渐开线圆柱齿轮精度检验规范
1 主题内容与适用范围
本标准规定了GB10095-88《渐开线圆柱齿轮精度》中规定的切向综合误差、一齿切向综合误差、径向综合误差、一齿径向综合误差,、齿距累积误差、K个齿距累积误差、齿圈径向跳动、公法线长度变动、齿形误差、齿距偏差、基节偏差、齿向误差、接触线误差、轴向齿距偏差、螺旋线波度误差、齿厚偏差、公法线平均长度偏差、齿轮副的切向综合误差、齿轮副的一齿切向综合误差、齿轮副的接触斑点等20项误差和齿轮副的侧隙的检验规范,并对齿厚偏差的其它代用误差项目:基本齿廓位移、量柱测量距(M值)偏差和双啮中心距偏差规定了检验规范。
本标准适用于平行轴传动的渐开线圆柱齿轮及其齿轮副,其法向模数mn大于或等于1mm。基本齿廓按GB1356《渐开线圆柱齿轮基本齿廓》的规定。
2引用标准
GB 10095 渐开线圆柱齿轮精度
GB 2821 齿轮几何要素代号
GB 3374 齿轮基本名词术语
GB 1356 渐开线圆柱齿轮基本齿廓
JJ G 1001 常用计量名词术语及定义
JJ G1010 长度计量名词术语及定义
JB3887 渐开线直齿圆柱测量齿轮
ZB J42006 测量蜗杆
3符号代号
La 齿顶点展开长度(齿顶点曲率半径),mm
Lf 齿根点展开长度(齿根点曲率半径),mm
Laf 齿顶点至齿根点展开长度(齿顶点与齿根点曲率半径之差),mm
φa 齿顶点展开角,(°)
φf 齿根点展开角,(°)
φaf 齿顶点至齿根点展开角,(°)
e 测量时齿轮的安装偏心量,μm
ΔTo 测量蜗杆啮合线误差,μm
ΔUo 测量蜗杆轴向窜动量,μm
Zo 测量蜗杆头数
α 材料线膨胀系数,10-6/℃
t 温度,℃
αpt 量柱中心点的端面压力角,(°)
注:①下角标o表示标准元件(标准齿轮、标准蜗杆、标准样板、量块)、测量元件(测量齿轮、测量蜗杆、测头)和测量仪的参数。
②下角标1表示使用时与被测齿轮配对啮合的齿轮的参数。
③本规范所列各公式对直齿轮斜齿轮均适用,对于直齿轮式中mn=m1=m;αn=αt=α;
Xn=Xt=X;β=βb=0。
4单面啮合综合误差的检验
单面啮合(简称单啮)综合误差的检验包括切向综合误差 和一齿切向综合误差 的检验。
4.1测量方法和测量仪器
单啮综合误差的测量方法有啮合法和坐标法。
啮合法的测量仪器有齿轮单面啮合检查仪和齿轮单面啮合整体误差测量仪等。
坐标法的测量仪器有万能齿轮测量机等。
4.1.1啮合法测量原理
啮合法测量原理参见图1。以被测齿轮回转轴线为基准,使被测齿轮2与测量齿轮1(或测量齿条、测量蜗杆等)作单面啮合传动,将此传动与标准传动发生装置3产生的标准传动相比较,并通过误差处理系统4连续测量出被测齿轮实际回转角和理论回转角的差值,由同步记录器5将其记录成功向综合误差曲线(图2),在该曲线上按误差定义取出

和

.
图1 啮合法测量原理图
1— 测量齿轮;2—被测齿轮;3—标准传动发生装置
4—误差处理系统;5—同步记录器。

和

也可用啮合法测整体误差的方法测得,其测量原理见16.1.1。
4.1.2坐标法测量原理
按16.1.2所述原理,测出截面整体误差曲线或全齿宽整体误差曲线,在该曲线上按误差定义取出

和

。
4.2测量
整体误差法测量见16.2。
4.2.1测量温度
见表15。
4.2.2测量仪器的检定
仪器应按检定规程或其它有关技术文件的规定进行检定,经法定部门检定合格方准使用。
4.2.3测量元件的选择
啮合法的测量元件可以是测量齿轮或测量蜗杆。
测量元件的法向模数mn、法向压力角αn应与被测齿轮一致,其齿形工作部分的齿高应能保证被测齿轮齿形工作部分全被测到。
测量齿轮的精度应符合JB3887的规定;测量蜗杆的精度应符合ZB J42006的规定。
4.2.4测量仪器的校准
测量5级和高于5级精度的齿轮时,测量前必须用经法定部门检定的标准齿轮对仪器(包括测量无件)进行校准。标准齿轮的检定误差不应大于被测齿轮对应误差项目公差的五分之一。
4.2.5测量基准的确定
见附录B(补充件)。
4.2.6测量位置的确定
应分别对左、右侧齿面整周的每个齿进行测量。被测齿高应大于或等于图样规定的工作齿高。
测量元件为测量蜗杆时,对于齿宽小于或等于160mm的直齿轮允许只测齿宽中部截面切向综合误差曲线;对于齿宽大于160mm的直齿轮应至少分别测量上、中、下、三个截面的截面切向综合误差曲线,上下截面各距端面约百分之十五齿宽;对于斜齿轮应测量至少由五个截面切向综合误差曲线组成的全齿宽切向综合误差曲线,截面间距应大致相等,上下截面各距端面约百分之十五齿宽。
单侧齿面工作的齿轮只测工作侧齿面。
4.2.7测量的不确定度
切向综合误差的测量不确定度

和一齿切向综合误差的测量不确定度

不应大于被测齿轮对应误差项目公差有三分之一。测量5级和高于5级精度的齿轮时,允许不大于二分之一,但此时应以五次以上重复测量结果的平均值作为测量结果。
当不能确定测量不确定度能否满足上述要求时,应进行测量不确定度的计算。
4.2.7.1切向综合误差测量不确定度

的计算

按下式计算:

……………………(1)
式中:δ1——仪器测量切向综合误差时的示值误差[见附录A(补充件),也允许按仪器检定规程确定],μm;
δ2——测量元件制造误差引起的测量误差,μm;
测量元件为测量蜗杆时,
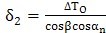
………………(2)
测量元件为测量齿轮时,

……………………(3)
式中:

——测量齿轮的切向综合误差,μm;
δ3——被测齿轮测量时的安装偏心引起的测量误差,μm;

……………………(4)
δ4——测量元件定位误差引起的测量误差,μm;
测量元件为测量齿轮时,

……………………(5)
测量元件为测量蜗杆时,
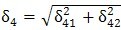
………………(6)
式中:δ41——测量蜗杆安装偏心引起的测量误差,μm;

………………(7)

——测量蜗杆端面圆跳动引起的测量误差,μm;
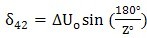
………………(8)
公式(7)和(8)中当

时,取

。
若式2中的

是在测量前用标准齿轮校准测量蜗杆测得的,即

已包括在

中,则

4.2.7.2一齿切向综合误差测量不确定度U

的计算
U

(μm)按下式计算:
U

………………(9)
式中:δ1——仪器测量一齿切向综合误差时的示值误差[见附录A(补充件),也允许按仪器检定规程确定],μm;
δ2——测量元件制造误差引起的测量误差,μm;
测量元件为测量蜗杆时,
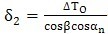
………………(10)
测量元件为测量齿轮时,

……………………(11)
式中:

——测量齿轮的一齿切向综合误差,μm。
δ3——温度误差引起的测量误差,μm;

………………(12)
δ4——被测齿轮测量时的安装偏心引起的测量误差,μm;
δ
4=

……………………(13)
δ5——测量元件定位误差引起的测量误差,μm。
测量元件为测量齿轮时,δ
5=

………………(14)
测量元件为测量蜗杆时,δ5按公式(6)、(7)(8)计算。
4.3测量结果处理

和

应在切向综合误差曲线上取值。对直齿轮允许在截面切向综合误差曲线上取值。对于斜齿轮允许在曲截面切向综合误差曲线组成的全齿宽切向综合误差曲线的外轮廓线上取值。
切向综合误差曲线(包括截面切向综合误差曲线和全齿宽切向综合误差的外轮廓线)图2(a)、图2(b)的X坐标代表被测齿轮的回转角,Y坐标代表被测齿轮的回转角误差。
切向综合误差曲线图[图2(a),图2(b)]沿X坐标360°范围内,Y坐标的最大变化量为

;沿X坐标

范围内,Y坐标的最大变化量为

。

和

应在被测齿轮分度圆切线方向计值(μm),沿其他方向测量时应对测得值进行换算,见附录C(补充件)。
以在4.2.6规定的各测量位置中测得的最大误差作为测量结果。
图2

和

取值示意图
5双面啮合综合误差的检验
双面啮合(简称双啮)综合误差的检验包括径向综合误差

和一齿径向综合误差

的检验。
5.1测量方法和测量仪器
双啮综合误差的测量方法有直接法和间接法。
直接法的测量仪器有齿轮双面啮合检查仪等。
间接法的测量仪器有齿轮单面啮合检查仪等。
5.1.1直接法测量原理
直接法测量原理参见图3。以被测齿轮回转轴线为基准,用径向拉力簧5,使用被测齿轮1与测量齿轮2作无侧隙的双面啮合传动,被测齿轮的双啮误差转化为双啮中心距的连续变动通过测量滑架3和测微装置4反映出来,将这种变动按被测齿轮回转一周(360°)排列,记录成径向综合误差曲线(图5),在该曲线上按误差定义取出

和

。
图3 双啮法测量原理图
1— 被测齿轮;2—测量齿轮;3—测量滑架;4—测微装置;5—径向拉力弹簧
5.1.2间接法测量原理
按4.1.1和4.1.2所述的测量原理先测出被测齿轮左右齿面的切向综合误差曲线,并使其按啮合时的相对角坐标位置排列,组成双向综合误差曲线[图4(a)],两条切向综合误差曲线间的间距变化曲线[图4(b)]即为径向综合误差曲线,在该曲线上按误差定义取出

和

(取值方法见5.3.1)。
图4间接法测量原理图
5.2测量
间接法测量见4.2。
5.2.1测量仪器的检定
仪器应按检定规程或其它有关技术文件的规定进行检定,经法定部门检定合格方准使用。
5.2.2测量无件的选择
测量元件为测量齿轮。测量齿轮的法向模数mn和法向压力角αn应与被测齿轮一致。
测量齿轮齿厚的确定和齿高的确定,应保证被测齿轮的工作齿高全被测到且齿顶齿根无干涉。
测量齿轮的齿宽应大于被测齿轮的齿宽。
测量齿轮的精度和参数应符合JB 3887的规定。
5.2.3测量基准的确定
见附录B(补充件)
5.2.4测量位置的确定
径向综合误差应在齿高工作范围内对所有齿的全齿宽进行测量。
5.2.5测量的不确定度
径向综合误差的测量不确定度

和一齿径向综合误差的测量不确定度

不应大于被测齿轮对应误差项目公差的三分之一。
当不能确定测量不确定度是否能满足上述要求时,应进行测量不确定度的计算。
5.2.5.1径向综合误差测量不确定度

的计算:

按下式计算:

……………………(15)
式中:δ1——仪器的示值变动性[见附录A(补充件),也允许按仪器检定规程确定],μm;
δ2——被测齿轮中截面与传感器在被测齿轮轴向位置不一致引起的测量误差,μm;
δ
2=

……………………(16)
式中:H——被测齿轮中截面与传感器在被测齿轮轴线方向的距离,mm;

——当测量滑架移动时,在两齿轮轴线所组成的平面内摆角差,(″)
δ3——传感器的示值误差,μm;
δ4——测量齿轮制造误差引起的测量误差,μm;
δ
4=

……………………(17)
式中:

——测量齿轮的径向综合误差,μm,
δ5——测量齿轮的安装偏心引起的测量误差,μm;
δ5=2eo………………………………(18)
δ6——被测齿轮测量时安装偏心引起的测量误差,μm。
δ6=2e……………………(19)
5.2.5.2一齿径向综合误差的测量不确定度

的计算

(μm)按下式计算:

……………………(20)
式中:δ1——仪器的示值变动性[见附录A(被充件)也允许按仪器检定规程确定,μm;
δ2——被测齿轮中截面与传感器在被测齿轮轴向位置的不一致引起的测量误差,μm;
δ2的计算式见式(16);
δ3——传感受器的示值误差,μm;
δ4——测量齿轮制造误差引起的测量误差,μm;
δ
4=

……………………(21)
式中:

——测量齿轮的一齿径向综合误差,
δ5——测量齿轮的安装偏心eo引起的测量误差,μm;
δ
5=2e
osin(

)……………………(22)
δ6——被测齿轮测量时的安装偏心e引起的测量误差,μm。
δ
5=2esin(

)……………………(23)
5.3测量结果的处理

和

应从径向综合误差曲线上取值。对8级和低于8级精度的齿轮允许直接用指示表读数。
5.3.1误差曲线取值
径向综合误差曲线的X坐标代表被测齿轮的回转角,Y坐标代表双啮径向误差(图5)。
图5径向综合误差曲线
径向综合误差曲线在X坐标360°范围内,Y坐标的最大变化量为

