确定管材韧性的小试件实验
4.1引言
提高钢材的使用性能已形成愈来愈强劲的全球化趋势。在本世纪,钢铁材料仍然是占主导地位的结构材料。各行各业的效益、效率和效能迫使结构材料最大限度地提高其使用性能水平。以石油天然气输送管道的应用为例,屈服强度由448MPa(X65)提高到690MPa(Xl00),经济效益提高了20%。
21世纪中期,我国钢材需求量可能超过2亿吨/年,即需要在目前基础上再增加1亿吨/年的生产能力,需再投入10000亿元。国家的财力、能源、资源、环境、运输等均无法承受。提高钢的使用性能,使一吨能够顶几吨使用,是我国钢铁工业的主要出路。
提高钢的使用性能必须提高其使用强度与断裂韧性的水平。为满足社会发展的要求,西方发达国家和我国都制订了面向21世纪的“超级钢”研究计划。
日本1997年提出STX21超级钢研究计划,为期10年,总费用高达1000亿日元。其目标为普通钢屈服强度达到80OMPa,高强度钢抗拉强度达到惊人的300OMPa;
我国973项目“新一代钢铁材料的重大基础研究”,为期5年,前两年投入1500万元人民币,目标为碳素结构钢屈服强度达到400MPa,低合金钢屈服强度达到800MPa,合金结构钢抗拉强度达到1500MPa。
国内外“超级钢”计划包括了石油用钢的管线钢、油井管钢和石油、石化装备用钢等。以管线钢为例:
日本STX21超级钢计划将高性能管线钢作为其中的重要内容。发达国家已批量生产供应的高钢级管线钢管为X80,酸性环境用管为X65,已研制成功开始试用的高强度和耐酸性环境腐蚀的管线管分别为Xl00和X70,目前正在研制高强度X12O和酸性环境用的X80管线钢管。
我国973中也包含了“高性能管线钢的重大基础研究”,其目标是将现有管线钢的使用寿命延长一倍,其中包括高强度X80和酸性环境用X65管线钢的重大基础研究。
钢材的强度与韧性性能决定于材料的成分/结构以及合成/加工。
在钢材的成分/结构,即材料设计方面,超低碳贝氏体钢和超低碳马氏体钢被誉为21世纪的管线钢,其钢级为X80~X100(贝氏体)、Xl00~Xl20(马氏体)。
在钢材的合成/加工,即冶炼和加工成型工艺方面,主要的工作是保障预期的组织状态,并使钢有超高纯净度、高的均匀性和晶粒的超细化。
现代冶金技术和加工成型工艺的进展主要包括:超纯净钢冶炼技术,保证钢材中的各元素比比例N≤20ppm,O≤10ppm,H≤1.0ppm;高均匀性的连铸技术,包括连续过程的电磁搅拌、连续板坯缓慢压缩(soft reduction)技术等;控制轧制、控制冷却、强制加速冷却,超细晶粒(可达1μm左右),沉淀硬化,以保障得到预期的组织结构;TiO处理等。
一般来说,对天然气管线有两种韧性要求。首先是要求全壁厚落锤撕裂实验,要求在最低设计温度下的最小剪切面积为85%,以保证不发生脆性断裂;其次是夏比冲击韧性的要求,以保证管线钢有足够的韧性,能够延性止裂。规定的夏比韧性值与下述相关:所有试件的平均值等于最小延性止裂的计算值。
本章采用我们同中国石油天然气集团公司西安石油管材研究所(CNPC)合作项目测定的高韧性管线钢CVN、DWTT冲击能量数据进行归纳比较,旨在确定现有X7O钢级钢材的物理性能及其中的规律,并为数值模拟动态断裂扩展中参数的确定提供依据。
4.2 V型缺口夏比冲击实验(Charpy V-Notch Impact Test)
CVN(Chary V-Notch)实验又称三点弯曲夏比冲击实验,是一种传统的评价材料断裂韧性的实验方法。它通过摆锤式冲击实验机对含V型缺口的小型试件的冲击破坏实验测量在此过程中的耗散功,即夏比冲击功,来评价材料的断裂韧度。
