圆柱齿轮、锥齿轮和准双曲面齿轮胶合承载能力计算方法
第1部分:闪温法
1 范围
GB/Z 6413本部分根据布洛克接触温度的概念规定了评价胶合危险的方法和公式。
布洛克的基本概念应用于具有移动接触区的所有机械零件。闪温公式对于带状或近似带状的赫兹接触区与足够高的佩克莱特(peclet)数为特征的工作条件下是有效的。
2规范性引用文件
下列文件中的条款通过GB/Z6413本部分的引用而成为本部分的条款,凡是注日期引用文件,其随后的修改单或修订版均不适用于本部份,然而,鼓励根据本部分达成协议的各方研究是否可使用这些文件的最新版本。凡是不注日期的引用文件,其最新版本适用于本部分。
GB/T3374—1992 齿轮基本术语(neq ISO/R1122-1:1983)
GB/T3480—1997 渐开线圆柱齿轮承载能力计算方法(eqv ISO6336-1~6336-3:1996)
GB/T3481—1997 齿轮轮齿磨损和损伤术语(idt ISO 10825:1995)
GB/T10062.1—2003 锥齿轮承载能力计算方法 第1部分:概述和通用影响系数(ISO 10300-1:2001,IDT)
3 术语、定义、代号和单位
3.1 术语和定义
GB/T3374和GB/T3481中给出的术语和定义适用于本部分。
3.2代号和单位
本部分所使用的代号见表1。根据通常做法,长度单位选用米、毫米、和微米。为了整个体系的协调性,BM、Cγ和XM的单位适合于米和毫米或毫米和微米的混合使用。
表1 代号和单位
代 号 |
意 义 |
单 位 |
公式(图)号 |
a |
中心距 |
mm |
式(A.5) |
B |
齿宽,取大轮和小轮中的较小值 |
mm |
式(11) |
Beff |
有效齿宽 |
mm |
式(12) |
bH |
赫兹接触区宽度的一半 |
mm |
式(3) |
BM |
热接触系数 |
N/(mm1/2·m1/2·s1/2·K) |
式(A.13) |
BM1 |
小轮的热接触系数 |
N/(mm1/2·m1/2·s1/2·K) |
式(3) |
BM2 |
大轮的热接触系数 |
N/(mm1/2·m1/2·s1/2·K) |
式(3) |
Ca1 |
小轮的齿顶修缘量 |
μm |
式(48) |
Ca2 |
大轮的齿顶修缘量 |
μm |
式(46) |
Ceff |
最佳齿顶修缘量 |
μm |
式(46) |
Ceq1 |
小轮的当量齿顶修缘量 |
μm |
式(B.2) |
Ceq2 |
大轮的当量齿顶修缘量 |
μm |
式(B.3) |
Cf1 |
小轮的齿根修缘量 |
μm |
式(B.3) |
Cf2 |
大轮的齿根修缘量 |
μm |
式(B.2) |
CM1 |
小轮单位质量的比热 |
J/(kg·K) |
式(9) |
CM2 |
大轮单位质量的比热 |
J/(kg·K) |
式(10) |
C |
啮合刚度 |
N/(mm·μm) |
式(B.1) |
d1 |
小轮的分度圆直径 |
mm |
式(34) |
d2 |
大轮的分度圆直径 |
mm |
式(35) |
da1 |
小轮的齿顶圆直径 |
mm |
式(34) |
da2 |
大轮的齿顶圆直径 |
mm |
式(35) |
E1 |
小轮的弹性模具 |
N/mm2 |
式(A1.0) |
E2 |
大轮的弹性模具 |
N/mm2 |
式(A1.0) |
Er |
当量弹性模具 |
N/mm2 |
式(A.9) |
Fex |
外加轴向力 |
N |
式(A18) |
Fn |
磨损试验中的法向载荷 |
N |
图1 |
Ft |
名义切向力 |
N |
式(11) |
H1 |
辅助参数 |
mm |
式(B.3) |
H2 |
辅助参数 |
mm |
式(B.2) |
ham1 |
小齿轮齿宽中点齿顶高 |
mm |
式(43) |
Ham2 |
大齿轮齿宽中点齿顶高 |
mm |
式(44) |
KA |
使用系数 |
—— |
式(11) |
KBa |
胶合承载能力计算的齿间载荷分配系数 |
—— |
式(11) |
KBβ |
胶合承载能力计算的齿间载荷分布系数 |
—— |
式(11) |
KHa |
接触强度计算的齿间载荷分配系数 |
—— |
式(15) |
KHβ |
接触强度计算的齿间载荷分布系数 |
—— |
式(14) |
Kmp |
分支系数 |
—— |
式(11) |
KV |
动载系数 |
—— |
式(11) |
mn |
法向模数 |
mm |
式(B.2) |
n1 |
小齿轮转速 |
r/min |
式(5) |
np |
啮合分支数 |
—— |
式(16) |
Pe1 |
小轮材料的佩克莱特数 |
—— |
式(9) |
Pe2 |
大轮材料的佩克莱特数 |
—— |
式(10) |
Q |
质量等级 |
—— |
式(57) |
Ra1 |
小轮齿面的粗糙度 |
μm |
式(28) |
Ra2 |
大轮齿面的粗糙度 |
μm |
式(28) |
Rm |
中点锥距 |
mm |
式(A.16) |
rm1 |
小轮齿宽中点分度圆半径 |
mm |
式(43) |
rm2 |
大轮齿宽中点分度圆半径 |
mm |
式(44) |
SB |
胶合承载能力计算的安全系数 |
—— |
式(100) |
SFZG |
FZG试验的载荷级 |
—— |
式(99) |
t1 |
小轮的瞬时接触时间 |
μs |
式(95) |
t2 |
大轮的瞬时接触时间 |
μs |
式(96) |
tc |
曲线弯曲处的瞬时接触时间 |
μs |
式(97) |
tmax |
最长瞬时接触时间 |
μs |
式(95) |
u |
齿数化 |
—— |
式(A.6) |
uv |
当量齿数比 |
—— |
式(B.6) |
vg |
滑动速度 |
m/s |
图1 |
vg1 |
小轮的切向速度 |
m/s |
式(3) |
Vg2 |
大轮的切向速度 |
m/s |
式(3) |
Vg∑C |
节点处的切向速度总和 |
m/s |
式(25) |
vt |
节圆线速度 |
m/s |
式(26) |
wBn |
法向单位载荷 |
N/mm |
式(3) |
wBt |
端面单位载荷 |
N/mm |
式(5) |
Xbut |
支撑系数 |
—— |
式(54) |
XbutA |
A点的支撑值 |
—— |
式(51) |
XbutB |
B点的支撑值 |
—— |
式(51) |
XG |
几何系数 |
—— |
式(A.5) |
XJ |
啮入系数 |
—— |
式(3) |
XL |
润滑剂系数 |
—— |
式(25) |
XM |
热弹系数 |
K·N-3/4·s-1/2·m-1/2·mm |
式(5) |
Xmp |
多点啮合小轮系数 |
—— |
式(22) |
XR |
粗糙度系数 |
—— |
式(25) |
XS |
润滑方式系数 |
—— |
式(22) |
WX |
组织系数 |
—— |
式(94) |
Xaβ |
角度系数 |
—— |
式(A.6) |
Xг |
载荷分担系数 |
—— |
式(3) |
XΘ |
胶合温度梯度 |
—— |
式(97) |
z1 |
小轮齿数 |
—— |
式(30) |
z2 |
大轮齿数 |
—— |
式(30) |
aa1 |
小轮端面齿顶圆压力角 |
( °) |
式(31) |
aa2 |
大轮端面齿顶圆压力角 |
( °) |
式(30) |
at |
端面压力角 |
( °) |
式(34) |
awn |
法面啮合角 |
( °) |
式(A.2) |
awt |
端面啮合角 |
( °) |
式(7) |
ay1 |
小轮任意点压力角 |
( °) |
式(29) |
β |
螺旋角 |
( °) |
式(18) |
βb |
基圆螺旋角 |
( °) |
式(49) |
βbm |
齿宽中点基圆螺旋角 |
( °) |
式(50) |
βw |
啮合螺旋角 |
( °) |
式(A.2) |
гA |
啮合线上A点的参数 |
—— |
式(24) |
ГAA |
啮合线上AA点的参数 |
—— |
式(68) |
ГAB |
啮合线上AB点的参数 |
—— |
式(66) |
ГAU |
啮合线上AU点的参数 |
—— |
式(49) |
ГB |
啮合线上B点的参数 |
—— |
式(31) |
ГBB |
啮合线上BB点的参数 |
—— |
式(70) |
ГD |
啮合线上D点的参数 |
—— |
式(32) |
ГDD |
啮合线上DD点的参数 |
—— |
式(72) |
ГDE |
啮合线上DE点的参数 |
—— |
式(67) |
ГE |
啮合线上E点的参数 |
—— |
式(24) |
ГEE |