;在X坐标

范围内,Y坐标的最大变化量为

。

和

应在被测齿轮和测量齿轮的中心距方向(被测齿轮双侧齿面的径向)计值(μm),以其他方向测量时,应对测得值进行换算,见附录C(补充件)。
5.3.2指示表读数
双面啮合测量时,被测齿轮旋转一周内指示表示值最大变化量为

;被测齿轮转动一个齿距角内,指示表示值的最大变化量为

。
6齿距误差的检验
齿距误差的检验包括齿距偏差Δfpt、齿距累积误差Δfp和K个齿距累积误差Δfpk的检验。
6.1测量方法和测量仪器
齿距误差的测量方法有相对法和绝对法。
相对法的测量仪器有万能测齿仪、半自动齿距仪、上置式齿距仪和旁置式齿距仪等。
绝对法的测量仪器有单面啮合整体误差测量仪、万能齿轮测量机等,也可在三坐标测量机、分度头和成能工具显微镜等仪器上测量。
6.1.1相对法测量原理
相对法测量原理参见图6。以被测齿轮回转轴线为基准(也可用齿顶圆代替),采用双测头2、4,以被测齿轮1上任一齿距或跨几个齿的齿距作为相对标准,通过传感器3依次测量各齿距或跨齿距的相对差值,按误差定义进行数据处理(见6.3.1),求得Δfp、Δfpk和Δfpt。
图6 相对法测量原理
1— 被测齿轮;2—测微测头;3—传感器;4—定位测头
6.1.2绝对法测量原理
绝对法又分为直接法和间接法。
直接法测量原理参见图7。以被测齿轮回转轴线为基准,用标准圆分度装置2(如圆光栅、分度盘等)对被测齿轮1分度,由测头4和传感器3测出齿距偏差。也可用测头4和传感器3定位,由标准圆分度装置测出实际齿距角,并装其与公称齿距角比较,其差值即为齿距偏差。按误差定义对测得值进行处理,求得Δfp、Δfpk和Δfpt。
图7绝对法测量原理图
1— 被测齿轮;2—标准圆分度装置;3—传感器;4—测头
间接法按16.1.1和16.1.2所述的测量原理先测出齿轮截面整体误差曲线,在该曲线上按误差定义取出Δfp、Δfpk、Δfpt。
6.2测量
间接法测量见16.2。
6.2.1测量温度
见表1。
表1齿距误差的测量温度
被测齿轮精度等级 |
测量室室温度 |
被测齿轮与测量仪器(或测量元件)的温差 |
相对法 |
绝对法 |
相对法 |
绝对法 |
3~5 |
20±2 |
20±3 |
≤2 |
≤3 |
6~7 |
20±3 |
20±5 |
≤3 |
≤4 |
≥8 |
20±5 |
20±8 |
≤4 |
≤5 |
6.2.2测量仪器的检定
仪器应按检定规程或其它有关技术文件的规定进行检定,经法定部门检定合格方准使用。
6.2.3测头的选择和调整
在保证不发生干涉和碰撞的情况下,宜选择直径较大的测头。
6.2.4测量基准的确定
见附录B(补充件)。
6.2.5测量位置的确定
齿距误差应在齿宽和齿高中部,对左、右侧齿面进行测量。对齿宽大于160mm的齿轮应至少测量上、中、下三个截面,上、下截面各距端面约百分之十五齿宽。单侧齿面工作的齿轮只测工作侧齿须。
用相对法测量齿数少于60的齿轮时,采用逐齿测量;测量齿数多于或等于60的齿轮时,对Δfpt仍应采用逐齿测量,对ΔFp和ΔFpk一般应采用跨齿和逐齿补点测量,允许在保证测量不确定符合6.2.6规定的前提下,采用逐齿测量。
6.2.6测量的不确定度
齿距累积误差的测量不确定度UFP、K个齿距累积误差的测量不确定度UFPK和齿距偏差的测量不确定度UfPt不应大于被测齿轮对应误差项目公差的三分之一。测量5级和高于5级精度的齿轮时,允许不大于二分之一,但此时应以五次以上重复测量结果的平均值作为测量结果。用测量法向齿距的方法测量斜齿轮时,UFP、UFPK和UfPt不应大于五分之一;使用手提式仪器测量时UFP、UFPK和UfPt不应大于五分之一。
当不能确定测量不确定度是否能满足上述要求时,应进行测量不确定度计算。
6.2.6.1齿距累积误差测量不确定度UFP的计算
UFP(μm)按下式计算:
UF
P=

……………………(24)
式中:δ1——仪器测量齿距累积误差时的示值误差[见附录A(补充件),也允许按仪器检定规程确定],μm;
当被测齿轮齿数Z或跨齿测量的分组数Q大于仪器检定时所使用的标准齿轮齿数Z。时,还需用下式被充考核,下式中I为仪器的示值变动性:
δ
1=

……………………(25)
δ2——被测齿轮测量时的安装偏心引起的测量误差,μm;
δ2=2e/cosαt……………………(26)
齿顶圆定位时,以顶圆跳动的一半作为安装偏心量。
6.2.6.2齿距偏差的测量不确定度Ufpt的计算
Ufpt(μm)按下式计算:
Uf
pt=

………………(27)
式中:δ1——仪器测量齿距偏差时的示值误差[见附录A(补充件),也允许按仪器检定规程确定] μm;
δ2——被测齿轮测量时的安装偏心引起的测量误差,μm;
δ
2=2esin(

)/cosα
t……………………(28)
齿顶圆定位时,以顶圆跳动量的一半作为安装偏心量。
6.3测量结果处理
对齿距误差测量结果的处理可以采用计算法或作图法或误差曲线取值法(从整体误差曲线取值的方法见16.3.1)。
以在6.2.5所规定的各测量位置中测得的最大误差值作为测量结果。
Δfp、Δfpk、Δfpt应在被测齿轮分度圆切线方向计值(μm),以其它方向测量时,应对测得值进行换算,见附录C(补充件)。
6.3.1相对法测量结果处理
6.3.1.1逐步测量
a.计算法
从逐齿测量数据计算fp、Δfpk和Δfpt的方法列于表2,以Z=12、K=2的齿轮为例。
表2逐齿测量数据处理

……………………(29)

(取绝对值最大的偏差作为测量结果)………………(30)

…………(31)

……………………(32)
b.作图法
直角坐标图上的X坐标代表齿序号i,Y坐标代表齿距误差(以公度圆弧长

计值)。将测得值按齿序号i依次累积标在坐标图上(图8),过坐标原点和最后一个误差点作一直线,该直线即为计算

的基准线,所有误差点相对基准线的Y坐标最大值和最小值之差为

,相隔K个齿距的二个误差相对基准线的Y坐标最大差值为

,相邻两个误差点相对基准的Y坐标最大差值为

图8逐齿测量结果处理作图法
c.误差曲线取值方法
在数据处理系统直接画出的齿距误差曲线(图9)上,X坐标代表齿序i(此X坐标轴就是图8中的基准线),Y坐标代表齿距误差(以分度圆弧长μm计值),误差曲线在被测齿轮齿数范围内,Y坐标的最大变化量为ΔFp,相邻两个误差点Y坐标的最大差值为Δfpt,相隔K个齿距的两个误差点Y坐标的最大差值为ΔFpk。
图9齿距误差曲线取值法
6.3.1.2跨齿测量
a.计算法
从跨齿测量数据中求取ΔFp的方法列于表3、4、5、6、7,以Z=60跨齿数N=6,分组数Q=10为例。
表3跨齿齿距累积误差的数据处理
计算结果给出了相对0#齿的跨齿齿距累积误差的最大值ΔFpj max=+10 和最小值ΔFpj min=-11。为了求得ΔFpj max应对i=12~18、i=18~24进行逐齿补点测量。为了求得ΔFpj min应对i=42~48、i=48~54进行逐齿补点测量。补点测量数据的处理方法列于表4、5、6、7。
表4 i= i=12~18逐齿补点数据处理
表5 i=18~24逐齿补点数据处理
表6 i=42~48逐齿补点数据处理
表7 i=48~54逐齿补点数据处理
b.作图法
第一步跨齿齿距累积误差图(图10),以直角坐标图上的X坐标代表跨齿序号j,Y坐标代表相对对齿距偏差的累积值

将测得值(表3中的

)按跨齿序j依次累积标在坐标图上,过原点和最后一个误差点连一直线,该直线即为计算跨齿齿距累积误差的基准线。找出所有误差点中相对基准线的纵坐标最大值为

,最小值

。
图10跨齿齿距累积误差图
第二步作分组逐齿齿距累积误差图:在直角坐标图上X坐标代表组内齿序号i,Y坐标代表相对齿距偏差的累积值
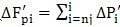
。将测得值(表4中的

)按齿序i依次累积标在坐标图上,将最后一个误差点的Y坐标减去(
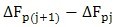
)后,与原点连一直线,该直线即为计算组内各齿相对于j齿的齿距累积误差的基准线。作与该基准给Y坐标相距(

)的平行线,则此平行线为各齿相对于0#齿的齿距累积误差的基准线。按上述方法分别作i=12~18,i=18~24, i=42~48,i=48~54四组的齿距累称误差图(图11、12、13、14)。并从图中求出

。
图14 i=48~54逐齿齿距累积误差图
6.3.2绝对法测量结果处理
6.3.2.1计算法
从逐齿测量数据中求取Δfpt、ΔFp、ΔFpK的方法见表8。以Z=12,K=2的齿轮为例。
表8绝对法测量数据处理
齿距累积误差

