圆柱齿轮 检验实施规范 第4部分:
表面结构和轮齿接触斑点的检验
1范围
GB/Z18620的这一部分提供了关于齿轮齿面表面粗糙度和轮齿接触斑点检测方法的推荐文件。
本指导性技术文件所提供的数值不应作为严格的精度判据,而作为共同协议的关于钢或铁制齿轮的指南来使用。
2 引用标准
下列标准所包含的条文,通过在本指导性技术文件中引用而构成为本指导性技术文件的条文。本指导性技术文件出版时,所示版本均为有效。所有标准都会被修订,使用本指导性技术文件的各方应探讨使用下列标准最新版本的可能性。
GB/T 131-1993 机械制图 表面粗糙度符号、代号及其注法(eqv ISO 1302:1992)
GB/T1356-2001通用机械和重型机械用圆柱齿轮 标准基本齿条齿廓(idt ISO 53:1998)
GB/T3505-2000产品几何技术规范 表面结构 轮廓法 表面结构的术语、定义及参数(eqv ISO 4287:1997)
GB/T 6062-1985 轮廓法触针式表面粗糙度测量仪 轮廓记录仪及中线制轮廓计(neq ISO 1880:1979)
GB/T 10095.1-2001渐开线圆柱齿轮 精度 第1部分:轮齿同侧齿面偏差的定义和允许值(idt ISO 1328-2:1997)
GB/T 10095.1-2001渐开线圆柱齿轮 精度第2部分:径向综合偏差与径向跳动的定义和允许值(idt ISO 1328-2:1997)
GB/T10610-1998 产品几何技术规范 表面结构 轮廓法评定表面结构的规则和方法(eqv ISO 4288:1996)
ISO11562:1996 产品几何技术规范(GPS) 表面结构:轮廓方法 相位校正滤波器的计量特征
ISO 13565-1:1996 产品几何技术规范(GPS) 表面结构:轮廓方法 分层功能性质的表面 第1部分:滤波和一般测量条件
ISO13565-2:1996产品几何技术规范(GPS) 表面结构:轮廓方法 分层功能性质的表面 第2部分:使用等效直线的实体比率曲线的高度特征
3 符号和定义
3.1符号
单项要素测量所用的偏差符号,用小写字母(如f)加上相应的下标组成;而表示若干单项要素偏差组合的“总”偏差所用的符号,采用大写字母(如F)加上相应的下标组成。
fwβ |
齿面波度的波幅 |
μm |
bc1 |
接触斑点的较大长度 |
% |
bc2 |
接触斑点的较小长度 |
% |
hc1 |
接触斑点的较大高度 |
% |
hc2 |
接触斑点的较小高度 |
% |
lr |
精糙度轮廓的取样长度 |
mm |
ln |
评定长度(不注明规定ln=5×lr见
GB/T3505-2000中表C2和GB/T10610-1998中4.4) |
mm |
Wr |
实体长度 |
% |
Mr1,Mr2 |
实体(粗糙度核心轮廓)分段点 |
% |
Ra |
粗糙度轮廓的算术平均偏差 |
μm |
Rk |
粗糙度核心轮廓深度 |
μm |
Rpk |
减去的峰高 |
μm |
Rυk |
减去的谷深 |
μm |
RZ |
粗糙度轮廓的最大高度(见GB/T3505) |
μm |
Z(x) |
纵坐标值 |
μm |
λ |
波长 |
mm |
λc |
截止波长(波纹度的截止短波长) |
mm |
λs |
粗糙度的截止短波长 |
mm |
3.2 术语和定义
3.2.1 通用术语
3.2.1.1 表面加工纹理
表面主要加工痕迹的方向(见图1a)。
注:表面加工纹理通常是由所用的加工方法决定的。
3.2.1.2 粗糙度
粗糙度轮廓的微观不平度(见3.2.2.1)。它是在加工过程中所形成的表面结构(微观几何形状特性)的一种组成成分,不包括波纹度和形状偏差。
3.2.1.3波纹度
波纹度轮廓的不平度(见3.2.2.2)。它是表面形状特性的一种组成成分,粗糙度是叠加在它的上面的(见图1a,b,c)。通常,加工的齿轮轮齿表面的波纹度间距显著大于粗糙度间距。
图1
3.2.2 与评定表面轮廓有关的术语
3.2.2.1 粗糙度轮廓
