试验齿轮的疲劳极限σHlim, σFlim
8.1.1 概述
σHlim和σFlim是指某种材料的齿轮经长期持续的重复载荷作用后轮齿保持不失效时的极限应力。其主要影响因素有:材料成分,力学性能,热处理及硬化层深度、硬度梯度,结构(锻、轧、铸),残余应力,材料的纯度和缺陷等。
σHlim和σFlim可由齿轮的负荷运转试验或使用经验的统计数据得出。此时需阐明线速度、润滑油粘度、表面粗糙度、材料组织等变化对许用应力的影响所引起的误差。
无资料时,可参考图22~图26根据材料和齿面硬度查取σHlim和σFlim值。
图中的σHlim和σFlim值试验齿轮的失效概率为1%时的轮齿接触疲劳和弯曲疲劳极限。对于其他失效概率和疲劳极限值,可用适当的统计分析方法得到。
图中硬化齿轮的疲劳极限值对渗碳齿轮适用于有效硬化层深度(加工后的)δ≥0.15mn,对于氮化齿轮,其有效硬化层深度δ=0.4~0.6mm。
在σHlim和σFlim的图中,给出了代表材料质量等级的三条线,其对应的材料处理要求见GB8539。
ML——表示齿轮材料质量和热处理质量达到最低要求时的疲劳极限取值线。
MQ——表示齿轮材料质量和热处理质量达到中等要求时的疲劳极限取值线。此中等要求是有经验的工业齿轮制造者以合理的生产成本能达到的。
ME——表示齿轮材料质量和热处理质量达到很高要求时的疲劳极限取值线。这种要求只有在具备水平的制造过程可控能力时才能达到。
MX——表示对淬透性及金相组织有特殊考虑的调质合金钢的取值线。
在选取材料疲劳极限时,除了考虑上述等级对材料质量热处理质量的要求是否有把握达到外,还应注意所用材料的性能、质量的稳定性以及齿轮精度以外的制造质量同图列数值来源的试验齿轮的异同程度。这在选取σFlim时尤为重要。要留心一些常不引人注意的影响弯曲强度的因素,如实际加工刀具圆角的控制,齿根过渡圆角表面质量及因脱碳造成的硬度下降等。有可能出现齿根磨削台阶而计算中又未计Ysg时,在选取σFlim时也应予以考虑。
8.1.2 试验齿轮的接触疲劳极限σH lim
σH lim是指某种材料的齿轮以长期持续的重复载荷作用(对大多数材料其应力循环数为5×107)后,齿面不出现进展性点蚀时的极限应力。
图22a,23a,24a,25a,26a中提供的σH lim值是试验齿轮在标准的运转条件下得到的。具体的条件如下:
中心距 a=100mm
螺旋角 β=0(Zβ=1)
模数 m=3~5mm
齿面的微观不平度10点高度 Rz=3μm(ZR=1)
圆周线速度 υ=10m/s(Zv=1)
润滑剂粘度 v50=100mm2/s(ZL=1)
相啮合齿轮的材料相同(ZW=1)
齿轮精度等级 4~6级(GB10095-88)
载荷系数 KA=KV=KHβ=KHa=1
试验齿轮的失效判据如下:
对于非硬化齿轮,其大小齿轮点蚀面积占全部工作齿面的2%,或对单齿占4%;
对于硬化齿轮,其大小齿轮点蚀面积占全部工作齿面的0.5%,或者对单齿占4%。
8.1.3 试验齿轮的弯曲疲劳极限σFlim
σFlim是指某种材料的齿轮经长期的重复载荷作用(对大多数材料其应力循环数为3×106)后,齿根保持不破坏时的极限应力。
图22b,23b,24b,25b,26b中提供的σFlim值是试验齿轮在标准的运转条件下得到的。具体的条件如下:
螺旋角 β=0(Yβ=1)
模数 m=3~5mm(YX=1)
应力修正系数 YST=2
齿根圆角参数 qs=2.5(Yδrel T=1)
齿根圆角表面的微观不平度10点高度 Rz=10μm(Yδrel T =1)
齿轮精度等级 4~7级(GB10095-88)
基本齿廓按GB1356-87
齿宽 b=10~50mm
载荷系数 KA=KV=KFβ=KFa=1
以上图中的σFlim值适用于轮齿单向弯曲的受载状况;对于受对称双向弯曲的齿轮(如中间轮、行星轮),应将图中查得σFlim值乘上系数0.7;对于双向运转工作的齿轮,其σFlim值所乘系数可稍大于0.7.
8.2 寿命系数ZNT,YNT
寿命系数ZNT和YNT分别考虑齿轮寿命小于或大于持久寿命条件循环次数Nc时(见图27、图28),其可承受的接触应力和弯曲应力值与其相应的条件循环次数Nc时疲劳极限应力的比例的系数。