啮合线上EE点的参数 |
—— |
式(74) |
ГEU |
啮合线上EU点的参数 |
—— |
式(49) |
ГM |
啮合线上M点的参数 |
—— |
式(86) |
Гy |
啮合线上任意点的参数 |
—— |
式(7) |
γ1 |
小轮切向速度的方向夹角 |
—— |
式(3) |
γ2 |
大轮切向速度的方向夹角 |
—— |
式(3) |
δ1 |
小轮节锥角 |
( °) |
式(37) |
δ2 |
大轮节锥角 |
( °) |
式(39) |
εa |
端面重合度 |
—— |
式(76) |
εβ |
纵向重合度 |
—— |
式(52) |
ηoil |
润滑油在工作温度下的绝对(动力)黏度 |
mpa·s |
式(27) |
ΘB |
接触温度 |
℃ |
式(1) |
ΘBmax |
接触最大接触温度 |
℃ |
式(2) |
Θfl |
闪温 |
K |
式(1) |
Θflm |
平均闪温 |
K |
式(22) |
Θflmax |
最大闪温 |
K |
式(2) |
ΘflmaxT |
试验时的最大闪温温度 |
K |
式(94) |
ΘM |
本体温度 |
℃ |
式(22) |
ΘMi |
接触面的本体温度 |
℃ |
式(1) |
ΘM1 |
小轮轮齿的本体温度 |
℃ |
式(20) |
ΘM2 |
大轮轮齿的本体温度 |
℃ |
式(20) |
ΘMT |
试验时的本体温度 |
℃ |
式(94) |
Θoil |
进入啮合前的油温 |
℃ |
式(22) |
ΘS |
胶合温度 |
℃ |
式(94) |
ΘSc |
较长接触时间的胶合温度 |
℃ |
式(97) |
λM1 |
小轮的热传导系数 |
N/(s·K) |
式(9) |
λM1 |
大轮的热传导系数 |
N/(s·K) |
式(10) |
μ |
柱——环试验的磨擦因数 |
—— |
图1 |
μm |
平均磨擦因数 |
—— |
式(3) |
V1 |
小轮材料的泊松比 |
—— |
式(A.10) |
V2 |
大轮材料的泊松比 |
—— |
式(A.10) |
ρM1 |
小轮材料的密度 |
Kg/m3 |
式(9) |
ρM2 |
大轮材料的密度 |
Kg/m3 |
式(10) |
ρrelC |
节点处的相对曲率半径 |
mm |
式(25) |
ρy1 |
小轮任意点处的曲率半径 |
mm |
式(5) |
ρy2 |
大轮任意点处的曲率半径 |
mm |
式(5) |
ρyrel |
任意点处的相对曲率半径 |
mm |
式(5) |
∑ |
轴交角 |
( °) |
式(A.15) |
Φ |
齿轮空心套轴的扭转角 |
( °) |
式(17) |
4 胶合和磨损
4.1胶合和磨损的产生
当齿轮轮齿完全被润滑油膜分开时,两齿面的凹凸不平之间是不接触的,通常不存在胶合和磨损,此时的磨擦因数相当小。在油膜较厚时,由于突然的热不稳定性[19]引起的类似胶合损伤的这种特殊情况不在此讨论。
当弹性流体动力油膜较薄时,齿面凹凸之间偶尔会直接接触,随着平均油膜厚度的减薄,直接接触的次数相应增加,则可能会产生磨料磨损、粘着磨损或胶合。由于齿轮轮齿的滚动作用或润滑油中含有磨粒会引起磨料磨损。粘着磨损是由先局部焊合,随即分离,从而导致一个或两个啮合轮齿上的材料微粒转移而引起的。如果磨粒磨损或粘着磨损是轻微的,且随着时间的推移而减轻,作为一种正常跑合过程则对轮齿不会造成危害。
与轻微磨损不同,胶合是能导致轮齿扩展性损伤的黏着磨损的严重形式。与具有明显发展期的点蚀和疲劳折断不同,瞬时过载会导致胶合失效。
润滑油中过分进气或存在污染,诸如悬浮的金属颗粒或水,也会增加胶合的危险。高速齿轮胶合后,由于振动而引起更大的动载荷,振动通常会导致进一步的胶合、点蚀、断齿损伤。
在大多数情况下,使用具有增强抗胶合添加剂1)的润滑油能提高齿轮抗胶合承载能力,然而,重要的一点是要意识到使用抗胶合添加剂的一些不足之处:使铜腐蚀、弹性材料的脆化,以及缺乏全球通用性等。
本方法不适用于评价冷胶合,冷胶合通常在低速(节圆线速度小于4m/s)、质量很差的调质重载齿轮上产生。
4.2转换图
在使用液体润滑油润滑的运行条件下,较严重的钢接触滑动的润滑状况可用转换图描述[20][21][22][23]。图1所示的转换图适用于恒定油浴温度下的接触运行。
当法向力Fn和相对滑动速度vg同时落在A1-S线以下,即图1的Ⅰ区时,润滑状况的特征可用磨擦因数大约为0.1、单位磨损率(即:每单位法向力、每单位滑动距离下的体积磨损量)为10-2~10-6mm3(N·m)来表达。
当vg不大于S点的值,且载荷增加进入Ⅱ区时,刚转换进入第二种润滑状况。这种轻微磨损润滑条件的特征可用磨擦因数大约为0.3~0.4、单位磨损率为1~5 mm3(N·m)来表达。
图1具有计算接触温度实例的逆向形状转换图
如果载荷进一步增加,则转换进入第三种润滑状况,即进入以A2-S为边界线的Ⅲ区。这个区域的特征可用磨擦因数等于0.4~0.5来表达,然而,与Ⅰ区和Ⅱ区相比磨损率相当高,从100~1000 mm3(N·m)。磨损表面呈现胶合形式的严重磨损。当相对滑动速度超过S点后,如果载荷增加,则直接从Ⅰ区转换到Ⅲ区。
有足够的证据证明A1-S-A3线的位置取决于润滑油黏度[24]及赫兹接触压力[20][21]。当Fn和vg同时落在此线以下时,则认为,齿面由一层较薄的润滑油膜分隔开,但此膜被粗糙的凹凸部分所穿透。对于这种情况,称为“边界弹流动力润滑”[21]。
在Ⅲ区中,液体油膜完全推动了作用,这个区域即为“初始胶合”区域[25]。有证据表明以A2-S线为边界发生的转换与接触温度达到临界值相关。这就是布洛克的基本概念。
给出的这个转换图适用于新的组件(即未氧化钢的接触),如齿轮、凸轮及从动件等。这个转换图符合四球试验及柱——环试验的结果。
沿A1-S-A3曲线的温度范围(从油池温度开始,依次为整个本体温度,接触面本体温度):在vg=0.001m/s时为28℃到vg=10m/s时的接触温度为498℃。这个温度特性充分表明在恒定的接触或接触面本体温度下,(边界)弹流动力润滑未被破坏,例如与化学吸附性材料的软化有关。相反,随着滑动速度的增加承载能力的明显降低则认为是由于润滑油黏度的降低[24] [24] [26] [27] [28] [29]。
与上述情况不同,沿曲线A2-S-A3的计算接触温度则趋向于一个恒定的值,即用GCr15钢时大约为500℃,见图1。这表明从Ⅱ区到Ⅲ区的转换与用钢的不同有关,从轻微粘着到严重粘着,引起了表面磨损机理的变化,也许还包括热弹不稳性机理[30][31]。
因此,结果表明胶合与接触温度的临界值有关。对于钢,用矿物油润滑时,临界值大约为500℃,它并不取决于载荷、速度和几何参数。
4.3初始胶合时的磨擦
在图1所示的转换图中,胶合时,磨擦因数从0.25跳跃到0.5。相应的接触温度大约为500℃。这个接触温度是测量的接触面的本体温度28℃与计算的闪温470℃的和。
在计算闪温时所用的磨擦因数是刚要转换前的磨擦因数,即μ=0.35。如果这种方法不仅要用于柱与环实验而且还要用于齿轮传动(在设计阶段)时,在计算中接触温度的临界值和磨擦因数值的选取应协商一致。
齿轮承载能力可以预估:
——当使用磨擦因数μ=0.5时,偏于安全;
——根据润滑油的不同,所使用的磨擦因数为μ=0.25μ~=0.35时,较精确;
——根据以前的经验,在稳定的工作条件下,所用的磨擦因数较低,那么限定的接触温度相应地也较低。
根据经验,对于不加和加少量添加剂和矿物油,油和滚动材料的每一种组合有一个临界胶合温度。通常,这个温度是恒定的,与运行条件、载荷、速度和几何参数无关。
对于加大量添加剂的矿物油和一些种类的复合油,临界胶合温度随着装置运行条件变化而变化。因此,此时的临界温度必须由模拟齿轮装置运行条件的实验分别确定。
5 基本公式
5.1 接触温度
在引言中已经叙述过,接触温度是接触面的本体温度ΘMi(见5.4)和闪温Θfl(见5.2)之和。
ΘB=ΘMi+Θfl……………………………………..(1)
闪温温度沿接触轨迹的变化见图2。
最大接触温度为:
ΘBmax=ΘMi+Θflmax……………………………………..(2)
式中:
Θflmax——Θfl的最大值,它不是位于啮入轨迹上就是位于啮出轨迹上。
胶合的可能性可通过计算最大接触温度和其临界值的比较进行预测。接触温度的临界值可通过齿轮胶合实验确定,或通过使用现场的调查研究确定。
a 在啮合线上的位置
图2沿接触轨迹的接触温度
对于胶合危险性的可靠评价,重要的是在分析中,要使用齿轮本体温度的精确值。
5.2闪温公式
对于(近似)带状接触区和不同方向的切向速度(如准双曲面齿轮),布洛克闪温公式[12][14][16][32]最常用的表达式见附录A,即:

……………….(3)
对于具有带状接触区和切向速度平行的圆柱齿轮和锥齿轮,常用的表达式见附录A,即:

…………………………….....(4)
或用等效表达式:

………(5)
式中:
μm——平均磨擦因数(见第6章);
XM——热弹系数(见附录A),对于常用钢:XM=50K·N-3/4·S1/2·m-1/2·mm;
XJ——啮入系数(见第8章);
Xг——载荷分担系数(见第9章);
wBt——端面单位载荷(见5.3),单位为牛每毫米(N/mm);
n1——小轮转速,单位为转每分(rimin);
ρyrel——局部相对曲率半径,单位为毫米(mm);

……………………………….(6)
ρy1——小轮齿廓局部曲率半径,单位为毫米(mm);
对圆柱齿轮:
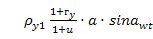
…………………(7)
ρy2——小轮齿廓局部曲率半径,单位为毫米(mm);
对圆柱齿轮:
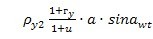
…………………(8)
对于锥齿轮,ρy1和ρy2见式(37)和式(38)。
对于Θn更适用的表达形式,见附录A。
两个佩克莱特数必须足够高,以使它能满足几乎所有可能发生胶合的情况。当佩克莱特数较低时,热量从接触带区流向整个轮齿,引起不同的温度分布,此时式(3)和式(6)无效。

……………………..(9)
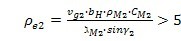
……………………..(10)
式中:
ρM1——小轮材料的密度,单位为千克每立方米(kg/m3);
ρM2——大轮材料的密度,单位为千克每立方米(kg/m3);
CM1——小轮单位质量的比热,单位为焦耳每千克开尔文[J/(kg·K)];
CM2——大轮单位质量的比热,单位为焦耳每千克开尔文[J/(kg·K)];
λM1——小轮的热导率,单位为千每秒开尔文[N/(S·K)];
λM2——大轮的热导率,单位为千每秒开尔文[N/(S·K)];
对于圆柱齿轮和锥齿轮sinγ1= sinγ2=1.
5.3 端面单位载荷
圆柱齿轮端面单位载荷:

……………………………(11)
锥齿轮端面单位载荷:

……………………………(12)
式中:
Ft——节圆上的名义切向力,单位为牛(N);
b——齿宽,单位为毫米(mm);
beff=0.85b……………………………………(13)
KA——使用系数(对于圆柱齿轮,见GB/T3480,对于锥齿轮,见GB/T10062.1);
KV——动载系数(对于圆柱齿轮,见GB/T3480,对于锥齿轮,见GB/T10062.1);
KBβ——胶合承载能力计算的齿向载荷分布系数;
KBβ= KHβ………………………………………..(14)
圆柱齿轮和锥齿轮的KHβ分别见GB/T3480和GB/T10062.1);
KBa——胶合承载能力计算的齿间载荷分配系数;
KBa= KHa…………………………………………..(15)
圆柱齿轮和锥齿轮的KHa分别见GB/T3480和GB/T10062.1);
Kmp——分支系数。
分支系数Kmp是考虑多分支传动时,每个分支上载荷分配不均匀的系数。如果没有可靠的分析数据可用时,可用下列方法确定:
——对于具有np(np3)个行星齿轮的行星齿轮传动:

……………………………………(16)
——对于在满载下,齿轮空心轴扭转角为Φ(°)的双联齿轮:
Kmp =1+(0.2/Φ) …………………………………………(17)
——对于外加轴向力为Fex的双斜齿轮:
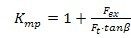
………………………………………………(18)
——对于其他情况:
Kmp =1……………………………………………(19)
5.4 本体温度的分布
齿轮传动最主要的磨擦损失是轮齿啮合区的磨擦损失。其损失形式主要由于轮齿的磨擦而产生热量。由于多余的供油侧面排放消耗的机械“泵”能,有时不能忽略。由轴承(滚动轴承或滑动轴承)产生的损失是另一种不可避免的磨擦损失。对于高速齿轮传动,滑动轴承产生的热量可能比齿轮啮合产生的热量大得多。另一些热源是搅油和油封的磨擦。所有以上热源有下列共同特点:
——对于每种热源,流体的磨擦取决于各自动转条件下的润滑油黏度;
——所有热源的热量是相互联系的,通过传动元件到散热装置,如周围的空气或冷却系统。
热量的相互联系可用下列计算方法:
——离散组元的有限元法;
——扩散图法;
——热网络类比法[18]。
接触面的本体温度ΘMi可能适当地取两个相接触轮齿的整体本体温度ΘM1和ΘM2的平均值。
下式为较精确的近似公式(在佩克莱特数较高时):
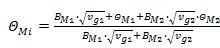
……………………………(20)
当 的比值在一个相当广的范围内时,可用简单的数学平均式来近似计算:

………………………………………(21)
当闪温长期超过150℃时,可能对齿面疲劳有不利的影响。
5.5 本体温度的粗略近似
为了粗略地研究本体温度,可用油温(要考虑喷油润滑对热传递带来的一些阻碍因素)加上决定闪温温度的那一部分取最大值之和来估算。
ΘM=Θoil+0.47Xs·Xmp·Θflm…………………………..(22)
式中:
对于喷油润滑:Xs =1.2;
对于油浴润滑:Xs =1;
对于具有附加喷油润滑冷却的啮合:Xs =1.0;
对于为提供足够的冷却而将齿轮浸没在油中时:Xs =0.2;
对于一个小轮与np个大轮啮合:

………………………………………(23)
Θflm——沿接触轨迹的平均闪温,单位为摄氏度(℃)
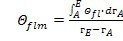
………………………………..(24)
然而,为了可靠地评价胶合的危险性,重要的是在分析中,要用齿轮本体温度的精确值来替代粗略的近似值。
6 磨擦因数
在一个啮合周期内,影响齿轮轮齿间磨擦的一些因素是变化的。两个啮合齿面间存在相对运动,且在一个齿面是均匀的加速,而在别一个齿面上是均匀的减速。仅在节点位置是纯滚动。在任何其他位置都存在滚动和滑动。作用在两啮合齿面上的载荷也随着啮合位置的变化而变化。这些因素引起油膜厚度、润滑状态和磨擦因数的连续变化。即使在相同的啮合位置,对于不同的轮和不同时间,磨擦因数也可能是变化的。
为消除各种影响,认为局部磨擦因数适用于相关局部点处磨擦因数的示值。通过计算或测量来几何确定局部磨擦因数的变化是很困难的。因此,用代表性的磨擦因数的平均值来代替局部磨擦因数的值。
通常所使用的是磨擦因数的平均值(沿接触轨迹),即使这个值是变化的。在实验报告中,常常忽略了一些重要的影响因素,例如确定入口黏度的本体温度和润滑状况。
平均磨擦因数2)(2)平均磨擦因数定义为沿接触轨迹局部磨擦因数的平均值。尽管节点处的实际局部磨擦因数与定义在整个接触轨迹上的平均磨擦因数不同,但平均磨擦因数可按节点来表达。)μm取决于端面啮合线的几何参数、切向速度、法向载荷、入品黏度(相同于轮齿在本体温度处的黏度)、压黏系数、当量弹性模量、表面粗糙度、法向相对曲率半径。其他的一些影响因素(如公式中的和使用现场的)也必须要考虑,当然,要取决于进一步的研究。通过量纲的分析[33],有些很小的影响量可能被略去,影响量的数目可能会减少。
可用各种方法来测量和估算磨擦因数,应根据磨擦因数来选择极限接触温度。
6.1 平均磨擦因数,A法
用齿轮实验或柱——环实验方法测出开始胶合时的磨擦因数。此法的极限接触温度相对较高。
6.2 平均磨擦因数,B法
根据经验,在有规则的工作条件下使用较小的磨擦因数,最后计算磨擦因数可用一些合适的公式进行,即这些公式包含了相当于齿轮本体温度的绝对(动力)黏度ηL。此法的极限接触温度相对较低,见第10章。
6.3 平均磨擦因数,C法
如果计算开始时,还不知道本体温度,通常工作条件下的平均磨擦因数可用下式计算:

……………………………(25)
式中:
wBt——切向单位载荷,见式(11)或式(12),单位为牛每毫米(N/mm);
vg∑C——节点的切向速度之和,单位为米每秒(m/s);
vg∑C =2·vt·sinawt………………………………(26)
vt——节圆线速度,单位为米每秒(m/s),如果vt>50m/s时,在式(26)中取vt=50m/s;
ρrelC——端面相对曲率半径(当гy=0时,按式(6)计算),单位为毫米(mm);
XL——润滑剂系数:
对于矿物油:XL=1.0(ηoil)-0.05
对于水溶性聚(乙)二醇:XL=0.6(ηoil)-0.05
对于非水溶性聚(乙)二醇:XL=0.7(ηoil)-0.05
对于聚a稀族烃:XL=0.8(ηoil)-0.05 ……………………(27)
对于磷酸酯:XL=1.3(ηoil)-0.05
对于牵引液:XL=1.5(ηoil)-0.05
ηoil——在油温Θoil下的动力黏度,单位为毫帕秒(mPa·s);
XR——粗糙度系数
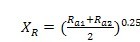
………………………………………..(28)
式中:
Ra1——跑合前的小轮齿面粗糙度Ra,单位为微米(μm)(适当跑合后Ra1可降低到初始值的大约60%);
Ra2——跑合前的小轮齿面粗糙度Ra,单位为微米(μm)(适当跑合后Ra2可降低到初始值的大约60%);
7 啮合线上的参数
啮合线上的点用无量纲线性参数гy来表示,在啮合线与小轮基圆的切点处гy为-1,在节点处гy为0[33],见图3。
a 基节
图3 啮合线上的参数
在接触轨迹上的任意点处:
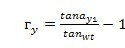
……………………………………………………(29)
在接触轨迹的下界点处:
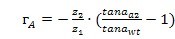
……………………………………………………(30)
在单对齿啮合区下界点处:
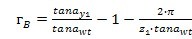
……………………………………………………(31)
在单对齿啮合区上界点处:
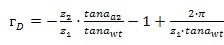
……………………………………………………(32)
在接触轨迹的上界点处:
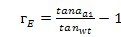
……………………………………………(33)
上述式中,齿顶压力角定义为:
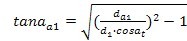
……………………………..(34)
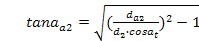
……………………………..(35)
锥齿轮的参数既可以用当量几何参数来计算(见GB/T 10062.1附录A),也可以用下述公式计算(也适用于轴交角∑=δ1+δ2不等于90°时的情况)。
在啮合线上的任意点处:
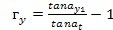
……………………………………………………(36)
ρy1=Rm·tanδ1·sinat·(1+гy) …………………………………………(37)
ρy2=Rm·tanδ1·sinat·(u+гy) …………………………………………(38)
在啮合线上的特征点处:

……………………………………………………(39)

……………………………………………………(40)

……………………………………………………(41)
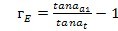
…………………………………………(42)
上述式中,压力角被定义为:

……………………………..(43)

……………………………..(44)
式中:
δ1——小轮的节锥角,单位为度(°);
δ2——大轮的节锥角,单位为度(°);
Rm——中点(齿宽中心)锥距,单位为毫米(mm);
ham1——小轮齿宽中点齿顶高,单位为毫米(mm);
ham2——大轮齿宽中点齿顶高,单位为毫米(mm);
rm1——小轮齿宽中点节圆半径,单位为毫米(mm);
rm2——大轮齿宽中点节圆半径,单位为毫米(mm)。
8 啮入系数
啮入系数是根据经验考虑,由于啮合开始时齿面上还未形成油膜而使胶合的危险性增加的系数。对于较大的齿轮其影响相对较大。
啮入系数为:
——对于小轮驱动大轮(减速)
当гy≥0时
XJ=1……………………………………(45)
当гy<0时

…………………….(46)
当гy≤0时
XJ=1……………………………………(47)
当гy>0时

…………………….(48)
式中:
Ceff——最佳齿顶修缘量(见附录B),单位为微米(μm);
Ca1——小轮的齿顶修缘量,单位为微米(μm);
Ca2——大轮的齿顶修缘量,单位为微米(μm);
当гy——啮合线上任意点的参数(见第7章);
当гA—啮合线上A点的参数(见第7章);
当гB—啮合线上B点的参数(见第7章)。
9 载荷分担系数
载荷分担系数Xг是考虑后续啮合的轮齿上的载荷分担的系数。根据常规,载荷分担系数表示为啮合线上的线性参数гy的函数。当前面的轮齿结束啮合时,在端面双齿啮合区的啮入轨迹上,载荷分担系数增加,当后面的轮齿进入啮合时,在端面双齿啮合区的啮出轨迹上,载荷分担系数减少。
由于前面啮合的轮齿的误差,可能引起理论载荷分担系数的瞬时增加或减少,这与由稍晚一点进入啮合的后续轮齿的误差引起的载荷分担系数的瞬时增加或减少无关。
对于圆柱齿轮,Xг的值不超过1.00,它指的是所有端面单对齿啮合区。由于动载荷不规则变化的位置可能引起端面单对齿啮合区的扩大。
载荷分担系数Xг取决于齿轮传动类型和齿廓修形。在有斜齿(偏向齿体内齿廓修形)支撑的情况下,载荷分担系数与支撑系数Xbut一起考虑。
齿廓修形(齿项修缘)公式见附录B。
9.1 支撑系数
对于斜齿轮,由于接触线的倾斜,在啮合线上的两端A点和E点附近可能有一个支撑的影响。这个影响适用于齿顶修缘量小于最佳值(Ca<Ceff)时的圆柱齿轮和锥齿轮。
支撑系数用Xbut表示,可简化为A-AU、AU-EU、EU-E范围内的线性函数,见图4。
图4 支撑函数
Xbut可用下述式子表达:
对圆柱齿轮
гAU-гA=гE-гEU=0.2sinβb…………………………………..(49)
对锥齿轮
гAU-гA=гE-гEU=0.2sinβb…………………………………..(50)
当εβ≥1时
XbutA=XbutE=1.3………………………………………………………….(51)
当εβ<1时
XbutA=XbutE=1+1.3εβ…………………………………………………..(52)
XbutAU=XbutEU=1………………………..…………………………………..(53)
对于гA≤гy<гAU时

…………………………………(54)
对于гAU≤гy≤гEU时
Xbut=1………………………..…………………………………..(55)
对于гEU<гy≤гE时

…………………………………(56)
9.2 齿廓未修形的直齿轮
通常认为齿廓未修形的直齿轮的载荷分担系数值是个不连续的矩形,见图5。然而,由于存在制造误差,在每个双啮区内,对于凸出的齿廓,载荷分担系数将增加,对于其他齿轮,载荷分担系数将减少[34]。不同精度等级齿轮的载荷分担系数是一个包络线族,见图6。
图5 齿廓未修形的直齿圆柱齿轮的载荷分担系数(精度等级Q为7级或7级以上)
图6 齿廓未修形的直齿圆柱齿轮的载荷分担系数(精度等级Q为8级或8级以上)
对于гA≤гy<гB
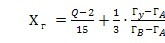
………………………………………(57)
对于гB<гy≤гD
Xг=1………………………..…………………………………..(58)
对于гD≤гy≤гE
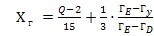
………………………………………(59)
当精度等级Q为7级或7级以上时
Q=7…………………………………………(60)
当精度等级Q为8级或8级以下时,取Q=精度等级。
9.3 齿廓修形的直齿轮
见图7和图8
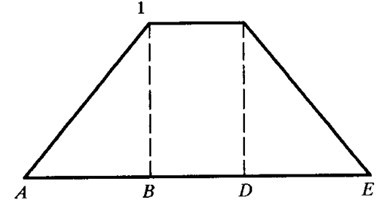
图7 具有最佳齿廓修形的直齿圆柱齿轮的载荷分担系数
图8 在A点附近具有偏向体外的齿廓修形,而在E点附近具有偏向体内的齿廓修形的直齿圆柱齿轮的载荷分担系数
对于гA≤гy≤гAB

………………………………………(61)
对于гAB≤гy≤гB

………………………………………(62)
对于гB≤гy≤гD

=1…………………………………………..(63)
对于гD≤гy≤гDE

………………………………………(64)
对于гDE≤гy≤гD

………………………………………(65)
гAB=0.5·(гA+гB)……………………………………………….(66)
гDE=0.5·(гD+гE)………………………………………………..(67)
对于Ca2>Ceff
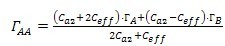
……………………………….(68)
对于Ca2≤Ceff
гAA=гA……………………………………………………………………..(69)
对于Ca1>Ceff

……………………………….(70)
对于Ca1≤Ceff
гBB=гB……………………………………………………………………..(71)
对于Ca2>Ceff
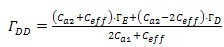
……………………………….(72)
对于Ca2≤Ceff
гDD=гD……………………………………………………………………..(73)
对于Ca1>Ceff