粗糙度轮廓的通过波段是由λc与λs轮廓滤波器限定的(见ISO 11562:1996第3章),见图1。
注
1 粗糙度轮廓是评定粗糙度轮廓参数的基础
2理论在ISO 11562:1996的3.2中给出了λc和λs之间的联系数。
3.2.2.2 波纹度轮廓
波纹度轮廓是在用轮廓滤波器λc后留下的长波成分的周期性部分
3.2.2.3 粗糙度轮廓的中线
粗糙度轮廓的中线是被轮廓滤波器λc所压缩后的长波轮廓成分(见ISO 11562:1996的3.2.1)。
注:粗糙度轮廓的中线是测量粗糙度轮廓纵坐标Z(x)的其准线,见图2。
3.2.2.4 纵坐标值
所评定轮廓在任一位置x的高度。
3.2.2.5 粗糙度的取样长度lr
用于识别所评定轮廓不平度特征的x轴方向的长度。粗糙度的取样长度lr在数值上同轮廓滤波器λc的特性波长相等(见GB/T3505)。
图2 测量长度
3.2.2.6 评定长度ln
用于评定被测定轮廓的x轴方向的长度,评定长度可以包括一个或几个取样长度(见GB/T3505-2000中4.4)。
3.2.2.7 轮廓滤波器的截止波长λc
正弦波轮廓的波长,在这一波长的幅值的50%被轮廓滤波器通过(见ISO 11562)。
3.2.2.8截止比
给定通过波段的长波截止波长与短波截止波长之比(见ISO11562)。
3.2.3 与表面粗糙度参数有关的术语
3.2.3.1粗糙度轮廓的最大高度RZ
在取样长度内最大的轮廓峰高Zp与最大的轮廓谷深Zυ之和(见GB/T3505-2000中4.1.3和图8)。
注:通常这个参数是按五个连接的取样长度的最大高度的平均值来测定的,这评定长度就包含五个取样长度(见图3)。
图3 粗糙度轮廓的最大高度
3.2.3.2 粗糙度轮廓的算术平均Ra
在取样长度内纵坐标绝对值Z(x)的绝对值的算术平均值(见GB/T3505-2000中4.2.1)。
Ra=
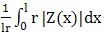
……………………(1)
式中:lr——Ra的取样长度;
Z(x),Zi——纵坐标值。
注:算术平均Ra是按五个连接的取样长度组成的评定长度来确定的(见图4和GB/T10610)。
3.2.4轮齿波度
波度是齿面的周期性波纹度,波度的特殊形状有以下特征:
——表面加工纹理接近平行于(同相啮齿轮的)接触线;
——投影在节圆上(在回转平面内)的波纹数为整数,见图5;
——它们是产生噪声的一个可能原因。
图5 斜齿轮的波度
4表面结构
试验研究和使用经验表明,在表面结构等级和齿轮承载能力状况之间存在某种关系。GB/T3480叙述了表面粗糙度对轮齿点蚀和弯曲强度的影响,在ISO/TR 13989中论述了粗糙度对胶合的影响。
同粗糙度一样,波纹度和表面结构的其他特征也会影响材料的表面抗疲劳能力,因此,当需要高标准的性能和可靠性时,要细心地记录未滤波的轮廓来反映轮齿表面结构。
在本指导性技术文件中没有推荐适用于特定用途的表面粗糙度、波纹度的等级和表面加工纹理的形状或类型,也未鉴别这种表面不平度的成因。
注意——要强调的是:在规定轮齿现在结构的特征极限值之前,齿轮设计者和齿轮工程师们应熟悉有关的国家标准和这方面的其他文献,参见第2章的引用标准。
5 功能考虑
受表面结构影响的轮齿功能特性可以分为几类:
——传动精度(噪声和振动);
——表面承载能力(如点蚀=胶合和磨损);
——变曲强度(齿根过渡曲面状况)。
5.1 传动精度
表面结构包含两个主要特征:粗糙度和波纹度。
表面波纹度或齿面波度会引起传动误关,这种影响依赖波纹的纹理相对于瞬间接触线和接触迹线的方向,如果波纹的纹理平行于瞬时接触线或接触区(垂直于接触迹线),齿轮啮合时会出现一个高音的刺耳声(高于啮合频率的古怪的谐波成分)。
在少数情况下,表面粗糙度会使齿轮噪声的特性产生差异(光滑的齿面与粗糙的比较),一般它对齿轮啮合频率的噪声及其谐波成分不产生影响。
5.2承载能力
表面结构可在两个大致的方面影响轮齿耐久性:齿面劣化和轮齿折断。
5.2.1 齿面劣化