该实验简便易行,且有大量的数据积累,因此在防止结构脆性破坏或延性裂纹扩展的评价上得到广泛的应用。
实验装置和参数示意图如图4-1所示。
GB2106-80和ASMME23-96规定试样标准尺寸为10×10×55mm,缺口深度为2mm。对于2/3尺寸试样,厚度减为6.67mm,截面尺寸不变,如图4-2。
HLP组织提到冲击功大致与试样厚度的1.5次方成正比,由此得到全尺寸冲击功和2/3尺寸冲击功的近似关系:
C2/3=0.544CKV (4-1)
式中CKV和C2/3分别表示全尺寸试样和2/3试样的夏比冲击功。
在20世纪60年代,管线钢管开始使用控轧或热机械加工工艺钢生产。这种工艺导致壁厚中的带状组织,其内含有马氏体和贝氏体晶粒薄层。这一结果实际上产生了低合金钢复合结构。马氏体钢和贝氏体钢在对材料韧性方面有一定的好处,但这些薄的马氏体和贝氏体晶粒薄层比厚的铁素体/珠光体层还要脆,并导致产生平行于钢管表面的开裂,这种剥离被认为在轴向扩展的裂纹尖端产生。在裂尖附近的钢将明显的存在一系列的孤立的分层。这些分层多被归类为分离,并应与条带夹杂物,如MnS夹杂区分开来。壁厚的减薄将减低韧脆转化温度,所以只需添加少量的合金,材料便可具有更高的抵抗脆断的能力。断口分离现象可以从试样的断裂表面观察到,如图4-3所示。
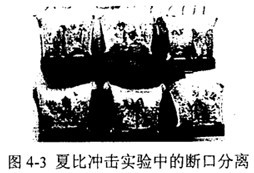
对于断口上有分离的材料,随温度的升高,分离将最终消失,这是因为马氏体和贝氏体带也达到了上平台温度。图4-4表示典型控轧钢的夏比能量随温度的变化。夏比冲击试样上100%剪切面积对应的最小夏比能称为CV100。当所有的分离都消失时,上平台能CVP出现,其大小可能高于CV100。
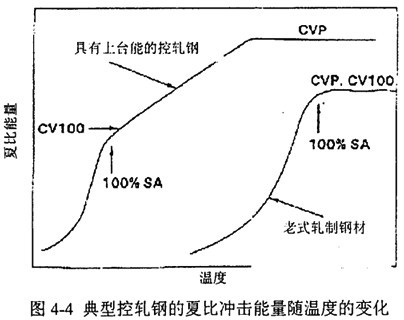
图4-5给出了某种控轧钢的CVN冲击能量随温度的变化。由于在脆性断裂行为中冲击韧性值远小于韧性断裂,因而当环境温度接近或低于材料的韧脆转化温度时,测得的CVN值会明显降低。图4-6中的系列试样经历了韧脆断裂过程的转变。一般定义SA为韧性撕裂所占断口面积比,85%SATT表示韧性占85%撕裂面积对应的转化温度。
断口分离的发生情况与温度有关。随着试样温度的升高,当钢材成分中的马氏体/贝氏体层达到其上台能时,断口分离会逐渐减少直至消失。分离对上平台韧性的影响是:钢中分层越薄,韧性断裂的抗力越低。因此,材料中分离多时,其韧性比大高温下无分离的相同材料的韧性低。
图4-7选择的管线钢在实验温度范围内同时经历了韧脆转化和断口分离,对上述结论给予了证实,并可以看到发断口分离的试件的韧性稍低于未发生断口分离的试件。
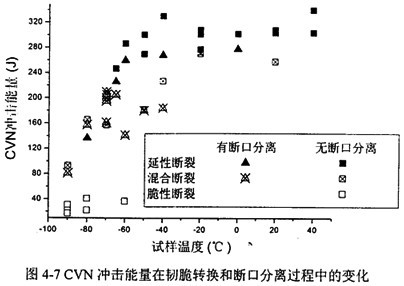
夏比冲击实验的缺点是摆锤的冲击速度远远低于实际裂纹的扩展速度,同时试件厚度偏薄,使得测到的CVN能量不能严格反映裂纹扩展过程中受到的材料韧性的影响。近年来人们开始注意选择不同的韧性测定实验以提高止裂评价的准确性。在这种背景下,DWTT实验得到了广泛的重视与应用。
4.3落锤撕裂实验(Drop Weight Tear Test)
落锤撕裂实验DWTT早期主要用于根据断口形貌确定铁素体钢的韧脆转变温度,近年来也用于评价材料的断裂韧性。同CVN实验相比,它的试样尺寸较大,锤刃更为厚重,因而要求试验机具备更高的冲击能量。
图4-8和图4-9分别表示DWTT的试样标准和断口形貌。
