圆柱齿轮 检验实施规范 径向综合偏差、径向跳动、齿厚和侧隙的检验
1 范围
本指导性技术文件是渐开线圆柱齿轮的径向综合偏差、径向跳动、齿厚和侧隙的检验实施规范,即涉及双面接触的检验、实施规范。
本文件提供了齿轮检验方法和测量结果的分析,补充了GB/T 10095.2,其大部分所用的名词,已在GB/T 10095.2中给出了定义。
附录A提供了齿轮啮合时选择齿厚公差和最小侧隙的方法,包括最小侧隙的建议数值。
2 引有标准
下列标准所包含的条文,通过在本指导性技术文件中引用而构成为本指导性技术文件的条文。本指导性技术文件出版时,所示版本均为有效。所有标准都会被修订,使用本指导性技术文件的各方应探讨使用下列标准最新版本的可能性:
GB/T 1356-2001 通用机械和重型机械用圆柱齿轮 标准基本齿条齿廓(idt ISO 53:1998)
GB/T 1357-1987 渐开线圆柱齿轮模数(neq ISO 54:1977)
GB/T 10095.1-2001 渐开线圆柱齿轮 精度 第1部分:轮齿同侧齿面偏差的定义和允许值(idt ISO 1328.1:1997)
GB/T 10095.2-2001 渐开线圆柱齿轮 精度 第2部分:径向综合偏差的定义和允许值(idt ISO 1328.2:1997)
GB/Z 18620.1-2002 圆柱齿轮 检验实施规范 第1部分:轮齿同侧齿面的检验(idt ISO/TR 10064-1:1992)
GB/Z 18620.3-2002 圆柱齿轮 检验实施规范 第3部分:齿轮坯、轴中心距和轴线平行度(idt ISO/TR 10064-3:1996)
3 符号、相亲项目和定义
3.1小写字母符号
a |
中心距 |
mm |
b |
齿宽 |
mm |
d |
分度圆直径 |
mm |
db |
基圆直径 |
mm |
da |
顶圆直径 |
mm |
dw |
节圆直径 |
mm |
fe |
偏心量 |
mm |
fi |
一齿径向综合偏差 |
μm |
ha |
齿顶高 |
mm |
hc |
分度圆弦齿高 |
mm |
mn |
法向模数 |
mm |
sn |
法向齿厚 |
mm |
snactual |
“实际齿厚” |
mm |
snc |
法向弦齿厚 |
mm |
sfunc |
“功能齿厚” |
mm |
x |
齿廓变位系数 |
- |
z |
齿数 |
- |
3.2 大写字母符号
DM |
测量用的球(圆柱)的直径 |
mm |
DMthe |
测量用的球(圆柱)的理论直径 |
mm |
Esni |
齿厚允许的下偏差 |
mm |
Esns |
齿厚允许的上偏差 |
mm |
Fi″ |
径向综合总偏差 |
μm |
Fr |
径向跳动 |
μm |
Fr″ |
综合测试得到的径向跳动 |
μm |
Md |
跨球(圆柱)尺寸 |
mm |
Wk |
公法线长度 |
mm |
Wkactual |
实际公法线长度 |
mm |
Wkthe |
理论公法线长度 |
mm |
3.3 希腊字母符号
aMt |
端面压力角 |
º |
an |
法向压力角 |
º |
β |
螺旋角 |
º |
δ |
棱柱(砧)半角 |
º |
εβ |
纵向重合度 |
- |
εβest |
纵向重合度(检测时) |
- |
η |
齿槽半角 |
º |
Ψ |
齿厚半角 |
º |
3.4 下角标志符号
0 |
工具 |
|
1 |
小齿轮 |
|
2 |
大齿轮 |
|
3 |
测量齿轮 |
|
b |
基础 |
|
t |
端面 |
|
w |
工作 |
|
y |
任意(给定)直径 |
|
3.5定义
3.5.1 关于综合偏差的含义
一个部件的“基准轴线”是借助于基准面来定义的,在多数情况下,内孔的轴线可通知相匹配的工作芯轴的轴线来代表(见GB/Z 18620.3)。
在径向综合偏差中“轮齿的几何轴线”是指该思轴线当用于测量时,在齿轮旋转一整圈后将获得最小的均方根综合总偏差。
3.5.2 关于齿厚的定义
在分度圆柱上法向平面的“公称齿厚sn”是指齿厚理论值,该齿轮与具有理论齿厚的相配齿轮在基本中心距之下无侧隙啮合。公称齿厚可用下列公式计算。
对外齿轮
s
n=m
n(