当齿轮在定载荷工况工作时,应力循环次数NL为齿轮设计寿命期内单侧齿面的啮合次数;双向工作时,按啮合次数较多的一侧计算。当齿轮在变载荷工况下工作并有载荷图谱可用时,应按附录B(提示的附录)中方法核算其强度安全系数;对于缺乏工作载荷图谱的非恒定载荷齿轮,可近似地按名义载荷乘以使用系数KA来核算其强度。
条件循环次数Nc是齿轮材料S-N(即应力-循环次数)曲线上一个特征拐点的循环次数,并取该点处的寿命系数为1.0,相应的S-N曲线上的应力称为疲劳极限应力。
8.2.1 接触强度计算的寿命系数ZNT
接触强度计算的寿命系数ZNT应根据实际齿轮实验或经验统计数据得出S-N曲线求得,它与一对相啮合齿轮的材料、热处理、直径、模数、齿面粗糙度、节线速度及使用的润滑剂明关。当直接采用S-N曲线确定和S-N曲线实验条件完全相同的齿轮寿命系数ZNT时,应取有关的影响系数ZR、ZV、ZL、ZW、ZX的值均为1.0。
当无合适的上述实验或经验数据可用时,ZNT可由表25中的公式计算得出,也可由图27查取。
8.2.2弯曲强度和寿命系数YNT
弯曲强度和寿命系数YNT应根据实际齿轮实验或经验统计数据得出的S-N曲线求得,它与材料、热处理、载荷平稳程度、轮齿尺寸及残余应力有关。当直接采用S-N曲线确定和S-N曲线实验条件完全相同的齿轮寿命系数YNT时,应取系数YδrelT,YRrelT,Yx的值为1.0。
当无合适的上述实验或经验数据可用时,YNT可用表26中的公式计算得出,也可由图28查取。
注:σFE=σFlimYST
图22b 正火处理的结构钢和铸钢的和σFlimσFE
3)灰铸铁
图23a 铸铁的σHlim
3)灰铸铁
图23b 铸铁的σFlim和σFE
采用说明:
12]ISO文体中图23b的1)与2)图样颠倒,已订正。
2)铸钢
图24a 调质处理的碳钢、合金钢及铸钢的σHlim
2)铸钢
注:σFE =σFlim
图24b 调质处理的碳钢、合金钢及铸钢的σFlim和σFE
2)火焰或感应淬火钢
图25a 渗碳淬火钢和表面硬化(火焰或感应淬火)钢的σHlim
2)表面硬化钢
注:σFE=σFlimYST
图25b 渗碳淬火钢和表面硬化(火焰或感应淬火)钢的σFlim和σFE
3)调质或正火——氮碳共渗处理的调质钢
图26a 渗氮和氮碳共渗钢的σHlim
3)调质或正火——氮碳共渗处理的调质钢
注:σ
FE=σF
limY
ST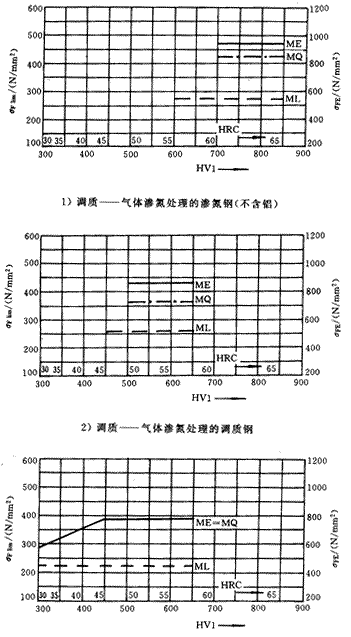
图26b 氮化及碳氮共渗钢的σFlim和σFE
图27 接触强度的寿命系数ZNT
图28 弯曲强度的寿命系数YNT
采用说明:
13]图27、28中灰铸铁在ISO6336:1996文本里误为可锻铸铁,已订正。
表25 接触强度的寿命系数ZNT
材料及热处理 |
静强度最大
循环次数N0 |
持久寿命条
件循环次数NC |
应力循环
次数NL |
ZNT计算公式 |
结构钢
调质钢
球墨铸铁(珠光体、贝氏体)球光体可锻铸铁;渗碳淬火
的碳钢;感应淬火或火焰淬火的钢和球墨铸铁 |
允
许
有
一
定
点
蚀 |
N0=6×105 |
NC=109 |
NL≤6×105
6×105<NL≤107
107<NL≤109
109<NL≤1010 |
ZNT=1.6
Z NT=1.3 0.0738 (216)
Z NT= 0.057 (217)
Z NT= 0.0706 (218) |
不
允
许
点蚀 |
N0=105 |
NC=5×107 |
NL≤105
105<NL≤5≤107
5×107<NL≤1010 |
ZNT=1.6
Z NT= 0.0756 (219)
Z NT= 0.0306 (220) |
灰铸铁、球墨铸铁(铁素体)
;渗氮处理的渗氮钢、调质钢、
渗碳钢 |
NC=2×106 |
NL≤105
105<NL≤2×106
2×106<NL≤1010 |
ZNT=1.3
Z NT= 0.0875 (221)
Z NT= 0.0191 (222) |
氮碳共渗的调质钢、渗碳钢 |
NL≤105
105<NL≤2×106
2×106<NL≤1010 |
ZNT=1.1
Z NT= 0.0318 (223)
Z NT= 0.0191 (224) |
注:当优选材料、制造工艺和润滑剂,并经生产实践验证时,式(218),(220),(222)和(224)可取ZNT=1.0 |