齿面劣化有磨损、胶合中擦伤和点蚀等。齿廓上的表面粗糙度和波纹度与此有关。表面结构、温度和润滑剂决定影响齿面耐久性的弹性流体动力(EHD)膜的厚度。
5.2.2 弯曲强度
轮齿折断可能是疲劳(高循环应力)的结果,表面结构是影响齿根过渡区应力的一个因素。
5.3测量方法的影响
测量方法的仪器、定位、方向和分析(滤波器等)必须选择得使其能体现轮齿的功能区域和接触迹线。
6图样上应标注的数据
当用户已规定时,或当设计和运行要求必需时,在图样上应标出完工状态表面粗糙度的适当的数值。如图6a和b所示。
图6
7测量仪器
触针式测量仪器通常用来测量粗糙度。可采用以下几种类型的仪器来进行测量,不同的测量方法对测量不确定度的影响有不同的特性(见图7)。
a) 在被测表面上滑行的一个或一对导头的仪器(仪器有一平直的基准平面);
b) 一个在具有名义表面形状的基准平面上滑行的导头;
c) 一个具有可调整的或可编程的导头组合一起的基准线生成器,例如,可由一个坐标测量机来实现基准线;
d) 用一个无导头的传感器和一个具有较大测量范围的平直基准对形状、波纹度和粗糙度进行评定。
图7 仪器特性以及与制造方法相半的测量行程方向
根据国家标准,触针的针尖半径应为2μm或5μm或10μm,触针的圆锥角可为60°或90°。此外,有关仪器特性的详细资料见GB/T 6062,在表面测量的报告中应注明针尖半径和触针角度。
在对粗糙度或波纹度进行测量时,需要有无导头传感器和一个被限定截止的滤波器,它压缩表面轮廓的长波成分或短波成分。测量仪器仅适用于某些特定的截止波长,表1给出了适当的截止波长的参考值。必须要认真选择合适的触针针尖径、取样长度和截止滤波器,见GB/T6062、GB/T10610和ISO11562,否则测量中就会出现系统误差。
根据波纹度、加工纹理方向和测量议器的影响的考虑,可能要选择一种不同的载止值。
表1滤波和截止波长
模数/mm |
标准工作齿高/mm |
标准截止波长/mm |
工作齿高内的截止波数 |
1.5 |
3.0 |
0.2500 |
12 |
2.0 |
4.0 |
0.2500 |
16 |
2.5 |
5.0 |
0.2500 |
20 |
3.0 |
6.0 |
0.2500 |
24 |
4.0 |
8.0 |
0.8000 |
10 |
5.0 |
10.0 |
0.8000 |
12 |
6.0 |
12.0 |
0.8000 |
15 |
7.0 |
14.0 |
0.8000 |
17 |
8.0 |
16.0 |
0.8000 |
20 |
9.0 |
18.0 |
0.8000 |
22 |
10.0 |
20.0 |
0.8000 |
25 |
11.0 |
22.0 |
0.8000 |
27 |
12.0 |
24.0 |
2.5000 |
30 |
16.0 |
32.0 |
2.5000 |
13 |
20.0 |
40.0 |
2.5000 |
16 |
25.0 |
50.0 |
2.5000 |
20 |
50.0 |
100.0 |
8.0000 |
12 |
8 齿轮齿面表面粗糙度的测量
本章论述了各参数的优先值、截止波长和评定长度以及渐开线圆柱齿轮轮齿和齿根过渡区表面结构的测量方法。
在测量表面粗糙度时,触针的轨迹应与表面加工纹理的方向相垂直,见图7和图8中所示方向。测量还应垂直于表面,因此,触针应尽可能紧跟齿面的变曲的变化。
在对轮齿齿根的过渡区表面粗数度测量时,整个方向应与螺旋线正交,因此,需要使作一些特殊的方法,图8中表示了一种适用的测量方法,传感器的头部,在触针前面,有一半径为r(小于齿根过渡曲线的半径R)的导头,安装在一根可旋转的轴上,当该轴转过角度约100°时,触针的针尖描绘出一条同齿根过渡区接近的圆弧。当齿根据过渡区足够大,并且该装置仔细的定位时方可进行粗糙度测量。
注:导头直接作用于表面,应使半径r>50λc,以避免因导头引起的测量不确定度。
图8 齿根过渡曲面粗糙度的测量