……………………(33)
齿距偏差

……………………(34)
K个齿距累积误差

………………(35)
6.3.2.2误差曲线取值方法
在由数据处理系统直接画出的齿距误差曲线上取

的方法与6.3.1.1c相同。
7齿圈径向跳动的检验
7.1测量方法和测量仪器
齿圈径向跳动ΔFr的测量方法有直接法和间接法。
直接法的测量仪器有齿圈径向跳动检查仪和成和测齿仪等。
间接法的测量仪器有齿轮单面啮合整体误差测量仪、万能齿轮测量机以及三坐标测量机等。
7.1.1直接法测量原理
直接法测量原理参见图15。以被测齿轮回转轴线为基准,将测头依次与齿轮各齿槽齿高中部双面接触,测头相对于齿轮回转基准轴线的最大径向变动量即为ΔFr。
图15直接法测量原理图
7.1.2间接法测量原理
按16.1.1和16.1.2所述的测量原理,先测出齿轮双向截面整体误差曲线,在该曲线上按误差定义取出ΔFr。
7.2测量
间接测量法见16.2。
7.2.1测量仪器的检定
仪器应按检定规程或其他有关技术文件的规定进行检定,经法定部门检定合格后方准使用。
7.2.2测头的选择
可选用球形测头,也可以选用圆锥形测头。测头直径应根据被测齿轮模数来选择,使测头与被测齿槽的左右齿面在齿高中部接触。
7.2.3测量基准的确定
见附录B(补充件)。
7.2.4测量位置的确定
齿圈径向跳动应在齿宽中部,对齿轮每个齿槽进行测量。对于齿宽大于160mm的齿轮,应至少测量上、下三个截面,上下截面各距端面约百分之十五齿宽。
7.2.5测量的不确定度
齿圈径向跳动的测量不确定度UFr不应大于被测齿轮齿圈径向跳动公差的三分之一。
当不能确定测量不确定度是否能满足上述要求时,应进行测量不确定度的计算。
UFr(μm)按下式计算:
UF
r=
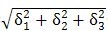
……………………(36)
式中:δ1——仪器的示值变动性[见附录A(补充件),也允许按仪器检定规和确定],μm;
δ2——传感器的示值误差,μm;
δ3——被测齿轮测量时的安装偏心引起的测量误差,μm。
δ3=2e……………………(37)
7.3测量结果处理
ΔFr的测量结果可用直接法直接在指示表上读出。也可以在用间接法测得的双向截面整体误差曲线上取值(详见16.3.2.1)。
直接法测量时,测头与被测齿轮作双面接触逐齿测量,测头相对于被测齿轮回转中心径向距离的最大变动量为ΔFr。
以在7.2.4所规定的各测量位置中测得的最大齿圈径向跳动作为测量结果。
ΔFr在被测齿轮双侧齿面的径向计值(μm),以其它方向测量时,应对测得值进行换算,见附录C(补充件)。
8公法线长度变动的检验
8.1测量仪器和测量原理
8.1.1测量仪器
公法线长度变动ΔFw的测量仪器有:公法线千分尺、公法线指示千分尺、公法线指示卡规、万能测齿仪,以及万能工具显微镜等测量仪器。
8.1.2测量原理
公法线测量原理参见图16。测量不需要以被测齿轮回转轴线为基准。两个跨一定齿数的具有平行量面的量爪2、4,大约在被测齿轮1的齿高中部与两异侧齿面相切,逐齿测量公法线长度。各公法线长度的最大差值即为ΔFw。
图16 公法线测量原理图
1— 被测齿轮;2、4—测量爪;3—传感器
8.2测量
8.2.1测量仪器的检定
仪器应按检定规程或其它有关技术文件的规定进行检定,经法定部门检定合格和后方准使用。
8.2.2测量位置的确定
两平行量爪应跨一定齿数,保证两测量面大约位于齿高中部与两异侧齿面相切。
应在齿宽中部逐齿测量公法线长度。
8.2.3测量的不确定度
公法线长度的测量不确定度UFw不应大于被测齿轮公法线长度变动公差的五分之一。
当不能确定测量不确定度是否能满足上述要求时,应进行测量不确定度的计算。
UFw(μm)按下式计算:
UF
w=
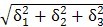
……………………(38)
式中:δ1——仪器的示值变动性[见附录A(补充件),也允许按仪器检定规程确定],μm;
δ2——传感受器的示值误差,μm;
δ3——温度误差引起的测量误差,μm;
δ3=Wk[α(t-20)-αo(to-20)]·1000……………………(39)
8.3测量结果处理
被测齿轮整周内逐齿所测得的公法线长度中最大值与最小值之差即为ΔFw。
ΔFw应在被测齿面法线方向计值(μm),以其它方向测量时,应对测得值进行换算,见附录C(补充件)。
9齿形误差有检验
9.1测量方法和测量仪器
齿形误差Δff的测量方法有展成法、坐标法和啮合法。
展成法的测量仪器有单盘式渐开线检查仪、万能渐开线检查仪(圆盘械杆、正弦械杆、靠模等)和渐开线螺旋线检查仪(万能、单盘、分级圆盘)等。
坐标法的测量仪器有渐开线样板检查仪、万能齿轮测量机、齿轮测量中心、上置式直角坐标测量仪以及三坐标测量机等。
啮合法的测量仪器有齿轮单面啮合整体误差测量仪等。
9.1.1展成法测量原理
展成法测量原理参见图17。以被测齿轮回转轴线为基准,通过和被测齿轮1同轴的基圆盘2在直尺3上纯滚动,形成理论的渐开线轨迹,实际齿形线与理论渐开线轨迹进行比交,其差值通过传感器5和记录器4画出齿形误差曲线,在该曲线上按误差定义取出Δff。
图17展成法测量原理
1— 被测齿轮;2—基圆盘;3—直尺;4—记录器;5—传感器
万能渐开线仪器是通过杠杆或正弦尺机构改变基圆半径实现对各种不同基圆半径齿轮的测量。
9.1.2坐标法测量原理
9.1.2.1极坐标法测量原理
极坐标测量原理参见图18。以被测齿轮回转轴线为基准,通过测角装置5(如圆光栅、分度盘)和测长装置2(如长光栅、激光)测量被测齿轮1的角位移和渐开线展开长度。通过数据处理系统3,将被测齿形线的实际坐标位置与理论坐标位置进行比较,其差值输入记录器4画出齿形误差曲线,在该曲线上按误差定义取出Δff。
图18极坐标法测量原理图
1— 被测齿轮;2—测长装置;3—数据处理系统;4—记录器;5—测角装置
9.1.2.2直角坐标法测量原理
直角坐标法测量原理参见图19。以被测齿轮回转轴线为基准(也可用齿顶圆代替)。测量时被测齿轮固定不动,测头在垂直回转轴线的平面内对齿形线作X-Y直角坐标测量,将测得值与理论值按坐标位置进行比较。将各点的差值绘成齿形误差曲线,在该曲线上按误差定义取出Δff。
图19直角坐标法测量原理
9.1.3啮合法测量原理
按16.1.1所述的测量原理,先测出齿形误差曲线,在该曲线上按误差定义取出Δff。
9.2测量
啮合法测量见16.2。
9.2.测量温度
见表9。
表9齿形误差的测量温度
被测齿轮精度等级 |
测量室温度 |
被测齿轮与仪器(包括样板)的温差 |
展成法仪器 |
坐标法或单盘式仪器 |
展成法仪器 |
坐标法或单盘式仪器 |
3~5 |
20±1 |
20±2 |
≤1 |
≤2 |
6~7 |
20±2 |
20±3 |
≤2 |
≤3 |
≥8 |
20±3 |
20±5 |
≤3 |
≤4 |
9.2.2测量仪器的检定
仪器应按检定规程或其它有关技术文件的规定进行检定,经法定部门检定合格后方准使用。
9.2.3测头的选择和调整
在保证不发生干涉和碰撞的情况下,宜选择直径较大的测头。
展成法测量和极坐标法测量时测头的安装位置应使其工作点位于被测齿轮基圆柱切平面上,其偏离量不应大于±0.02mm。
9.2.4测量仪器的校准
测量5级和高于5级精度的齿轮时,测量前必须先用经法定部门检定的齿形样板对仪器进行校准。测量5级齿轮时,应用二等样板校准;测量3级和4级齿轮时应用一等样板校准。对于万能式渐开线检查仪,当校准样板与被测齿轮的基圆半径不致时,应分别用大于和小于被测齿轮的基圆半径rb的两块样板(基圆半径rbL和rbs)对仪器进行校准,被测齿轮的基圆半径修正量Δrb(mm)按下式求得:
Δr
b=

……………………(40)
式中: ——仪器对两块样板基圆半径的实测值,mm;

两块样板基圆半径的检定值,mm;

——被测齿轮基圆半径的公称值,mm。
9.2.5测量基准的确定
见附录B(补充件)。
9.2.6测量位置的确定
齿形误差应在齿宽中部,对齿轮沿圆周均布的不少于四个齿的左、右侧齿面进行测量,被测量的齿高应大于或等于图纸规定的工作齿高,当图纸未作规定时,按被测齿轮与基本齿条啮合计算工作齿高。
对于齿宽大于160mm的齿轮,应至少测量上、中下、三个截面,上、下截面各距端面约百分之十五齿宽。单侧齿面工作的齿轮只测工作侧齿面。
9.2.7测量的不确定度
齿形误差的测量不确定度Uff不应大于被测齿轮齿形公差的三分之一。测量5级和高于5级精度的齿轮时,允许不大于二分之一,但此时应以五次以上重复测量结果的平均值作为测量结果。手提式仪器测量时的Uff不应大于五分之一。
当不能确定测量不确定度是否满足上述要求时,应时行测量不确定的度的计算。
Uff(μm)按下式计算:
Uf
f=

……………………(41)
式中:δ1——仪器测量齿形误差时的示值误差[见附录A(补充件),也允许按仪器检定规程确定],μm;
δ2——温度误差引起的测量误差,μm;

………………(42)
δ3——测量和校准时测头在被测齿轮轴向位置不一致引起的测量误差,μm;
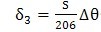
……………………(43)
式中:S——测头使用位置和校准间在被测齿轮轴向的距离,mm;

——测头滑架在基圆切平面的摆角误差,(″)

——被测齿轮测量时的安装偏心引起的测量误差,μm;

……………………(44)
直角坐标法测量时,

……………………(45)
式中:

——齿顶点和齿根起始检验点的径向直线与Y轴的夹角,(°)

——被测斜齿轮测量时的安装倾斜引起的测量误差,μm;
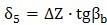
………………(46)
式中:

——在L
af范围内的测头移动轨迹线与被测齿轮轴线的垂直度误差,μm。
9.3测量结果的处理
9.3.1取值范围的确定
齿形误差曲线的取值范围应按设计图样给定的齿形工作部分确定。以展开长度L
af(mm)或展开角

(°)表示。当未给定时,顶部 范围内偏向齿体的负误差可不计入齿形误差,但负误差值不应超过3f
f,

。
9.3.1.1当已知配对齿轮的参数时,按与配对齿轮啮合计算取值范围。

………………(47)
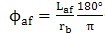
……………………(48)

………………(49)

………………(50)
式中:C——由中心距偏差和配对齿轮的齿顶圆径向跳动引起的齿根起始检验点展开长度的变化量,mm。
9.3.1.2当未知配对齿轮参数时,按与基本齿条啮合计算取值范围。

……………………(51)
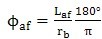
……………………(52)

………………(53)

………………(54)
9.3.2齿形误差的取值

应从齿形误差曲线上取值。对非修形的齿形,允许用指示表读出齿形误差。
齿形误差曲线的X坐标代表被测齿轮的展开角(或展开长度),Y坐标代表齿形误差(图20)。

应在被测齿轮端截面的齿轮基圆切线方向计值(μm),以其它方向测量时,应对测得值进行换算,见附录C(补充件)。
图20齿形误差曲线
齿形误差曲线沿X坐标,在9.3.1规定的取值范围

内,Y坐标的最大变化量为

(齿顶倒棱部分不计值)。计值范围以外的齿顶部分的齿形误差只允许偏向齿体内(详见9.3.1).
以在9.2.6所规定的各测量位置中测得的最大齿形误差作为测量结果。
10基节偏差的检验
10.1测量方法和测量仪器
基节偏差