表26 弯曲强度的寿命系数YNT
材料及热处理 |
静强度最
大循环次数N0 |
持久寿命条
件循环次数NC |
应力循环
次数NL |
YNT计算公式 |
球墨铸铁(珠光体、贝氏体)
球光体可锻铸铁;调质钢 |
N0=104 |
NC=3×106 |
NL≤104
104<NL≤3×106
3×106<NL≤1010 |
YNT=2.5
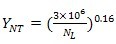 (225)
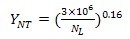 (226) |
渗碳淬火的渗碳钢;火焰淬火、
全齿廓感应淬火的钢、球墨铸铁 |
|
NL≤103
103<NL≤3×106
3×106<NL≤1010 |
YNT=2.5
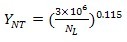 (227)
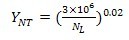 (228) |
结构钢;渗氮处理的渗氮钢、调质钢、
渗碳钢灰铸铁、球墨铸铁(铁素体) |
N0=103 |
NL≤103
103<NL≤3×106
3×106<NL≤1010 |
YNT=1.6
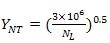 (229)
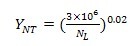 (230) |
氮碳共渗的调质钢、渗碳钢 |
|
NL≤103
103<NL≤3×106
3×106<NL≤1010 |
YNT=1.1
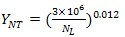 (231)
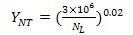 (232) |
注:当优选材料、制造工艺和润滑剂,并经生产实践验证时,式(226),(228),(230)和(232)可取YNT=1.0。 |
8.3 润滑油膜影响系数ZL,ZV,ZR
齿面间的润滑油膜影响齿面承载能力,影响齿面间润滑油膜状况的因素有:
润滑区的油粘度——其影响用润滑剂系数ZL来考虑;
相啮面间的相对速度——其影响用速度系数ZV来考虑;
齿面粗糙度———其影响用粗糙度系数ZR来考虑。
影响齿面间润滑油膜状况的还有齿面载荷和齿面相对曲率半径等。
确定润滑油膜影响系数数值的理想方法是总结现场使用经验或用具有可类比的尺寸、材料、润滑剂及运行条件的齿轮箱实验。当采用与设计的齿轮完全相同的参数、材料和条件实验决定其承载能力或寿命系数时,应取润滑油膜影响系数ZL,ZV,ZR的值均等于1.0。
当无合适的上述实验或以验数据可用时,可按本标准的一般方法或简化方法确定润滑油膜影响系数值。
8.3.1一般方法
对持久强度设计,ZL,ZV,ZR可由公式(235),(237),(239)分别计算或由图29、图30、图31分别查取。对静强度,取ZL=ZV=ZR=1.0。对于循环次数小于持久寿命条件循环次数Nc的有限寿命设计,ZL,ZV,ZR值由式(235),(237),(239)得到的持久强度时的值(即NL=Nc时)和静强度时的值(此时ZL=ZV=ZR=1.0)按公式(233a)至(233c)相应计算:
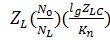
……………………………………………(233a)
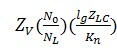
……………………………………………(233b)
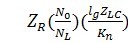
……………………………………………(233c)
上述各式中,不同材料的N0,NC值见表25;Kn是与N0,NC值有关的常数。
Kn=1g(N0/NC)…………………………………………………(234)
对结构钢;调质钢;球墨铸铁(珠光体、贝氏体);珠光体可锻铸铁;渗碳淬火钢;感应淬火或火陷淬火的钢、球墨铸铁
Kn=-3.222(允许一定点蚀)
Kn=-2.699(不允许点蚀)
对可锻铸铁;球墨铸铁(铁素体);渗氮处理的渗氮钢、调质钢、渗碳钢;氮碳共渗的调质钢、渗碳钢。
Kn=-1.301
8.3.1.1 润滑剂系数ZL