使用导头形式的测量仪器进行测量还有另一种办法,选择一种适当的注塑材料(如树脂等)制作一个相反的复制器。当对较小模数齿轮的齿根过渡部分的粗糙度进行测量时,这种方法是特别有用的。在使用这种方法时,应记住在评定过程中齿廓的记录曲线的凹凸是相反的。
8.1评定测量结果
直接测得的粗糙度参数值,可直接与规定的允许值比较。
参数值通常是按沿齿廓取的几个接边的取样长度上的平均值确定的,但是应考虑到表面粗糙度会高测量行程有规律地变化,因此,确定单个取样长度的粗糙度值,可能是有益的。为了改进测量数值的统计上的准确定性,可从几个平行的测量迹线计算其算术平均值。
如不用相对于基准有关的导头测量轮廓可望获得最好的结果,这就是第7章中7b和7d所提到的那种设备情况。
参见第7章中粗糙度、波纹度、形状和形状偏差同时被评定的情况。
在此情况下,为了将粗糙度从轮廓的较长波长的组成中分离出来,在按ISO11562和GB/T10610用相位校正滤波器进行滤波之前,首先必须将名义的形状成分消除。
当齿轮齿廓太小,以致无法在5个接连的取样长度进行测量时,允许在分离的齿上取单个取样长度进行测量(见GB/T10610-1998第7章),但必须在参数符号后面附注取样长度的个数,例如:RZ1、RZ3。
为了避免使用滤波器时评定长度的部分损失,可以在没有标准滤波过程的情况下,在单个取样长度评定粗糙度。图9说明为消除形状成分等,将(没有滤波器)轨迹轮廓细分为短的取样长度l1、l2、l3等所产生的滤波效果。为了同标准方法的滤波结果相比较,取样长度应与截止值λc为同样的值。
图9取样长度和滤波的影响
8.2参数值
从对数得出的值应该与规定值进行比较,规定的参数值应优先从表2和表3中所给出的范围中选择,无论是Ra还是RZ 均可作为一种判断依据,但是,两者不应在同一部分使用。
在GB/T10095.1中规定的齿轮精度等级和表2和表3中粗糙度等级之间没有直接的关系。
注:在关于Ra和RZ 的表中,相同的表面状况等级并不与特定的制造工艺对相应,这一点尤其适用表中1级到4级的表列值。
表2 算术平均偏差Ra的推荐极限值
等级 |
Ra |
模数/mm |
m>6 |
6≤m≤25 |
m>25 |
1 |
|
0.04 |
|
2 |
|
0.08 |
|
3 |
|
0.16 |
|
4 |
|
0.32 |
|
5 |
0.5 |
0.63 |
0.80 |
6 |
0.8 |
1.00 |
1.25 |
7 |
1.25 |
1.6 |
2.0 |
8 |
2.0 |
2.5 |
3.2 |
9 |
3.2 |
4.0 |
5.0 |
10 |
5.0 |
6.3 |
8.0 |
11 |
10.0 |
12.5 |
16 |
12 |
20 |
25 |
32 |
表3微观不平度十点高度R 的推荐极限值
等级 |
R |
模数/mm |
m>6 |
6≤m≤25 |
m>25 |
1 |
|
0.25 |
|
2 |
|
0.50 |
|
3 |
|
1.0 |
|
4 |
|
2.0 |
|
5 |
3.2 |
4.0 |
5.0 |
6 |
5.0 |
6.3 |
8.0 |
7 |
8.0 |
10.0 |
12.5 |
8 |
12.5 |
16 |
20 |
9 |
20 |
25 |
32 |
10 |
32 |
40 |
50 |
11 |
63 |
80 |
100 |
12 |
125 |
160 |
200 |
8.3粗糙度轮廓的实体比率曲线
本章的以下各条对与高应力接触表面相关的表面粗糙度的功能特性的各参数用实体比率曲线作了规定(见GB/T3505)。
对于高应力接触表面,将其形状偏差和波纹度偏差的规定极限值保持在一个很小值的范围内是很重要的。
这些参数描述了实体比率曲线的形状,从而说明粗糙度廓的高度和特性。首先要有一张全面有代表性的、无误差的,经过滤波的粗糙度轮廓图。才能进行下文中叙述的表面结构的评定过程。
8.3.1实体比率曲线的有关术语
a)截止线:一条平行于中线切割粗糙度轮廓的线(见图10a);
