渐开线直齿和斜齿圆柱齿轮承载能力
计算方法 工业齿轮应用
1范围
本标准规定了工业用齿轮和斜齿轮接触强度与弯曲强度 校核计算方法。
本标准中的计算公式并不适用于其他形式的轮齿损伤,如塑性变形、微点蚀、胶合、表层压溃、焊合以及磨损,也不能应用于预料不至齿廓破坏的振动条件下。弯曲强度公式可应用于轮齿齿根圆角处折断,而不能用在轮齿工作齿廓表面上的折断、齿轮齿圈的失效或齿坯辐板与轮毂的失效。本标准不适用于以锻压或烧结为最终加工方法的轮齿,也不能应用于接触斑点很差的齿轮。
本标准提供一种不同齿轮设计的对比方法,其目的不在于确保装配后传动齿轮系统的性能,也不是针对一般工程界使用,而是为有经验的齿轮设计人员所使用,他基于类似设计的知识与对所讨论的这些章节影响的了解,能为这些公式中的系数选择合理的数值。
注:使用者对本标准的计算结果应当用经验进一步确认。
2规范性引用文件
下列文件中的条款通过本标准中引用而成为本标准的条款,凡是注日期引用文件,其附后所有的修改单(不包括勘误的内容)或修订版均不适用于本标准,然而,鼓励根据本标准达成协议的各方研究是否可使用这些文件的最新版本。凡是不注日期的引用文件,其最新版本适用于本标准。
GB/T 1356-2001通用机械和重型机械用圆柱齿轮 标准基本齿条齿廓(idt ISO 53:1998)
GB/T 1357 通用机械和重型机械用圆柱齿轮 模数(ISO 54:1996,IDT)
GB/T3374-1992 齿轮基本术语(neq ISL/R1122-1:1983)
GB/T8539-2000 齿轮材料及热处理质量检验的一般规定的(eqv ISO6336-5:1996)
GB/T 10095.1-2001 渐开线圆柱齿轮 精度 第1部分:轮齿同侧齿面偏差的定义和允许值(idt ISO 1328-1997)
JB/T8830-2001高速渐开线圆柱齿轮和类似要求齿轮承载能力计算方法(idt ISO 9084:1998)
ISO4287:1997产品几何量技术规范(GPS) 表面结构:轮廓方法 表面结构的术语、定义和参数
ISO 6336-1:1996直齿轮和斜齿轮承载能力计算 第1部分:基本原理、概述和通用影响系数
ISO 6336-2:1996直角轮和斜齿轮承载能力计算 第2部分:齿面接触疲劳(点蚀)强度计算
ISO 6336-3:1996直齿轮和斜齿轮承载能力计算 第3部分:齿根弯曲强度计算
3术语和定义
本标准采用GB/T3374中给出的术语和定义。有关代号见表1。
表1代号与缩略语
a |
中心距 |
mm |
b |
齿宽 |
mm |
bβ |
双斜齿齿轮单螺旋线部分的齿宽 |
mm |
bH |
齿宽(点蚀) |
mm |
bF |
齿宽(齿根) |
mm |
bred |
减少后的齿宽(减去齿端修缘的齿宽) |
mm |
bs |
辐板厚度 |
mm |
bⅠ(Ⅱ) |
齿端修形的宽度 |
mm |
cr |
单位齿宽啮合刚度的平均值 |
N/(mm·μm) |
c′ |
单对齿单位齿宽的最大轮齿刚度(单齿刚度) |
N/(mm·μm) |
da1,2 |
小轮、大轮顶圆直径 |
mm |
dan1,2 |
当量直齿轮的小轮、大轮的基圆直径 |
mm |
db1,2 |
小量直齿轮的小轮、大轮单对齿啮合外界点所在圆直径 |
mm |
dbn1,2 |
小轮、大轮根圆直径 |
mm |
dcn1,2 |
小轮、大轮齿高中部直径 |
mm |
df1,2 |
当量直齿轮的小轮、大轮分度圆直径 |
mm |
dm1,2 |
弯曲强度计算的名义轴径 |
mm |
dn1,2 |
空心轴的内径 |
mm |
dsh |
小轮、大轮节圆直径 |
mm |
dshi |
齿根圆附近一个圆的直径,包含内齿轮或相啮齿轮的较大外齿轮的可用齿廓极限尺寸 |
mm |
dw1,2 |
小轮、大轮分度圆直径 |
mm |
dNf2 |
齿根圆附近一个圆的直径,包含内齿轮或相啮齿轮的较大外齿轮有可用齿廓极限尺寸 |
mm |
d1,2 |
小轮、大传输线分度圆直径 |
mm |
feff |
有效齿廓的形状偏差 |
μm |
ffα |
齿廓形状偏差(若公差符合GB/T10095.1-2001规定,也可用齿廓总偏差值Fa替代) |
μm |
fma |
因制造不精确引起的螺旋线偏差 |
μm |
fpb |
端面基节偏差(根据ISO6336:1996采用GB/T10095.1-2001规定的公差,计算时可使用fpt值) |
μm |
fbeff |
有效端面基节偏差 |
μm |
fsh |
由弹性变形引起的螺旋线偏差 |
μm |
fHβ |
螺旋线倾斜偏差(不包服务态度螺旋线形状偏差) |
μm |
gα |
啮合线长度 |
mm |
h |
齿高 |
mm |
ha |
齿顶高 |
mm |
hao |
刀具齿顶高 |
mm |
hf2 |
内齿轮轮齿的齿根高 |
mm |
hfp |
圆柱齿轮基本齿条齿顶高 |
mm |
hFe |
载荷作用于单对齿啮合区外界点时的弯曲力臂 |
mm |
hNf2 |
内齿轮齿根高,包含内齿轮或相啮的较大外齿轮的可用齿面极限尺寸 |
mm |
l |
轴承跨距 |
mm |
mn |
法向模数 |
mm |
mred |
齿轮副折合到啮合线上单位齿宽的质量 |
kg/mm |
nE |
临界转速 |
min-1 |
n1,2 |
小轮、大轮转速 |
r/min |
pbn |
法面基节 |
mm |
pbt |
端面基节 |
mm |
pr |
刀具突出部分 |
mm |
q |
精加工毛坯余量 |
mm |
qs |
齿根圆角参数SFh/2ρF |
- |
qsT |
标准的基准试验齿轮齿根圆角参数 |
- |
rb |
基圆半径 |
mm |
s |
小轮相对轴中心线的偏置量 |
mm |
sFn |
危险截面处的齿根法向弦齿厚 |
mm |
sR |
轮缘厚度 |
mm |
spr |
残留的齿根圆角处挖根量 |
mm |
u |
齿数比|u|=|z2/z1|≥1a) |
- |
v |
圆周速度(不带下标:分度圆上的圆周速度≈工作节圆上圆周速度) |
m/s |
x1,2 |
小轮(或大轮)的变位系数 |
- |
yf |
跑合量(齿距偏差) |
μm |
yp |
距合量(齿廓偏差) |
μm |
yα |
齿轮副的跑合量 |
μm |
yβ |
跑合量(当量的啮合齿向偏差) |
μm |
zn |
斜齿轮的当量齿数 |
- |
z1,2 |
小轮、大轮齿数a) |
- |
B |
双斜齿轮的总齿宽(包括退刀槽) |
mm |
Bf |
确定常数K的跑合参数 |
- |
Bk |
确定常数K的跑合参数 |
- |
Bp |
确定常数K的跑合参数 |
- |
B1,2 |
确定FβX的常数 |
- |
B* |
确定小轮偏置的常数 |
- |
Ca |
齿顶修缘量 |
μm |
Cay |
因跑合面导致的齿顶修缘量 |
μm |
Cv1,2,3 |
确定常数K的常数 |
- |
CB |
基本齿条系数 |
- |
CR |
齿坯系数 |
- |
Cβ |
鼓形系数 |
mm |
C1,…,9 |
确定qs的常数 |
- |
E |
弹性模量,杨氏模数 |
N/mm2 |
E |
计算Y的辅助值 |
- |
Fm |
分度圆柱上的平均端面力(=FtKAKV) |
N |
Ft |
分度圆柱上的(名义)端面切向力 |
N |
Ftmax |
分度圆柱上的最大端面切向力 |
N |
FtH |
分度圆柱上的决定性的端面力(= FtKAKVKHβ) |
N |
Fβ |
螺旋线总偏差 |
μm |
FβX |
初始当量啮合齿向误差(跑合前) |
μm |
G |
确定YF的辅助值 |
- |
H |
确定YF的辅助值 |
- |
J*1,2 |
小轮、大轮单位齿宽的转动惯量 |
kg/mm |
K |
确定KV的常数 |
- |
KV |
动载系数 |
- |
KA |
使用系数 |
- |
KFα |
弯曲强度计算的齿间载荷分配系数 |
- |
KFβ |
弯曲强度计算的齿向载荷分布系数 |
- |
KHα |
接触强度计算的齿间载荷分配系数 |
- |
KHβ |
接触强度计算的齿向载荷分布系数 |
- |
Kγ |
啮合载荷系数(考虑对于多分支传动,各啮合副间载荷的不均匀分布) |
- |
K1,2 |
常数 |
- |
K′ |
相对转矩输入端的小轮偏置常数 |
- |
L |
危险载面上的齿根弦齿厚与载荷作用于单对齿啮合区外界点处的弯曲力臂的比值 |
- |
N |
临界转速比 |
- |
NF |
指数(或幂) |
- |
NL |
载荷循环次数 |
- |
NS |
主共振区的临界转速比 |
- |
M1,2 |
确定ZB,D的辅助值 |
- |
P |
传递功率 |
kW |
Pmax |
最大传递功率 |
kW |
Ra |
算术平均粗糙度(按照ISO4287:1997)的规定 |
μm |
Rz |
平均峰谷粗糙度(按照ISO4287:1997)的规定 |
μm |
Rz10 |
齿轮平均峰谷粗糙度 |
μm |
SF |
弯曲强度的计算 |
- |
SFmin |