……………………………….(74)
对于Ca1<Ceff
гEE=гE……………………………………………………………………..(75)
9.4 齿廓未修形的窄斜齿轮
对于总重合度较小(εy<2)的斜齿轮仍然有单齿啮合区.因此,考虑到端面的几何参数以及支撑的影响,这种斜齿轮可以与直齿轮类似处理.见图9.
未修形的窄斜齿轮的载荷分担系数由9.2中的XГ乘以支撑系数Xbut获得.
图9齿廓未修形并考虑支撑影响的窄斜齿轮的载荷分担系数
9.5 齿廓修形的窄斜齿轮
总重合度较小(εy<2)的斜齿轮仍然有单齿啮合区.因此,考虑到端面的几何参数,这种斜齿轮可以与直齿轮类似处理.见图10和见图11.
这种齿轮的载荷分担系数由9.2中的XГ乘支撑系数Xbut获得.
图10 具有最佳或偏向体外的齿廓修形的窄斜圆柱齿轮的载荷分担系数
图11 具有偏向体内的齿廓修形的窄斜齿轮的载荷分担系数
9.6 齿廓未修形的宽斜齿轮
对于宽斜齿轮(εy<2),在倾斜接触线的末端,局部啮合刚度较高, , , , ,此时,假定支撑的影响[35]作用在沿斜齿的A点和E点附近的一个恒定长度上,这个长度相对于端面的长度为0.2sinβb,见图12、图4和9.1。
图12 齿廓未修形的圆柱宽斜齿轮的载荷分担系数
此时,载荷分担系数由表示平均载荷的值1/εa乘以支撑系数Xbut获得:
X
r=

……………………(76)
9.7 齿廓修形的宽斜齿轮
假定在接触轨迹两端的A-AB段和DE-E段的齿顶修缘长度相等,并导致未加载齿轮的商面重合度为ε
a=1,见图13。具有偏向体内或偏向体外齿廓修形的圆柱宽斜齿轮(ε
y>2)的载荷分担系数,在具有支撑影响的未修形齿廓和最佳齿廓修形的载荷分担系数之间分别用内插法或外插法确定,见图14。
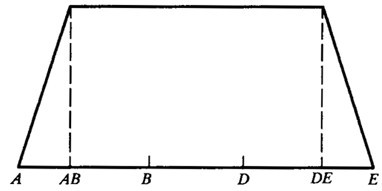
图13 具有最佳齿廓修形的圆柱宽斜齿轮的载荷分担系数
图14 在A点附近具有偏向体外、在E点附近具有偏向体内的
齿廓修形的圆柱宽斜齿轮的载荷分担系数
用以下的各点来区分这些不同的范围:
ГAB=0.5(ГA+ГB)………………………………….(77)
ГDE=0.5(ГD+ГE)………………………………….(78)
对于Ca2≥Ceff

………………….(79)
对于Ca1≥Ceff

………………….(80)
对于Ca1<Ceff,ГAA≤Гy≤ГAB或对于Ca2≥Ceff,ГA≤Гy≤ГAB

……………..(81)
对于Ca2<Ceff,ГAA≤Гy≤ГAB
XΓ=0…………………………………(82)
对于Ca2≥Ceff,ГAB≤Гy≤ГDE

………………….(83)
对于Ca1<Ceff,ГDE≤Гy≤ГE或对于Ca1≥Ceff,ГDE≤Гy≤ГEE

………………….(84)
对于Ca2≥Ceff, ГDE≤Гy≤ГEE
XГ=0………….………………………………….(85)
9.8 窄锥齿轮
具有齿廓修形(Ca2 <Ceff)的窄锥齿轮(εy<2),载荷分担系数XГ在按9.4计算的XГ(Ca=0)和按9.9计算的XГ(Ca= Ceff)之间用线性内插法确定。记住Xbut.
具有齿廓修形(Ca2≥Ceff) 的窄锥齿轮(εy<2),载荷分担系数XГ在按9.9计算。
9.9 宽锥齿轮
具有最佳齿廓修形(Ca1=Ceff ,Ca2=Ceff) 的宽锥齿轮,假定载荷分担系数为抛物线形[35],见图15。
中点M的定义为:

…………………….………………….(86)
图15具有最佳齿廓修形锥齿轮的载荷分担系数
最佳齿廓修形(C
a1=C
eff ,C
a2=C
eff)的载荷分担系数:
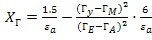
………………….(87)
如果齿廓修形量Ca1与Ca2不同,那么在M点曲线不连续,AM段和ME段应分别计算,见图16。
图16 在A点附近具有偏向体内的齿廓修形、在E点附近具有偏向体外的
齿廓修形锥齿轮的载荷分担系数
对于偏向体内的齿廓修形,载荷分担系数在具有支撑影响(见9.6)的未修形齿廓的载荷分担系数和最佳修形齿廓的抛物线形载荷分担系数之间用内插法确定。
对于偏向体外的齿廓修形,抛物线形有一个新的端点AA或EE。
对于偏向体内的齿廓修形,XГ在具有最佳齿廓修形的XГ(公式87)和齿廓未修形时的XГ(公式76)之间用线性内插法确定。插值确定应分段进行,即受Ca2影响的AM段和受Ca1影响的ME段。
对于偏向体内的齿廓修形,则有新的端点AA和EE。

…………………….………………….(88)

