的附加载荷(例如带或链传动);
e)设计中有无元件变形补偿措施(例如齿向修形)。
由于影响因素众多,确切的载荷分布系数应通过实际的精密测量和全面分析已知的各影响因素的量值综合确定。这时,要论证应用方法的精确度和可靠性,并明确其前提条件。这种方法特别适用于调质小齿轮宽径比b/d>1.5或硬齿面小齿轮b/d>1.2的重要齿轮装置的校核计算。
各影响因素引起轮齿沿齿宽的综合变形、位移和制造误差的合成量称初始啮合齿向误差(跑合前轮齿啮合齿向误差)以表示Fβx表示。它是决定齿向载荷分布系数的重要数据。在通过实测或综合的精确计算得到初始啮合齿向误差Fβx时,可按式(56)至式(60)求得齿向载荷分布系数KHβ值。
当按上述方法得到的啮合齿向误差由齿向修形补偿的高精度齿轮副,在给定的运行条件下,其齿向载荷接近均匀分布,KHβ接近于1。
在无法按上述方法确定KHβ时,可按本标准提供的下述两种方法——一般方法或简化方法近似计算齿向载荷分布系数。
6.3.2 KHβ计算的一般方法
KHβ计算的一般方法适用条件列于6.3.2.1,计算公式按6.3.2.2。对于符合6.3.2.7中条件的一些典型结构齿轮装置,如单对齿轮、轧机齿、简单行星齿轮,其可KHβ按6.3.2.7所列公式计算。
6.3.2.1 基本假定和适用范围
a)沿齿宽将轮齿视为具有啮合刚度CY的弹性体,载荷和变形都呈线性分布(参见图4);
b)轴齿轮的扭转变形按载荷 沿齿宽均布计算,弯曲变形按载荷集中作用于齿宽中点计算,没有其他额外的附加载荷;
c)箱体、轴承、大齿轮及其轴的刚度足够大,其变形可忽略;
d)等直径轴或阶梯轴, dsh为与实际轴产生同样弯曲变形量的当量轴径;
e)轴和小齿轮的材料都为钢;小齿轮轴可以是实心轴或空心轴(其内径应﹤0.5dsh)齿轮的结构支承形式见图5,偏心距s/l≤0.3。
6.3.2.2 KHβ的计算公式
KHβ可用式(57)或式(59)计算
a) 当
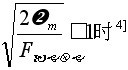
b
ca1/b=
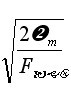
……………………..…………..(56)
K
Hβ=2(b/b
ca1)=

…………………………………(57)
b)
b
ca1/b=0.5+

…………………………………….(58)
采用说明:
4]ISO 6336原判别式为bca1/b在设计时为未知,故改用此判别式。
K
Hβ=
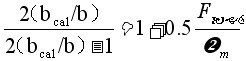
......................(59)
上述各式中:bca1——计算齿宽,见图4;
Cy——轮齿啮合刚度,见6.5;

—跑合后啮合齿向误差,UM;
ωm——计算见式(55)。

=

-yβ=

…………………………………………(60)
式中:

—初始啮合齿向误差,UM,见6.3.2.3;
yβ——齿向跑合量,UM,见6.3.2.6;
Xβ——齿向跑合系数,见6.3.2.6.
当KHβ>1.5时,通常应采取措施降低KHβ值。
K’ |
图号 |
结构示图 |
刚性 |
非刚性 |
0.48 |
0.8 |
a) |
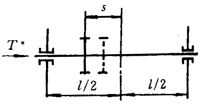 s/l<0.3 |
-0.48 |
-0.8 |
b) |
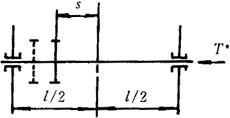 s/l<0.3 |
1.33 |
1.33 |
c) |
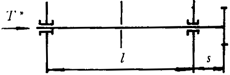 s/l<0.5 |
-0.36 |
-0.6 |
d) |
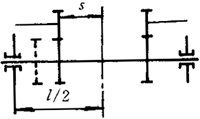 s/l<0.3 |
-0.6 |
-1.0 |
e) |
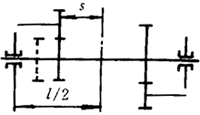 s/l<0.3 |
注
1 对人字齿轮或双斜齿轮,图中实、虚线各代表半边斜齿轮中点的位置,S按用实线表示的变形大的半边斜齿轮的位置计算,b取单个斜齿轮宽度。
2 图中,d1/dsh ≥1.15为刚性轴,d1/dsh <1.15为非刚性轴。通常采用键联接的套装齿轮都属非刚性轴。
3 齿轮位于轴承跨距中心时(S≈0),最好按6.3.2.7的公式计算。
4 当采用图5以外的结构布置型式或s/l超过图5规定的范围,或轴上作用有皮带轮或链轮之类的附加载荷时,推荐进一步的分析。
图5 小齿轮结构系数K’
6.3.2.3初始啮合向误差KHβ
可据KHβ可据不同情况分别按式(61)~(63)计算。
a) 在载荷作用下没达到全齿宽接触或未能验证有良好的接触长度和位置时
=1.33fah+fma; 
≥F
βxmin………………………………………………(61)
b) 当已证实达到所希望的接触斑点时(例如彩齿向修形或装配时调整、对研、部分加载跑合、精确计算鼓形量或齿端修薄量等方法,使弹性变形和制造误差相互补偿)
=|1.33fah-
fma; 
≥F
βxmin………………………………………(62)
5]
c) 在载荷作用下达到理想的接触斑点时