弯曲强度的最小安全系数 |
- |
SH |
接触强度的计算安全系数 |
- |
SHmin |
接触强度的最小安全系数 |
- |
T1,2 |
小轮转矩(名议的)、大轮转矩 |
Nm |
Tmax |
最大转矩 |
Nm |
YF |
齿形系数 |
- |
YN |
弯曲强度计算的寿命系数 |
- |
YNT |
在标准试验条件下弯曲强度计算的寿命系数 |
- |
YRrelT |
相对齿根表面状况系数 |
- |
YS |
应力修正系数 |
- |
YX |
弯曲强度计算的尺寸系数 |
- |
Yβ |
弯曲强度计算的螺旋角系数 |
- |
YδrelT |
相对齿根圆角敏感系数 |
- |
Yε |
弯曲强度计算的重合度系数 |
- |
Zv |
速度系数 |
- |
ZB,D |
小轮、大轮单对齿啮合系数 |
- |
ZE |
弹性系数 |
|
ZH |
节点区域系数 |
- |
ZL |
润滑剂系数 |
- |
ZN |
接触强度计算的寿命系数 |
- |
ZNT |
标准试验条件下接触强度的寿命系数 |
- |
ZR |
影响接触强度的粗糙度系数 |
- |
ZW |
齿面工作硬化系数 |
- |
ZX |
接触强度计算的尺寸系数 |
- |
Zβ |
接触强度计算的螺旋角系数 |
- |
Zε |
接触强度计算的重合度系数 |
- |
αen |
当量直齿轮单对齿啮合区外界点处的压力角 |
(°) |
αn |
法面压力角 |
(°) |
αt |
端面压力角 |
(°) |
αwt |
节圆柱上的端面压力角 |
(°) |
αFen |
当量直齿轮单对齿啮合区外界点处的载荷作用角 |
(°) |
αpn |
圆柱齿轮基本齿条法向压力角 |
(°) |
β |
分度圆柱上的螺旋角 |
(°) |
βb |
基圆螺旋角 |
(°) |
γe |
确定σFen的辅助角 |
(°) |
δbth |
齿宽载荷均匀分布条件下相啮轮齿的综合变形 |
μm |
εα |
端面重合度 |
- |
εαn |
当量齿轮的端面重合度 |
- |
εβ |
纵向重合度 |
- |
εγ |
总重合度(εγ=εα+εβ) |
- |
ν |
泊松比 |
- |
θ |
确定YF的辅助值 |
- |
ρa0 |
刀具的顶圆半径 |
mm |
ρfp |
圆柱齿轮基本齿条的齿根圆角半径 |
mm |
ρrel |
相对曲率半径 |
mm |
ρF |
危险截面处齿根圆角半径 |
mm |
ρ′ |
滑动层厚度 |
mm |
σB |
抗拉强度 |
N/mm2 |
σF |
齿根应力 |
N/mm2 |
σFlim |
试验齿轮的弯曲疲劳极限 |
N/mm2 |
σFE |
材料的弯曲疲劳极限=σFlim·YST(YST=2) |
N/mm2 |
αFG |
齿根应力极限 |
N/mm2 |
αFP |
许用齿根应力 |
N/mm2 |
αFO |
计算齿根应力基本值 |
N/mm2 |
αH |
计算接触应力 |
N/mm2 |
αHlim |
试验齿轮接触疲劳极限 |
N/mm2 |
αHG |
修正的许用接触应力极限=σHPSHmin |
N/mm2 |
αHP |
许用接触应力 |
N/mm2 |
αH0 |
计算接触应力基本值 |
N/mm2 |
αS |
屈服点 |
N/mm2 |
α0.2 |
0.2%弹性极限应力 |
N/mm2 |
X* |
齿根圆角内相对应力梯度 |
mm-1 |
X P * |
平滑抛光试验件的相对应力梯度 |
mm-1 |
XT* |
标准抛光试验件的相对应力梯度 |
mm-1 |
ω1,2 |
小轮、大轮的角速度 |
rad/s |
a对于外齿轮副,a、u、z1与z2为正值,对于内齿轮副,a、u、和z2的负值,z1为正值。 |
4应用
4.1设计、具体应用
4.1.1概述
齿轮设计人员必须认识到各种应用场合的要求是不相同的。对具体应用场合,使用本标准的方法时,特别需要仔细考虑所有适用条件,尤其是:
——材料的许用应力与载荷循环次数;
——失效百分率的影响(失效率);
——适当的安全系数。
为避免齿面上因应力提升装置的发生折断的设计条件,端顶修缘以及齿坯辐板或轮毂的失效,应该用普通机械设计方法分析。
对以下内容有任何改变,应在计算书中说明:
a)如果希望有一个精确的计算方法,或由于任何原因在4.1中的限制条件不适用,则相关的系数可按照基础标准或其他应用标准评价。
b)由可靠经验而得到的系数与试验数据可用以替代根据本标准得到的各个系数。关于这一点,适用于ISO6336-1:1996的4.1.8.1中A法的准则。
另一方面,承载能力计算在任何情况下应严格按照本标准执行,应力、安全系数等的分等应与本标准一致。
本标准适用以下形式的工业传动装置。
——产品目录所列闭式传动装置:设计时按名义载荷计算,按产品目录 所列或为存销售。设计时实际载荷与运行条件并不完全知道。
注:对每种应用情误解的实际载荷要进行计算,以选择产品目录中相应尺寸的装置。经常用根据类似应用经验确定的选择系数来降低产品目录所列的功率档次,以适应应用条件。
——用户的设计和传动装置:针对一种特定的场合。在些情况下,设计时其运行条件已知或被规定。
当齿坯、轴和毂配合联结、轴承、箱休、螺纹联结、地基及联轴器等都满足精度、承载能力和刚度的要求时,才可应用本标准。
虽然本标准在叙述的方法主要目的在于校核,借助于迭代法,它也可用以确定齿轮的载荷能力。对于小轮来说,选择一种载荷半计算其抗点蚀的相应安全系数SH1来表达迭代的目的。如果SH1大于SHmin,可增加载荷;如果小于SHmin,则降低载荷。这样做到所选载荷相当于SH1=SHmin为止。对于大轮采用同样方法(SH2=SHmin),抗轮齿折断的安全系数也一样,SF1=SF2=SFmin。
4.1.2齿轮参数
本标准适用于下列范围。
a)齿轮类型
——外齿和内齿渐开线直齿、斜齿及双斜齿齿轮;
——对于双斜齿齿轮,假定总的切向载荷在两条螺旋线间均匀分布;若不是这种情况(例如由于外部施加的轴向力所引起的),必须考虑将两条螺纹线处理为两个并联的单斜齿齿轮。
b)速度范围
——n1低于或等于3600r/min(供电频率60HZ,两极电机的同步速度)1)(1)对于更高的速度,应使用ISO 6336:1996或JB/T8830-2001);
——工作转速低于临界转速范围(见5.6中KV);
——在速度v<m/s时,齿轮承载能力通常受磨损的限制。
a)齿轮精度
——根据GB/T10095.1-2001,精度等级为10级或10级以上(影响KV、KHα与KHβ)
b)当量直齿轮副端面重合度范围
——1.2<εαn<1.9(影响c′、cγ、KV、KHβ、KFβ、KHα和FFβ)
c)螺旋角范围:
——β小于或等于30°(影响cγ、KV和KHβ)
4.1.3小齿轮与小齿轮轴
本标准适用于与轴形成一体的小齿轮(轴齿轮)或SR/d1≥0.2的带孔小齿轮(影响c′、cγ、KV与KHβ)。假定带孔的小齿轮安装在实心轴上或dshi/dsh<0.5的空心轴上(影响KHβ)。
4.1.4齿坯、轮缘
所给公式适用于齿根以下最小轮缘厚度为SR>3.5mn的直齿轮和斜齿轮。KHβ的计算是假定齿轮和轴有足够的刚度,它们的变形可以略去。
4.1.5材料
包括钢、球墨铸铁及灰铸铁(ZE、σHlim、σFE、Kr、KHβ、KFβ、KHα、KFα)。在本标准中使用的材料与它们的缩略语见表2。
材料 |
缩略语 |
钢(σB≥800N/mm2)
铸钢(合金的或碳的)(σB≥800N/mm2)
调质钢(合金的或碳的),调质处理(σB≥800N/mm2)
灰铸铁
球墨铸铁(珠光体,贝氏体,铁素体组织)
黑色可锻铸铁(珠光体组织)
表面硬化钢,表面硬化外理
钢与球墨铸铁,火焰或感应淬火处理
氮化钢,氮化处理
调质与表面硬化钢,氮化处理
调质与表面硬化钢,氮碳共渗处理 |
St
St(cast)
V
GG
GGG(perl,bai,ferr.)
GTS(perl.)
Eh
IF
NT(nitr.)
NV(nitr.)
NV(nitrocar.) |
4.1.6润滑
本计算方法适用于在齿轮啮合时具有足够的适当黏度的润滑剂的油润滑齿轮,且有适当的工作温度(影响润滑油膜的形成,也即系数ZL、ZV及ZR)。
4.2安全系数
必须对点蚀的安全系数SH和轮齿折断的安全系数SF加以区别。
对于给定的应用场合,足够的齿轮承载能力是分别用SH和SF的计算值等于或大于SHmin和SFmin的值表示的。
安全系数值的选择应基于对所用数据的可靠度及失效造成的后果。
考虑的重要因素如下:
a) GB/T8539-2000中材料疲劳极限是失效概率为1%时得到的;
b) 在整个制造过程中所规定的质量与质量控制的有效性;
c) 工作载荷与外部载荷描述的精确度;
d) 通常认为断齿比点蚀造成的危害更大。
因此,SFmin的先用值应比SHmin的选用值更大。
实际安全系数的计算,见6.15(SH,点铡)与7.1.4(SF,轮齿折断)。最小安全系数见6.12(点蚀)与7.9(轮齿折断)。然而,建议安全系数最小值应由供需双方协商一致。
4.3输入数据
为了计算应给出下数据:
a) 齿轮数据
a,