GB 8363-87和ASMM E436规定试样外形尺寸为300×75mm,缺口深度为5mm,厚度即为原板厚度。
实验证实,对有上台能的控轧钢进行的实验中,标准DWTT实验比夏比冲击实验在评价延性裂纹扩展行为上有更好的对应关系。但对于高韧性的淬火回火钢,标准DWTT试样由于在起裂过程中吸收了大量的功,致使裂纹扩展的应变速度过低而与真实扩展状况不符。采用静态预制裂纹DWTT试样或双试样DWTT法是解决这一问题的两种方案,如图4-10所示。
在预制裂纹DWTT实验中,起裂功由于预开裂纹的原因基本上被消除了;在双试样DWTT实验中,采用了V形槽和DWTT试样,这种试样对V形缺口根据实际应用的要求进行了修正,在后端加开了凹槽,两次实验的开槽深度不同,以其DWTT功的差作为最终评价的依据,有效地抵消了起裂功。这样实验得到的DWTT功只有裂纹扩展功,能够很好地估计延性裂纹的扩展。
DWTT实验过程中也会发生断口分离,如图4-11所示。DWTT分离形貌与全尺寸行为在相同温度下很相似,CVN则明显不同。
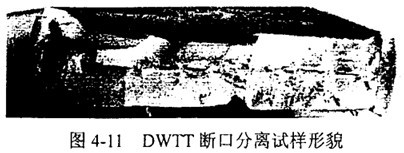
DWTT试样的断口分离平行于钢板表面,垂直于断一口平面。钢材从高温轧制冷却到接近于低温相变温度时,厚度方向上发生组织转变,形成贝氏体或马氏体板条束,引起平行于板材平面的方向发生开裂。板材越厚,裂纹尖端塑性区的应力越大,越容易发生断口分离。
随着裂纹扩展成为一系列小的薄片,断口分离使得轴向传播的裂纹尖端充分显露出来,从而减小了管子的有效壁厚,降低韧脆转化温度,使材料整体上更适于低温使用。当断口表面发生大量分离时,相应的延性断裂功会有所降低。为了准确地测定材料的断裂韧性,应尽可能避免断口分离现象的发生。与CVN实验类似,DWTT冲击韧性也随温度的升高而增加。图4-12给出了与图4-6相对应的具有上台能的控轧钢材标准DWTT吸收功与温度的变化关系。DWTT试样和夏比试样的厚度差异导致了两图85%SATT不同。
图4-13比较了在延性和脆性断裂中有无断口分离试样的DWTT韧性值。结论与CVN实验类似,发生断口分离的试样,测得韧性值略低。
4.4 CVN实验与DWTT实验的比较研究
CVN实验是被广泛采用的测定钢材断裂韧性的方式。近二十年来的研究工作表明,随着管线输送技术的发展,就高韧性钢而言,基于DWTT实验的结果比CVN实验更准确。对于这种现象成因的解释一般基于以下几种观点:
●锤击速度。CVN和DWTT实验的锤击速度均小于全尺寸实验裂纹的扩展速度,相比之下DWTT实验的锤击速度更高,更接近真实状态。随着输送压力的提高,断裂扩展速度大幅提升,CVN实验的摆锤撞击速度比真实断裂速度低引起的能量耗散上的非线性差异更加突出:
●尺寸效应。CVN实验标准试样厚度小于管道壁厚,使止裂韧性预测发生偏差;而DWTT实验测定止裂韧性一般采用全厚度试样,这与它用于评价韧脆转变温度时一致,裂纹的断裂路径比夏比试样更长,因此完全剪切撕裂破坏可以像全尺寸断裂行为那样得到充分的发展。对于高韧性材料,CVN实验中为采用试样标准厚度而对原管壁进行加工对实验结果的影响更为显著;
●缺口形状。DWTT试样的尺寸比CVN试样宽阔,利于调整缺口形状和性质使实验结果趋于精确。除采用预开裂试件或双V形槽试件的方法消除起裂功以外,缺口的角度和脆性都对实验结果有一定的影响;
●试验机容量。CVN和DWTT试验机的过剩能容量可以有很大的不同,通常DWTT设备的过剩能容量是相同的CVN设备的两个数量级以上。一般认为仪器容量相当于最高韧性样品能量的五倍即是具有足够的过剩能量。在此范围之内,过剩能量的多少是影响CVN和DWTT实验断口形貌和韧性数值的最主要因素。