b)实体长度;截线所截位于轮廓峰内各段截线长度之和,用它与评定长度之比的百分数表示(见GB/T3505-2000中3.2.14的轮廓的实体长度)。
8.3.2实体比率曲线的结构
在粗糙度轮廓的实体比率曲线上每点的坐标:
a) 在x轴:用评定长度的百分数表示的五个接连的取样长度的实体长度;
b) 在 轴:粗糙度轮廓截线的纵坐标(见图10a)。
8.3.3 实体比率曲线的参数
a)粗糙度核心轮廓:粗糙度核心轮廓是不包含有突出的峰点和深谷的粗糙度轮廓(见ISO13565-2:1996中3.1);
b)核心粗糙度深度Rk(μm):核心粗糙度深度是粗糙核心轮廓的深度(图10b)(见ISO 13565-2:1996中3.1.1);
图10按ISO13565-2规定的实体比率曲线的特性值
c) 实体区段Mr1(%):是为突峰从粗糙度核心轮廓分开的截线而确定的实体区段Mr1(见ISO 13565-2:1996中3.1.2);
d) 实体区段Mr2(%):是为深谷从粗糙度核心轮廓分开的截线而确定的实体区段Mr2(见ISO 13565-2:1996中3.1.2)
e) 削减的峰高Rpk(μm):是粗糙度核心轮廓之上的突出的峰的平均高度(见ISO 13565-2:1669中3.28);
f) 削减的谷深Rυk(μm):穿过粗糙度核心轮廓的谷底的平均深度值(见ISO13565-2:1996中3.3)。
注:8.3.5中的平均方法减少了界外值对Rpk和Rυk的影响。
8.3.4 实体比率曲线的测量条件
a)实体比率曲线的测量仪器:使用触针式仪器来测定实体比率曲线的参数,此仪器用几何表面或基准线生成器对触针轨迹进行控制。
b)测量方向:应选择给出粗糙度最大值的测量路程。
8.3.5实体比率曲线的参数的确定
8.3.5.1 Rk、Mr1、Mr2的确定
在横坐标Mr1和Mr2之间取间距40%的分段,贯穿实体比率曲线,画一条相对于x轴斜率最小的平均直线,见图11。假如有两个或多个斜率相同的线段,则选定较接近曲线较高端的线段,此直线在0%和100%处两点纵坐标之间的差值等于Rk。
图11 Rk、Mr1和Mr2特性值的确定与测量
8.3.5.2 Rpk和Rυk的确定
从0%和100%处的Z轴上交点画切向粗糙度轮廓的横截线A和B,见图11和12,确定线A以上的粗糙度轮廓所围面积AA和线B以下的谷部轮郭所围的面积BA。
在0%处的 轴方向与在线段c1—a1以上构造出一个面积等于BA的直角三角形a2b2c2。
边上c1—b1与Rpk相等,边长c1—b2与Rυk相等。
对不同粗糙度轮廓的实体比率曲线的对比,说明了如何利用实体比率曲线来估计给定表面对表面损伤的相对抵抗能力。
8.3.6实体比率曲线的参数Rk、Rpk、Rυk的应用
图11阐明Rk不能仅以轮廓深度值来表示,还要有实体比率的主要部分的斜率值。
实体比率曲线的斜率是十分重要的,它的值表明了在更深地进入核心轮廓时实体比率的增加趋势,因此Rk对表面的承载能力有重要意义。
图12 Rpk和Rυk的测定
ISO13565-2借助于3条直线的参数描述了实体比率曲线的形状,它将轮廓总深度细分为:
——突峰区域(与初始运转状况有关,例如磨合和磨损);
——核心区域(与承载能力、使用特性有关);
——深谷区域(与润滑=保存油有关)。
图13说明把突出的峰和谷从核心轮廓中分离出来的方法。假如Rk等于0时(见图13a),图中清楚地表明了峰和谷的明显分离。图13b表明了Rk值的扩展(向中间的直线两边),除去表面很突出的峰和谷,具有接近高斯分布的纵坐标。
虽然计量学上确定实体比率曲线的参数,并不比确定齿轮的Ra或R 1)(1)Beyer,Eckolt,Hillmann,Witteklpf用扫描电子显微镜和触针式测量表面仪器研究轮齿齿面PTB报告PTB-F-2(1987年11月)。)更困难,但实体比率曲线的参数所能提供的信息,对当前要使用来说研究得还不够充分。因此,目前还不能给出那些参数的推荐值。
图13 粗糙度核心区域对突峰和深谷的量值的影响及其特性
9能轮齿接触斑点的检验