=F
βxmin………………………………………(63)
上述各式中:Fβxmin=max{(0.005mm·um/N)ωm,0.5Fβ}……………………………(64)
即Fβxmin取0.005ωmt 0.5 Fβ二者中之大值。Um;
fsh——综合变形产生的啮合齿向误差分量,Um,见6.3.2.4;
fma——制造、安装误差产生的啮合齿向误差分量,Um,见6.3.2.5;
Fβ——齿向误差,um;
Fβ6——GB10095-88的6级精度的齿向公差Fβ,um.
6.3.2.4 综合变形产生的啮合齿向误差分量fsh
fsh——是考虑小齿轮和小齿轮轴的弯曲和扭转变形产生的啮合齿合误差。
当 fsh无法实测或精确计算时,要按下式确定:
fsh=ωmfsho=(Fm/b)fsho………………………………………………(65)
式中fsh——载荷作用下的的啮合齿向误差,um;
fsho——单位载荷作用下的啮合齿向误差,um·mm/N;可按表7中的公式计算。
表7 fsho计算公式
齿轮型式 |
fsho计算公式 |
一般齿轮 |
0.023y (66) |
齿端修薄的齿轮 |
0.016y (67) |
修形或鼓形修整的齿轮 |
0.012y (68) |
表中:y——小齿轮结构尺寸系数,可根据图5先取系数K’值后,按表8中的公式计算。
表8 小齿轮结构尺寸系数y
齿轮型式 |
Y的计算
公式 |
B# |
功率不分流 |
功率分流,通过该对齿轮K%的功率 |
直齿轮及
单斜齿轮 |
|
B#=1 |
B#=1+2(100-k)/k |
人字齿轮或
双斜齿轮 |
|
B#=1.5 |
B#=0.5+(200-k)/k |
注:l——轴承跨距,mm; s——小轮齿宽中点至轴承跨距中的距离,mm;d1——小轮分度圆直径,mm;dsh——小轮轴弯曲变形当量直径,mm;k’——结构系数,见图5;bB——单斜齿轮宽度,mm. |
采用说明:
5] 式(62)是ISO6336新增的,因含有|1.33fsh-fβ6|项,使用时需加限制条件(如精度及b/d值),否则将出现明显不合理的结果。
6.3.2.5 制造、安装误差产生的啮合齿向误差分量fma
fma的大小取决于齿轮副加工的齿向误差与轴线间平行度的组合(彼此叠加或补偿)以及是否进行装配调整。
如无实测数据, fma可按表9中的方法之一确定。
表9fma计算公式(um)
类别 |
确定方法或公式 |
粗略数值 |
某些高精度的高速齿轮 |
fma=0 |
一般工业齿轮 |
fma=15μm |
给定精度等级 |
装配时无检验调整 |
fma=1.0Fβ |
装配时进行检验调整(对研,轻载跑合,调整轴承,螺旋线修形,鼓形齿等) |
fma=0.5Fβ |
齿端修薄 |
fma=0.7Fβ |
给定空载下接触斑点长度bco |
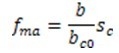 (71)
SC——涂色层厚度,一般为2~20μm,计算时可取
SC=6μm
如按最小接触斑点长度bcomin计算
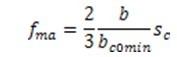 (72)
如测得最长和最短的接触点长度
 (73)
|
6.3.2.6 齿向跑合量yβ,跑合系数Xβ
齿向跑合量yβ是考虑跑合后使啮合齿向误差减小的量,um; Xβ是表示跑合啮合齿向误差Fβy的比例数据,yβ,Xβ可用表10中各式计算。
表10 yβ、Xβ 计算公式
齿轮材料 |
齿向跑合量yβ,um,跑合系数Xβ |
适用范围及限制条件 |
结构钢、调质钢、珠光体或贝氏体球墨铸铁 |
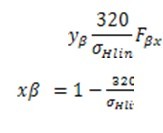 (74) |
V>10m/s时,
yβ≤12800/σHlim FβX≤40μm; ≤12
5<v≤10m/s时,
yβ≤25600/σHlim
FβX≤80μm;
v≤5m/s时,
yβ无限制 |
灰铸铁、铁体球墨铸铁 |
yβ=0.55FβX
xβ=0.45 (75) |
V>10m/s时,
yβ≤22μm, FβX≤40μm; ≤12
5<v≤10m/s时,
yβ≤45μm, FβX≤80μm;