,

,m
n,d
1,d
a1,d
a2,b,b
H,b
F,x
1,x
2,α
n,β,ε
α,ε
β(见GB/T 1356、GB/T1357),(b,b
H与b
F的定义,见4.4);
b) 刀具基本齿条齿廓
ha0,ρa0;
c) 设计与制造数据
Ca1,Ca2,fpb,SHmin,SFmin,Ra1,Ra2,R ,R ;
材料、材料硬度与热处理的详细资料;齿轮精度等级,轴承跨距l,齿轮相对于轴承的位置,小轮轴的尺寸dsh及需要时的螺旋线修形(鼓形,齿端修缘);
d) 功率数据
P或T或Ft,n1,v1,原动机和工作机的详细情况。必要的几何数据可根据相关资料计算。
供需双方之间交换的资料应包含给定材料的优选、润滑、安全系数以及由于振动与过载引起的外部作用力(使用系数)。
4.4齿宽
下面这些齿宽必须区别开来。
——b:在节圆上测量的小轮与大轮齿宽中的较小者(对双斜齿轮,bH=2bB)。齿端部倒棱与倒圆应该略去。在齿宽方向接触不良时,应使用接触齿宽的长度。
——bH:在齿轮节圆柱上的宽度(对双斜齿轮,bH=2bB)。当齿宽bH大于与它相啮齿轮的齿宽时,bH应使用较小的齿宽,忽略任何有意的齿端倒棱和齿端齿圆。不包括表面硬化齿轮的百硬化区和过渡区。在齿宽方向接触不良时,应使用接触齿宽的长度。
——bF:齿轮齿根圆柱上的齿宽(对双斜齿轮,bH=2bB)。当齿宽bF大于与它相啮齿宽时,bF应使用较小齿宽加一个长度,该长度不超过每端任一延伸部分的一个模数。然而如果预见到由于修鼓形或齿端修缘面啮合不扩展到齿宽端部,则应使用小轮与大轮两者之间的较小齿宽。在齿宽方向接触不良时,应使用接触齿宽的长度。
4.5数字公式
所有的计算均用第3章表列的各单位,促进本标准使用的资料在ISO6336-1:1996的附录C 中提供。
5影响系数
5.1概述
影响系数KV、KHα、KHβ、KFβ、KFα均取决于轮齿载荷等。用作用载荷(名义切向载荷乘以使用系数)作为最初的计算值。
这些系数相互影响,所以应按以下顺序计算:
a) 用切向载荷FtKA计算KV;
a) 用载荷FtKAKV计算KHβ或KFβ;
c)用切向载荷FtKA计算KHα或KFα
当一个了轮带动两个或更多的相相啮齿轮时,必须用KAKY替代KA。如果可能,啮合载荷系数应该用检测方法确定,或者,它的数值也可由文献资料确定。
5.2名义切向力Ft、名义转矩T、名义功率P
名义切向力在分度圆柱的端平面内确定。它由工作机的输入转矩确定,此转矩为正常工作条件下的最大值。另一方面,当原动机的名义转矩与工作机的转矩一致时,可采用原动机的名义转矩,或者选取其他合适的值。

…………………………(1)

………………………………(2)

……………………(3)
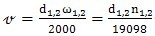
……………………(4)

……………………(5)
5.3非均匀力、非均匀转矩、非均匀功率
当被传递载荷不均匀时,不仅要考虑峰值载荷及其预期的循环次数,而且考虑中等载荷及其循环次数。这种类型的载荷归入载荷循环类并可用载荷谱来表示。在此情况下,载荷循环的累积疲劳的影响在评定齿轮装置时要考虑。在ISO/TR10495中已给出计算此情误解下载荷影响的方法。
5.4最大切向力Ftmax、最大转矩Tmax、最大功率Pmax
变载荷下,最大切向载荷Ftmax(或相应的转矩Tmax,相应的功率Pmax)的大小可用一个适当敏感度的安全离合器来限制。在计算由于加载到相当于静应力极限而可能出现的点蚀损坏与突然断齿的可靠性时,必须知道Ftmax、Tmax与Pmax(见5.3)。
5.5使用系数KA
5.5.1概述
为了补偿由于外部因素而引起的齿轮载荷的增加,用KA来调节名义载荷Ft。这种附加的力很大程度上取决于原动机和从动机的特性,也依赖于轴和联轴器在内的系统的质量和刚性。
建议供(或设计者)需双方对使用系数值协商一致。
5.5.2A法——系数KA-A
KA可通过精密测量和对系统的综合分析或根据应用现场的可靠使用经验确定(见5.3)。
5.5.3 B法——系数KA-B
如果无法用5.5.2所述方法获得KA的可靠数据,或在初步设计阶段时,可使用附录C给出的KA推荐值。
5.6动载系数KV
动载系数展示了把包含“多谐振”系统的内部动载影响的轮齿总载荷与传递的轮齿切向载荷之间的关系。
在本标准中使用了修正的ISO6336-1:1996的B法。当供需双方协商一致时或在确定产品目录所列闭式传动装置承载能力时,可用ISO6336-1:1996的E法来估算其动载系数。
在此法中,假定齿轮副由一个基本单质量弹簧系统组成(包括大、小齿轮的诱导质量和轮齿的啮合刚度)。同时带假定每对齿轮副像单级齿轮副一样,即不考虑多级齿轮系统中其他各级的相互影响。这个假定仅适用于大轮和小轮轴的扭转刚度(在齿轮基圆半径处测量)小于啮合刚度。刚性轴的处理方法见5.6.3与附录A。
由轴的扭转与联轴器质量引起的力不包括在KV中,这些力应包含在其他外部作用力中(例如在使用系数中考虑)。
在多点啮合齿轮系中有多个固有频率,这些频率可能高于或低于只有一点啮合的单级齿轮副的固有频率。当这样的齿轮在超临界区运转时,建议用A法进行分析,见ISO6336-1:1996的6.3.1。
计算KV的单位载荷是(FtKA)/b。
若(FtKA)/b>100N/mm,则Fm/b=(FtKA)/b;
若(FtKA)/b≤100 N/mm,则Fm/b=100N/mm.
当单位载荷(FtKA)/b<50N/mm时,尤其对于在较高速度运;志的低精度等级直齿传输线或斜面齿轮存在着很大的振动危险(在某些情况下会造成工作齿面的脱啮)。
5.6.2计算KV所要求的参数计算
5.6.2.1诱导质量的计算
a)单级齿轮副诱导质量mred的计算:
m
red=

……………………(6)
式中:mred——齿轮副的诱导质量,即每个齿传输线单位齿宽质量的诱导质量,与其基圆半径或啮合线有关;

——小轮及大轮单位齿宽的转动惯量;
rb1,2——小轮及大轮基圆半径(=0.5db1,2)。
b) 多级齿轮副诱导质量的计算
见附录A。
c) 非常规设计齿轮的当量质量的计算
下列几种情况见A.1.2:
——齿高中部直径dm1大约等于轴径的轴齿轮;
——两个刚性联结的同轴齿轮;
——行星齿轮;
——中间齿轮。
5.6.2.2齿轮副共振运转速度(主共振)的确定
a)小轮的共振运转速度nE1/(r/min):
n
E1=

……………………(7)

按附录B确定。
b)共振转速比N
共振转速比N是小轮速度与共振速度之比,其计算如下:
N=
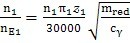
……………………(8)
由于未考虑刚度(例如轴、轴承或箱体的刚度)和阻尼,因此,共振运转速度可能高于或低于由式(7)计算的运转速度。由于安全的原因,共振区用下述方法确定。
Ns<N<1.15……………………(9)
载荷(FtKA)/b<100N/mm时,共振转速比下限Ns可确定如下:
——若(FtKA)/b<100N/mm,则
N
s=0.5+0.35

……………………(10)
——若(FtKA)/b≥100N/mm,则
N=0.85……………………(11)
5.6.2.3齿轮精度与跑合参数BP、Bf、Bk
BP、Bf与Bk是用于考虑轮齿偏差与齿廓修形对动载荷影响的无量纲参数2)(2)齿顶修缘量Ca仅适用于GB/T10095.1-2001规定的0~6级精度齿轮)。
B
p=

……………………(12)
B
f=

……………………(13)
B
k=|1-

|……………………(14)
式中:

——按附录B确定;

——设计齿廓修形量(在轮齿啮入与啮出处的齿顶修缘)。在没有说明齿离修形量时,由跑合得到的C
ay值代替式(14)中的C
a,C
ay值可由表3查得。
有效基李偏差与有效齿廓形状偏差是跑合后的值,

与

值根据相应的跑合量y
p与y
f来确定:

或

……………………(15)
取其中的较大者。

或

……………………(16)
取其中的较大者。
5.6.2.4跑合量ya
a)对于St,St(cast),V,GGG(perl.,bai.),GTS(perl.)3)
y
p=y
a=

……………………(17)
y
f=

……………………(18)
b)对于GG,GGG(ferr)3)
y
p=y
a=

……………………(19)
y
f=

……………………(20)
c)对于Eh,IF,NT(nitr.),NV(nitr.),NV(nitrocar.)3)(3)所用缩略语的说明见表2。)
y
p=y
a=