在已进行的大多数全尺寸实验中,对钢材断裂性能的描述汉限于CVN冲击能量方面。如果能够保存实际止裂点处钢材的性能,便可制作试样取得止裂所需的DWTT能量数据。实际上无法做到这一点,这意味着只有找到DW竹韧性和CVN韧性之间的关系,已有的裂纹扩展全尺寸实验数据库才能用于DWTT吸收功做止裂预测。因而从实用的角度来看,应该建立同种材料的夏比吸收功和DWTT功之间的大致对应关系。
Wilkowski对老式控轧钢,包括有无上台能的情况做了检验,得到标准DWTT韧性和夏比韧性的对应关系:
ds=3cKV+0.63 (4-2)
日本HLP委员会在大量实验基础上针对淬火回火高韧性钢进行了调整:
Ds=5.9h1.5CKV0.544 (4-3)
上两式中Ds表示标准DWTT吸收功相应的,ds表示标准DWTT韧性值,即单位面积的DWTT吸收功。CKV和cKV分别表示全尺寸试样的夏比冲击功和冲击韧性值,即单位面积的夏比冲击功。h为壁厚,mm。
本文根据我们最近的实验数据修正了(4-3)式的系数:
Ds=3.5h1.5CKV0。6 (4-4)
图4-14将(4.2)~(4.4)式预测的对应关系同真实实验结果做了对比。可以看到对于相近的CVN韧性预测结果,实际的DWTT功从低到高在大范围内分布。
由于DWTT实验和Charpy冲击实验存在根本区别,实验结果受试验机过剩容量、断口分离情况、起裂功比例不同、尺寸效应、锤击速度差异等因素的直接影响,DWTT实验和夏比实验结果之间对应关系的分散性不可避免。总结二者之间近似的对应关系,目的是给通过DWTT韧性的止裂预测提供更多的实测参考。
4.5双试件DWTT法测定Gd和(CTOA)c
(CTOA)c可以通过摄像机从实物裂纹扩展的照片上观测得到,也可同CVN或DWTT实验建立联系。Wilkowski分别建立了基于CVN和DWTT吸收功的(CTOA)c经验算法,模型如图4-15。另一种方法是通过测定作用于试件上的总功,从裂纹扩展能的角度计算(CTOA)c。
Wilkowski从实验归纳了夏比冲击韧性和(CTOA)c之间的关系:
(CTOA)c=

(4-5)
式中k是待定系数,σfd是动态流变应力(MPa),σfd=1.3σf=0.65(σy+σu),σy为屈服应力,σu为拉伸强度,cKV是单位面积的夏比冲击韧性(J/mm2)。
比较常用的(CTOA)c。实验室测定是双试样DWTT法。美国西南研究院SwRI发展了这一模型,测得的(CTOA)c可如下表示:
式中

为槽深为a的V形槽DWTT韧性(J/mm
2);a
l、a
2为V形槽深度(mm);a
fd是动态屈服应力(MPa)。
大量的实验表明,在高韧性钢的冲击实验中,裂纹成长大约一个壁厚以后CTOA即达到稳定状态,稳态扩展持续到初始韧带宽度的40%为止。夏比实验的韧带宽度尚不足一个壁厚,断裂行为难以得到持续稳定的发展。
双试样DWTT法测(CTOA)c因其简便易行和结果可信被广泛采用。据此对西气东输采用的某管道工况做了止裂性能的静态评价,列于表4-1和表4-2中。
表4-1列出了一种X7O管材的力学性能的测试结果,并根据式(4-8)估算了(CTOA)max,其中参数取p=l0MPa,D=1ll8mm,E=14.7mm,E=2.1×105MPa。
表4-1 西气东输1550×14.7mmX70板材强度
|
头部 |
中部 |
尾部 |
实测 |
平均 |
实测 |
平均 |
实测 |
平均 |
屈服强度
(MPa) |