v≤5m/s时,
yβ无限制 |
渗碳淬火钢、表面硬化钢、氮化钢、
氮碳共渗钢、表面硬化球墨铸铁 |
yβ=0.15FβX
xβ=0.85 (76) |
yβ≤6um. FβX≤40um |
注
1σhlim——齿轮接触疲劳限值,N/mm2,见8.1.2
2 当大小齿轮材料不同时,yβ=(yβ1+ yβ2)/2,Xβ=(Xβ7=+Xβ2)/2,式中下标1,2分别表示大、小齿轮。 |
6.3.2.7 典型结构齿轮的FβX
a)适用条件
1)沿齿宽将齿轮视为具有啮合刚度cy的弹性体,载荷和变形均呈线性分布;
2)在载荷作用下接触斑点布满全齿宽,轴齿轮的扭转和弯曲变形均按载荷沿齿宽均布计算,没有其他额外的附加载荷;
3)小齿轮直径和轴径相近,轴齿轮为实心或空心轴(内孔径应<0.5dsh),对称布置在两轴承之间(s/l≈0);非对称布置时,应把估算出的附加弯曲变形量加到fma上;
4)箱体、轴承、大齿轮及其轴的刚度足够大,其变形可忽略。
符合上述条件的单对齿轮、轧机齿轮和简单行星传动可按下述b)~d)中的公式计算KHβ.
b) 单对齿轮
符合a)中条件的单对齿轮,可按表11中的公式计算KHβ.
表11 单对齿轮的KHβ计算公式
齿轮类型 |
修形情况 |
KHβ计算公式 |
直齿轮、斜齿轮 |
不修形 |
|
部分修形 |
|
完全修形 |
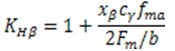 且K Hβ≥1.05 |
人字齿轮或双斜齿轮 |
不修形 |
|
完全修形 |
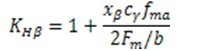 且K Hβ≥1.05 |
注
1 本表各公式适用于全部转矩从轴的一端输入的情况,如同时从轴的两端输入或双斜齿轮人两半边斜齿轮的中间输入,则应作更详细的分析。
2 部分修形指只补偿扭转变形的螺旋线修形;完全修形指同时可补偿弯曲、扭转变形的螺旋线修形。
3 B——包括空刀槽在内的双斜齿全齿宽,mm;bB——单斜齿轮宽度,mm.对因结构要求而超过一般工艺需要的大齿槽宽度的双斜齿轮,应采用一般方法计算。 |
c) 轧机齿轮
轧机齿轮机座采用一对轴齿轮,u=1,功率分流,被动齿轮传递k%的转矩、另外(100-K)%有转矩由主动齿轮的轴端输出,两齿轮皆对称布置在两端的轴承之间,其KHβ值可按表12中公式计算。
表12 轧机齿轮的KHβ计算公式
是否修形 |
齿轮类型 |
KHβ计算公式 |
不修形 |
直齿轮、
斜齿轮 |
 (82) |
双斜齿轮或
人字齿轮 |
 (83) |
完全修形 |
直齿轮、
斜齿轮 |
按式(79) |
双斜齿轮或
人字齿轮 |
按式(81) |
注
1 如按式(83)计算的KHβ>2,应核查设计,最好用更精确的方法重新计算。
2 B为包括空刀槽在内的双斜齿宽度,mm;bB为单斜齿轮宽度,mm. |
d) 简单行星传动齿轮
符合项a)中条件的行星传动中的各齿轮副:太阳轮(S)/行星轮(P)、内齿轮(H)/行星轮,其KHβ可按表13中的公式计算。计算时应取
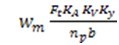
……………………………………….(84)
式中:ωm——单位齿宽平均载荷,N/mm;
Ky——不均载系数;
Np——行星轮个数。
表13 行星传动齿轮的KHβ计算公式
|
齿轮副 |
轴承型式 |
修形情况 |
KHβ计算公式 |
直齿轮、单斜齿轮 |
太阳轮
(S)
|
行星轮
(P) |
Ⅰ |
不修形 |
 (85) |
修形(仅补偿
扭转变形) |
按式(79) |
Ⅱ |
不修形 |
 (86) |
完全修形(弯曲和扭转变形完全补偿) |
按式(79) |
内齿轮
(H)
|
行星轮
(P) |
Ⅰ |
修形或不修形 |
按式(79) |
Ⅱ |
不修形 |
 (87) |
修形(仅补偿弯曲变形) |
按式(79) |
人字齿轮或双斜齿轮 |
太阳轮
(S)
|
行星轮
(P) |
Ⅰ
|
不修形 |
 (88) |
修形(仅补偿弯曲变形) |
按式(81) |
Ⅱ |
不修形 |
 (89) |
完全修形(弯曲和扭转变形完全补偿) |
按式(81) |
内齿轮
(H)