……………………(21)
y
f=

……………………(22)
5.6.3亚临界区的动载系数(N≤Ns)
在这个区域,如果轮齿啮合频率符合N=1/2与N=1/3,就可能存在共振。对于精密斜齿轮或经适当修形后的直齿轮(如GB/T10095.1-2001)规定的6级精度或更高的齿轮)共振的危险性很小。
当直齿轮的重合度很小或精度较低时,KV达到主共振速度范围内的KV值。若出现这种情况,应修改设计或运行参数。
在N=1/4、1/5时的共振由于相应的振幅一般很小,很少会引起麻烦。
对于主动轴和从动轴刚度不同的齿轮副,在N≈0.2~0.5范围内,如果刚性轴转化到啮合线上的扭转刚度C与轮齿刚度的数量级相同,即如果c/rb2和cr的数量相同时,轮齿啮合频率可能激励固有频率。此时,则动载荷增量可能超过用式(23)
计算的值。
KV=(NK)+1………………(23)
K=(CV1BP)+(CV2BF)+( CV3Bk)………………(24)
式中,Cv1与Cv2分别是考虑齿距偏差与齿廓偏差的影响,Cv3是考虑啮合刚度的周期性变化的影响,见表3。
表3系数数Cv1~Cv3与Cv1与Cay的计算式
|
1<  ≤2 |
 >2 |
Cv1 |
0.32 |
0.32 |
Cv2 |
0.34 |
|
Cv3 |
0.23 |
|
C ay= 
注:当小轮(1)的材料和大轮(2)的材料不同时,Cay1与Cay2要分别计算,且Cay=0.5(Cay1+Cay2) |
由跑合而产生的Cay值在齿轮不规定齿廓修形的情况下,代替公式中的Ca。Ca可由表3查取。单对齿刚度c′见附录B。
5.7接触强度计算的齿向载荷分布系数KHβ
5.7.1概述
齿向载荷分布系数是考虑沿齿宽上载荷分布不均匀的影响。用以修正轮齿应力。
本标准采用了修正的ISO6336-1:1996的C2法,目的是为了考虑 由于小轮弹性变形与制造误差而引起的啮合齿向误差的影响。
KHβ应根据跑合后总的啮合齿向误差计算,它包含以下两部分:
——系统误差 是由fsh来考虑的(因轴的变形引起的啮合齿向误差),而且主要是由小齿轮轴变形引起的,但基本上可包括在数量和方向上能足够精确计算的所有机械变形。
——随机误差 是由fma表示的(因制造公差引起的啮合齿向误差)。由制造引起的实际啮合齿向误差的方向和数量是不能计算的,只是用制造公差限制其范围(这与齿轮精度等级有关)。
螺旋线修形与鼓形修形的应用包括以下内容:
——螺旋线修形是导程修形,它用于调正系统误差。理论上应用螺旋线修形是可行的,对特定的载荷可与计算的变形精确一致。所以可消除fsh对KHβ的影响,但在计算fsh时变载荷与误差对KHβ留下残余的影响,这必须要考虑。
——鼓形是导程修形,它是针对啮合齿向误差的随机成分的最好的防御策略。因fma可以在任一方向上,鼓形修形应对称于齿宽中部。
当设计与ISO6336-1:1996的7.2.31要求不一致或当以下任何一项对啮合齿向误差有重要影响时,建议使用ISO6336-1:1996的更精确方法与综合分析法。
——弹性变形不是由齿轮啮合力而是由外部载荷引起的(例如带、链、联轴器);
——齿轮与齿轮轴的弹性变形;
——齿轮箱的弹性变形与制造误差;
——轴承游隙与变形;
——布置与图2中表示的型式不同;
——指明需作更详细分析的任何制造变形或其他变形。
当采用本法计算的KHβ值大于2.0时,通常真实的数值将小于此值。然而,若KHβ的计算值大于1.5时,应重新考虑设计(例如增加轴的刚度,改变轴承的位置,改善螺旋线的精度)。
5.7.2KHβ的计算
计算KHβ的单位载荷是(FtKAKV)/b。
若(FtKAKV)/b>100N/mm,则Fm/b=(FtKAKV)/b;
若(FtKAKV)/b≤100N/mm,则Fm/b=100N/mm;
K
Hβ=1+

……………………(25)
适用于KHβ≤2,且cy 由附录B取得。
本标准不适用于KHβ>2的情况。
5.7.3跑合后的啮合齿向误差Fβy
Fβy=Fβx-yβ……………………(26)
式中:
,,
Fβx——跑合前的啮合齿向误差(见5.7.4);
yβ——跑合最(见5.7.8)。
5.7.4跑合前的啮合齿向误差Fβx
5.7.4.1概述
Fβx是在啮合平面内测量的制造偏差与小轮和轴的变形量总和的绝对值。
5.7.4.2用户设计的齿轮传动装置(见第4章)
a)对于没有检验接触斑点位置的齿轮副4)(4)弹性变形与制造偏差可以相互补偿时,具有良好的接触斑点(见图1的补偿作用)。)
Fβx=1.33B1fsh+B2fma………………(27)
其中B1与B2可由表4获得。
表4式(27)中使用的常数
序号 |
螺旋线修形 |
公式常数 |
类型 |
数量 |
B1 |
B2 |
1 |
无 |
- |
1 |
1 |
2 |
仅作中央鼓形修形 |
Cβ=0.5fmaa |
1 |
0.5 |
3 |
仅作中央鼓形修形 |
Cβ=0.5(fma+fsh)a |
0.5 |
0.5 |
4b |
仅作螺旋线修形 |
计算的修正形状符合分析的转矩 |
0.1c |
1.0 |
5 |
螺旋线修正加中央鼓形修形 |
方案2+方案4 |
0.1c |
0.5 |
6 |
齿端倒坡 |
CⅠ(Ⅱ)合适的最,见附录D |
0.7 |
0.7 |
a 适当的鼓形修形量Cβ,见附录D。
b 主要应用在不变载荷条件的场合。
c适用于有充分制造经验的齿轮,否则用较高的值。 |
b)对于检验有良好接触斑点的齿轮副(例如采用调整轴承方法)
Fβx=|1.33 B1fsh –fHβ5|………………(28)
式中:
fHβ5——5级精度齿轮的最大螺旋线倾斜偏差(见GB/T10095.1-2001).
对于fHβ5作减法计算是考虑到弹性变形与制造偏差的补偿作用而留的余量。
图1按照接触斑点位置确定Fβx的规则
5.7.4.3产品目录中的闭式传动装置(见第4章)
对于具用螺旋线修形与鼓形修形或没有螺旋线修形的产品目录中所列装置的齿轮副使用公式(27)。这种情况下,齿轮副的位置,轴的变形、轴承、悬臂载荷均应考虑5)(5)例如,当选用系数为1.0时,产品目录中所列齿轮箱功率为400KW,把螺旋线修形与鼓形修形用于表4中的齿轮,没有检验接触斑点,在产品目录中所列速度下,实际传递的功率将小于400kw。对于400kw的情况可用式(27)计算,当实际传递功率低于400KW时,虽然Fβx与KHβ较高,总的轮齿应力也将较低。若将以上装置中齿轮也用在其他的齿轮箱中可采用名义鼓形量,选择这个鼓形量适应所有可能的位置,但不是每个功率级和位置的最佳鼓形量。对于这些情况可应用式(29)。)
另一方向,对具有适当螺旋线修形与鼓形修形的产品目录中所列的齿轮副:
F
βx=
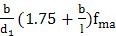
………………(29)
当使用式(29)时,跑合最yβ=0。
5.7.5KHβ的最小值
对于没有螺旋线修形与鼓形修形的齿轮副,在最低速度级时KHβ的最小值为1.25(对单级减速齿轮传动装置也一样),对于所有其他的速度级为1.45。
对于具用适当螺旋线修形与鼓形修形的齿轮副,在最低速度级时KHβ的最小值为1.10(对单级减速齿轮传动装置也一样),对于所有其他的速度级为1.25。对于由用户设计的传动装置,KHβ的最小值为1.0。
以上规定的KHβ最小值适用于各种载荷情况,包括过载的情况。
5.7.6当量啮合齿向误差fsh
对直齿轮与单斜齿轮:

……………………(30)
对于双斜齿轮,fsh的计算与最靠近的被驱动或驱动载荷的轴端的螺旋有关:

……………………(31)
式中:
b =2bB
bB——单边螺旋线宽度。
式(30)与式(31)中的K′、s与l见图2。
在图2中的点划线给出的小轮表示双斜齿轮fsh值较小的单边螺旋线的中点位置,且为正常套装(对于正常套装,其支撑影响可忽略不计)。其根径应较轴径稍大些。
5.7.7因制造误差产生的啮合齿向误差fma
由制造误差产生的啮合齿向误差fma等于螺旋线公差fHβ:
fma=fHβ……………………(32)
取大轮和小轮中的较大值。理论上,可能会出现小轮、大轮制造公差和轴的不对中相互叠加这种最坏的情况。例如,应该用接触斑点控制来修正载荷的分布。
图2计算fsh时,公式(30)与公式(31)中的常数K′
5.7.8跑合最yβ
a)对于St,St(cast),V,GGG(perl.,bai.)及GTS(perl.)6):
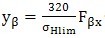
……………………(33)
式中:

当

:没有限制;
当5m/s〈

:上限为

=25600/

,相当于F
βX=80μm;
当

>10m/s:上限为

=12800/

,相当于F
βX=40μm。
b)对于GG与GGG(ferr.)6)(6)所用缩略语的说明见表2。)

=0.55F
βX……………………(34)
当

:没有限制;
当5m/s <

:上限为

=45μm,相当于F
βX=80μm;
当

>10m/s:上限为

=22μm,相当于F
βX=40μm。
c)对于Eh,IF,NT(nitr.),与NV(nitrocat.)6)(所用缩略语的说明见表2。)

=0.15F
βX……………………(35)
对所有的速度,上限为

=6μm,相当于F
βX=40μm;
当大、小轮材料不同时,小轮的

与大轮的

应分别确定。
取两者的平均值,用于计算:
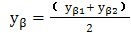
……………………(36)
5.8弯曲强度计算的了向载荷分布系数


……………………(37)
若b/h≥3,则
N
F=

………………(38)
或b/h<3,则
NF=0.6923……………………(39)
式中:
b——齿宽(见4.4节)
h——从齿顶到齿根的轮齿高度:h=(da-df)/2。
5.9齿间载荷分配系数

、
5.9.1概述
齿间载荷分配系数是考虑几对同时啮合的轮齿之间的载荷分配不均匀的影响。其值按下述方法确定7):(7)式(40和式(41)基于这样假定,即符合规定的齿轮精度的基节偏差,且是沿小轮和大轮的圆周正常分布。当轮齿具有某种故意的偏差时,它们是不适用于的。)
a) 总重合度ε
γ≤2的齿轮的

与

值

……………………(40)
b) 总重合度ε
γ>2的齿轮的

与

值

……………………(41)
式中:

——啮合刚度,按附录B确定;

——取大、小轮基节偏差中的较大值;当齿廓修形补偿实际载荷极下的轮齿变形时,可以用其公差50%
8);(基节偏差 考虑了影响齿间载荷系数的所有轮齿偏差的总影响。然而,如果齿廓形状偏差 大于基节偏差时,用齿廓形状偏差代替基节偏差。)

——跑合留量,见5.9.4;

——在端平面内确定的切向载荷,F
tH=F
tK
AK
VK
Hβ。
5.9.2

的限制条件
按照公式(40)或式(41),
…………………(42)
5.9.3

的限制条件
按照公式(40)或式(41),
…………………(43)
式中:
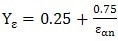
……………………(44)

由公式(95)确定。
根据式(42)和式(43)的限制值,假定载荷最不利的分布为整个切向载荷仅用一对啮合轮齿传递。
此外,建议在选择斜齿轮的精度时,应使

与

不大于

,因此,必须限制低精度等级齿轮的基节偏差。
5.9.4跑合量


值是在运转初期由于跑合使初始基节偏差减小的量;

不考虑作为生产过程一部分的控制手段(例如研磨)面跑全到任意程度的余量。在考虑齿轮质量时,应考虑这种调整。
跑合量

可用式(45)~式(48)计算。
a) 对于St,St(cast),V,GGG(perl.,bai.)与GTS(perl.)9):(缩略语的说明见表2。)
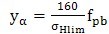
………………(45)
当