…………………….………………….(89)
对于ГA≤Гy≤ГAA
XГ=0………….………………………………….(90)
对于ГAA<ГA≤ГM

…………………….………(91)
对于ГM<ГA≤ГEE

…………………….………(92)
对于ГEE<Гy≤ГE
XГ=0………….………………………………….(93)
10胶合温度和安全性
10.1 胶合温度
胶合温度是根据所选择的润滑油和齿轮材料的组合可能发生胶合时的接触温度。认为一对齿轮的材料-润滑油-材料系统的胶合温度有一个特定的值,这个值由相同材料-润滑油-材料系统的齿轮试验来确定[36]。
当使用较低添加剂的矿物油时,认为在相当广的范围内胶合温度与工作条件无关。
当使用具有抗胶合或减磨添加剂的矿物油或合成油时,对于不同的材料和工作条件下,胶合温度可能是非恒定值这一特性的确定仍需要一步研究。尤其应注意的是试验条件和实际工作条件或设计条件之间的修正,转换图中(见图1)所显示的特性可能对这种修正的影响很大。
10.2 组织系数
引入经验性的组织系数后,具有较低添加剂矿物润滑油,由齿轮试验确定的胶合温度,可扩展到不同的齿轮钢、热处理或表面处理。
ΘS=ΘMT + XWΘflmaxT………………………………….(94)
式中:
ΘMT——试验齿轮的闪温,单位为摄氏度(℃);
ΘflmaxT——试验齿轮的最大闪温,单位为开尔文(K);
XW——组织系数(见表2)。
然而,对于通常的工作条件和使用热弹系数的平均值时,组织系数的这个近似值受所用磨擦因数的方法的限制。如果所使用的方法是考虑磨擦因数和热弹系数的真实值时,则不必再使用组织系数。
表2组织系数
材 料 |
XW |
调质钢 |
1.00 |
磷化钢 |
1.25 |
镀铜钢 |
1.50 |
液体或气体氮化钢 |
1.50 |
渗碳淬火钢,奥氏体含量:
——低于平均值
——平均值(10%~20%)
——高于平均值 |
1.15
1.00
0.85 |
奥氏体钢(不锈钢) |
0.45 |
10.3 瞬时接触时间
试验[37]表明:用抗胶合油润滑时,齿轮的胶合温度受瞬时接触时间的影响。瞬时接触时间是指齿面上的一点暴露在相啮齿的赫兹接触带内的时间。
一对齿面确定的瞬时接触时间tmax为t1和t2中的最大值。
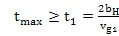
…………….……………….………(95)
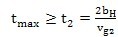
…………….……………….………(96)
胶合温度ΘS和接触温度之间关系可近似地用图17所示的由两条直线组成的曲线表达。
对于tmax<tC
ΘS=ΘSC+XΘXW(tC -tmax)……………………………………………(97)
tmax≥tC
ΘS=ΘSC……………………………………………(98)
式中:
ΘSC——较长接触时间的胶合温度,单位为报氏度(℃);
XΘ——胶合温度梯度,单位为开尔文每微秒(K/μs);
XW——组织系数;
tc——曲线变曲处的瞬时接触时间,单位为微秒(μs);
tmax——啮合齿的瞬时接触时间,单位为微秒(μs)。
对于不同的润滑油XΘ和tc可用下列值:
——不加抗胶合添加剂:XΘ=0 K/μs,tc=18μs;
——加抗胶合添加剂:XΘ=18 K/μs,tc=18μs。
图17 对于加抗胶合添加剂润滑油瞬时接触时间对胶合温度的影响
10.4 齿轮试验的胶合温度
胶合温度可由齿轮试验确定,如Ryder[38],FZG-Ryder[39],FZGL-42[40],FZGA/8.3/90[41]等方法。
试验结果的表达应包括胶合温度和试验条件。如果试验结果用其他方式表达,则应给出关系式,如:
ΘS=80+(0.85+1.4XW)·XL·(SFZG)2…………………………………(99)
式中:
XW——组合系数(见表2);
XL——润滑油系数(见式27);
SFZG——FZG A/8.3/90试验的载荷级。这里指的是发生胶合时载荷级。
然而,油有参数变化容易引起SFZG更大的变化,假定在换油间隔期间油稍微有点变质,载荷级的变化通常为±1。因此,计算时间可用比规定载荷级较小的载荷级。
10.5 安全范围
与疲劳损伤的时间较长相比,一次简单的瞬时过载就会引起严重的胶合使齿轮在较矩的时间失效。因此在选择合适的安全范围时,应谨慎考虑,尤其要注意运行时节线速度较高的齿轮。
在较知瞬时接触时间tmax情况下,安全条件是基于胶合温度的增加(ΘS>ΘSC)(见10.3),而瞬时接触温度tmax不应该增加,除非传动功率适当降低。
安全系数定义为:
S
B=

…………………………(100)
式中:
ΘS——胶合温度,单位为摄氏底(℃);
ΘBmax——最大接触温度,单位为摄氏底(℃);
Θoil——油温,单位为摄氏底(℃)。
然而,齿轮的实际载荷与确定的接触温度之间的关系很复杂,用温度的任何比值来表达安全系数可能会引起混淆。
因此,除了试验载荷级的说明以外(见10.4节),建议用胶合温度与计算的最大接触温度之间所要求的最小差别(如≥50K)来表达安全概念。
附录A
(资料性附录)
闪温公式提示
自从最初的闪温公式[12][14]公布以来,布洛克又作了下列修改:
——将赫兹接触带的全宽改为半宽,并用椭圆形磨擦热分布的1.11代替抛特线形磨擦热分布的0.83 =1.17[16];
——扩展到不同方向的切线速度[32]见式(3)。
为方便起见,作了确切的修改:
——有些量有另一些量来表达,如赫兹接触带半宽和曲率半径;
——公式的某些部分被集中为独立的系数,如热弹系数,见A,3。
为实际应用,作了适当的修改:
——重新定义的系数,如载荷分担系数,见第9章;
——增加了经验系数,如啮入系数,见第8章。
A.1 常用情况
在轮齿接触的最通常的情况(如准双曲面齿轮)中,认为连续接触区呈锥形带状,见图A.1。两轮的切向速度vg1和 vg2的方向角γ1和γ2不同,γ1和γ2分别为vg1和 vg2与接触区长轴的夹角。在较简单的情况下(如圆柱齿轮),方向角简化为:γ1=γ2=π/2.
锥形接触区的一些横截面上的接触压力分布近似于半椭圆分布,半椭圆在处于两面三刀平行平面之间的替代带状接触区上,带状接触区有一个均匀的宽度且等于前述的局部宽度,见图A.1。
图A.1 两轮切线速度方向不同的替代带接触区
准双面齿轮的实际赫兹接触区可假定为椭圆形,并且切向速度方向与接触区长轴的方向既不垂直也不平行。然而,椭圆接触区可能相当长,有足够高的椭圆率,或它可能是稍有锥度的带状。
两个切线速度的方向偏离椭圆短轴不太多。换句话说,让两个速度在长轴上有一个分量。
为了寻找确定最大闪温,实际椭圆接触区由一个带状接触区来代替,带状接触区的宽度为2bH等于椭圆短轴的长度,见图A.1。
注意:最大接触压力(在短轴上)直接与载荷立主根而不是平方根成正比。在一些情况下,为了延长点接触,必须采用赫兹公式[42]。
总之,目前的方法可以说是一个合理的近似方法。主要原因在于这样的特征;即在上述定义的动态条件下,对于实际的足够长的椭圆接触,希望实际最大闪温发生在接近短轴的一个点上。
对于替代带状接触区切向速度方向不同时,布洛克闪温公式[12][14][16][32]为:
Θ
B=1.11·

………………(A.1)
式中:
μm——平均磨擦因数;
XJ——啮入系数,见第8章;
Xr——载荷公担系数,见第9章
ωBn——法向单位载荷,单位为牛每毫米(N/mm):
ω
Bn=

……………………(A.2)
式中:
ωBt——端面单位载荷,见5.3,单位为牛每毫米(N/mm);
awn——法向啮合角,单位为度(°);
awn=arcsin(sinawt·cosβw) ……………………(A.3)
βW——啮合螺旋角,单位为度(°);
β
W=arctan

………………(A.4)
bH——赫兹接触带半宽,单位为毫米(mm);
Vg1——小轮的切向速度(矢量)单位为米每秒(m/s);
Vg2——大轮的切向速度(矢量)单位为米每秒(m/s);
BM1——小轮的热接触系数,见A.3,[N/(mm1/2·m1/2·s1/2·K)];
BM2——大轮的热接触系数,见A.3,[N/(mm1/2·m1/2·s1/2·K)];
γ1——小轮的切向速度的方向角,单位为度(°);
γ2——大轮的切向速度的方向角,单位为度(°)。
A.2 圆柱齿轮
圆柱齿轮所使用的闪温公式3)(3)为了避免旋转频率单位的不正确表达,公式中用节线速度和中心距来表示,以代替更富逻辑性的旋转频率和中心距。过去,“n”表达为每分钟转数,单位为“r/min”。为了获得有条理的单位体系数,重新定义“”单位时间转的任何试图都是要失败的,原因是单位“1/s”有双重含义,即角度/s,或弧度/s。在国际单位制中这种含糊状况的深层原因是角度量缺乏量纲,并且在太多的情况下,弧度的单位被错误地忽略了。解决的办法是把旋转的“量”简化为以Hz为单位的这种“非平常”的旋转频率。)为:
Θ
fl=μ
mX
MX
JX
G(X
r·ω
Bt)
3/4·