+2tana
nx)……………………(1)
对内齿轮
s
n=m
n(

-2tana
nx)……………………(2)
对斜齿轮,sn值应在法向平面内测量。
齿厚的“最大和最小极限” sns和sni是指齿厚的两个极端的允许尺寸,齿厚的实际尺寸应该位于这两个极端尺寸之间(含极端尺寸),见图1。
图1 公法线长度和齿厚的允许偏差
齿厚上偏差和下偏差(Esns和Esni)统称齿厚的极限偏差。见式3、式4和图1。
Esns=Sns-Sn……………………(3)
Esni=Sni- Sn……………………(4)
“齿厚公差”Tsn是指齿厚上偏差与下偏差之差
Tsn= Esns-Esni……………………(5)
齿厚的设计值的确定,要考虑齿轮的几何形状、轮齿的强度、安装和侧隙等工程因素,在给定的应用条件下,如何确定设计齿厚的方法,不属于本指导性技术文件的范围之内。
“实际齿厚”Snactual是指通过测量确定的齿厚。
“功能齿厚”Sfunc是指用经标定的测量齿轮在径向综合(双面)啮合测试所得到的最大齿厚值。
这种测量包含了齿廓、螺旋线、齿距等要素偏差的综合影响,类似于最大实体状态的概念,见6.5,它绝不可超过设计齿厚。
齿轮的“实效齿厚”是指测量所得的齿厚加上轮齿各要素偏差及安装所产生的纵使影响的量,类似于“功能齿厚的”含义。
这是最终包容条件,它包含了所有的影响因素,这些影响因素最大实体状态时,必须予以考虑。
相配齿轮的要素偏差,在啮合的不同角度位置时,可能产生叠加的影响,也可能产生相互抵消的影响,想把个别的轮齿要素偏差从“实效齿厚”中区分出来,是不可能做到的。
3.5.3 关于侧隙的定义
“侧隙”是两个相配齿轮的工作齿面相接触时,在两个非工作齿面之间所形成的间隙,如图2所示。
注:图2是按最紧中心距位置绘制的,如中心距有所增加,则侧隙也将增大,最大实效齿厚(最小侧隙)由于轮齿各要素偏差的综合影响以及安装的影响,与测量齿厚的量是不相同的,类似于功能齿厚,这是最终包容条件,它包含了所有影响因素,这些影响因素在确定最大实体状态时,必须予以考虑。
通常,在稳定的工作状态下的侧隙(工作侧隙)与齿轮在静态条件下安装于箱体内所测得的侧隙(装配侧隙)是不相同的(小于它)。
图2 端平面上齿厚
“圆周侧隙”jwt(图3)是当固定两相啮合齿轮中的一个,另一个齿轮所能转过的节圆弧长的最大值。
“法向侧隙”jbn(图3)是当两个齿轮的工作齿面互相接触时,其非工作齿面之间的最短距离,它与圆周侧隙jwt的关系,按下面的公式表示:
jbn=jwtcoxawtcosβb……………………(6)
“径向侧隙”jr(图3)将两个相配齿轮的中心距缩小,直到左侧和右侧齿面都接触时,这个缩小的量为径向侧隙:
j
r=