:没有限制;
当5m/s 〈

:上限为

=12800/

,相当于

=80μm;
当

>10m/s:上限为

=6400/

,相当于

=40μm。
b)对于GG与GGG(ferr.)9)(9)缩略语的说明见表2。)

=0.275

……………………(46)
当

:没有限制;
当5m/s 〈

:上限为

=22μm,相当于

=80μm;
当

>10m/s:上限为

=11μm,相当于

=40μm。
c)对于Eh,IF,NT(nitr.),与NV(nitrocat.)9)(缩略语的说明见表2。)

=0.075

……………………(47)
对所有的速度没有限制的情况下,上限为

=3μm,相当于

=40μm;
当材料不同时,

应由小轮材料确定,

由大轮材料确定。计算时使用平均值。
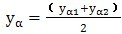
……………………(48)
6齿面接触强度(点蚀)计算
6.1基本公式
6.1.1概述
接触强度计算基于节点或单对齿啮合区内界点(下界点)处的接触应力

,用两者中的较大值计算承载能力。

值与许用接触应力

对于大小齿轮应分别计算;

应小于或等于

。
6.1.2小轮接触应力

的确定
小轮接触应力

计算如下:

……………………(49)

……………………(50)
式中:

——节点处计算接触应力的基本值,即无缺陷(无误差)齿轮传动在静态名义转矩作用下引起的应力;
bH——齿宽(见4.4);
ZB——小轮的单对齿啮合系数(见6.2);
对于内齿轮取负号。
6.1.3大轮接触应力

计算如下:

……………………(51)
式中:
ZD——大轮的单对齿啮合系数(见6.2)。
大多分运河传动的齿轮系、行星齿轮系或分流式齿轮系的情况下。总切向载荷在各单个啮合处上并不完全均匀分布(取决于设计、切线速度与制造精度)。因此,在式(49)和式(51)中用KrKA替代KA,以调整每个啮合处的平均切向载荷(见第5章)是必要的。
6.1.4许用接触应力

的确定
6.1.4.1方法
本标准采用ISO6336-2:1996中的B法。

……………………(52)
6.1.4.2许用接触应力(参考)

许用接触应力(参考)

是由式(52)在Z
N=1及适当的

值下得出的。
6.1.4.3许用接触应力(静态)

是根据式(52)按照6.8关于静态应力的Z
N=Z
NT及

的相应值下确定。
6.1.4.4许用接触应力(10
10循环次数)

是根据式(52)按照6.8关于载荷循环次数为10
10时的Z
N=Z
NT及

的相应值下确定。
6.1.4.5有限寿命或长寿命许用接触应力
有限寿命的范围是载荷循环次数NL处于表6所列相应参考许用应力值和载荷循环次数为1010之间(见表3)。
——在有限寿命范围内,对于一个给定的载荷循环次数N
L的

在按6.1.4.2得到的参考强度值与根据6.1.4.3得到的静态强度之间用图解或计算插值法(按log-log双对数坐标)确定。
——在长寿命范围内,对于一个给定的载荷循环次数N
L的

在按6.1.4.2得到的参考强度值与根据6.1.4.4取得的载荷循环次数为10
10的值之间用图解或计算插值法(按log-log双对数坐标)确定。
对于载荷循环次数多于10
10的许用接触应力值

尚未建立。
6.1.5接触强度的安全系数SH
大小轮的安全系数SH应分别计算。
S
H=

……………………(53)
式中:

——是根据式(52)和6.14确定的参考应力与静态应力;

对于小轮按照式(49)确定,对于大轮按式(51)确定(见6.1)。
注:这是接触应力(赫兹应力)的计算安全系数。相应的转矩安全系数为SH。
接触强度的最小安全系数SHmin见6.12。
图3 关于有限寿命与长寿命许用接触应力的图形确定
6.2小轮、大轮单对齿啮合系数ZB、ZD
当ZB>1或ZD>1时,系数ZB与ZD用以将直齿轮节点上接触应力分别转换为小轮和大轮单对齿啮合区下界点处的接触应力,见6.1.1。
a) 内齿轮
ZD取为1.0。
b) 直齿轮
M
1(用小轮单对齿内界点(下界点)处

除以节点处

的商)与M
2(用大轮的

除以

商)可由下述式子确定。
M
1=
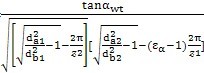
……………………(54)
M
2=
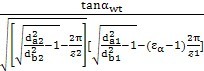
……………………(55)
齿廓重合度εα的计算,见6.5.2。
若M1>1,取ZB=M1;若M1≤1,取ZB=1.0;
若M2>1,取ZD=M2;若M2≤1,取ZD=1.0。
c) εβ≥1的斜 轮
ZB=ZD=1
d) εβ<1的斜齿传输线
ZB与ZD由直齿与εβ≥1的斜齿轮传动之间线性插值确定:
ZB=M1-εβ(M1-1); ZB≥1
………………(56)
ZD=M2-εβ(M2-1); ZB≥1
当ZB或ZD为1,用式(49)或式(51)计算的接触应力是节圆柱上的接触应力值。当节点处于啮合线上时,用6.2的方法计算接触应力。若节点C是限定的,并处在啮合线之外时则ZB和ZD按邻近的顶圆接触确定。对于斜齿轮,当εβ<1.0时,ZB与ZD在直齿轮与εB≥1的斜齿轮的值(在节点或邻近的顶圆上确定)之间用线性插值法确定。
6.3节点区域系数ZH
节点区域系ZH是考虑节点处齿廓曲率对赫兹力的影响并将分度圆上的切向转换为节圆上的法向力。
Z
H=

……………………(57)
6.4弹性系数ZE
弹性系数ZE是考虑材料特性E(弹性模量)与v(泊松比)对接触应力影响的系数。
ZE的数值见表5。
齿轮1 |
齿轮2 |
ZE/
|
材料 |
弹性模量
|
泊桑比
V |
材料 |
弹性模量
|
泊桑比
V |
St,V,Eh,
NT(nitr.),
NV(nitr.),
NV(nitrocat.) |
206000 |
0.3 |
St,V,Eh,NT(nitr.),
NV(nitr.),
NV(nitrocat.) |
206000 |
0.3 |
189.8 |
St(nitr), |
202000 |
188.9 |
GGG(perl.,bai.,ferr.) |
173000 |
181.4 |
GTS(perl.) |
170000 |
180.5 |
GG |
126000~118000 |
165.4~162.0 |
St(cast) |
202000 |
St(nitr), |
202000 |
188.0 |
GGG(perl.,bai.,ferr.) |
173000 |
180.5 |
GTS(perl.) |
170000 |
179.7 |
GG |
118000 |
161.4 |
GGG(perl.,bai.,ferr.) |
173000 |
GGG(perl.,bai.,ferr.) |
173000 |
173.9 |
GTS(perl.) |
170000 |
173.2 |
GG |
118000 |
156.6 |
GTS(perl.) |
170000 |
GTS(perl.) |
170000 |
172.4 |
GG |
118000 |
156.1 |
GG |
126000~118000 |
GG |
118000 |
146.0~143.7 |
6.5接触强度计算的重合度系数Zε
6.5.1概述
重合度系数Zε是考虑端面重合度与纵向重合度对圆柱齿轮齿面承载能力影响的系数。
a) 直齿轮
Z
ε=

……………………(58)
对于重合度小于2.0的直齿轮,可选用保守值Zε=1.0。
b) 斜齿轮
当εβ<1时
Z
ε=
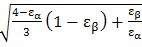
……………………(59)
当εB≥1时
Z
ε=

……………………(60)
6.5.2端面重合度

……………………(61)
啮合线长度

……………………(62)
上式中对外齿轮取正号,内齿轮取负号。
端面基节
Pbt=mtπcosαt……………………(63)
式(62)仅在啮合线长度被小轮与大轮的顶圆有效限定时才有效,而且被挖根齿廓限定时是不适用的。
6.5.3纵向重合度


……………………(64)
6.6接触强度 计算的螺旋角系数Zβ
螺旋线系数Zβ是考虑螺旋角对齿面应力的影响。

………………(65)
6.7试验齿轮的接触疲劳极限

GB/T8539-2000给出了常用齿轮材料、热处理以及齿轮质量对接触疲劳极限

的影响的有关资料,

由标准试验齿轮的试验结果获得。
质量等级ML、MQ、ME与MX对热处理的要求见GB/T8539-2000。
除非另有协议,工业齿轮选用材料质量等级MQ。
6.8接触强度计算的寿命系数ZNT
本标准使用ISO6336-3:1996的B法。表6中列入了ZNT的数值。
材料a |
载荷循环数 |
寿命系数ZNT |
St,St(cast),V,
GGG(perl.,bai.),
GTS(perl.),
Eh,IF
仅当一定程度的点蚀可允许时 |
NL≤6×105(静态) |
1.6 |
NL=107 |
1.3 |
NL=109(参考) |
1.0 |
NL=1010 |
ME,MX:1.0b |
MQ:0.92 |
ML:0.85 |
St,St(cast),V,
GGG(perl.,bai.),
GTS(perl.),
Eh,IF
不允许有点蚀 |
NL≤105(静态) |
1.6 |
NL=5×107 |
1.0 |
NL=1010 |
ME,MX:1.0b |
MQ:0.92 |
ML:0.85 |
GG,GGG(ferr.),
NT(nitr.),
NV(nitr.)
|
NL≤105(静态) |
1.3 |
NL=2×106 |
1.0 |
NL=1010 |
ME,MX:1.0b |
MQ:0.92 |
ML:0.85 |
NV(nitrocat.) |
NL≤105(静态) |
1.1 |
NL=2×106 |
1.0 |
NL=1010 |
ME,MX:1.0b |
MQ:0.92 |
ML:0.85 |
a所有缩略语的说明见表2。
b建议最佳润滑,制造与试验。 |
6.9润滑油膜形的影响系数ZL、ZV与ZR
6.9.1S概述
正如ISO6336-2:1996中所述,ZL是考虑润滑剂名义黏度的影响,ZV是考虑齿面速度的影响,ZR是考虑表面粗糙对啮合区润滑油膜形成的影响。本标准采用的是ISO6336-2:1996的C法。
润滑剂黏度的得选择要适合于运转条件(节线速度、载荷、尺寸),因此,ZL、ZV的乘积应近似为1.0。
ZR取决于与加工方法有关的齿面粗糙度。假定系数ZR基本上为常数
6.9.2基准强度与长寿命时的ZL、ZV、ZR乘积
——对于用滚削、插削或刨削或不符合以下三种情况的齿轮
ZL、ZV、ZR=0.85……………………(66)
——对于研磨、磨削或剃齿轮以及平均相对峰-谷粗糙度 的齿轮:

……………………(67)
ZL、ZV、ZR=0.92……………………(68)
——对于一个齿轮是滚削、插削或刨削加工相啮齿轮为磨削或剃削,且

μm
ZL、ZV、ZR=0.92……………………(69)
——对于

μm的磨削或剃削齿轮传动
ZL、ZV、ZR=1.0……………………(70)
6.9.3静强度时的ZL、ZV、ZR乘积
在所有情况下,静强度时:ZL、ZV、ZR=1.0。
6.10齿面工作硬化系数ZW
如ISO6336-2:1996所述,齿面工作硬化系数ZL是考虑由钢制大齿轮(结构钢,调质刚)与比大轮更硬(≈200HB或更多)并具有光滑齿面(Rz< μm,本标准不包括磨损的影响)的小齿传输线相啮合,而使大齿传输线齿面接触强度提高的系数。本标准采用ISO6336-2:1996的B法:
当HB<130时
ZW=1.2………………(71)
当130≤HB≤470时
Z
W=1.2-

………………(72)
当HB 时
ZW=1.0………………(73)
式中:
HB——齿轮副中较软齿轮齿面的布氏硬度。
6.11接触强度计算的尺寸系数ZX
ZX是考虑由统计表明因尺寸的增大使被劳损伤的应力小平降低的尺寸效应因素(在结构中有大最的薄弱点)。尺寸效应的后果是次表面的缺陷使应力梯度降低(理论应力分析)、尺寸影响材料质量(锻造、结构变化等的影响)。重要影响因素有:
a) 材料质量(炉料、纯净度、锻压);
b) 热处理、硬化深度、硬度分布;
c) 齿廓曲线半径;
d) 模数:在齿面硬化的情况下,相对于轮齿厚度的硬化层深度(芯部支承影响)。
对于调擀齿轮在相对于轮齿尺寸、相对曲率半径有足够渗层深度的表面硬化齿轮,尺寸系数ZX取为1.0。
6.12接触强度计算的最小安全系数SHmin
关于安全系数的一般叙述见第4单;接触强度 计算的安全系数SH见6.1.5。除非供需双方另有协议,应采用以下最小安全系数SHmin:
SHmin=1.0………………(74)
7齿根弯曲强度计算
7.1基本公式
7.1.1概述
如ISO6336-3:1996所述,齿根的拉抻应力不应超过材料的许用齿根应力。这是计算轮齿弯曲强度的基础。
实际齿根应力σF与许用齿根应力σFp、大小轮应分别计算,σF应小于σFp。
7.1.2齿根应力σF的确定
本标准采用ISO6336-3:1996的B法。
齿根应力σF计算
σF=σF0KAKVKFβKFα≤σFP………………(75)
σ
F0=

………………(76)
式中:
σF——齿根应力的基本值,即一对无误差齿轮在静态名义转矩作用下,齿根处产生的最大局部拉应力;
bF——齿宽(见4.4)。
对于多传动分支的齿轮系(行星齿轮系或分流式齿轮系的情况下,总切向载荷不能很均匀地分布在每个啮合副上(取决于设计、切向速度与制造精度)。需用KrKA替代式(75)中的KA,以调整单个啮合副上的平均切向载荷,见第5章。
7.1.3许用齿根应力σFP的确定
7.1.3.1概述
用式(77)确定许用齿根应力。
σ
FP= 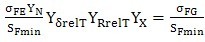
…………………………(77)
7.1.3.2许用齿根应力(基准)
用式(77)计算许用齿根应力(基准)

,此时取Y
N=1,并选取适当的

、Y
X与

值。
7.1.3.3许用齿根应力(静强度)

,此时,根据7.5的循环次数10
10,并选取适当的

、Y
X与

值。
7.1.3.4许用齿根应力(载荷循环次数10
10)
用式(77)计算许用齿根应力(载荷循环次数10
10) ,此时,根据7.5的循环次10
10,取Y
N=Y
NT,并选取适当的

、Y
X与

值。
7.1.3.5许用齿根应力(有限寿命或长寿命)
有限寿命的范围是载循环次数NL处在相当于静态齿根许用应力时的载荷循环次数与3×106载荷循环数之间。
——对于有限寿命范围内一个给定的载荷循环次数N
L,确定

是用图解或在根据7.1.3.2由基准强度得到的值与根据7.1.3.4由载荷循环次数10
10得到的值之间插值计算;
——对于长寿命范围内一个给定的载荷循环次数N
L,确定

是用图解或在根据7.1.3.2由基准强度得到的值与根据7.1.3.4由载荷循环次数10
10得到的值之间插值计算;
对于大于循环次数10
10的许用齿根应力

的值尚未建立。
7.1.4弯曲强度计算的安全系数SF
S
F=

……………………(78)
大小轮的S
F应分别计算,

按式(77)与7.1.3确定,

根据式(75)确定。
有关安全系数与失效概率的详细资料见ISO 6336-1:1996的4.1.3。弯曲强度的最小安全系数见7.9
7.2齿形系数YF与应力修画龙点睛系数YS
这两个系数用于考虑齿形对名义弯曲应力的影响,大小轮的YF与YS分别确定。详细资料可见ISO6336-3。
对于斜齿轮,按当量直齿轮确定YF。当量直齿轮的参数见7.2.2.4。
以下给出的公式适用于具有或没有挖根的所有基本齿条齿廊。但需满足下列条件:
a)30°切线的切点应位于齿根圆角处;
b)齿轮的基本齿条齿廓具有齿根圆角;
c)轮齿是用齿条刀具(如滚刀或梳齿刀)展成加工的。
7.2.2YF的确定
7.2.2.1概述
齿形系数YF由齿根危险截面的法向弦齿厚SFn与载荷作用在外齿轮齿顶的弯曲力臂hFe确定。
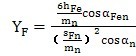
……………………(79)
7.2.2.2外齿轮传动
当齿顶有倒圆或倒棱时,需用“有效顶圆直径”dNa来代替计算中的顶圆直径da;dNa是靠近顶圆柱面包容可用齿廓极限的圆的直径。
首先确定辅助值E、G与H:
E=

……………………(80)
式中:

(见图4)。
当齿传输线不挖根时(见图4),
G=

……………………(81)
H=
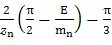
……………………(82)
用G与H以

作为式(83)中右边的初始值计算

。
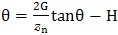
………………(83)
用计算得出的

再代入式(83)计算

,并连续用式(83)计算直到

的值没有明显的改变为止。经过二或三次迭代后函数收敛。在式(84)~式(86)中,使用

的最终值。
齿根法向弦齿厚SFn:

……………………(84)
齿根圆角处的圆弧半径
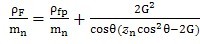
……………………(85)
弯曲力臂hFe:

………………(86)
当量齿轮的参数见7.2.2.4。
图4刀具的基本齿条齿廓
7.2.2.3内齿轮传动
假定用一个特殊齿条的齿形系数值近似地替代内齿轮的齿形系数。该齿条的齿廓是基本条齿廓的一种改型,它能展成内齿轮的精确配对齿轮的法向齿廓(包括齿顶圆与齿根圆),齿顶载荷角为αn。
式(79)中所用参数的值确定如下:
齿根法向弦齿厚SFn2

………………(87)
式中:

——刀具圆角半径。
弯曲力臂hFe2

…………(88)
式中:

——由式(100)确定,参数加下标2;

——与d
an的确定方法相同(见式99);注意d
fn2-d
f2=d
n2-d
2
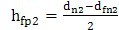
……………………(89)
齿根圆角半径

当内齿轮齿根圆角半径

为已知时,取

;当

为未知时,可按下列所似方法确定。

………………(90)
下式也是有效的:

………………(91)
式中:

——接近齿根圆的一个圆的直径,包含啮合副的内齿轮或较大外齿轮可用齿廓极限。
对内齿轮直径用负号。
7.2.2.4当量齿轮的参数

………………(92)
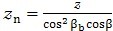
………………(93)
近似值

………………(94)

………………(95)
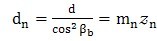
………………(96)

………………(97)
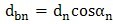
………………(98)

………………(99)

………………(100)
对外齿轮

取正值,对内齿轮

取负值(见表1的脚注)。
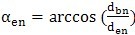
………………(101)

………………(102)

………………(103)
7.2.3YS的确定
应力修正系数YS用式(104)计算,该公式在1≤qs≤8范围内是有效的。
Y
S=(1.2+0.13L)
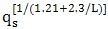
……………………(104)
L=

………………(105)
式中:

——对外齿轮用式(84),对内齿轮用式(87);

——对外齿轮用式(86),对内齿轮用式(88)。
q
s=

……………………(106)
式中:

——对外齿轮用式(85),对内齿轮用式(91)。
7.3弯曲强度计算的螺旋角系数Yβ
将当量直齿轮的齿根应力(计算的原始值)通过螺旋角系数Yβ转换为相应斜齿轮的齿根应力,用此方法考虑斜齿轮倾斜线的影响(齿根应力偏小)。
当