的测量方法有直接法和间接法。
直接法的测量仪器有基节仪、万能测齿仪及万能工具显微镜等。
间接法的测量仪器有齿轮单面啮合整体误差测量仪和万能齿轮测量机等。
10.1.1直接法测量原理
直接法测量又可分为比较法和绝对法。这两种方法都不需以被测齿轮回转轴线为基准。
10.1.1.1比较法
比较法的测量原理参见图21(a)。测头1、2为两个平面测头,其测量面互相平行。测量前先用基节块(或量块)将两测头测量面间的距离调整至等于被测齿轮的公称基节值,同时使表3指零。测量时将两测头同时靠向被测齿轮的两个相邻的同侧齿面,在齿形工作范围内与齿面相切接触,此时指示表3所指示的相对零点的变化即为基节偏差。
图21(a)中的活动测头2也可以为球形测头[图21(b)],测量时通过平面测头1在所靠齿面上转动,得到球与平面的最短距离即被测基节的实际值,此时指示表所指示的相对于零点的变化量是实际基节与公称基节之差即为基节偏差。
图21比较法测量原理图
1— 固定平测头;2—活动平测头; 1—固定平测头;2—活动球测头
3—指示表 3—指示表;4—定位测头
10.1.1.2绝对法
绝对法测量可在一般测长仪(如万能工具显微镜)上实现。平面测头与测长系统中的长度标准量垂直。测量时,测头在齿形工作高度范围内与相邻两个同侧齿面相切接触,测长系统直接指示测头的实际移动距离即实际基节。实际基节与公称基节之差为基节偏差。
10.1.2间接法测量原理
按16.1.1和16.1.2所述的测量原理,先测出齿轮截面整体误差曲线,在此曲线上按误差定义取出Δfpb。
10.2测量
间接法测量见16.2。
10.2.1测量温度
见表10。
表10基节偏差的测量温度
被测齿轮精度等级 |
测量室温度 |
工件与仪器(包括校准块)温差 |
4~5 |
20±4 |
≤2 |
6~7 |
20±6 |
≤4 |
≥8 |
20±10 |
≤6 |
10.2.2测量仪器的检定
仪器应按检定规程或其它有关技术文件的规定进行检定,经法定部门检定合格后方准使用。
10.2.3测量仪器的校准
采用比较法测量时,测量前、后应用标准基节块或量块校准仪器。测量5级和高于5级精度的齿轮时,选用四等量块;测量6级和低于6级精度的齿轮时,选用五等量块。
10.2.4测量位置的确定
基节偏差应在齿宽中部对圆周均布的不少于四个齿的左、右侧齿面在图纸规定的工作齿高内(齿形修形部分除外)进行测量。当图纸未作规定时,按被测齿轮与基本齿条啮合计算工作齿高。对于齿宽大于160mm的齿轮应至少测量上、中、下三个截面,上、下截面各距端面约百分之十五齿宽。单侧齿面工作的齿轮只测工作侧齿面。
10.2.5测量的不确定度
基节偏差测量的不确一度Ufpb不应大于被测齿轮基节极限偏差的三分之一。使用手提式仪器时,不应大于五分之一。
当不能确定测量不确定度是否满足上述要求时,应时行测量不确定度的计算。
Ufpb(μm)按下式计算:
Ufpb= ……………………(55)
式中:δ1——仪器的示值误差[见附录A(补充件)也允许按仪器检定规程确定],μm;
比较法测量时,δ1为仪器的示值变动性,μm;
δ2——传感受器的示值误差,μm
绝对法测量时,此误差包括在δ1中,此时δ2=0;
δ3——被测齿轮与校正量块(或测长系统的标准尺)温度不一致产生的测量误差,μm。
δ3=Pb[α(t-20)- αo(to-20)]·1000………………(56)
10.3测量结果的处理
Δfpb可在用间接法测得的截面整体误差曲线上取值(见16.3.1.4)也可用直接法在指示表上读出(齿形修形部分不计值)。
以在10.2.4所规定的各测量位置中测得的绝对值最大的基节偏差作为测量结果。
Δfpb应在被测齿面的法线方向计值(μm),以其它方向测量时,应对测得值进行换算,见附录C(补充件)。
11齿向误差的检验
11.1测量方法和测量仪器
齿向误差ΔFβ的测量方法有展成法、坐标法和啮合法。
展成法的测量仪器有单盘式渐开线螺旋线检查仪、分级圆盘式渐开线螺旋线检查仪、杠杆圆盘式万能渐开线螺旋线检查仪和导程仪等。
坐标法的测量仪器有螺旋线样板检查仪、齿轮测量中心、带齿向测量装置的齿轮单面啮合整体误差测量仪和三坐标测量机等。
啮合法的测量仪器有齿轮单面啮合整体误差测量仪等。
11.1.1展成法测量原理
展成法测量原理参见图22。以被测齿轮回转轴线为基准,通过精密传动机构实现被测齿轮1回转和测头2沿轴向移动,以形成理论的齿线轨迹。实际齿线与理论齿线轨迹进行比较,其差值输入记录器绘出齿向误差曲线,在该曲线上按误差定义取出ΔFβ。
图22展成法测量原理
1— 被测齿轮;2—测头;3—测头滑架
11.1.2坐标法测量原理
以被测齿轮回转轴线为基准,通过测角装置(如圆光栅、分度盘)和测长装置(如长光栅、激光)测量齿向线的回转角坐标和轴向坐标,将被测齿线的实际位置与理论坐标位置进行比较,其差值输入记录器绘出齿向误差曲线,在该曲线上按误差定义取出ΔFβ。
11.1.3啮合法测量原理
以被测齿轮回转轴线为基准,使齿条(或圆柱)与被测齿面作接触点沿被测齿面齿线移动的啮合运动,由测量该实际啮合运动与理论啮合运动之差测得齿向误差。或按16.1.1所述的测量原理,测出齿轮全齿宽整体误差曲线,在该曲线上按误差定义取出ΔFβ。
11.2测量
啮合法测量见16.2。
11.2.1测量温度
见表11。
被测齿轮精度等级 |
测量室温度 |
被测齿轮与仪器温差 |
展成法仪器 |
单盘式或坐标法仪器 |
展成法仪器 |
单盘式或坐标法仪器 |
3~5 |
20±1 |
20±2 |
≤1 |
≤2 |
6~7 |
20±2 |
20±3 |
≤2 |
≤3 |
≥8 |
20±3 |
20±5 |
≤3 |
≤4 |
11.2.2测量仪器的检定
仪器应按检定规程或其它有关技术文件的规定进行检定。经法定部门检定合格后方准使用。
11.2.3测头的选择
在保证不发生干涉和碰撞的情况下,宜选用直径较大的测头。
11.2.4测量仪器的校准
测量5级和高于5级精度的齿轮,测量前必须用经法定部门检定的齿轮螺旋线样板对仪器进行校准。
11.2.5测量基准的确定
见附录B(补充件)。
11.2.6测量位置的确定
齿向误差应在齿高中部,对齿轮沿圆周均布的不少于四个齿的左、右侧齿面进行测量。单侧齿面工作的齿轮只测工作侧齿面。
11.2.7测量的不确定度
齿向误差的测量不确定度UFβ不应大于被测齿轮齿向公差的三分之一,测量五级和高于五级精度的齿轮时,允许不大于二分之一,但此时应以五次以上重复测量结果的平均值作为测量结果。使用手提式仪器测量时的UFβ不应大于五分之一。
当不能确定测量不确定度是否满足上述要求时,应进行测量不确定度的计算。
UFβ(μm)按下式计算:
UF
β=
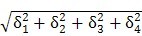
……………………(57)
式中:δ1——仪器的示值误差[见附录A(补充件),也允许按仪器检定规程确定],μm;
δ2——温度误差引起的测量误差,μm;
δ2=bud[α(t-20)αo(to-20)]tgβ·1000……………………(58)
式中:bud——被测齿向所在齿宽和度,mm。
δ3——被测齿轮测量时的安装 倾斜引起的测量误差,μm;
δ3=Δy·bud/100/cosαt………………(59)
式中:Δy——被测齿轮轴线在100mm长度上的倾斜量,μm。
δ4——被测齿轮测量时的安装偏心引起的测量误差,μm。
δ4=2e·sin(θ/2)/cosαt………………(60)
式中:θ——齿向线在齿轮分度圆柱面上所点的圆周角。(°)。
11.3测量结果处理
11.3.1取值范围的确定
齿向误差的取值范围bud应按设计图样给定的齿宽工作部分确定。当未给定时,距齿宽每端Δb齿宽部分偏向齿体的误差可不计入齿向误差,但负误差值不应超过3Fβ,Δb=bud·5%,Δb≤mn.
11.3.2齿向误差的取值
ΔFβ应从齿向误差曲线上取值,也允许在全齿宽整体误差曲线上取值(详见16.3.3.2)。对齿向线不修形的齿轮也允许直接用指示表读出齿向误差。
齿向误差曲线的X坐标代表被测齿轮轴向位置,Y坐标代表被测齿轮的齿向误差(图23)。
齿向误差曲线沿X坐标在11.3.1规定的取值范围内Y坐标的最大变化量为ΔFβ(端面倒角部分不计值)。计值范围以外的齿宽两端的齿向误差只允许偏向齿体内(见11.3.1).
ΔFβ应在被测齿轮端截面的齿轮分度圆切线方向计值(μm),以其它方向测量时,应对测得值进行换算,见附录C(补充件)。
以11.2.6所规定的各测量位置中测得的最大齿向误差作为测量结果。
图23齿向误差曲线
12接触线误差的检验
12.1测量方法和测量仪器
接触线误差ΔFb的测量方法有直接法和间接法。
直接法的测量仪器有接触线误差检查仪、具用测量接触线误差功能的渐开线螺旋线检查仪、万能工具显微镜和三坐标测量机等。
间接法的测量仪器有齿轮单面啮合整体误差测量仪等。
12.1.1直接法测量原理
直接法测量原理参见图24。以被测齿轮回转轴线为基准,齿轮固定不转使测头在齿轮基圆柱2的切平面3上沿与基圆柱母线成基圆螺旋角的斜直线方向称动,以形成理论接触线轨迹4,实际接触线与理论接触线轨迹进行比较,其最大差值即为ΔFb(图24)。也可使测头沿齿面接触线逐点与齿面接触,测量点的实际坐标位置与理论坐标位置之最大差值即为ΔFb。
图24直接法测量原理
1— 传感器;2—基圆柱;3—基圆切平面;4—接触线
12.1.2间接法测量原理
按16.1所述的测量方法,先测出齿轮全齿宽整体误差曲线,在该曲线上按误差定义取出接触线误差。
12.2测量
间接法测量见16.2。
12.2.1测量仪器的检定
仪器应按检定规程或其它有关技术文件的规定进行检定,经法定部门检定合格后方准使用。
12.2.2测头的选择
在保证不发生干涉和碰撞的情况下,宜选用直径较大的测头。
12.2.3测量基准的确定
见附录B(被充件)
12.2.4测量位置的确定
按触线误差应对齿轮沿圆周均布的不少于四个齿的左、右侧齿面在工作齿高范围内进行测量。
接触线长度Lb(mm)的所对应的齿宽baf(mm)按下列式计算:
Lb=Laf/sinβb………………(61)
baf= Laf/tgβb………………(62)
式中:Laf——见9.3.1。
当齿宽b<3baf时,所测的接触线应大致通过齿高和齿宽的中部。
当齿宽b≥3baf时,沿齿宽应至少测量上、中、下、三个部位,上、下部位被则接触线的最上一点或最下一点距端面约十分之一齿宽。
单测齿面工作的齿轮,只测工作侧齿面。
当采用设计齿形和设计齿向线时,修形部分不检ΔFb。
12.2.5测量的不确定度
接触线误差的测量不确定度UFb不应大于被测齿轮接触线公差的三分之一,测量五级和高于五级精度的齿轮时,允许不大于二分之一,但此时应以五次以上重复测量结果的平均值作为测量结果。
当不能确定测量不确定度是否满足上述要求时,应进行测量不确定度的计算。
UFb(μm)按下式计算:
UF
b=

……………………(63)
式中:δ1——仪器的示值误差[见附录A(补充件),也允许按仪器检定规程确定],μm;
δ2——被测齿轮测量时的安装倾斜引起的测量误差,μm;
δ
2=
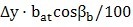
……………………(64)
式中:

——基准轴线在100mm长度上的倾斜量,μm。
12.3测量结果的处理
12.3.1取值范围的确定
接触线误差的取值范围lb应按设计图样给定的接触线长度范围确定。当未给定时,齿顶部接触线Δlb范围内偏向齿体的负误差可不计入接触线误差,但负误差值不应大于3Fb,Δlb等于lb的百分之八。
lb按下试计算:
a) 当齿宽b<baf时:Lb=Laf/sinβb……………………(65)
b) 当齿宽b≤baf时:Lb=b/cosβb……………………(66)
12.3.2接触线误差的取值
ΔFb应从接触线误差曲线上取值,也允许在全齿宽整体误差曲线上取值(详见16.3.3.3)。对齿形和齿向均不修形的齿轮也允许直接用指示表读出接触线误差。
接触线误差曲线的X坐标代表被测齿轮接触线长度,Y坐标代表接触线误差(图25)。
接触线误差曲线沿X坐标,在12.3.1的规定的取值范围lb内,Y坐标的最大变化量为ΔFb。
ΔFb应在被测齿轮的齿面法线方向计值(μm),以其它方向测量时,应对测量结果进行换算,见附录C(补充件)。
以在12.2.4所规定的各测量位置中测得的最大接触线误差作为测量结果。
图25接触线误差曲线图
13轴向齿距偏差的检验
13.1测量方法和测量仪器
轴向齿距偏差ΔFpx的测量方法有直接法和间接法。
直接法的测量仪器有上置式轴向齿距仪和旁置式轴向齿距仪等。也可在万能工具显微镜等仪器上测量。
间接法的测量仪器有齿轮单面啮合整体误差测量仪等。
13.1.1直接法测量原理
直接法测量原理又可分为比较法和绝对法。
13.1.1.1比较法
比较法测量原理参见图26。以被测齿轮轴线为基准,在与轴线平行的直线上,先用具有公称轴向齿距的基准块(或量块)校准2、3两个球测头的轴向距离,测量时把校准过的两个测头同时靠向被测齿轮轴向上两齿的同侧齿面上,直接测出齿轮的实际轴向齿距与公称轴向齿距的差值,其最大差值为轴向齿距偏差。
图26比较低法测量原理图
1— 被测齿轮;2—测头;3—测头;4—传感器
13.1.1.2绝对法
绝对法测量原理参见图27。以被测齿轮轴线为基准,在与轴线平行的直线上,用一个球测头2分别靠向不同齿的同侧齿面上,通过测长装置3(如光栅、激光、刻线尺)直接测出被测齿轮1的实际轴向齿距,所测的实际轴向齿距与公称轴向齿距的最大差值即为ΔFPX。
图27绝对法测量原理图
1— 被测齿轮;2—测头;3—长度测量系统
13.1.2间接法测量原理
按16.1所述的测量方法先测出齿轮全齿宽整体误差曲线,在该曲线上按误差定义取出ΔFPX。
13.2测量
间接法测量见16.2。
13.2.1测量温度
见表12。
表12轴向齿距偏差的测量温度
齿轮精度等级 |
测量室温度 |
工作与仪器(包括校准块)温差 |
4~5 |
20±4 |
≤2 |
6~7 |
20±6 |
≤4 |
≥8 |
20±10 |
≤6 |
13.2.2测量仪器的检定
仪器应按检定规程或其他有关技术文件的规定进行检定,经法定部门检定合格后方准使用。
13.2.3测量仪器的校准
比较法测量前、后应用量块和专用检具校准仪器。
13.2.4测量基准的确定
见附录B(补充件)。
13.2.5测量位置的确定
轴向齿距偏差应在齿高中部对圆周均布的不少于四个位置的左、右侧齿面沿轴向逐齿进行测量。单侧齿面工作的齿轮,只测工作侧齿面。
采用比较法测量时,应逐个测量各单个轴向齿距偏差,对于5级和高于5级精度的齿轮应加测跨距最大的轴向齿距偏差。
采用绝对法测量时,应以工作齿宽内最靠某端的齿为起始位置依次沿轴向逐齿测量对该齿的轴向齿距偏差。
13.2.6测量的不确定度
轴向齿距测量的不确定度UFpx不应大于被测齿轮轴向齿距极限偏差的三分之一,使用手提式仪器测量时,不应大于五分之一。
当不能确定测量不确定度是否能满足上述要求时,应时行测量不确定度的计算。
UFpx(μm)按下式计算
UF
px=
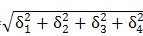
……………………(67)
式中:δ1——仪器的示值误差[见附录A(补充件)也允许按仪器检定规程确定],μm;
比较法测量时,δ1为仪器的示值变动性,μm。
δ2——传感器的示值误差,μm;
绝对法测量时,此误差已包括在δ1中,此时δ2=0。
δ3——被测齿轮与量块(或测量系统标准尺)温度不一致产生的测量误差,μm;
δ3=Lx[α(t-20)- αo(to-20)]sinβb·1000……………………(68)
式中:Lx——被测两个同侧齿面的公称轴向齿距,mm。
δ4——双测头的连心线或单测头的移动方向与轴心线不平行产生的测量误差,μm;
δ
4=