615 |
606 |
610 |
594 |
610 |
588 |
593 |
582 |
582 |
623 |
590 |
584 |
592 |
594 |
575 |
抗拉强度
(MPa) |
705 |
705 |
740 |
735 |
695 |
690 |
705 |
725 |
682 |
707 |
739 |
691 |
704 |
734 |
691 |
流变应力
(MPa) |
656 |
665 |
639 |
动态流变应力(MPa) |
852 |
864 |
831 |
(CTOA)max(°) |
9.98 |
9.87 |
10.2 |
临界状态下,最大的延性裂纹扩展驱动力等于材料的延性裂纹扩展阻力,即(CTOA)max=(CTOA)c。文献中给出了估算管道裂纹扩展中(CTOA)max的公式:
上式中σh是初始管道压力下的环向应力:σh=pD/2h,σf是材料的流变应力,E是钢材的杨氏模量,P是输送压力,D是管道直径,h是管道壁厚。C、m、n和q是特定的常数:C=106,m=0.753,n=0.778,q=0.65。
表4-2给出了通过同种管材的双试样DWTT实验,经式(4-6)和(3-32)得到的(CTOA)c和Gd的值,并作了止裂预测。
表4-2 西气东输1550×14.7mmX70板材双试样DWTT实验结果
缺口深度 |
温度℃ |
头部 |
中部 |
尾部 |
吸收功(J) |
平均(J) |
吸收功(J) |
平均(J) |
吸收功(J) |
平均(J) |
10mm |
20 |
5120 |
5080 |
4310 |
4453 |
5520 |
5403 |
5070 |
4400 |
5360 |
5050 |
4650 |
5330 |
-10 |
4730 |
4347 |
3820 |
3713 |
4900 |
4730 |
3820 |
3300 |
4290 |
4490 |
4020 |
5000 |
36mm |
20 |
2300 |
2223 |
1760 |
1860 |
2230 |
2250 |
2240 |
1890 |
2100 |
2130 |
1930 |
2420 |
-10 |
1880 |
1773 |
1180 |
1297 |
1540 |
1683 |
1620 |
1310 |
1830 |
1820 |
1400 |
1680 |
(CTOA)c(°) |
20 |
9.57(扩展) |
9.29(扩展) |
11.8(止裂) |
-10 |
9.69(扩展) |
10.6(止裂) |
13.7(止裂) |
Gd
(KN/m) |
20 |
7.48 |
7.26 |
9.22 |
-10 |
7.57 |
8.29 |
10.7 |
4.6对X70钢管的韧性评测
本节对西气东输用到的某种国产X70钢进行CVN和DWTT韧性评价。实验中的板卷由B钢厂生产,钢管分别由BB、BQ、BL三家管厂生产。
4.6.1CVN实验结果
图4-16是夏比能与实验温度曲线。图4-17是剪切面积百分比与实验温度曲线。三家管厂钢管的转变曲线和上平台能很似。
图4-18a,b,c给出了三家钢管的夏比能与剪切面积的关系,以及85%剪切面积对应的转变温度。图中CV100表示100%剪切面积时最低的夏比能,CVI表示最低夏比平台能,也称夏比转变能,CVP表示夏比平台能。菱形实验点表示剪切面积高于90%,方形实验点表示低于90%可以看到,剪切面积低于90%时,夏比能与剪切面积呈线性关系。