时
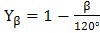
………………(107)
当

时

……………………(108)
当

时
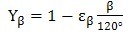
………………(109)
当

时
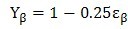
………………(110)
7.4材料的弯曲疲劳极限σFE
GB/T 8539-2000提供了常用齿轮材料的σFlim与σFE的资料,也包含ML、MQ与ME质量等级对热处理与材料质量的要求。
除非另有协议,工业齿轮采用MQ质量等级。本标准选用ISO6336-3:1996的B法。
7.5弯曲强度计算有寿命系数YNT
本标准采用ISO 6336-3:1996的B 法。YNT值由表7给出。
表7寿命系数YNT
材料a |
载荷循环数 |
寿命系数YNT |
V
GGG(perl.,bai.)
GTS(perl.) |
NL≤104(静态) |
2.5 |
NL=3×106 |
1.0 |
NL=1010 |
ME,MX:1.0b |
MQ:0.92 |
ML:0.85 |
Eh,IF(root) |
NL≤103(静态) |
2.5 |
NL=3×106 |
1.0 |
NL=1010 |
ME,MX:1.0b |
MQ:0.92 |
ML:0.85 |
St,St(cast),
NT(nitr.),
NV(nitr),
GG,GGG(ferr.) |
NL≤103(静态) |
1.6 |
NL=3×106 |
1.0 |
NL=1010 |
ME,MX:1.0b |
MQ:0.92 |
ML:0.85 |
NV(nitrocar.) |
NL≤103(静态) |
1.1 |
NL=3×106 |
1.0 |
NL=1010 |
ME,MX:1.0b |
MQ:0.92 |
ML:0.85 |
a所有缩略语说明见表2。
b建议最佳制造与试验。 |
7.6相对齿根圆角敏感系数YδrelT
7.6.1概述
YδrelT近似地表示齿根圆角区域的应力集中程度。本标准采用的是ISO633-3:1996的B法。
7.6.2关于参考与长寿命应力的YδrelT
YδrelT可用式(111)计算
Y
δrelT=

……………………(111)
滑移层厚度

是材料的函数,可由表8查得。
表8滑移层厚度

值
材料a |
 /mm |
GG:σB=150N/mm2
GG,GGG(ferr.):σB=300N/mm2 |
0.3124
0.3095 |
NT,NV;全部硬化 |
0.1005 |
St: σB=300N/mm2
St: σB=400N/mm2 |
0.0833
0.0445 |
V,GTS,GGG(, perl.,bai.);σB=500N/mm2
V,GTS,GGG(perl.,bai.);σB=600N/mm2
V,GTS,GGG(perl.,bai.);σB=800N/mm2
V,GTS,GGG(perl.,bai.);σB=1000N/mm2 |
0.281
0.0194
0.0064
0.0014 |
Eh,IF(齿根);全部硬化 |
0.0030 |
a对所有缩略语说明见表2。 |
用式(112)计算相对应力梯度10):(应用于模数m=5mm,尺寸的影响包含在尺寸系数YX中(见7.8节)。)

………………………………(112)
标准的基准试验齿轮的值用

值用q
sT=2.5替代q
s代入式(112)中求得。
7.6.3静强度的YδrelT
YδrelT可用式(113)~式(117)计算。
a) 对于有较好限定屈服极限的钢St11):
Y
δrelT=
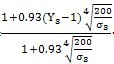
……………………(113)
b) 对于具用平稳增加的延伸率曲线与0.2%残余变形的钢、V钢与GGG(Perl.,bai.)铸铁11):
Y
δrelT=
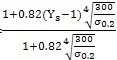
……………………(114)
c) 对于以产生初始裂纹时的应力为极限应力的Eh与IF(齿根)钢11):
YδrelT=0.44 YS+0.12……………………(115)
d)对于以产生初列裂纹时的应力为极限应力的NT, 与NV钢11)(所用缩略语说明见表2。)
YδrelT=0.20 YS+0.60……………………(116)
e)对于以产生初列裂纹时的应力为极限奕力的GG与GGG(ferr.)铸铁11):
YδrelT=1.0……………………(117)
7.7相对齿根表面状况系数YδrelT
7.7.1概述
相对齿根表面状况系数YδrelT用于考虑齿根表面状况对齿根应力的影响。主要取决于齿根圆角处的表面粗糙度。
表面状况对齿根弯曲强度的影响不仅取决于齿根圆角处的表面粗糙度,而且取决于尺寸和形状(这是缺口的缸口问题)。至今还没有经过充分的研究数据可供在本标准中采用。这里应用的方法仅是当伤痕或类似缺陷的深度不大于2R Z 时才有效。
注:2R Z为初步估计值。
本标准使用ISO 6336-3:1996的C法。
7.7.2基准应力与长寿命应力的YRelT
对于所有材料
——当R

时
YRelT=1.0……………………(118)
——当R

时
YRelT=0.9……………………(119)
7.7.3静强度的YRelT
对于所有材料的YRelT,与齿根圆角粗糙度无关。
RelT=1.0……………………(120)
7.8弯曲强度计算的尺寸系数YX
YX用以考虑尺寸大小对下列因素的影响:
——材料组织薄弱点的概率分布;
——应力梯度,根据材料理论,应力梯度随着尺寸的增加而减小;
——材料质量;
——锻造质量,缺陷的存在等。
本标准采用ISO6336-3:1996的B法。
按表9计算YX。
表9弯曲强度计算的尺寸系数YX
材料a |
循环次数 |
法向模数 |
尺寸系数YX |
St,St(cast),V,
GGG(perl.,bai),
GTS(perl.) |
3×104~1010 |
mn≤5
5<mn<30
mn≥30 |
Yx=1.0
Yx=1.03~0.0006 mn
Yx=0.85 |
Eh,IF(root),
NT(nitr.),
NV(nirt.),
NV(nirtocar) |
mn≤5
5<mn<30
mn≥30 |
Yx=1.0
Yx=1.05~0.01 mn
Yx=0.8 |
GGG,GGG(ferr.) |
mn≤5
5<mn<30
mn≥30 |
Yx=1.0
Yx=1.075~0.015 mn
Yx=0.7 |
所有材料 |
静态 |
- |
x=1.0 |
a 对所用缩略语说明见表2。 |
7.9弯曲强度计算的最小安全系数SFmin
关于安全系数的一般概念见第4章;弯曲强度计算的安全系数SF,见7.1.4。如果供需双方没有其他协议,本标准使用以下弯曲强度的最小安全系数SFmin;
SFmin=1.2……………………(121)
附录A
(规范性附录)
非常设计齿轮的特点
A.1行星齿轮的动载系数KV
A.1.1概述
在齿轮系中,包括多点啮合的齿轮,如惰轮与行星齿轮装置中的行星轮与太阳轮有各种不同的自然频率,这些频率可能高于或低于仅有一个啮合点的单对齿轮副的自然频率。
虽然用本标准的公式确定的KV值可能认为不可靠,但它们可以用于初步的评定。如果可能,建议使用更精确的方法重新评估。
应优先选用ISO6336-1:1996的A法分析非常规设计齿轮。为进一步取得资料可参考ISO6336-1:1996的6.1.1节。
A.1.2外齿轮副当量质量的计算
参见5.6.2
A.1.3非常规设计齿轮中共振速度的确定
A.1.3.1概述
应用A法确定非常规设计齿轮中的共振速度,然而,其他方法也可以近似使用。下面是一些例子:
a) 轴齿轮的轴径近似等轮齿中部的直径;
b) 两个刚性联结的同轴齿轮;
c) 两个小齿轮驱动一个大齿传输线;
d) 行星齿轮;
e) 惰轮(中间轮)。
A.1.3.2轴齿传输线的轴径近似等轮齿中部的直径
轴齿轮的高扭转刚度在很大程度上由轴的质量来补撑,因此,共振速度可用常规方法,即用小齿轮(轮齿部分的质量与法向啮合刚度cr计算)。
A.1.3.3两个刚性联结的同轴齿轮
计入较大齿轮的质量。
A.1.3.4两个小齿轮驱动一个大齿轮
因大轮的质量一般比小轮的质量大很多,各对啮合可分开考虑,即:
a) 第一个小轮与大轮构成的齿轮副;
b) 第二个小轮与大轮构成的齿轮副。
A.1.3.5行星齿轮
因为多个传动分支包含了不只是一个啮合刚度,行星齿轮的振动特性非常复杂,用简公式,例如B法计算动载系数通常是不精确的。尺管如此,下面经修改过的B法可用于KV的初步估算,估算后应进行仔细的理论或实验分析,或在使用经验的基础上加以验证。也可见本附录的引言部分。
a) 太阳轮和行星轮
确定太阳轮的共振速度nE1的诱导质量:
m
red=
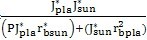
……………………(A.1)
式中:

——分别为太阳轮与一个行星轮单位齿宽的转动惯量,单位为千克·平方毫米每毫米(kg·mm
2/mm);
rbsun=0.5dbsun;
rbpla=0.5dbpla;
p——计算轮系中行星轮的个数。
由式(A.1)确定的mred值,用于计算N的公式中(见5.6.2.2),这里用的啮合刚度cr近似等于单个行星齿轮的啮合刚度,z1用太阳轮的齿数。
关于行星齿轮装置,应该注意式(12)~式(14)(见5.6.2.3)中的Ft等于作用在太阳轮上的总切向力除以行星轮的个数。
b) 行星轮和固定内齿圈
在此情况下,可假定内齿圈的质量为无穷大,因此,透导质量等于行星轮的当量质量,可由下式确定:
m
red=

……………………(A.2)
c) 行星轮和转动内齿圈
这各情况下,内齿圈的当量质量按外齿轮处理。行量轮的诱导质量可按式(A.2)计算。当内齿圈与几个行星轮啮合时,按A.1.3.4处理。
A.1.3.6中间轮
当驱动与被子驱动齿轮的尺寸大致桢,中间轮尺寸也大致相同或稍大时,可按下列公式近似值计算:
——诱导质量
m
red=

……………………(A.3)
——啮合刚度

……………………(A.4)
式中:

——分别为小轮、中间轮与大轮单位齿宽的转动惯量,单位为千克·平方毫米每毫米(kg·mm
2/mm);
——主动轮与中间轮副的啮合刚度;

——中间轮与从动轮副的啮合刚度(C
Y 的确定见附录B)。0.6<N<1.5时,建议进行更精确的分析。
如果中间轮明显大于主动轮和从动轮或主动轮和从动轮明显小于其他两轮时,KV按单个啮合副分别计算,即:
——主动轮——中间轮组合;
——中间轮——从动轮组合。
根据以上计算的mred值代入式(7),以确定共振速度。
对于未提及的情况,建议进行精确分析。
附录B
(规范性附录)
轮齿刚度c′和cr
B.1概述
轮齿刚度表示使一对或几对无偏差啮合的轮1mm
齿宽上产生1μm变形量所需的啮合线上的载荷12)。(轮齿变形可以用Ft(FmFtH)代替Fbt近似地确定。即采用相关系数将Ft转换成Fbt(切于基圆柱的载荷),当存在不确定因素(如测量误差)时也可不转换)。
单对齿刚度c′是直齿轮副一对轮齿的最大刚度。它大致等于单对齿啮合状态下一对轮齿的最大刚度13)。(当εα>1.2时,单对齿啮合区处界点处的c′可以假定近似于单对齿刚度的最大值。)
啮合刚度cr是啮合中所有轮齿刚度的平均值。
本标准使用权的ISO6336-1:1996的B法,适用于x1≥x2和-0.5≤(x1+x2)≤2的范围。
B.2单对齿刚度c′
B.2.1 c′的计算
对于单位载荷FtKA/b≥100N/mm2:
c′=0.8