本章将对获得与分析接触斑点的方法进行解释,还给出对齿轮精度估计的指导。
检测产品齿轮副在其箱体内所产生的接触斑点,可以帮助我们对轮齿间载荷分布进行评估。
产品齿轮与测量齿轮的接触斑点,可用于装配后的齿轮的螺旋线和齿廓精度的评估。
9.1 检测条件
9.1.1精度
产品齿轮与测量齿轮副轻载下的接触斑点,可以从安装在机架上的齿轮相啮合得到。为此,重要的是,齿轮轴线的不平行度,在等于产品齿轮齿宽的长度上的数值,尽可能在接近的位置上测定,不得超过0.005mm。同时也要保证测量齿轮的齿宽不小于产品齿轮的齿宽,通常这意味着对于斜面齿轮需要一个专用的测量齿轮,对于大齿轮来说,这样的测量齿轮可以是一个特制的产品齿轮的样品,并保留它,便于作为备件替换损坏了的齿轮。
相配的产品齿轮副的接触斑点也可以在相啮合的机架上获得。
9.1.2载荷分布
产品齿轮副在其箱体内的轻载接触斑点,有助于评估载荷的可能分布,在其检测过程中,齿轮的轴颈应当位于他们的工作位置,这可以通过对轴承轴颈加垫片调整来达到。
9.1.3印痕涂料
适用的印痕涂料有:装配工的蓝色印痕涂料和其他专用涂料。应选择那些能确保油膜层厚度在0.006~0.012mm的应用方法。
9.1.4 印痕涂料层厚度的标定
这对判明接触斑点的检查结果是很重要的,操作者掌握了稳定的工艺后,就可来确立印痕涂料层的厚度,在垂直于切平面的方向上以一个已知小角度移动齿轮的轴线,即在轴承座上加垫片并观察接触斑点的变化,这标定工作应该有规范地进行以确保印痕涂料、测试载荷和操作工人的技术都不改变。
9.1.5测试载荷
用于获得轻载接触斑点所施加的载荷,应能恰好保证被测齿面保持稳定的接触。
9.1.6记录测试结果
接触斑点通常以画草图、照片、录像记录下来,或用透明胶带覆盖在接触斑点上,再把粘住接触斑点的涂料的胶带撕下来,贴在优质的白卡片上。
9.2操作者的培训
要完成以上操作的人员,应训练正确地操作,并定期检查他们的效果,以确保操作效能的一致性。
9.3接触斑点的判断
接触斑点可以给出齿长方向配合不准确的程度,包括齿长方向的不准确配合和波纹度,也可以给出齿廓不准确性的程度,必须强调的是作出的任何结论都带有主观性,只能是近似的并且依赖于有关人员的经验。
9.3.1与测量齿轮相啮的接触斑点
图14到图17所示的是产品齿轮与测量齿轮对滚产生的典型的接触斑点示意图。
9.3.2齿轮精度的接触斑点
图18和表4、表5给出了在齿轮装配后(空载)检测时,我们所预计的在齿轮精度等级和接触斑点分布之间关系的一般指示,必须记住实际的接触斑点不一定同图18中所示的一致,在啮合机架上所获得的齿轮检查结果应当是相似的。
注:图18、表4和表5对齿廓和螺旋线修形的齿面是不适用的。
注意:这些表格试图描述那些从通过直接的测量,证明符号表列精度的齿轮副中获得的最好接触斑点,不要把它们理解为证明齿轮精度等级的可替代方法。
图18接触斑点分布的示意图
表4 斜齿轮装配后的接触斑点
精度等级按GB/T10095 |
bc1
占齿宽的百分比 |
hc1
占有效齿面高度的百分比 |
bc2
占齿宽的百分比 |
hc2
占有效齿面高度的百分比 |
4级及更高
5和6
7和8
9至12 |
50%
45%
35%
25% |
50%
40%
40%
40% |
40%
35%
35%
25% |
30%
20%
20%
20% |
表5直齿轮装配后的接触斑点
精度等级按GB/T10095 |
bc1
占齿宽的百分比 |
hc1
占有效齿面高度的百分比 |
bc2
占齿宽的百分比 |
hc2
占有效齿面高度的百分比 |
4级及更高
5和6
7和8
9至12 |
50%
45%
35%
25% |
70%
50%
50%
50% |
40%
35%
35%
25% |
50%
30%
30%
30% |
附录A
(标准的附录)
用接触斑点控制齿轮轮齿的齿长方向配合精度
A1目的
本附录叙述用接触斑点来规定和控制齿轮轮齿的齿长方向配合精度。
论述接触斑点的两种产生办法:
——静态方法,通过软涂层的转移;