表4-3给出了归纳的夏比冲击能量值及85%剪切面积对应的转变温度。
表4-3夏比能及85%剪切面积对应的转变温度
管厂名 |
CVI(J) |
CVP100(J) |
CVP (J) |
CVP/CVI |
CVP/CV100 |
85%SATT(℃) |
BB |
180 |
224 |
287 |
1.59 |
1.28 |
-52 |
BL |
265 |
218 |
267 |
1.01 |
1.22 |
-40 |
BQ |
200 |
200 |
254 |
1.27 |
1.27 |
-36 |
4.6.2 DWTT实验结果
图4-19显示了标准压制缺口DWTT试样能量与实验温度数据。
图4-20是剪切面积百分比与实验温度的数据。
图4-21a,b,c是能量与剪切面积百分比图。和前面-样,菱形实验点表示剪切面积高于90%,方形表示低于90%。与对CVN数据的处理类似,分别定义DWTT-100表示100%剪切面积时最低的DWTT能,DWTT-I表示DWTT转变能,DWTT-P表示DWTT平台能。由图4-21可确定DWTT和DWTT-100的值。
表4-4给出了这些DWTT实验的特征值和85%剪切面积对应的转变温度。
表4-4DWTT能及85%剪切面积对应的转变温度
管厂名 |
DWTT-I(J) |
DWTT-100(J) |
DWTT-P(J) |
DWTT-P/
DWTT-I |
DWTT-P/
DWTT-100 |
85%SATT(℃) |
BB |
5800 |
6220 |
7704 |
1.33 |
1.24 |
-6 |
BL |
5100 |
6985 |
8963 |
1.76 |
1.28 |
-4 |
BQ |
6100 |
6771 |
7509 |
1.23 |
1.11 |
-1 |
4.6.3CVN与DWTT数据比较
图4-22是CVN与DWTT试样的上台能量特征值数据图。总的来说,CVN与DWTT试样的特征能量比率有较好的一致性。图中P/100的符合性比P/I更好,很大程度上是因为CV100、DWTT-100比CVN-I、DWTT-I的获得方法更为明确。
从CVN数据得到的85%剪切面积转变平均温度是-42.7℃,而从DWTT数据得到的85%剪切面积转变平均温度是3.7℃。两种试样的转变温度差是39℃。这个转变温度的变化比Eiber从普通热轧钢中得出的结论更大。通过Eiber的关系式得出14.7mm厚的CVN与DWTT试样的转变温度差是10℃。正是这种不同使得在高韧性管线钢中使用CVN能量产生很多不便。
CVN和DWTT试样数据表明,这些钢均具有很高的上平台能。虽然很难准确地确定上升平台行为的程度,但这些钢材断口分离不明显,CVP/CV100和DWTT-PDWTT-100均小于1.2,这表明这些钢的上升平台很小。
4.7本章小结
本章考查了CVN和DWTT两种动态韧性测试手段以及二者之间的关系。特别是对具有上台能的高韧性钢,文中详细地分析了断口分离与能量平台的形成原因,并结合具体材料进行了实测。
根据前两章的需要,本章自行设计了双试件DWTT实验并测定了韧性减速机理和完善止裂判据所需的伪和(CTOA)c值。
通过对国产X70管线钢的冲击实验,发现这些钢上升平台能很小。相比韧性止裂所需的最小韧性值,均有很高的上平台韧性。
DWTT实验因韧性值与断口形貌更接近于全尺寸断裂而被广泛采用。然而CVN冲击韧性仍然占领着难以动摇的垄断地位。发展二者之间的联系,同时寻找(CTOA)c等新的表示管材韧性的物理量是对高性能钢进行韧性评估的关键。