………………(B.1)
B.2.2单对齿刚度的理论值

………………(B.2)
式中:

表B.1公式(B.3)中的常数
c1 |
c2 |
c3 |
c4 |
c5 |
c6 |
c7 |
c8 |
c9 |
0.04723 |
0.15551 |
0.25791 |
-0.00635 |
-0.11654 |
-0.00193 |
-0.24188 |
0.00529 |
0.00182 |
B.2.3轮坯结构系数CR
对于由实心的圆盘形轮坯制成的齿轮CR=1。对于其他的齿轮:
C
R=1+

……………………(B.4)
边界条件:
有关代号见图B.1。
图B.1确定CR时的代号
B.2.4基本齿条系数CB
CB可按式(B.5)计算:
C
B=[1+0.5(1.2-

)][1-0.02(20°-α
pn)]………………(B.5)
B.2.5 附加的资料
a)内齿轮:内齿轮的单对齿刚度理论值的近似值可由公式(B.2),公式(B.3)确定,这时取

为无穷大。
b)单位载荷(FtKA)/b<100N/mm2:

………………(B.6)
c)以上情误解是基于钢制齿轮副,对于其他的材料组合,见ISO6336-1:1996第9章。
B.2.6啮合刚度cγ
对于εα≥1.2的直齿轮与β≤30°的斜齿轮,其啮合刚度:
c
γ=

(0.75 ε
α+0.25)……………………(B.7)
式中:

——根据式(B.1)确定。
附录C
(资料性附录)
使用系数KA的推荐值
C.1使用系数的确定
使用系数最好通过具体应用场合的实际使用经验的分析来确定(见ISO/TR10495:1997),当无实践经验可用时,通过仔细的分析研究确定。
使用系数KA用以修正Ft。KA是考虑齿轮啮合外部因素引起的附加到名义载荷上的载荷的影响系数。当不可能全面的系统分析或用合适的累积损伤准则的测量值来确定当量切向载荷时(见5.2),可使用表C.1中的经验性指导值。
C.1使用系数的近似值
当缺乏使用经验或无详细的分析资料可用时,可使用表C.1中的值。使用表C.1时注意,在某些使用场合KA的值会比表(C.1)中的值高得多,已使用过的值高达10。
表C.1中的值仅用于在非共振区运行的、载荷相对稳定的传动。如果运行中有非共振区运行的、载荷相对稳定的传动。如果运行中有非正常重载、电机的起动转矩大、间歇使用或严重的反复冲击负荷,应当核算其静强度和有限寿命下的承载能力(见ISO6336-1:1996、ISO-6336-2:1996、ISO6336-3:1996)。
例子:
a) 透平机械和发电机
若系统中的电流矩路,转矩可高达名义转矩的6倍。这样的过载可通过安全联轴器保护。
b) 电动机和压缩机
若泵的频率和扭转振动的固有频率相同,会产生相当大的交变应力。
c)厚板轧机和钢坯轧机
要考虑到入轧转矩可高达轧制转矩的6倍。
d)用同步电动机驱动
启动瞬时(大约10个波幅变化的时间),产生的交变转矩可高达名义转矩的5倍。但,这个危险的交变转矩通常可以通过合适的调节予以完全避免。
由于尖峰转矩的大小取决于质量弹性系统,力的作用时间和安全保护(安全联轴器、电器的非同步转换保护),这里给出的资料和数值通常不能使用。
因此,在重要的场合要认真进行分析。建议达成合适的协议。
在用户的订单中说明的使用系数应考虑作为最小要求值。
要考虑附加的转动惯量(如飞轮效应产生的转矩)。有时,制动转矩是最大载荷,半影响承载能力计算。
假定使用的材料应有合适的过载能力。当使用的材料的过载能力很小时,应对尖峰载荷进的强度进行校核。
当使用的联轴器有如下特性时——液力偶合器、弹性联轴器和特殊的减振联轴器——KA在中等和严重冲击时的取值可以减小。
表C1使用系数KA
原动机工作特性 |
工作机工作特性 |
均匀平稳 |
轻微冲击 |
中等冲击 |
严重冲击 |
均匀平稳 |
1.00 |
1.25 |
1.50 |
1.75 |
轻微冲击 |
1.10 |
1.35 |
1.60 |
1.85 |
中等冲击 |
1.25 |
1.50 |
1.75 |
2.00 |
严重冲击 |
1.50 |
1.75 |
2.00 |
2.25或更大 |
表C2原动机工作特性
工作特性 |
原动机 |
均匀平稳 |
电动机(如直流电动机)、平稳运行的1)蒸汽轮机或燃汽轮机(起动力矩
很小,起动不频繁) |
轻微冲击 |
蒸汽轮机、燃汽轮机、液压马达或电动机(具有大的、频繁的起动转矩)2) |
中等冲击 |
多缸内燃机 |
严重冲击 |
单缸内燃机 |
a可根据振动试验或类似设备确定。
b见GB/T 3480中寿命系数ZNT、YNT的图。考虑瞬间过载的影响,见C2中的例子。 |
表C3工业齿轮工作机的工作特性示例
工作特性 |
工作机 |
均匀平稳 |
载荷平稳的发电机,载荷平稳的带式或板式输送机,螺杆输送机,轻型升降机,
包装机械,机床进给机械,通风机,轻型离心机,离心泵,用于轻质液体或均匀
密度物料的搅拌机、混料机,剪切机,压力机,冲压机1);立式传动装置和往复
移动齿轮装置2) |
轻微冲击 |
载荷非均匀平稳的带式或板式输送机,机床主传动装置,重型升降机,起重机
回转齿轮装置,工业或矿山用风机,重型离心机,离心泵,粘性介质和非均匀
密度物料的搅拌机、混料机,多缸活塞泵、给水泵,通用挤压机,压延机,回
转窑,轧机连续的锌带、铅带轧机,线材和棒材轧机3) |
中等冲击 |
橡胶挤压机,连续工作的橡胶和塑料混料机,轻型球磨机,木工机械
(锯片和车床),钢坯轧机3),4) |
严重冲击 |
挖掘机(斗轮驱动、斗链驱动、筛分驱动),挖土机,重型球磨机,橡胶压轧机,
破碎机(石料、矿石),铸造机械,重型给水泵,钻机,压砖机,卸载机,落砂机
,带材冷轧机3),5),压坯机,轧碎机。 |
a额定载荷为最大转矩。
b额定载荷为最大启动转矩。
c额定载荷为最大轧制转矩。
d转矩受限流器限制。
e带钢的频繁开裂会导致KA上升到2.0。 |
附录D
(资料性附录)
圆柱齿轮轮齿鼓形修形与齿端修缘量的指导值
D.1概述
良好设计的鼓形修形和齿端修缘对齿轮齿宽上载荷分布具有益的影响。设计的零件图应该基于对齿轮的变形与制造偏差的认真考虑。如果变形较大,应将螺旋修正叠加地鼓形与齿端修缘上,但首先应将螺旋线修形设计好。
D.2鼓形量Cβ
从经验中得出以下非强制性的规则,达到可接受的载荷分布所必需的鼓形量(见图D.1)按如下确定。
在10μm≤Cβ≤40μm,加上制造公差5~10μm的条件下,如果齿轮不修鼓形,bcai/b值会大于1,Cβ≈0.5Fβxcv.
为避免齿端过载,取鼓形量为:
Cβ=0.5(fsh+fHβ)……………………(D.1)
实际应用中当齿轮的结构刚度使得fsh, 可以忽略,或当螺旋线修形使齿宽中部的变形得到补偿时,可按下列计算:
Cβ=0.5fHβ……………………(D.2)
在10μm≤Cβ≤25μm,加上大约5~10μm的条件下,对于高精度可靠度的高速齿轮来说,以上数值的60%~70%已经足够。见图D.1。
图D.1鼓形量Cβ(b)与宽度b(b)
D.3齿端修缘量CⅠ(Ⅱ)和宽度bⅠ(Ⅱ)
D.3.1 C1法
本方法是基于对没有齿端修缘的齿轮副,当量啮合向误差的设定值与齿轮鼓形量的推荐值。
a) 齿端修缘量(见图D.2)
图D.2齿端修缘量CⅠ(Ⅱ)和宽度bⅠ(Ⅱ)
对调质齿轮:CⅠ(Ⅱ)≈Fβxcv加上制造公差5~10μm。
那么,用D.2中对Fβxcv的分析,CⅠ(Ⅱ)应近似地为:
CⅠ(Ⅱ)= fsh+1.5fHβ………………(D.3)
对表面硬化与氮化齿轮:CⅠ(Ⅱ)≈0.5Fβxcv加上制造公差5~10μm。
那么,用D.2中对Fβxcv的分析,CⅠ(Ⅱ)应近似地为:
CⅠ(Ⅱ)=0.5( fsh+1.5fHβ)+1.5fH………………(D.4)
当齿轮结构刚度使得fsh可以忽略不计,或当螺旋线修形补偿时,按式(D.2)计算。
对于高精度高可靠度的切线速度齿轮,CⅠ(Ⅱ)取上述计算值的60%~70%。
c) 齿端修缘的宽度
当载荷 近似恒定和线速度较高时;取bⅠ(Ⅱ)和(0.1b)或(1.0m)两者中的较小者。
对于变载荷,线速度为低、中速时:
brel=(0.5~0.7)b……………………(D.5)
D.3.2 C2法
本方法基于假一沿齿宽的载荷均匀分布时的齿轮副的变形:
δbth=Fm/(bcγ)……………………(D.6)
式中:
Fm=FtKAKV
对于高精度高可靠度的高切线速度齿轮,用下列公式计算:
CⅠ(Ⅱ)=(2~3)δbth……………………(D.7)
brel=(0.8~0.9)b……………………(D.8)
对于较差精度的类似齿轮:
CⅠ(Ⅱ)=(3~4)δbth……………………(D.9)
brel=(0.7~0.8)b……………………(D.10)