——动态方法,通过硬涂层的磨损。
A2应用
A2.1典型用途
用接触斑点作定量和定性控制齿轮的齿长方向配合精度的方法,经常用于以下场合:大齿轮不能装在现成的检查仪上及工作现场没有检查仪可用。其优点是:
——测试工具的便于携带;
——可以测试其他方法不能测试的大型和复杂的表面;
——测试简单和快捷;
——如果通过适当的标定,测试结果具用可再现性;
——对装配状况的敏感性,例如轴承配合不良和齿轮箱变形;
——可以探测微小的齿长方向配合误差和系统差的能力,例如齿面波度,这在导程和齿廓检测曲线图里并不表现;
——能够评定轮齿的配合性,包括大齿轮和小齿轮的叠加或累积偏差的作用,这在导程和齿廓检测曲线图里并不表现;
——能评定整个齿面,而不是单单一条表示齿廓或齿长方向配合的曲线。
A2.2特定应用领域
一些使用接触斑点测试方式的例子:
——船舰用大型齿轮;
——高速齿轮;
——船舰和高速齿轮箱的现场组装;
——起重机、提升机、桥、微波天线等的开式末级传动齿轮的装配;
——圆锥齿轮;
——航天齿轮。
A2.3使用方法
静态方法:通过小齿轮和大齿轮之间一层薄薄的涂层转移来完成,不加载荷,一般用手转动。
动态方法:需要可控制的递增适当的载荷并按设计规定的动转速度来完成。
A3 使用说明
A3.1静态方法
接触斑点检测,使一个齿轮的齿上的规定厚度的印痕涂料转移到相配齿轮的齿上。将接触斑点检测的结果与规定的斑点作比较。这规定斑点是分析想要的无载荷接触状况得出的,或按类似齿轮副的经验得出的。这技术与精密仪器和精密机床的接触表面的手工配合或刮研相类似。
A3.2动态方法
接触斑点是靠受载区域的啮合面涂层被磨掉来显示的,观察和记录随着载荷增加短期转动后的斑点。典型载荷递增最为5%,25%,50%,75%和100%用所得到的接触斑点进行比较,以保证在规定工作条件下,观察到轮齿逐渐发展的接触面积达到设计的接触面大小。
A4测试器具和材料
a) 清洗剂
b) 印痕的涂料
c)——红丹;
——专用涂料;
——基础颜料和油的混合物;
——普鲁士蓝软膏;
——染料渗透显示剂,喷雾器包装的白色粉剂,作为裂纹探伤检测渗秀显示剂套件之一(有销售);
——划线用蓝油。
c)记录手段:
——照相;
——和轮齿一样大小的透明胶带和白纸;
——画草图。
d)标定用量具:
——精密垫片或塞尺;
——千分表。
A5静态方法
A5.1测试
A5.1.1轴线的校正
当没有现成的齿轮箱体可用或齿轮在车间测试,以便以后在现场装配,车间使用试验台架和转动夹具把齿轮定位在正确的相互位置上。必须保证齿轮轴线在同一平面上并且相互平行,即使0.00010rad微小的轴线对准误差,对测试结果的再现性将产生有害影响。典型的测试程序,是把一个精密直尺横置于齿轮轴上,将精密块垫于直径较小的轴和直尺之间,以补偿轴半径之差。把精密的水平仪放在精密直尺的上面,然后调速齿轮轴的高度,直至精密直尺水平为止。在每对支承轴颈中间重复这个操作程序,用精密测量来检测支撑所测齿轮的两轴之间的中心距和轴线平行度。在作接触试验的车间常能找到带易调整支承座的转动夹具(啮合台架)。
如果在未装配的齿轮箱内做接触试验时,则必须先保证齿轮箱以尽量高的精度放置水平,以避免齿轮轴线的不对准,齿轮轴线偏移使接触斑点测试结果受到影响,其影响的程度与在转动夹具内测试是一样的。
当装配后齿轮箱重新做接触测试,其接触斑点如果和调好水平而未装配齿轮箱的测试结果有差别,这反映出安装时由于箱体变形而引起齿轮轴线产生了歪斜。
A5.1.2 测试程序
将准备测试的齿轮用清洗剂彻底清洗,清除任何污染和残油。然后将小齿轮的三个或更多轮齿上涂一层薄的印痕涂料,使用硬毛刷操作,可以将普通25mm宽度油漆刷子的硬毛修剪成大约10mm长度,做成一把合适刷子。涂层要薄而均匀,没有必要除掉所有的毛刷痕迹,因为测试时这些痕迹会被抹平,涂层厚度应该在5~15μm之间(见A5.2标定)。
小齿轮的轮齿涂完后应盖起来,以免过于溅散,并在大齿轮的和跟小齿轮涂了涂料的齿啮合的轮齿上喷一层薄薄的显像液膜。喷显像液是为了消除齿面反光,以便观察接触斑点的试验结果,而不要制作一层会影响接触斑点真实性的厚膜。