|
行星轮
(P) |
Ⅰ |
修形或不修形 |
按式(81) |
Ⅱ |
不修形 |
 (90) |
修形(仅补偿弯曲变形) |
按式(81) |
注
1 Ⅰ,Ⅱ表示行星轮及其轴承在行星架上的安装型式:Ⅰ——轴承装在行星轮上,转轴刚性固定在行星架上;Ⅱ——行星轮两端带轴颈的轴齿轮,轴承装在转架上。
2 ds——太阳轮分度圆直径,mmdp——行星轮分度圆直径,mm;;lp——行星轮轴承跨距,mm;
B为包括空刀槽在内的双斜齿宽度,mm;bB为单斜齿轮宽度,mm. |
6.3.3 KHβ计算的简化方法
6.3.3.1 适用范围
a) 中等或较重载荷工况:对调质齿轮,单位齿宽载荷Fm/b为400~1000N/mm;对硬齿面齿轮,Fm/b为800~1500N/mm。
b) 刚性结构和刚性支承,受载时两轴承变形较小可忽略:齿宽偏置度s/l较小,符合表14、表15限定范围。
c) 齿宽b为50~400mm,齿宽与齿高比b/h为3~12,小齿轮宽径比b/d1对调质的应小于2.0,对硬齿面的应小于1.5.
d) 轮齿啮合刚度cy为15~25N/(mm·um).
e) 齿轮制造精度对调质齿轮为5~8级,对硬齿面齿轮为5~6级;满载时齿宽全长或接近全长接触(一般情况下未经齿向修形)。
f) 矿物油润滑。
6.3.3.2 计算公式
齿轮第Ⅲ公差组精度为5~8级(硬齿面为5~6级)及相应的结构布局限制条件的KHβ简化计算公式见表14或表15。
表14 调质齿轮KHβ的简化计算公式
表15 硬齿面齿轮KHβ的简化计算公式
6.3.4 KFβ的计算公式
齿向载荷分布系数KFβ是考虑沿齿宽载荷分布对齿根弯曲应力的影响。对于所有的实际应用范围,KFβ可按下式计算:
KFβ=(KHβ)N…………………………………………….(139)
式中:KHβ——接触强度计算的齿向载荷分布系数,见6.3.2或6.3.3;
N——幂指数。
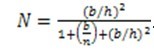
…………………………….(140)
式中:b——齿宽,mm,对人字齿或双斜齿齿轮,用单个斜齿轮的齿宽;
H——齿高,mm.
b/h应取大小齿轮中的小值。
图6给了按式(139)、(140)确定的近似解。
图6 弯曲强度计算的齿向载荷分布系数KFβ
齿间载荷分配系数KHa,KFa
齿间载荷分配系数是考虑同时啮合的各对轮齿间载荷分配不均匀影响的系数。齿间载荷分配系数的定义为:在无任何动载荷的情况下,一对齿轮在啮合区内轮齿上的最大载荷与相同的一对精确齿轮轮齿的相应最大载荷之比。
影响齿间载荷分配系数的主要因素有:
a) 受载后轮齿变形;
b) 轮齿制造误差,特别是基节偏差;
c) 齿廓修形;
d) 跑合效果。
齿间载荷分配系数如能通过精密实测或对所有影响因素的精确分析得到,则应优先采用;但此时应对其测量或分析方法的精度和可靠性进行论证。在一般情况下,可按下述方法确定KHa,KFa。
6.4.1 一般方法
齿间载荷分配系数一般可按下式确定:
当总重合度εy≤2时

…………………………….(141)
当总重合度εy>2时
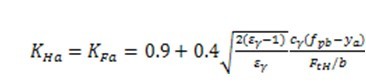
…………………………….(142)
按式(141)或(142)计算时
若

,则取;若

;K
Ha<1.0,则取K
Ha=1.0
若

,则取;若

;K
Fa<1.0,则取K
Fa=1.0
但对于斜齿轮,如计算得的KHa值过大,则应调整设计参数,使得KHa及KFa不大于εao同时,式(141)和(142)仅适用于齿轮基节偏差在圆周方向呈正常分布的情况。
上述各式中:εγ——总重合度;
εγ=εa+εβ……………………………………….(143)
cγ——啮合刚度,见6.5;
fpb——基节极限偏差,通常以大轮的基节极限偏差计算;当有适宜的修缘时, 按此值的一半计算;
Ya——齿廓跑合量,见6.4.3;
Zε,Yε——接触强度和弯曲强度的重合度系数,分别见7.1.3和7.2.3;
FtH=FtKAKVKHβ………………………………………(144)
FtH——计算FHa时的切向力,N;
Ft,KA,KV,KHβ——见第5章6.1-6.3。