…………………………….(235)
式中:CZL——系数。在850N/mm2≤σHlim≤在1200N/mm2范围内,CZL可由式(236)算得。当σHlim<850 N/mm2时取CZL =0.83;当σHlim≥1200 N/mm2时取CZL =0.91。
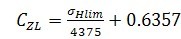
…………………………………………(236)
V50——在50℃时润滑油的名义运动粘度,mm2/s(cSt);
V40——在40℃时润滑油的名义运动粘度,mm2/s(cSt)。
式(235),(236)及图29适用于矿物油(加或不加添加剂)。应用某些具有较小摩擦系数的合成油时,对于渗碳钢齿轮ZL应乘以系数1.1,对于调质钢齿轮应乘以系数1.4。
ZL对静强度几乎没有影响,因此静强度计算时可取ZL=1.0。
图29 润滑剂系数ZL
8.3.1.2 速度系数ZV
速度系数ZV按式(237)计算或按图30查取。

…………………………………………..(237)
式中:CZV——系数。在850N/mm2≤σHlim≤在1200N/mm2范围内,CZV可由式(238)算得。当σHlim<850 N/mm2时以850 N/mm2计;当σHlim≥1200 N/mm2时以1200 N/mm2计。

……………………………………….(238)
V——节点线速度,m/s。
ZV对静强度几乎没有影响,因此静强度计算时可取=1.0。
图30 速度系数ZV
8.3.1.3 粗糙度系数ZR
当所计算的齿轮要求持久寿命时(NL>2×106~5×107,视材料而异,见8.2,ZR可由式(239)计算得出,或由图31查得。
图31 粗糙度系数ZR
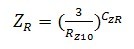
(极限条件为:ZR≤1.15)……………………………………..(239)
式中:CZR——系数。在σHlim<850N/mm2时,CZF =0.15,当σHlim>在1200N/mm2时,当CZF=0.08。在850 N/mm2≤σHlim≤1200 N/mm2范围内,CZR可由式(240)算得。
CZR =0.32-0.0002σHlim…………………………………………………..(240)
RZ10——相对(峰-谷)平均粗糙度。

………………………………………………………(241)
RZ1,RZ2——小齿轮及大齿轮的齿面微观不平度10点高度5)(5)若粗糙度以Ra值(Ra=CLA值,=AA值)给出,则可近似取Rz≈6Ra。),μm。如经事先跑合,则RZ1,RZ2应为跑合后的数值;
ρred——节点处诱导曲率半径,mm;ρred =ρ1ρ2(ρ1±ρ2)。式中“+”用于外外啮合,“-”用于内啮合,ρ1, ρ2分别为小轮及大轮节点处曲率半径;对于小齿轮-齿条啮合,ρred =ρ1;ρ1,2=0.5db1,2tan a't,式中db基圆半径。
ZR对静强度几乎没有影响,因此静强度计算时可取ZR=1.0。
8.3.2 简化方法
ZL,ZV,ZR的乘积在持久强度和静强度设计时由表27查得。对于应力循环次NL小于持久寿命条件循环次数NC的有限寿命设计,(ZLZVZR)值由其持久强度(NL≥NC)和静强度(NL≤NC)时的值参照式(233a)~(233c)插值确定。
表27简化计算的(ZLZVZR)值
计算类型 |
加工工艺及齿面粗糙度RZ10 |
(ZLZVZR)
N0 NC |
持久强度
(NL≥NC) |
RZ10>4μm经展成法滚、插或刨削加工的齿轮副 |
0.85 |
研、磨或剃齿的齿轮副(RZ10>4μm);滚、插
、研磨的齿轮与RZ10≤4μm的磨或剃齿轮啮合 |
0.92 |
RZ10<4μm的磨削或剃的齿轮副 |
1.00 |
静强度
(NL≤NC) |
各种加工方法 |
1.00 |
8.4 齿面工作硬化系数ZW
工作硬化系数ZW是用以考虑经光整加工的硬齿面小齿轮在运转过程中对调质钢大齿轮齿面产生冷作硬化,从而使大齿轮的许用接触应力得以提高的系数。