………………(A.5)
式中:
μm——平均磨擦因数(见第6章)
XM——热弹系数(见A.3)
XJ——啮入系数(见第8章)
XG——几何系数
对于外齿轮副:
X
G=0.15X
αβ(u+1)
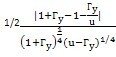
……………………(A.6)
对于内齿轮副(实际上是符号的转换)
X
G=0.15X
αβ(u-1)
1/2
……………………(A.7)
Xr——载荷分担系数(见第9章);
ωBt——端面单位载荷 (见5.3);
vt——节线速度;
α——中心距。
法向压力角和螺旋角的影响为:
Xαβ=1.22sin1/4αwtcos-1/2αwtcos1/2βb………………(A.8)
然而,系数Xαβ的值非常接近于4)(4)在式(A.8)的分子中和在式(A.6)、式(A.7)的分母(0.15=0.62/1.22)引入常数1.22,目的是为了简化式(A.8)。)1,见表A.1,它的近似值可取为1。
A.3 热弹系数
热弹系数是考虑大、小齿轮材料特性的影响。
表A.1系数Xαβ
αwt |
Xαβ |
β=0
αt=20.000° |
β=10°
αt=20.284° |
β=20°
αt=21.173° |
β=30°
αt=22.796° |
18° |
0.947 |
- |
- |
- |
20° |
0.978 |
0.975 |
0.966 |
- |
22° |
1.007 |
1.004 |
0.995 |
0.981 |
24° |
1.035 |
1.032 |
1.023 |
1.008 |
26° |
1.064 |
1.060 |
1.051 |
1.036 |
28° |
- |
- |
- |
1.063 |
X
M=
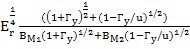
……………………(A.9)
式中:
Er——当量弹性模量,单位为牛每平方毫米(N/mm2).
E
r=
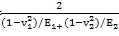
……………………(A.10)
式中:
E1——小轮材料的弹性模量,单位为牛每平方毫米(N/mm2);
E2——大轮材料的弹性模量,单位为牛每平方毫米(N/mm2);
V1——小轮材料的泊松比;
V2——大轮材料的泊松比;
BM1——小轮的热接触系数,[N/(mm1/2·m1/2·s1/2·K)];
BM2——大轮的热接触系数,[N/(mm1/2·m1/2·s1/2·K)];
B
M1=(0.001

……………………(A.11)
B
M2=(0.001

……………………(A.12)
式中:

——小轮材料的热传导系数,单位为牛每秒开尔文[N/(s·K)];

——大轮材料的热传导系数,单位为牛每秒开尔文[N/(s·K)];

——小轮的材料的密度,单位为千克每立方米(kg/m
3);

——大轮的材料的密度,单位为千克每立方米(kg/m
3);

——小轮材料单位质量的比热,单位为焦耳每千克开尔文[J/(kg·K)];

——大轮材料单位质量的比热,单位为焦耳每千克开尔文[J/(kg·K)];
大多数情况下,大、小轮的热接触系数相同,热弹系数完全取决于材料特性。
X
M=

……………………(A.13)
对于马氏体钢:λM=41~52N/(s·K),ρM·cM约为3.8N/(mm2·K);因此,对这种钢,当热弹系数为未知时,可采用其平均值BM=435N/(mm1/2·m1/2·s1/2·K)=13.8N/(mm·s1/2·K)而不会有太大的误差。对于用特种钢制造的齿轮:E1=E2=206000N/mm2,υ1=υ2=0.3,还用:
XM=500K·N-3/4·S1/2·m-1/2·mm……………………(A.14)
A.4锥齿轮
锥齿轮的边疆接触区为稍带锥度的带状形。然而,在大多数情况,可较好地用平行的带状接触区来近似,连同两个切向速度的重合并在方向上与长轴垂直,尤其是当曲率半径的正确定值和赫兹接触带已知时,可直执着使用权原来的公式(A.1)。为了方便起见,公式可以被改写,即用直线来近似“8”字作用线,并且系数用锥齿轮的一般量来表达。
对于改写的运动学公式作如下假充5)(5)这些假设对曲率半径作了适当的近似,但不包括用当量圆柱齿轮副代替锥齿轮。)[43],见图A.2。
图A.2近似作用线
——大、小轮有一个公共顶点并有任意轴交角:
Σ=δ1+δ2……………………(A.15)
——所有的计算与分锥有关;
——啮合线用直线近似;
——啮合面为一个平面
锥齿轮的闪温既可以作为当量圆柱齿轮副来计算,也可以用直接的公式计算。
Θ
fl=μ
mX
MX
JX
G(X
Γω
Bt)
3/4 
……………………(A.16)
式中:
μm——平均磨擦因数;
XM——热弹系数(见A.3);
XJ——啮入系数(见第8章)
XG——几何系数。
X
G=0.51X
αβ(cosδ
1+ cosδ
2)
1/4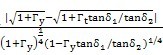
……………………(A.17)
式中:
Xαβ——角度系数(见A.2);
Xr——载荷分担系数(见第9章);
Bt——端面单位载荷(见5.3);
t——节线速度;
RM——中点锥距。
附录B
(资料性附录)
最佳齿廓修形
如果齿廓进行修形,修形量的设计和加工应满足要求的载荷分配,如图6。小轮和大轮的最佳齿顶修缘量可近似表达为:C
eff=

……………………(B.1)
式中:
KA——使用系数;
Kmp——分支系数(见5.3);
Ft——切向力,单位为牛(N);
b——齿宽,单位为毫米(mm);
αt——端面压力角,单位为度(°);
cr——啮合刚度,单位为牛每毫米微米[N/(mm·μm)]。
圆柱齿轮的齿顶修缘高度在齿轮未加载时既不到达单对啮合区,也不能导致重合度εα<1(即计算εα时假定的顶圆直径等于修缘区开始的直径)。
如果相啮齿轮的齿根也修形,那么齿顶修缘量应该用当量齿顶修形量来代替,当量修形量为齿顶修缘量和相啮齿轮的偏向齿体内的齿根修表量之和。
C
eq1= C
a1+ C
f2
……………………(B.2)
C
eq2= C
a2+ C
f1
……………………(B.3)
对于圆柱齿轮
H
2=d
a2
……………………(B.4)
H
1=d
a1
……………………(B.5)
对于锥齿轮,使用当量齿轮的量值,见GB/T10062.1-2003附录A,或用下式:
H
2=

……………………(B.6)
H
1=

……………………(B.7)
u
v=

……………………(B.8)
式中:
mn——法向模数,单位为毫米(mm);
da1——小轮顶圆直径,单位为毫米(mm);
da2——大轮顶圆直径,单位为毫米(mm);
α——中心距,单位为毫米(mm);
u——齿数比;
Rm——中点锥距,单位为毫米(mm);
δ1——小轮的节锥角,单位为度(°);
δ2——大轮的节锥角,单位为度(°);
ham1——小轮齿宽中心齿顶高,单位为毫米(mm);
ham2——大轮齿宽中心齿顶高,单位为毫米(mm);
αwt——端面啮合角,单位为度(°);
ГA——啮合线上A点的参数;
ГE——啮合线上E点的参数。