…………(69)
式中: ——在切向平面内的平行度误差,μm;
——在径向平面内的平行度误差,μm。
13.3测量结果的处理
ΔFpx的测量结果可用直接法直接在指示表上读出,也可在用间接法测得的全齿宽整体误差曲线上取值(详见16.3.3.4)。
ΔFpx应在齿面法线方向计值(μm),以其它方向测量时,应对测量结果进行换算(见附录C)。
以在13.2.5所规定的各测量位置中测得的绝对值最大的轴向齿距偏差作为测量结果。
13.3.1比较法测量结果的处理
由指示表读出的逐齿轴向齿距偏差ΔPxi经计算得到ΔFPX(见表13)。
表13逐齿测量数据处理
ΔFPXi——第i齿面相对0号齿面的轴向齿距累积偏差。
当加测跨齿距最大的轴向齿距偏差ΔPx(0-5)时,可用测得的ΔPx(0-5)对表13列误差值进行修正,按表14的计算顺序算出较精确的ΔFPX。
表14跨齿修正法数据处理
ΔPxm——轴向齿距偏差修正量;
ΔPmi——修正后逐齿单轴向齿距偏差;
ΔFpxmi——修正后第i齿相对于0齿面的轴向齿距偏差。
13.3.2绝对法测量结果的处理
用单测头在轴向上第一个齿面对零,逐齿测出各齿面相对于第一齿面的轴向齿距偏差,所测昨的各齿轴向齿距偏差中最大偏差和最小偏差之差值即为ΔFpxo
14螺旋线波度误差的检验
14.1测量方法和测量仪器
螺旋线波度误差Δffβ的测量有相对测量法和绝对测量法。
相对法的测量仪器, 有上置式波度及旁置式波度仪等。
绝对法的测量仪器有渐开线螺旋线检查仪和导程仪等。
14.1.1相对法测量原理
螺旋线波度相对测量法以三球测量为行特征。相对法又可分为单面接触法和双面接触法。
14.1.1.1单面接触法
单面接触法测量原理参见图28。以被测齿轮回转轴线为基准,用机床或仪器的螺旋运动作为测头在被测齿面沿螺旋线移动的粗传动。仪器采用旁置式,仪器上三个球测头中有两个测头是定位测头1,测量前先把二定位测头的间距调整至螺旋线波宽波距的奇数倍,测微测头2置于二定位测头的中间位置并使测头位移方向与齿面垂直,三个测头应置于单侧齿面的同一螺旋线上。测量时,依靠粗传动,三个测头沿齿面螺旋线移动,此时测微测头相对于定位测头的最大位移变化量即为2Δffβ。
图28单面接触法测量原理
1— 定位测头;2—测微测头
14.1.1.2双面接触法
双面接触法测量原理参见图29。它与单面接触法的主要差别是仪器为上置式,测量时被测齿轮不动,仪器的两个定位测头1与被测齿轮同一齿槽的左右侧齿面接触并沿齿槽作螺旋线移动,(测头3与齿顶面接触,防止转动)此时测微测头2相对于定位测头的最大位移变化量即为2Δffβ。
图29双面接触法测量原理
1— 定位测头;2—测微测头;3—防转定位测头
14.1.2绝对法测量原理
按11.1所述方法测出齿向误差曲线,在此曲线上按误差定义取出Δffβ。
14.2测量
绝对法测量见11.2。
14.2.1测量仪器的检定
仪器应按检定规程或其它有关技术文件的规定进行检定,经法定部门检定合格后方准使用。
14.2.2测头的选择与调整
双面接触测量仪器的两个定位球测头的直径应一致,并根据被测齿轮模数选择,要使定位球测头与被测齿轮齿槽的左右侧齿面大约在齿高中部接触。
单面接触测量仪器的两个定位球测头的直径应一致,并使定位测头与被测齿面大约在齿高中部接触而又不能触及另一侧齿面。
仪器两定位测头之间的距离测量前应调整到被测波度误差波距的奇数位(1、3、5……等)。波距应根据设计图样确定。在图样未作规定时,应分别按加工机床分度蜗轮副的周期误差,机床走刀架丝杠的周期误差和昼夜自然温度变化产生的齿向波度计算波距λ。
按分度蜗轮副的周期误差计算:
λ
1=

(mm)………………(70)
按走刀架丝杠的周期误差计算:
λ
2=

(mm)………………(71)
按昼夜自然温度变化计算:
λ
2=

………………(72)
式中:S——加工时工件每转进给量,mm/r;
n——单头滚刀每分钟转数,r/mim;
Zw——机床分度蜗轮齿数;
tp——刀架丝杠螺距,mm。
测微测头应位于两定位测头的1/2处,在齿面法线方向与被测齿面接触,而又不触及另一侧齿面。在保证不发生干涉和碰撞的情况下,测微测头直径应尽量接近定位测头的直径。三个测头与被测齿面的接触点应位于被测齿轮的同一条螺旋线上。
14.2.3测量位置的确定
波度误差应在齿高中部,对圆周均布的不少于4个齿槽的左右齿面在工作齿宽范围内进行测量。单侧齿面工作的齿轮只测工作侧齿面。
14.2.4测量的不确定度
波度误差的测量不确定度Uffβ不应大于被测齿轮螺旋线波度公差的五分之一。
当不能确定测量不确定度是否能满足上述要求时,应时行测量不确定度的计算。
Uffβ(μm),按下式计算:
Uf
fβ=
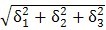
……………………(73)
式中:δ1——仪器的示值变动性[见附录A(补充件),也允许按仪器检定规程确定],μm;
δ2——传感受器的示值误差,μm;
δ3——仪器测量时定位误差引起的测量误差,μm;
单面测量法此项误差为零。
δ
3=
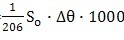
……………………(74)
式中: ——测微头球心和两定位测头球心连线的垂直距离,mm;
——测量过程中由防转定位测头在齿顶面定位点的齿顶圆半径变化引起的仪器在垂直螺旋线的平面上的转角,(″)。
14.3测量结果处理
相对法的测得值可以从波度误差曲线上读取,也可以从指示表直接读取。波度误差曲线上,多次重复出现的误差的最大波高的二分之一Δffβ
绝对法的测得值从齿向误差曲线上读取。齿向误差曲线上多次重复出现的误差的最大波高为Δffβ(图30)。
Δffβ应在被测齿面的法线方向计值(μm),以其它方向测量时,应对测量结果进行换算,见附录C(补充件)。
在14.2.3所规定的各测量位置中,以不同波距测得的最大误差作为测量结果。单侧齿面工作的齿轮只计单侧齿面的误差。
图30齿向误差曲线上取波度误差
15齿厚的检验
齿厚的检验包括齿厚偏差ΔEs、公法线平均长度偏差ΔEwm、基本齿廊位移ΔEH、量柱测量距(M值)偏差ΔEM和双啮中心距偏差 的检验。
15.1测量方法和测量仪器
齿厚的测量方法有直接法和间接法。间接法又可分为四种:公法线平均长度偏差的测量、基本齿廓位移的测量、量柱测量距(M值)偏差的测量和双啮中心中工偏差的测量。
直接法的测量仪器有齿厚游标卡尺、光学测齿卡尺等。也可在万能工具显微镜等仪器上测量。
公法线平均长度偏差的测量仪器有公法线千分尺等。也可用游标卡尺、万能工具显微镜等仪器测量。
基本齿廓位移的测量仪器有正切齿厚规等。
量柱测量距(M值)偏差的测量仪器一般用变通千分尺和标准圆柱组合使用。
双啮中心距偏差的测量仪器有双面啮合检查仪等。
15.1.1齿厚偏差的测量原理参见图31。
图31齿厚偏差测量原理。
以被测齿轮回转轴线为基准一(一般用齿轮外圆代替),测量齿轮分度圆柱上同一齿左右齿面之间的弧长或弦长,实测值与公称值之差即为齿厚偏差。各齿中最大齿厚与公称齿厚之差为齿厚上偏差ΔESS,最小齿厚与公称齿厚之差为齿厚下偏差ΔEsi。
15.1.2公法线平均长度偏差的测量原理
公法线平均长度偏差的测量原理基本和8.1.1一样,但公法线长度必须测出绝对长度,按各齿公法线实测长度,通过计算求得平均值,此平均值和公称值之差即为ΔEwm。
由于公法线测量不以齿轮回转轴线为基准,它不反蚋齿轮径向偏心误差对齿厚偏差的影响(但齿厚偏差包括径向偏心误差的影响)。因此用公法线平均长度偏差来代替齿厚偏差时,除了应按齿轮精度标准压缩齿厚偏差的公差处,还应保证齿圈径向跳动在公差范围内。
15.1.3基本齿廓位移的测量原理
基本齿廓位移测量原理参见图32。以被测齿轮回转轴线为基准(一般用齿轮外圆代替),测量被测齿轮齿体或齿槽固定弦相对于回转轴线的径向距离。实际距离与公称距离之差即为基本齿廓位移。其最大距离与公称距离这差为基本齿廓位移上偏差ΔEHs,最小距离与公称距离之差为基本齿廓位移下偏差ΔEHi。
图32基本齿廓位移测量原理图
基本齿廓位移的测量实际上也就是测量固定弦齿偏差在齿轮径向的反映值。
15.1.4量柱测量偏差的测量原理参见图33。
图33量柱测量距偏差测量原理
量柱测量距偏差的测量不需以齿轮回转轴线为基准,而是将两个与左右齿面高中部接触的精密圆柱(或圆球)放于被测齿轮沿圆周相隔180°(偶数齿)或(1-1/Z)180°(奇数齿)的两个齿槽内。用千分尺或其它通用长度量仪测量两圆柱外尺寸(内齿轮为内尺寸)之间的距离,即量柱测量距的M值。实测M值的平均值与公称M值之差为量柱测量距偏差,其最大差值即为ΔEM。
由于量柱测量距偏差不反映齿轮径向偏心误差的影响(但齿厚偏差包括齿轮径向偏心误差的影响),除了应按齿轮精度标准的规定压缩齿厚偏差的公差外,还应保证齿圈径向跳动在公差范围内。
15.1.5双啮中心距偏差的测量原理
双啮中心距偏差的测量原理和5.1.1基本一样,但测量前应按双啮中心距的公称值α″,用量块或其它标准量具将仪器对零(指示表对零或在记录纸上画一条零线),测得的实际中心距与公称中心距之差即为双啮中心距偏差。被测齿轮一转中最大中心距与公称中心距之差为双啮中心距上偏差 。
15.2测量
15.2.1齿厚偏差的测量
15.2.1.1测量仪器的检定
仪器应按检定规程或其它有关技术文件的规定进行检定,经法定部门检定合格后方准使用。
15.2.1.2测量基准有确定
应选择被测齿轮的设计基准作为测量基准。由测量时的定位误差造成的被测齿轮的径向跳动不大于齿圈径向跳动公差的八分之一。当以顶圆作测量基准时,顶圆直径即顶圆的径向跳动应符合GB10095中附录B的规定。
15.2.1.3测量位置的确定
应对沿圆周均布的至少四个轮齿进行测量,可在被测齿轮分度圆上测量分度圆弧齿厚(或弦齿厚)。也可测量固定弦齿厚。
对于斜齿轮应在法平面测量,也允许在端面测量。
15.2.1.4测量的不确定度
齿厚偏差测量的不确定度UEs不应大于齿厚极限偏差的五分之一。
当不能确定测量不确定度是否能满足上述要求时,应时行测量不确定度的计算。
UEs(μm)按下式计算:
UE
s=

……………………(75)
式中:δ1——仪器的示值误差[见附录A(补充件),也允许按仪器检定规程确定],μm;
δ2——测量圆半径的定位误差或外圆定位半径的定位误差所引起的测量误差,μm;
δ
2=2·
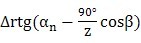
……………………(76)
式中: ——定位半径误差,μm;
Z——被测齿轮次数。
15.2.2公法线平均长度偏差的测量
15.2.2.1测量仪器的检定
仪器应按检定规程或其它有关技术文件的规定进行检定,经法定部门检定合格后方准使用。
15.2.2.2测量位置的确定
两平行量爪应跨一定齿数,决定跨齿数时应保证两测量面大约于齿高中部与两异测齿面相切。
至少测量被测齿轮沿圆周均布的四个位置的公法线长度。
15.2.2.3测量的不确定度
公法线平均长度偏差测量的不确定度UEwm不应大于公法线平均长度公差的五分之一。
当不能确定测量不确定度是否能满足上述要求时,应进行测量不确定度的计算。
UEwm(μm)按下式计算:
UEwm=δ1……………………(77)
式中:δ1——仪器的示值误差[见附录A(补充件),也允许按仪器检定规程确定],μm。
15.2.3基本齿廓位移的测量
15.2.3.1测量仪器的检定
仪器应按检定规程或其它有关技术文件的规定进行检定,经法定部门检定合格后方准使用。
15.2.3.1测头的选择与调整
测头可以是具有标准基本齿廓的齿槽测头,也可以是具用标准基本齿廓的齿本齿头或具有标准压力角的圆锥测头。
测头所具有的标准基本齿廓的模数和压力角应和被测齿轮一致。
基本齿廓相对被测齿轮回转轴线(或用外圆找替)的理论径向位置在测量前应先用标准齿轮或标准圆柱或其经标准化校准。
15.2.3.3测量基准的确定
见15.2.1.2。
15.2.3.4测量位置的确定
应对沿圆周均布的至少四个轮齿进行测量。可以测量齿体固定弦,也可测量齿槽固定弦。
15.2.3.5测量的不确定度
基本齿廓位移测量的不确定度UEH不应大于基本齿廓位移公差的五分之一。
当不能确定测量不确定度是否满足上述要求时,应进行测量不确定度的计算。
UEH(μm)按下式计算:
UE
H=
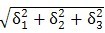
……………………(78)
式中:δ1——仪器的示值误差[见附录A(补充件),也允许按仪器检定规程确定],μm;
δ2——传感器的示值误差,μm;
δ3——齿顶圆半径的定值误差,μm。
不用齿顶圆定位时,δ3=0
15.2.4量柱测量距(M距)偏差的测量
15.2.4.1测量仪器的检定
仪器应按检定规程或其它有关技术文件的规定进行检定,经法定部门检定合格后方准使用。
15.2.4.2测量圆柱(或圆球)的选择
测量圆柱(或圆球)的直径按被测齿轮的模数来选择,应保证能与被测齿槽的左右齿面在分度圆附近接触。
15.2.4.3测量位置
至少测量圆周上均布的两对齿的M值。
15.2.4.4测量的不确定度
量柱测量距偏差测量的不确定度UEM不应大于被测齿轮量柱测量距公差的五分之一。
当不能确定测量不确定度是否能满足上述要求时,应进行测量不确定度的计算。
UEM(μm)按下式计算:
UE
M=