大齿轮齿面承载能力的提高还和其他许多因素有关,如材料中的合金元素、赫兹应力、硬化过程、表面粗糙度等。所以,工作硬化效果应优先由试验数据来确定,如无合适的试验或经验数据,ZW值可由式(242)计算得出,或由图32查取。此公式和图的使用条件为:小齿轮齿面微观不平度10点高度RZ<6μm,大齿轮齿面硬度为130~470HB。
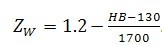
……………………………………(242)
式中HB为大轮齿面布氏硬度值。
当HB<130时,取ZW=1.2;当HB>470时,取ZW=1.0。
图32工作硬化系数ZW
8.5 尺寸系数ZX,YX
尺寸系数ZX和YX是考虑因尺寸增大使材料强度降低的尺寸效应因素,分别用于接触强度和弯曲强度计算。确定尺寸系数最理想的方法是通过实验或经验总结。当用与设计齿轮完全相同尺寸、材料和工艺的齿轮进行实验得到齿面承载能力或寿命系数时,应取ZX或YX值为1.0。静强度(NL≤N0)的ZX=YX=1.0。
当无合适的实验或经验数据可用时,持久强度(NL≥NC)的尺寸系数ZX,YX可分别由下列表28或表29中公式计算确定,也可由图33或图34查取。有限寿命(NO<NL<NC)的尺寸系数由持久强度和静强时的尺寸系数值照式(233)的办法插值确定。
8.5.1 接触强度尺寸系数ZX
持久强度的ZX可按表28中公式计算或图33查取。
表28 接触强度计算的尺寸系数ZX
材料 |
ZX |
备注 |
调质钢、结构钢 |
ZX =1.0 |
|
短时间液体渗氮;气体渗氮钢 |
ZX =1.067-0.05 6mn |
mn<12时,取mn =12
mn>30时,取mn =30 |
渗碳淬火钢、感应或火焰淬火表面硬化钢 |
ZX =1.076-0.010 9mn |
mn<7时,取mn =7
mn>30时,取mn =30 |
注:mn是单位为mm的齿轮法向模数值。 |
8.5.2 弯曲强度尺寸系数YX
持久强度的YX可按表29中公式计算得出,或由图34查取。
a——结构钢、调质钢、静强度计算时的所有材料;
b——短时间液体渗氮钢,气体渗氮钢;c——渗碳淬火钢、感应或火焰淬火表面硬化钢
图33 接触强度计算的尺寸系数ZX14] (14]按DIN3990增补了ZX。 )
a——结构钢、调质钢、球墨铸铁(珠光体、贝氏体)、珠光体可锻铸铁;b——渗碳淬火钢和全齿廓感应或火焰淬火钢,渗氮或氮碳共渗钢;c——灰铸铁,球墨铸铁(铁素体);d——静强度计算时的所有材料
图34 弯曲强度计算的尺寸系数YX
表29 弯曲强度计算的尺寸系数YX
材料 |
YX |
备注 |
结构钢、调质钢、球墨铸铁(珠光体、贝氏体)、
珠光体可锻铸铁 |
1.03~0.006mn |
当mn<5时,取mn =5
当mn>30时,取mn =30 |
渗碳淬火钢和全齿廓感应或火焰淬火钢、渗氮钢
或氮碳共渗钢 |
1.05~0.01mn |
当mn<5时,取mn =5
当mn>25时,取mn =25 |
灰铸铁、球墨铸铁(铁素体) |
1.075~0.015mn |
当mn<5时,取mn =5
当mn>25时,取mn =25 |
注:mn为齿轮法向模数值。 |
8.6相对齿根圆角敏感系数YδrelT
齿根圆角敏感系数表示在轮齿折断时,齿根处的理论应力集中超过实际应力集中的程度。
相对齿根圆角敏感系数YδrelT是考虑所计算齿轮的材料、几何尺寸等对齿根应力的敏感度与试验齿轮不同而引进的系数。定义为所计算齿轮的齿根圆角敏感系数与试验齿轮的齿根圆角敏感系数的比值。
在无精确分析的可用的数据时,可按下述方法分别确定YδrelT值。
8.6.1持久寿命时的相对齿根圆角敏感系数YδrelT
持久寿命时的相对齿根圆角敏感系数YδrelT可按式(243)计算得出,也可由图35查得(当齿根圆角参数在1.5<qs<4的范围内时,YδrelT可近似地取为1,其误差不超过5%)。
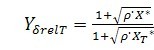
………………………………..(243)
式中:P′——材料滑移层厚度,mm,可由表30按材料查取;
X*——齿根危险截面处的应力梯度与最大应力的比值。其值可由下式确定:

…………………………………………………..(244)
qs——齿根圆角参数,见7.2.2式(209);
——试验齿轮齿根危险截面处的应力梯度与最大应力的比值,仍可用式(244)计算,式中qs取为qsT =2.5。此式适用于m=5mm,其尺寸的影响用YX来考虑。
表30 不同材料的滑移层厚度P′
序号 |
材 料 |
滑移层厚度
P′mm |
1 |
灰铸铁 σb=150N/mm2 |
0.3124 |
2 |
灰铸铁、球墨铸铁(铁素体) σb=300N/mm2 |
0.3095 |
3a
3b |
球墨铸铁(珠光体)
渗氮处理的渗氮钢、调质钢 |
0.1005 |
4 |
结构钢 σs=300N/mm2 |
0.0833 |
5 |
结构钢 σs=400N/mm2 |
0.0445 |
6 |
调质钢,球墨铸铁(珠光体、贝氏体) σs=500N/mm2 |
0.0281 |
7 |
调质钢,球墨铸铁(珠光体、贝氏体) σs=600N/mm2 |
0.0194 |
8 |
调质钢,球墨铸铁(珠光体、贝氏体) σs=800N/mm2 |
0.0064 |
9 |
调质钢,球墨铸铁(珠光体、贝氏体) σs=1000N/mm2 |
0.0014 |
10 |
渗碳淬火钢,火焰淬火或全齿廓感应淬火的钢和球墨铸铁 |
0.0030 |
注:图中材料数字代号意见同表30序号
图35 持久寿命时的相对齿根圆角敏感系数YδrelT
8.6.2 静强度的相对齿根圆角敏感系数YδreT
静强度的YδrelT值可按表31中的相应公式计算得出(当应力修正系数在1.5<YS<3的范围内时,静强度的相对敏感系数YδrelT近似地可取为:YS/YST;但此近似数不能用于氮化的调质钢与灰铸铁)。
表31 静强度的相对齿根圆角敏感系数YδrelT
计算公式 |
公式号 |
备注 |
结构钢
|
(245) |
YS——应力修正系数,见7.2.2
σS——屈服强度 |
调质钢、铸铁和球墨铸铁(珠光体、贝氏体)
|
(246) |
σ0.2——发生残余变形0.2%时的条件屈服强度 |
渗碳淬火钢、火焰淬火和全齿廓感应淬火的钢、球墨铸铁
YδrelT= 0.44YS +0.12 |
(247) |
表层发生裂纹的应力极限 |
渗氮处理的渗氮钢、调质钢
YδrelT= 0.20YS +0.60 |
(248) |
表层发生裂纹的应力极限 |
灰铸铁、球墨铸铁(铁素体)
YδrelT=1.0 |
(249) |
断裂极限 |
8.6.3 有限寿命的齿根圆角敏感系数YδrelT
有限寿命的YδrelT可用线性插入法从持久寿命的YδrelT静强度的YδrelT之间得到。
8.7 相对齿根表面状况系数YRrelT
齿根表面状况系数是考虑齿廓根部的表面状况,主要是齿根圆角处的粗糙度对齿根弯曲强度的影响。
相对齿根表面状况系数YRrelT为所计算齿轮的齿根表面状况系数与试验齿轮的齿根表面状况系数的比值。
在无精确分析的可用数据时,按下述方法分别确定6)(6)对经过强化处理(如喷丸)的齿轮,其YRrelT值要稍大于下述方法所确定的数值。对有表面氮化或化学学腐蚀的齿轮,其YRrelT值要稍小于下述方法所确定的数值。)。
8.7.1 持久寿命时的相对齿根表面状况系数YRrelT
持久寿命时的相对齿根表面状况系数YRrelT可按表32中的相应公式计算得出,也可由图36查得。
a——灰铸铁;铁素体球墨铸铁,渗氮处理的渗氮钢、调质钢;b——结构钢;c——调质钢,球墨铸铁(珠光体、铁素体),渗碳淬火钢,全齿廓感应或火焰淬火钢;d——静强度计算时的所有材料
图36 相对齿根表面状况系数YRrelT
表32持久寿命时的相对齿根表面状况系数YRrelT
计 算 公 式 或 取 值 |
材 料 |
RZ<1μm |
1μm≤ RZ<40μm |
调质钢,球墨铸铁(珠光体、贝氏
体),渗碳淬火钢、火焰和全齿廓感
应淬火的钢和球墨铸铁 |
YRrelT=1.120 |
YRrelT=1.674-0.529(RZ+1)0.1 (250) |
结 构 图 |
YRrelT=1.070 |
YRrelT=5.306-4.203(RZ+1)0.01 (251) |
灰铸铁、球墨铸铁(铁素体), 渗
氮的渗氮钢、调质钢 |
YRrelT=1.025 |
YRrelT=4.299-3.259(RZ+1)0.005 (252) |
注:RZ为齿根表面微观不平度10点高度。 |
8.7.2 静强度的相对齿根表面状况系数YRrelT
静强度的相对齿根表面状况系数YRrelT等于1。
8.7.3 有限寿命的相对齿根表面状况系数YRrelT
有限寿命的YRrelT可从持久寿命的YRrelT和静强度的YRrelT之间用线性插入法得到。
9 轮齿静强度核算
9.1 适用范围
当齿轮工作可能出现短时间、少次数(不大于表25和26中规定的N0值)的超过额定工况的大负荷,如使用大起动转矩电机,在运行中出现异常的重载荷或有重复性的中等甚至甚至冲击时应进行静强度核算。作用次数超过上述表中规定的载荷应纳入疲劳强度计算。
9.1 载荷及其修正系数
9.2.1 载荷
应取载荷谱中或实测的最大载荷来确定计算切向力。当无上述数据可用时,可取预期的最大载荷Tmax(如起动转矩、堵转转矩、短路或其他最大过载转矩)为静强度计算载荷。
计算切向力和最大转矩的关系式如下:
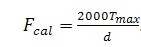
…………………………………………………………(253)
式中:Fcal——计算切向载荷,N;
d——齿轮分度圆直径,mm;
Tmax——最大转矩,N·m。
9.2.2 修正载荷的系数
a)因已按最大载荷计算,取使用系数KA=1。
b)对在起动或堵转时产生的最大载荷或低速工况,可取动载系数KV=1;其余情况KV按6.2取值。
c)齿向载荷分布系数FHβ,KFβ见6.3,但此时单位齿宽载荷应取 。
d)齿向载荷分配系数FHa,KFa取值同6.4。
9.3 静强度核算公式
9.3.1 齿面静强度核算
齿面静强度必须保证:
σHst≤σHPst…………………………………………………….(254)
当大、小齿轮材料σHPst不同时,应取小者进行核算。
式中:σHst——静强度最大齿面应力,N/mm2,见9.3.1.1;
σHPst——静强度许用齿面应力,N/mm2,见9.3.1.2。
9.3.1.1 静强度最大齿面应力σHst