完成涂料涂刷后,操作者转动小齿轮,使其涂有涂料的轮齿和大齿轮相啮合,由助手在大齿轮上施加一个足够反力矩以保证接触,然后把齿轮反转回到原来位置,在轮齿的背面做上记号,以便对接触斑点进行观察。这个操作程序至少要在大齿轮三个等距离的位置上重复地做,以显示由于摆动或其他周期性误差所产生接触斑点的变异。
A5.1.3 记录结果
得到的接触斑点要用照相、画草图或透明胶带记录下来。一步成像照相和透明胶带纸是最常用的方法。使用胶带时把透明胶带小心压在接触区域上,然后再小心地把它撕取下来,贴在白纸上,这样接触斑点就被保存在胶带和白纸之间。接触斑点还可用黑白或彩色的静电复印来复制。胶带上应编号以指明使用了哪一个轮齿,同时在接触斑点上注明方向,齿的一哪一侧齿面,哪是齿顶,哪是齿根。
接触斑点的记录纸带可随现场装配的齿轮备件一起提供。与现场装配后的测试接触斑点作比较,验证装配是否正确。
A5.2标定
为了使测试结果有意义和可再现性,印痕涂料层的厚度必须控制且前后一致。
印痕涂料层厚度可以很容易地通过以下任意一种技术测定。
A5.2.1 作为接触试验的一部分,小心地抬起小齿轮轴的一端轴承,其抬高量应足以使小齿轮轴倾斜面0.00010rad,记录下接触斑点,并使轴承在正常(水平)位置时在同一轮齿上重复试验,涂层厚度由接触斑点的飘移量和角度为100mm,则涂层厚度应为0.010mm。
A5.2.2 另一个类似的考证操作员技术的方法是,用一块标准平板和精密直尺,在直尺的边上涂以印痕涂料,然后将直尺一端落在平板上,另一端放在平板上已知厚度的垫片上,则涂层厚度等于垫片厚度乘以接触斑点长度和直尺长度的比值。
A5.2.3应该进行标定试验并用为测试试验记录的一部分,印痕涂层厚度取决于操作者的技巧和技术,如果是一个正规操作接触斑点的操作人员,则不必对其每一次试验的技术进行重新标定。可随时使用以上标定方法标定涂层厚度并记录其结果作为评判试验或审查用。
A6 动态方法
A6.1试验程序
每次试验前,都要把待测试的轮齿用清洗液彻底洗净,以除去任何污染和残油,将小齿轮和大齿轮至少三个以上的轮齿喷上划线用蓝油,产生的膜应光滑和薄。千万不能造成过厚的膜,所以,每次做完试验,应彻底用清洗液洗净任何残留在轮齿上的蓝油、污垢或油。
当轮齿被涂层后,给齿轮副一个载荷增量作短时间运行,然后停止,将其接触斑点记录下来,彻底清洗干净轮齿后在下一个载荷增量下重复运行以上程序。整个操作过程应至少在三个不同载荷上重复进行。
A6.2记录结果
接触斑点的结果应照相或画草图加以记录。
附录B
(提示的附录)
文献目录
1) GB/T 1357-1987 渐开线圆柱齿轮模数
2) GB/T1800.1-1997极限与配合 基础 第1部分:词汇
3) GB/T2821-1992 齿轮几何要素代号
4) GB/T3374-1992 齿轮基本术语
5) GB/T3480-1997 渐开线圆柱齿轮承载能力计算方法
6) GB/Z18620.1-2002 圆柱齿轮 检验实施规范 第1部分:轮齿同侧齿轮的检验
7) GB/Z18620.2-2002圆柱齿轮 检验实施规范 第2部分:径向综合偏差、径向跳动、齿厚和侧隙的检验
8) GB/Z1860.3-2002 圆柱齿轮 检验实施规范 第3部分:齿轮坯、轴中心距和轴线平行度
9) ISO/TR13989-1:2000齿轮 圆柱齿轮、圆锥齿轮和次双曲面齿轮胶合承载能力的计算方法 第1部分:闪温法
10) ISO/RT13989-2:2000 齿轮 圆柱齿轮、圆锥齿轮和准双曲面齿轮胶合承载能力的计算方法 第2部分:积分温度法
11) ANSI/AGMA 2000-A88齿轮分级和检测手册 未安装的直齿轮和斜齿轮的公差和测量方法(1992修订版附录D)
12) Beyer,Eckolt,Hillmann,Wittekopf,用扫描电子显微镜和触针式测量表面仪器研究轮齿齿面PTB报告PTB-F-2(1987年11月)