……………………(79)
式中:δ1——仪器的示值误差[见附录A(补充件),也允许按仪器检定规程确定],μm;
δ2——测量圆柱(或圆球)引起的误差,μm;
δ
2=2·
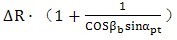
……………………(80)
式中: ——测量圆柱(或圆球)的半径误差,μm;
——圆柱(或圆球)中心点的端面压力角,(°)。
15.2.5双啮中心距偏差的测量
15.2.5.1测量仪器的检定
仪器应按检定规程或其它有关技术文件的规定进行检定,经法定部门检定合格后方准使用。
15.2.5.2测量元件的选择
测量元件应为测量齿轮或测量蜗杆。
测量元件的法向模数mn和法向压力角αn应与被测齿轮一致。
测量元件齿厚的实际值应标注在测量元件上或专用检验单上。
测量齿轮各齿厚的变动量不应大于被测齿轮齿厚公差的八分之一。
15.2.5.3测量基准的确定
见附录B(补充件)。
15.2.5.4测量位置的确定
应在齿高和齿宽中部对所有齿进行测量。
15.2.5.5测量的不确定度
双啮中心距偏差测量的不确定度UEa″不应大于被测齿轮双啮中心距公差的三分之一。
当不能确定测量的不确定度是否满足上述要求时,应进行测量不确定度的计算。
UEa″(μm)按下式计算:
UE
a″=

……………………(81)
式中:δ1、δ2、δ3、δ5、δ6见5.2.5.1;
δ4——测量齿轮齿厚变动量ΔSp(μm)引起的测量误差,μm;
δ
4=

……………………(82)
δ7——公称中心距调整误差,μm。
15.3测量结果处理
15.3.1齿厚偏差测量结果处理
以在15.2.1.3所规定的各测量位置中测得的最大齿厚偏差和最小齿厚偏差作为测量结果。
ΔEss、ΔEsi以被测齿轮双侧齿面分度圆螺旋线的法线方向计值(μm),以其它方向测量时,应对测量结果进行换算,见附录C(补充件)。
15.3.2公法线平均长度偏差测量结果处理
以在15.2.2.2所规定的各测量位置中测得的各个公法线各个公法线长度偏差的算术平均值作为测量结果。
ΔEwm以被测齿面法线方向计值(μm),以其他方向测量时,应对测量结果进行换算,见附录C(补充件)。
对公法线平均长度偏差的测量结果ΔEwm,应用设计图样规定的公法线平均长度极限偏差ΔEwms、ΔEwmi对其进行评定。当设计图样未作规定时,应将图样规定的齿厚极限偏差Ess、Esi按公试(83)、(84)换算为Ewms、Ewmi;也可将测得的ΔEwm按分式(85)、(86)换算为ΔEss、ΔEsi,用设计图样规定的Ess、Esi对其进行评定。
将Ess、Esi换算成Ewms,Ewmi的换算式为:

……………………(83)

……………………(84)
在使用上述换算式时,应保证被测齿轮的ΔFr在允许公差Fr范围内。
将ΔEwm换算成ΔEss、ΔEsi的换算式为:
ΔE
ss=
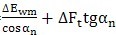
……………………(85)
ΔE
si=
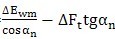
……………………(86)
若被测齿轮的ΔFr在允许公差Fr范围内,上两式中的ΔFr可以用0.72Fr代替。
15.3.3基本齿廓位移测量结果处理
以在15.2.3.4所规定的各测量位置中测得的最大基本齿廓位移和最小基本齿廓位移作为测量结果。
ΔEHs,ΔEHi以被测齿轮的双侧齿面径向计值(μm),以其它方向测量时,应对测量结果进行换算,见附录C(补充件)。
对基本齿廓位移的测量结果ΔEHs,ΔEHi,应用设计图样规定的基本齿廓位移极限偏差EHs,EHi对其进行评定。当设计图样未作规定时,应将图样规定的齿厚极限偏差Ess、Esi按公试(87)、(88)换算成EHs、EHi;也可以将测得的ΔEHs,ΔEHi,按公试(89)(90)换算为ΔEss、ΔEsi,用设计图样规定的Ess、Esi对其进行评定。
将Ess、Esi换算为EHs、EHi换算式为:

……………………(87)

……………………(88)
将ΔEHs,ΔEHi换算为ΔEss、ΔEsi的换算式为:
ΔE
ss=

E
Hs 
……………………(89)
ΔE
si=

E
Hi 
……………………(90)
15.3.4量柱测量距(M值)偏差测量结果处理
以在15.2.4.3所规定的各测量位置中测得的各个M值的算术平均值作为测量结果。
ΔEM以被测齿轮的双侧齿面径向计值(μm),以其它方向测量时,应对测量结果进行换算,见附录C(补充件)。
对量柱测量齿距(M值)偏差的测量结果ΔEM应用设计图样规定的量柱测量距极限偏差EMs、EMi对其进行评定。当设计图样未作规定时,应将图样规定的齿厚极限偏差Ess、Esi按公试(91)、(92),(93),(94)换算为EMs、EMi;也可以将测得的ΔEM按公试(95),(96)(97),(98)换算为ΔEss、ΔEsi,用Ess、Esi对其进行评定。
将Ess、Esi换算成EMs、EMi的换算式为:
被子测齿轮炎偶数齿时

……………………(91)

……………………(92)
被测齿轮为奇数齿时

……………………(93)

……………………(94)
在使用上述换算式时,应保证被测齿轮的ΔFr在允许公差Fr范围内。
将ΔEM换算成ΔEss、ΔEsi换算式为:
被测齿轮为偶数齿时

……………………(95)

……………………(96)
被测齿轮为奇数齿时

……………………(97)
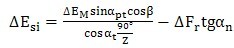
……………………(98)
若被测齿轮的ΔFr在允许公差Fr范围内,ΔFr可以用0.72Fr代替。
15.3.5双啮中心距偏差
以在15.2.5.4所规定的各测量位置中测得的双啮中心距最大时的中心距偏差作为上偏差ΔEas″,双啮中心距最小时的中心距偏差作为下偏差ΔEai″。
ΔEas″、ΔEai″应在被测齿轮双侧齿面的径向计值(μm),以其它方向测量时,应对测量结果进行换算,见附录C(补充件)。
对双啮中心距偏差测量结果ΔEas″,ΔEai″应用设计图样规定的双啮中心距极限偏差Eas″,Eai″对其进行评定。当设计图样未作规定时,应将图样规定的Ess、Esi按公式(99),(100)换算成Eas″,Eai″;也可以将测得的ΔEas″,ΔEai″按公式(101),(102)换算为ΔEss、ΔEsi,用Ess、Esi对其进行评定。
将Ess、Esi换算为Eas″,Eai″的换算式为:
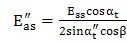
………………(99)
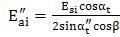
………………(100)
将ΔEas″,ΔEai″换算为ΔEss、ΔEsi的换算式为:
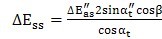
……………………(101)
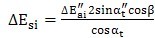
……………………(102)
以上各式中αt″为双面啮合时的端面啮合角,(°)。
16整体误差的检验
整体误差有检验包括切向综合误差ΔFi′、一齿切向综合误差Δfi′、齿距累积误差ΔFP、k个齿距累积误差ΔFPk、齿圈径向跳动ΔFr、齿向偏差Δfpt、基节偏差Δfpb、齿形误差Δff、齿向误差ΔFβ、接触线误差ΔFb和轴向齿距偏差ΔFpX等的检验。
ΔFP、ΔFPk、Δfpt、Δfpb、Δff、直齿轮的ΔFi′和Δfi′在截面整体误差曲线上取值;ΔFβ、ΔFP、ΔFpX、斜齿轮的ΔFi′和Δfi′在全齿宽整体误差曲线上取值;ΔFr在双向截面整体误差曲线上取值。
16.1测量方法和测量仪器
整体误差的测量方法有啮合法和坐标法。
啮合法的测量仪器有齿轮单面啮合整体误差测量仪等。
坐标法的测量仪器有万能齿轮测量机等。
16.1.1啮合法测量原理
啮合法测量原理参见图34。以被测齿轮回转轴线为基准,使被测齿轮1和间齿测量齿轮或间齿测量蜗杆2作单面啮合传动,将此传动与标准传动发生装置3所发生的标准传动相比较,通过误差处理系统4测量出被测齿轮的实际回转角与理论回转角的差值,由同步记录器5将其记录成整体误差曲线。对被测齿轮某一截面测得的上述曲线称作截面整体误差曲线,它是由各齿齿形误差曲线按啮合时的相对角坐标位置排列组成。左右齿面的截面整体误差曲线按啮合时的相对角坐标位置排列组成双向截面整体误差曲线。全齿宽不同截面的整体误差曲线按啮合时的相对角坐标位置排列组成全齿宽整体误差曲线。在上述三种整体误差曲线上按误差定义取出各种误差。
图34啮合法测量原理图
1— 被测齿轮;2—测量蜗杆;3—标准误差发生装置;
4—误差处理系统;5—同步记录器
16.1.2坐标法测量原理
坐标法测量原理参见图35。以被测齿轮回转轴线为基准,测头2与被测齿轮1的齿面接触,被测齿轮回转,接触点沿被测齿轮的基圆切线移动,由测长传感器3和测角传感器6测量出测头的直线位移量和被测齿轮的角位移量,经误差处理系统与理论位移量进行比较,其差值即为单齿齿形误差,再经测角传感器6测出各齿齿距偏差,由同齿记录器5将其记录成整体误差曲线(包括截面整体误差曲线、双向截面整体误差曲线、全齿宽整体误差曲线见(16.1.1)),在该曲线上按误差定义取出各种误差。
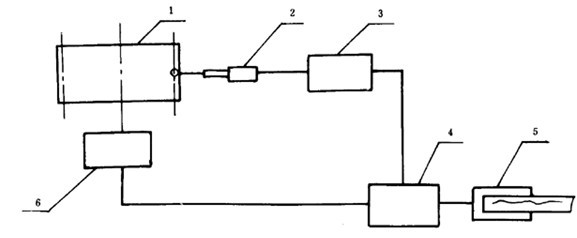
图35坐标法测量原理图
1— 被测齿轮;2—测头;3—测长传感器;4—误差处理系统;
5—同步记录器;6—测角传感器
16.2测量
16.2.1测量温度
见表15。
表15整体误差的测量温度
被测齿轮精度等级 |
测量室温度 |
被测齿轮与测量仪器(或测量元件)的温差 |
啮合法 |
坐标法 |
啮合法 |
坐标法 |
4~5 |
20±4 |
20±2 |
≤2 |
≤2 |
6~7 |
20±6 |
20±3 |
≤4 |
≤3 |
≥8 |
20±10 |
20±5 |
≤6 |
≤4 |
16.2.2测量仪器的检定
仪器应按检定规程或其它有关技术文件的规定时行检定,经法定部门检定合格后方准使用。
16.2.3测量元件的选择
啮合法测量元件可以是间齿测量蜗杆或间齿测量齿轮。测量元件的法向模数mn、法向压力角αn应与被测齿轮一致;测量元件的工作齿高应大于或等于被测齿轮的工作高;测量齿轮的精度和参数应符合JB3887的规定;测量蜗杆的精度和参数应符合ZB J42006的规定。
坐标法的测头可为球形、倒锥形、锥形或圆柱形。在保证不与另侧齿面和齿底面发生干涉和碰撞的情况下,宜选择直径较大的测头。测头的工作点应位于被测齿轮的基圆切平面上,其偏离量不大于±0.02mm。
16.2.4测量仪器的校准
测量5级和高于5级精度的齿轮时,测量前必须用经法定部门检定的标准元件(标准齿轮或样板)对仪器(包括测量元件)进行校准(见表16)。标准元件的检定误差不应大于被测齿轮允许公差的六分之一。
表16仪器应校准的误差项目
仪器用于检测齿轮的误差项目 |
应校准的误差项目 |
Δff
ΔFβ
ΔFP
ΔFPK
ΔfPt
ΔFi′
Δfi′
ΔFPx
ΔfPb |
Δff
ΔFβ
ΔFP
ΔFP
ΔfPt
ΔFP、Δff、ΔfPt
Δff、ΔfPt
ΔFβ、ΔfPt
Δff、ΔfPt |
16.2.5测量基准的确定
见附录B(补充件)
16.2.6测量位置的确定
对于Δff、Δfpb、Δfpt、ΔFP、ΔFPk和直齿轮的ΔFi′和Δfi′应测量截面整体误差曲线,测量截面应大致位于齿宽中部,但当齿宽大于160mm时应至少测量上、中、下三个截面,上、下截面各距端约百分之十五齿宽。
对于斜齿轮的ΔFβ、ΔFb、ΔFi′和Δfi′;应测量至少由5条截面整体误差曲线组成的全齿宽整体误差曲线,对于直齿轮的ΔFβ和ΔFb允许少至三条。截面间距应沿全齿宽均布。测量ΔFPX时,截面间距应等于被测齿轮的公称轴向齿距。
对于ΔFr应测双向截面整体误差曲线。测量截面应大致位于齿宽中部,但当齿宽大于160mm时,应至少测量上、中、下三个截面,上、下截面各距端面约百分之十五齿宽。
在测量Δff、Δfpb、ΔFb、ΔFi′和Δfi′时,被测截面应大于或等于图纸规定的工作齿高,当图纸未作规定时,按被测齿轮与基齿条啮合计算工作齿高。
除ΔFr外,其它各项误差均应分别对左、右侧齿面进行测量。单侧齿面工作的齿轮只测工作侧齿面。
16.2.7测量不确定度
切向综合误差的测量不确定度U fi′、一齿切向综合误差的测量不确定度U fi′、齿距累积误差的测量不确定度UFP、 k个齿距累积误差的测量不确定度UFpk、齿圈径向跳动的测量不确定度UFr、齿距偏差的测量不确定度Ufpt、基节偏差的测量不确定度Ufpt、齿形误差的测量不确定度Uff、齿向误差的测量不确定度UFβ、接触线误差的测量不确定度UFb和轴向齿距偏差的测量不确定度UFpx均不应大于被测齿轮对应误差项目公差的三分之一。测量5级和高于5级精度的齿轮时,允许不大于二分之一,但此时应以五次以上重复测量结果的平均值作为测量结果。
当不能确定测量不确定度是否能满足上述要求时,应按下述方法确定测量不确定度。
16.2.7.1齿形误差的测量不确定度Uff的计算
Uff(μm)按下式计算:
Uf
f=