………………………………(254)
式中KV,KHβ,KHa取值见9.2.2,ZH,ZE,Zε,Zβ及u,b等代号意义及计算同7.1和4.1。
9.3.1.2 静强度许用齿面接触应力σHPst
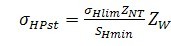
…………………………………………(256)
式中:σHlim——接触疲劳极限应力,N/mm2,见8.1;
ZNT——静强度接触寿命系数,此时取NL=N0,见表25;
ZW——齿面工作硬化系数,见8.4;
SHlim——接触强度最小安全系数,参见附录A。
9.3.2 弯曲静强度核算
弯曲静强度应保证:
σFat≤σFPst………………………………………………..(257)
式中:σFat——静强度最大齿根弯曲应力,N/mm2,见9.3.2.1
σFPst——静强度许用齿根弯曲应力,N/mm2,见9.3.2.2。
9.3.2.1静强度最大齿根弯曲应力σFat
9.3.2.2静强度最大齿根弯曲应力σFPst

…………………………………………………(260)
式中:
σFlim——弯曲疲劳极限应力,N/mm2,见8.1;
YST——试验齿轮的应力修正系数,如用本标准给出的σFlim值计算时,YST =2.0;
YNT——弯曲强度寿命系数,此时取NL=N0,见8.2表26;
YσrelT——相对齿根圆角敏感系数,见8.6;
SFlim——弯曲强度最小安全系数,参见附录A。
附录A
最小安全系数参考值15]
使用要求 |
最 小 安 全 系 数 |
SFmin |
SHmin |
高可靠度 |
2.00 |
1.50~1.60 |
较可靠度 |
1.60 |
1.25~1.30 |
一般可靠度 |
1.25 |
1.00~1.10 |
低可靠度 |
1.00 |
0.85 |
注
1 在经过使用使用验证或对材料强度、载荷工况及制造精度拥有较准确的数据时,可取表中SFmin下限值。
2 一般齿轮传动不推荐采用低可靠度的安全系数值。
3 采用低可靠度的接触安全数值时,可能在点蚀前先出现齿面塑性变形。 |
15]附录A表中各SFmin推荐值是根据ISO6336:1996规定SFmin=1.25,经理论分析论证并参考权威的经验数据确定的。
附录B
(提示的附录)
在变动载荷下工作的齿轮强度核算16] (16]等效采用ISO/DTR10495:1995。)
B1 有载荷图谱的强度计算
当齿轮在变动载荷下工作且有载荷图谱(示意图见图B1)可用时,应按Palmgreen-Miner定则核算其不同载荷水平下的应力及其疲劳累积损伤计算的强度安全系数。上述定则假定:齿轮在一系列不同的重复应力水平下工作所造成的疲劳累积损伤度,等于每一个应力水平的应力循环次数与材料应力-循环次数特性线(S-N曲线)上该应力水平对应的循环次数的比值之和(参见式(B2))。为了偏于安全,这里所谓的每一应力水平应取每一应力水平区间中的最大应力值。例如,在第i级应力水平下工作的循环次数为NLi,该应力水平所对应的S-N曲线上的应力循环次数为Ni,i=1,2,3,…,则有

……………………………………………..(B1)
U=∑Ui

……………………………………………………..(B2)
式中:Ui——在第i级应力水平下的疲劳损伤度;
U——齿轮疲劳累积损伤度。
为保证齿轮强度安全系数S≥1.0,则需有
U≤1.0…………………………………………………………(B3)
各应力水平区间的接触应力σHL和弯曲应力σFL分别按式(B4)、(B5)计算,大、小轮应分别计算。
图B1 工作载荷图谱示意图

……………………………..(B4)

………………………………………………..(B5)
式中:TL——应力水平区间内最大的小轮转矩,N·m;
d1——小轮分度圆直径,mm;
b——工作齿宽,mm;
ZBD——单对齿啮合系数ZB与ZD中之大值者,按5.1.5规定取值。
KVL,KHβL,KFβL,KHaL,KFaL是指在TL载荷下的KV,KHβ,KFβ,KHa,KFa值。各系数K及Y的定义见本标准正文第2章。
在计算各应力水平的σHL和σFL时,应取使用系数KA=1.0。
在S-N曲线上有
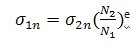
…………………………………………………..(B6)
式中:σ1n, σ2n——S-N曲线上点1、点2处的应力,N/mm2;
N1,N2——S-N曲线上点1、点2处的应力循环次数;
e——材料指数。
对接触强度

………………………………………………………..(B7)
对弯曲强度

………………………………………………………..(B8)
Pi值见表B1。
因此,在变动载荷工况下且有工作载荷谱可用时,齿轮的强度安全系数S可按下式计算:

………………………………………………………….(B9)
亦即
对接触强度

………………………………………………………..(B10)
对弯曲强度

………………………………………………………..(B11)
为保证齿轮安全工作,需要足本标准(正文)的式(2)式(10),即
和
式中SHmin和SFmin分别是接触强度和弯曲强度的最小安全系数值,参见附录A。
表B1 材料疲劳曲线指数pi
计算类别 |
材料及其热处理 |
工作循环次数NL |
pi |
接触强度 |
结构钢;调质钢;
球墨铸铁(珠光体、贝氏体);
珠光体可锻铸铁;
渗碳淬火的渗碳钢;
感应淬火或火焰淬火的钢、球墨铸铁 |
允许有一定点蚀时 |
6×105<NL≤107 |
6.77 |
107<NL≤109 |
8.78 |
109<NL≤1010 |
7.08 |
不允许出现点蚀 |
105<NL≤5×107 |
6.61 |
5×107<NL≤107 |
16.30 |
灰铸铁、球墨铸铁(铁素体);
渗氮处理的渗氮钢、调质钢、渗碳钢 |
105<NL≤2×106 |
5.71 |
2×106<NL≤1010 |
26.20 |
氮碳共渗的渗氮钢、渗碳钢 |
105<NL≤2×106 |
15.72 |
2×106<NL≤1010 |
26.20 |
弯曲强度 |
球墨铸铁(珠光体、贝氏体);
珠光体可锻铸铁;调质钢; |
104<NL≤3×106 |
6.23 |
3×106<NL≤1010 |
49.91 |
渗碳淬火的渗碳钢;火焰淬火、全齿廓感应
淬火的钢、球墨铸铁 |
103<NL≤3×106 |
8.74 |
3×106<NL≤1010 |
49.91 |
灰铸铁、球墨铸铁(铁素体);结构钢;
渗氮处理的渗氮钢、调质钢、渗碳钢 |
103<NL≤3×106 |
17.03 |
3×106<NL≤1010 |
49.91 |
氮碳共渗的渗氮钢、渗碳钢 |
103<NL≤3×106 |
84.00 |
3×106<NL≤1010 |
49.91 |
B2 无载荷图谱时的强度核算
在变动载荷下工作的齿轮又缺乏载荷图谱可用时,可近似地用常规的方法即用名义载荷乘以使用系数KA来确定计算载荷。当无合适的数值可用时,使用系数KA可参考本标准第6章表3确定。这样,就将变动载荷工况转化为变动载荷工况来处理,并按本标准正文中各章的有关公式核算齿轮强度。
附录C
轮缘系数YB17]
C1 概述
计算分析表明,当齿轮的轮缘厚度SR相对地小于轮齿全齿高ht时(SR及ht意义见C1),轮齿的齿根弯曲应力将明显增大。光弹实验和有限元分析均指出:当轮缘齿高比mB=SR/ht≥2.0时,mB对齿根弯曲应力没有影响。在mB=1.0~2.0区间,齿根弯曲应力开始增大。图C1是经分析归纳得出轮缘系数YB与轮缘高比mB的关系曲线,它由以mB=1.0和1.56为折点的三段直线组成。
需指出,轮缘系数YB没有考虑加工台阶、缺口、箍环、键槽等结构影响对齿根弯曲应力的影响。
C2 轮缘系数YB
在薄轮缘齿轮根应力基本值计算时,应增加一项轮缘系数YB,用以考虑轮缘齿高比mB对齿根弯曲应力的影响。即对用方法一[见4.2.2a]计算σF0时,本标准中式(12)应改写成
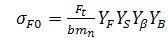
…………………………….(C1)
或采用方法二[见4.2.2a]计算σF0时,公式(13)应改写成

…………………………….(C2)
式中:σF0——齿根应力基本值,N/mm2;
b——齿轮宽度,mm;
mn——齿轮模数,mm;
YF,YFa——弯曲强度计算方法一及方法二的齿形系数,见7.2.1;
YS, YSa——弯曲强度计算方法一及方法二的应力修正系数,见7.2.2;
Yβ——弯曲强度计算的螺旋角系数,见7.2.4;
Yε——弯曲强度计算的重合度系数,见7.2.3。
轮缘系数YB可按式(C3)~(C5)计算或由图C1查取。
当mB<1.0时,
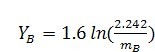
…………………………………………….(C3)
当1.0≤mB<1.56时,
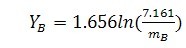
…………………………………………….(C4)
当mB≥1.56时,
YB=1.0…………………………………………….(C5)
图C1 轮缘系数 YB
采用说明:
17]ISO 6336中弯曲应力计算未给出SR≤3.5mn时的公式。此附录等效采用AGMA2010-C95中的处理方法并根据ISO限用条件拟合了当1.0≤mB<1.56的YB公式。