……………………(103)
式中:δ1——仪器测量齿形误差时的示值误差[见附录A(补充件),也允许按仪器检定规程确度],μm;
δ2——测量元件制造误差引起的测量误差,μm;
测量元件为测量蜗杆时,δ2=ΔTo;
测量元件为测量齿轮时,δ2=Δffo;
测量元件为测量头时,δ2=0;
δ3——温度误差引起的测量误差,μm;
δ3=Laf[α(t-20)-αo(to-20)]·1000………………(104)
δ4——被测齿轮测量时的安装偏心引起的测量误差,μm;

………………(105)
δ5——测量元件的定位误差引起的测量误差,μm;
测量元件为测量齿轮时,
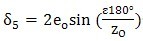
………………(106)
测量元件为测量蜗杆时,
δ
5=

………………(107)
δ51——测量蜗杆安装偏心引起的测量误差,μm;
δ
51=

………………(108)
δ52——测量蜗杆轴向窜动引起的测量误差,μm。
δ
52=ΔU
ocos

……………………(109)
若δ1是在测量前用标准齿轮校准测量蜗杆时测得的,即δ1中已包括δ2和δ5,则δ2=0、δ5=0。若δ2式中的ΔTo是在测量前用标准齿轮校准测量蜗杆时测得的,即δ2中已所括δ5,则δ5=0。
16.2.7.2齿距累积误差测量不确定度UFP
UFP(μm)按下式计算:
UF
P=

………………(110)
式中:δ1——仪器测量齿距累积误差时的示值误差[见附录A(补充件),也允许按仪器检定规程确定],μm;
δ2——被测齿轮测量时的安装偏心引起的测量误差。μm;
δ
2=

………………(111)
16.2.7.3齿距偏差测量不确定度Ufpt
Ufpt(μm)按下式计算:
Uf
Pt=

………………(112)
式中:δ1——仪器测量齿距偏差时的示值误差[见附录A(补充件),也允许按仪器检定规程确定],μm;
δ2——被测齿轮测量时安装偏心引起的测量误差,μm。
δ
2=

……………………(113)
16.2.7.4齿向误差的测量不确定度UFβ
UFβ(μm)按下式计算:
UF
β=

………………(114)
式中:δ1——仪器测量齿向误差时的示值误差[见附录A(补充件),也允许按仪器检定规程确定],μm;
δ2——被测齿轮测量时的安装偏心引起的测量误差,μm;
δ
2=
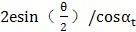
……………………(115)
式中: ——齿线在分度圆柱面上所占的圆周角,(°)
δ3——温度误差引起的测量误差,μm;
δ3=bud[α(t-20)-αo(to-20)]tgβ·1000………………(116)
δ4——被测齿轮子测量时的安装倾斜面引起的测量误差,μm。
δ4=ΔSt/cosαt……………………(117)
式中:ΔSt——是被测齿宽范围内的倾斜量,μm。
16.2.7.5其它各项误差的测量不确定度
其它各项误差的测量不确定度均是由上述四项基本误差中某几项的测量不确定度组合成的,其组成关系见表17。表中左边所列误差项目的测量不确定度不需再作计算,而是要求列于表中右边参与组合的误差项目的测量不确定度应不大于该项误差在与左边的误差项目的精度级相同时的公差的三分之一。测量5级和高于5级精度的齿轮时,允许不大于二分之一,但此时应以五次以上重复测量结果的平均值作为测量结果。
表17测量不确定度的组合关系
其它各项误差(被组成的误差项目) |
参与组合的误差项目
的测量不确定度 |
名称与代号 |
测量不确定度代号 |
切向综合误差ΔFi′
一齿切向综合误差Δfi′
接触线误差ΔFb
轴向齿距偏差ΔFPx
基节偏差ΔfPb |
UFi′
Ufi′
UFb
UFPx
UfPb |
UFP、Uff、UfPt
Uff、UfPt
U Fβ、Uff
UFβ、UfPt
Uff、UfPt |
16.3测量结果处理
整体误差曲线的X坐标代表被测齿轮的回转角,Y坐标代表被测齿轮的误差。
以在16.2.6规定的各测量位置中测得的最大误差(或偏差)作为测量结果。
16.3.1截面整体误差曲线
16.3.1.1截面切向综合误差ΔFij′和截面一齿切向综合误差Δfij′的取值
ΔFij′和Δfij′应在截面切向综合误差曲线上取值。截面整体误差曲线的外轮廓线就是截面切向综合误差曲线(图36)。
截面切向综合误差曲线沿X坐标360°范围内Y坐标的最大变化量为ΔFij′,沿X坐标 范围内Y坐标的最大变化量为Δfij′。
ΔFij′和Δfij′应在被测齿轮分度圆的切线方向计值(μm),沿其它方向测量时应对测量值进行换算,见附录C(补充件)。
图36截面整体误差曲线取值示意图
16.3.1.2齿距偏差ΔfPt、齿距累积误差ΔFb和K个齿距累积误差ΔFPK的取值
各齿齿形误差曲线上(图36),大致位于误差曲线中部,X坐标间隔360°/Z的误差点为齿距误差取值点。
所有齿距误差取值点Y坐标的最大变化量为ΔFP。
相隔k个齿距(K=360°/Z)两个误差取值点Y坐标的最大变化量为ΔFPK。
相邻两个误差取值点Y坐标的最大变化量为ΔFPt。
ΔfPt、ΔFP、ΔFPK应在被测齿轮分度圆的切线方向计值(μm),沿其它方向测量时应对测量值进行换算,见附录C(补充件)。
ΔfPt的“+”“-”按下述方法确定,所测齿面上的误差取值点较先测齿面上的误差取值点正,则为+ΔfPt,反之则为-ΔfPt。以绝对值最大的齿距偏差作为齿距偏差的测量结果。
16.3.1.3齿形误差Δff
X坐标在齿形工作范围φaf(或Laf)内,Y坐标的最大变化量为Δff(图36)。
Δff应在被测齿轮的基圆切线方向计值(μm),沿其它方向测量时应对测量值进行换算,见附录C(补充件)。
16.3.1.4基节偏差ΔfPb的取值
在相邻两条齿形误差曲线上(图36),位于同一X坐标的二个齿形工作范围内的误差点的Y坐标的最大差值为ΔfPb(齿形修形部分不计值)。
在上述的二个误差点中,Y坐标偏正的点位于齿形误差曲线的顶部时为+ΔfPb,反之则为-ΔfPb。以绝对值最大的基节偏差作为基节偏差的测量结果。
ΔfPb应在被测齿轮的齿面法线方向计值(μm),沿其它方向测量时应对测量值进行换算,见附录C(补充件)。
16.3.2双向截面整体误差曲线
16.3.2.1齿圈径向跳动ΔFr的取值
在左右齿面的截面整体误差曲线上(图37),代表轮齿(或齿槽)固定弦位置的一对误差取值点为CL、CR(或CL′、CR′),CL与CR或(CL′与CR′)应位于同一X坐标上,且到各自齿形误差曲线的齿顶(或齿根)点的展开角相等。
CL′和CR′(或CL′与CR′)间的Y坐标距离为LC(或LC′),被测齿轮所有轮齿(或齿槽)的LC(或LC′)的最大变化量为ΔFr。
ΔFr应在被测齿轮双侧齿面的径向计值(μm),沿其它方向测量时应对测量值进行换算,见附录C(补充件)。
图37ΔFr取值示意图
16.3.3全齿宽整体误差曲线
16.3.3.1切向综合误差ΔFi′和一切向综合误差Δfi′的取值
全齿宽整体误差曲线的外廓线沿X坐标360°范围内Y坐标的最大变化量为ΔFi′,沿X坐标 范围内Y坐标的最大变化量为Δfi′。
Δfi′和ΔFi′应在被测齿轮分度圆切线方向计值(μm),沿其它方向测量时应对测量值进行换算见附录C(补充件)。
16.3.3.2齿向误差ΔFβ的取值
同一齿面的各截面齿形误差曲线上(图38),大约位于齿形误差曲线的中部且距各自的齿顶点(或齿根点)的展开角相等的点为齿向误差取值点。
同一齿面的各齿向误差取值点的Y坐标最大差值为该齿面的齿同误差。以所有齿面的最大齿向误差作为ΔFβ的测量结果。
ΔFβ应在被测齿轮的分度圆切线方向计值(μm),沿其它方向测量时应对测量值时行换算,见附录C(补充件)。
图38ΔFβ取值示意图
16.3.3.3接触线误差ΔFb的取值
同一齿面的各截面齿形误差曲线上(图39),X坐标相同的各误差点为接触线误差的取值点。
各取值点的Y坐标最大差值为该接触线的接触线误差。以各齿面及各X坐标上测得的最大接触线误差作为ΔFb的测量结果(齿形或齿向的修形部分不计值)。
ΔFb应在被测齿轮的齿面法线方向计值(μm)沿其它方向测量时应对测量值进行换算,见附录C(补充件)。
图39ΔFb取值示意图
16.3.3.4轴向齿距偏差ΔFpx的取值
轴向齿距偏差ΔFpx应在截面间距等于轴向齿距的全齿宽整体误差曲线上取值(图40)。
在此误差曲线图上,当截面变化一个轴向齿距时,相邻二齿的齿形误差曲线的X坐标完全重合。X坐标完全重合的各齿面的齿形误差曲线的中点为轴向齿距偏差取值点。
各取值点Y坐标的最大差值为ΔFpx。
ΔFpx应在被测齿轮的齿面法线方向计值(μm),沿其它方向测量时应对测量值进行换算,见附录C(补充件)。
图40ΔFpx取值示意图
17齿轮副单啮综合误差的检验
齿轮副单啮综合误差的检验包括齿轮副的切向综合误差ΔFic′和齿轮副的一齿切向综合误差Δfic′的检验。
17.1测量方法和测量仪器
齿轮副单啮综合误差的测量方法有传动链法和成对法。
传动链法的仪器有光栅式传动链测量仪、地震式传动链测量仪和磁分度式传动链量仪等。
成对法的仪器有齿轮式单面啮合检查仪等。
17.1.1传动链法测量原理
传动链法测量原理参见图41。在安装好齿轮副的箱体上用传动链测量仪测量。传动链测量仪有两个回转测量头2、3,分别同轴安装在一对被测齿轮副1的两个齿轮的轴端,并分别与两个被测齿轮同步回转,通过与标准传动链4进行比较,连续测出被测齿轮实际回转角与理论回转角的差值,通过同步记录系统5将其记录成齿轮副单啮综合误差曲线,在该曲线上按误差定义取出ΔFic′和Δfic′。
图41传动链式法测量原理
1— 齿轮副;2、3—回转测量头;4—标准传动链;
5—同步记录系统;6—箱体
17.1.2成对法测量原理
将一对被测齿轮副安装在齿传输线式单面啮合检查仪上进行单面啮合成对测量(详见4.1.1)。也允许分别测量两个齿轮的ΔFi′和Δfi′,经计算合成ΔFic′和Δfic′。
17.2测量
17.2.1测量仪器的检定
仪器应按检定规程或其它有关技术文件的规定进行检定,经法定部门检定合格后方准使用。
17.2.2测量基准的确定
见附录B(补充件)。
17.2.3测量位置的确定
应在中心距和使用时中心距相同的情况下,分别对左右侧齿面进行测量。单侧齿面工作的齿轮只测工作侧齿面。
17.2.4啮合圈数的确定
应在啮合传动足够多的圈数内测量齿轮副的单啮综合误差。若小齿轮(齿数Z1)为主动齿轮,大齿轮(齿数为Z2)为被动齿轮,则大齿轮的转动圈数n2可按下式计算:
n
2=

………………(118)
式中:X——Z1和Z2的公因数。
当Z1和Z2互为质数时,可认为X=1,故n2= Z1(转)。
17.2.5测量的不确定度
齿轮副的切向综合误差的测量不确定度U Fic′和齿轮副的一齿切向综合误差的测量不确定度U Fic′不应大于被测齿轮对应误差项目公差的三分之一,测量五级和高于五级精度的齿轮时,允许不大于二分之一,但此时应以五次以上重复测量结果的平均值作为测量结果。
当不能确定测量不确定度是否能满足上述要求时,应时行测量不确定度的计算。
17.2.5.1齿轮副的U Fic′的计算
U Fic′(μm)按下式计算:
U F
ic′=
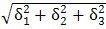
………………(119)
式中:δ1——仪器测量齿轮副切向综合误差时的示值误差[见附录A(补充件),也允许按仪器检定规程确定],μm;
δ2——主动齿轮测量时的安装偏心e1(μm)引起的测量误差,μm;
δ2=2 e1/cosαt1……………………(120)
传动链测量时δ2=0。
δ3——被动齿轮测量时的安装偏心e2(μm)引起的测量误差,μm。
δ3=2 e3/cosαt3……………………(121)
传动链测量时δ3=0。
17.2.5.2齿轮副U fic′的计算
U f
ic′=
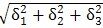
………………(122)
式中:δ1——仪器测量一齿切向综合误差时的示值误差[见附录A(补充件),也允许按仪器检定规程确定],μm;
δ2——主动齿轮测量时的安装偏心e1(μm)引起的测量误差,μm;
δ
2=

……………………(123)
传动链测量时δ2=0。
δ3——被动齿轮测量时的安装偏心e2(μm)引起的测量误差,μm;
δ
3=

……………………(124)
传动链测量时δ3=0。
17.3测量结果处理
ΔFic′和Δfic′应从齿轮副的的单啮综合误差曲线上取值。也允许以单个齿轮的ΔFi′之和及Δfi′之和作为测量结果。
单啮综合误差曲线的X坐标代表被测齿轮的回转角,Y坐标代表被测齿轮转角误差(图42)。
ΔFic′和Δfic′应在分度圆切线方向计值(μm),以其它方向测量时,应对测量结果进行换算,见附录C(补充件)。
图42齿轮副单啮综合误差曲线
单啮综合误差曲线在X坐标n2360°范围内,Y坐标的最大变化量为ΔFic′;在X坐标360°/Z2 范围内,Y坐标的最大变化量为Δfic′。
以左右侧齿面测得值中的最大误差作为测量结果,单侧齿面工作的齿轮只计工作侧齿面的误差。
18齿轮副接触斑点的检验
18.1测量方法和测量仪器
齿轮副接触斑点的测量方法有光泽法和着色法。
齿轮副接触斑点的检验应在箱体中进行,也可以在齿轮副滚动试验机上或齿轮式单面啮合检查仪上进行。
18.1.1光泽法的测量原理
光泽法是在被测齿轮副齿面上不涂涂料进行测量,经足够时间的啮合运转,使齿面能见到清晰的擦亮痕迹。
18.1.2着色法的测量原理
先在被测齿轮副中的小齿轮部分齿齿面上涂以适当的厚度的涂料,攀动小齿轮轴使齿轮副作工作齿面的啮合,直至齿面上出现清晰的涂料被擦掉的痕迹。
18.2测量
18.2.1测量仪器的检定
仪器应按检定规程或其它有关技术文件的规定进行检定,经法定部门检定合格后方准使用。
18.2.2测量基准的确定
见附录B(补充件)。
18.2.3测量位置的确定
应在中心距和使用时中心距相同的情况下对左右齿面时行测量。单侧齿面工作的齿轮许只测工作侧齿面。
18.2.4着色法的涂层
涂层应涂于小齿轮的不少于5个齿的工作齿面上。涂层应均匀,其厚度不应大于6μm。
18.2.5测量力和啮合转数
在轻微制动的条件下进行测量。
光泽法需进行连续回转,直至齿面上的接触擦亮痕迹充分呈现出来。
着色法测量时,小齿轮可正反反复转动也可作连续回转,直至齿面上接触斑点充分呈现出来。
18.3测量结果处理
齿轮副的接触斑点应以小齿轮齿面上的斑点为准,并以小齿轮齿面上接触斑点面积最小的齿面所计算的接触斑点的大小,作为测量结果。
18.3.1接触斑点的大小
接触斑点的大小是以在齿面上接触痕迹沿齿长方向的长度(扣除超过模数值的断开部分)和沿齿高方向的平均高度分别相对于工作长度和工作高度之比的百分比来确定(图43)。
18.3.1.1沿齿长方向接触痕迹的百分比计算
沿齿长方向接触痕迹的百分比为:
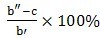
………………(125)
式中:b″——接触痕迹的总长度(包括断开部分),mm;
c——超过模数值的断开部分的长度,mm;
b′——工作长度,mm。
18.3.1.2沿齿高方向接触痕迹的百分比计算
沿齿高方向接触痕迹的百分比为:

………………(126)
式中:h″——接触痕迹的平均高度,mm;
h′——工作高度,mm。
图43接触斑点图
18.3.2接触斑点的位置
对于齿面不修形的齿轮,接触斑点的分面位置应趋近齿面中部,齿顶和两端部棱边不允许接触。
对于修形齿轮,接触斑点的位置按设计规定。
19齿轮副侧隙的检验
齿轮副侧隙的检验包括齿轮副圆周侧隙jt和法向侧隙jn的检验。
19.1测量方法和测量仪器
齿轮副侧隙的测量方法有单点法、单啮法和双啮法。
单点法在箱体上对安装好的齿轮副进行测量,也可在滚动试验机上进行测量。
单啮法的仪器有齿轮式单面啮合检查仪和传动链测量仪。
双啮法的仪器有双面啮合检查仪。
19.1.1单点法测量原理
单点法测验量圆周侧隙时的原理参见图44。单点测量圆周侧隙时,在中心距和使用时中心距相同的情况下,将齿轮副的一个齿轮固定,在另一个齿轮的分度圆切线方向上置一百分表然后晃动此齿轮,其晃动量由百分表读出,即为圆周侧隙值。
图44圆周侧隙单点测量示意图
单点法测量法向侧隙的原理参见图45。单点测量法向侧隙时:在中心距和使用时中心距相同的情况下,可用测片或塞片进行测量。也可和测量圆周侧隙相似使用百分表,但要将百分表测头放置在与齿面垂直的方向上,此时从百分表上读出的晃动量即为法向侧隙值。
图45法向侧隙单点测量示意图
19.1.2单啮法测量原理
在中心距和使用时中心距相同的情况下,按17.1.1和17.1.2的测量原理,以同一零位测出左、右齿面的齿轮副切向综合误差曲线。左右齿面的齿轮副切向综合误差曲线之间的距离即为齿轮副侧隙(图46)。
图46单啮法侧隙形成示意图
19.1.3双啮法测量原理
双啮法测量原理参见图3。它是在一般双啮测量的基础上扩展的。双啮法测量侧隙需先按齿轮副实际使用时的公称中心距来校准双啮仪的测量中心距并使测微装置4置零,并在记录纸上画出零线,然后再按5.1.1的测量方法测出带零线的径向综合误差曲线(参见图47)。曲线和零线之间的距离即为侧隙在双啮中心距方向的反映值。在该曲线上按误差定义取出jn和jt。
图47带零线的径向综合误差曲线
19.2测量
19.2.1测量仪器的检定
仪器应按检定规程或其它有关技术文件的规定进行检定,经法定部门检定合格后方准使用。
19.2.2测量基准的确定
见附录B(补充件)。
19.2.3单点法测量位置的确定
应对大齿轮每转过大约60°的位置进行齿轮副侧隙的测量。
19.2.4单啮法,双啮法啮合圈数的确定
应在大齿轮一圈的范围内进行齿轮副侧隙的测量。
19.3测量结果的处理
单点法测量侧隙时,可直接在指示表上读出或根据测片或塞片的厚度定值。以在19.2.2所规定的各测量位置中,测得的最大侧隙和最小侧隙作为测量结果。
单啮法测量侧隙时,以同零位测出的左右齿面的单啮综合曲线之间的距离来定值(参见图46)。
双啮法测量的侧隙在带零线的径向综合误差曲线(图47)上取值。X轴就是零线,X坐标代表大齿轮的回转角,Y坐标代表侧隙。曲线在X坐标360°范围内,Y坐标的最小负值为jn min(或jt min),最大负值为jn min(或jt min)。
jn应在被测齿轮齿面法线方向计值(μm),jt应在被测齿轮分度圆切线方向计值(μm),以其它方向测量时应对测得值进行换算,见附录C(补充件)。
附录A
测量仪器示值误差及示值变动性的确定
(补充件)
A1测量仪器示值误差的确定
仪器的示值误差用经法定部门检定过的标准元件(标准块或标准样板或标准齿轮)来确定。确定方法如下:
仪器经校准后,应在仪器的测量范围内用两个和两个以上不同规格的标准元件进行仪器示值误差的确定。
对每个标准元件,在被检定仪器上进行n次重复测量(n≥)将每次测得值(或曲线)与标准值(或曲线)进行比较,其差值为ΔX1,ΔX2,……ΔXn,仪器的示值误差φ为:

………………(A1)
以对不同规格标准元件所测得的最大φmax作为仪器的示值误差。
A2测量仪器示值变动性的确定
对被测齿轮进行n次重复测量(n=5~10),n次测得值的最大差值即为仪器的示值变动性。
附录B
测量时被测齿轮定位精度的确定
(补充件)
B1 应选择被测齿轮的设计基准作为测量基准。由测量时的定位误差造成的被测齿轮的径向跳动不大于齿圈径向跳动公差的八分之一。当选用端面定位时,除上述定位精度的要求外,定位端面的端面跳动不得大于在齿宽等于跳动圆直径时同精度齿向公差的五分之一。
附录C
不同传感方向测量时误差值的换算
(补充件)
C1在测量齿轮误差时测头的传感受方向有齿面法线方向、基圆切线方向、分度圆切线方向、轴线方向、双侧齿面分度圆螺旋线(在展开平面上)法线方向、回转角方向和双侧齿面径向。
C2齿轮各项误差应按下述规定的方向计值:Δfpb、ΔFb、ΔFpX、Δffβ、ΔFw、ΔEwm、jn在齿面法线方向计值;ΔFi′、Δfi′、ΔFp、ΔFpk、Δfpt、ΔFβ、ΔFic′、Δfic′、jt在分度圆切线方向计值;Δff在基圆切线方向计值;ΔFr、ΔFi″、Δfi″、ΔEα″和ΔEH在双侧齿面径向计值;ΔEs在双侧齿面分度圆螺旋线的法线方向计值。
C3对不在规定的计值方向测得的误差值应按下列各式换算:
式中:

——齿轮回转角误差,(″);

——齿轮分度圆切线方向的误差,μm;

——齿轮基圆切线方向的误差,μm;

——齿面法线方向的误差,μm;

——齿轮轴线方向的误差,μm;

——齿轮分度圆螺旋线法线方向的误差,μm;

——齿轮双侧面分度圆螺旋线法线方向的误差,μm;

——齿轮双侧齿面的径向误差,μm。
附加说明:
本标准由中华人民共和国机械电子工业部提出。
本标准由机械电子工业部郑州机械研究所归口。
本标准由机械电子工业部成都工具研究所和中国计量科学研究院共同负责起草。
本标准主要起草人黄潼年、唐启昌、张乃君、柏永新、苏桂兰、谢时骅、杨春发、于秋思、商向东、张伟、刘振福、蔡康洪。