……………………(7)
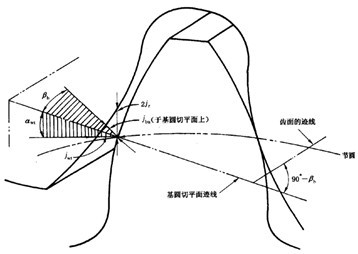
图3 圆周侧隙j
wt、法向侧隙j
bn与径向侧隙j
r之间的关系
“最小侧隙”jwtmin是节圆上的最小圆周侧隙,即当具有最大允许实效齿厚的轮齿与也具有最大允许实效齿厚相配轮齿相啮合时,在静态条件下在最紧允许中心距时的圆周侧隙(图2)。
所谓最紧中心距,对外齿轮来说是指最小的工作中心距,而对内齿轮来说是指最大的工作中心距。
“最大侧隙”jwtmax是节圆上的最大圆周侧隙,即当具有最小允许实效齿厚的轮齿与也具有最小允许实效齿厚相配轮齿相啮合时,在静态条件下在最大允许中心距时的圆周侧隙(图2)。
4 径向综合偏差的测量
4.1 测量原理
径向综合偏差检测时,所用的装置上能安放一对齿轮,其中一个齿轮装在固定的轴上,另一个齿轮则装在带出滑道的轴上,该滑道带一弹簧装置,从面使两个齿轮在径向能紧密地啮合(见图4)。在旋转过程中测量出中心距的变动量,如果需要的话,可将中心距变动曲线图展现出来。
对于大多数检测目的,要用一个测量齿轮对产品齿轮作此项检测。测量齿轮需要做得很精确,以达到其对径向综合偏差的影响可忽略不计,在此情况下,当一个产品齿轮旋转一整周后,就能展现出一个可接受的记录来。
被检测齿轮径向综合总偏差

等于齿轮旋转一整周中最大的中心距变动量,它可以从记录下来的线图上确定。一齿径向综合偏差

等于齿轮转过一个齿距角时其中心距的变动最(见图5)。
GB/T 10095.2中所给出的公差值,适用于与一个测量齿轮所进行的此项测量。
图4 测量径向综合偏差的原理
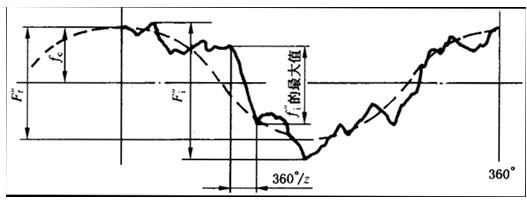
图5 径向综合偏差曲线图
必须十分重视测量齿轮的精度和设计,特别是它与产品齿轮啮合的压力角,会影响测量的结果,测量齿轮应该有足够的啮合深度,使其能与产品齿轮的整个有效齿廓相接触,但不应与非有效部分或根部相接触,避免产生这种接触的办法是将测量齿轮的齿厚增厚到足以补偿产品齿轮的侧隙允差。
当用此方法对精密齿轮作质量评级时,对所用的测量齿轮的精度和测量步骤,应由采购方和供方协商一致。
对直齿圆柱齿轮,所规定的公差值可以用来确定精度等级,但当用于斜齿轮时,其测量齿轮的齿宽应该设计的使其与产品齿轮的εβtest等于或小于0.5。测量齿轮的设计应由采购方和供方协商一致,纵向重合度εβtest可影响斜齿轮的径向综合测量的结果。齿廓偏差的影响,对直齿轮而言,将是很明显的,但对斜齿轮而言,由于多个齿和对角接触线的存在,将会被陷蔽起来。
齿轮旋转一整周记录下的,曲线图,接近于正弦形状(幅值为fe),表示齿轮的偏心量fe。图5中表示出如何在此曲线图上绘制出正弦曲线来。齿轮的偏心量是指轮齿的几何轴线与基准轴线(即孔或轴)间的偏移。
4.2 径向综合偏差数据的应用
径向综合偏差包含了右侧和左侧齿面综合偏差的成分,故而,想确定同侧齿面的单项偏差是不可能的。径向综合偏差的测量可迅速提供关于生产用的机床、工具或产品齿轮装夹而导致的质量缺陷方面的信息,此法主要用于大批量生产的齿轮以及小模数齿轮的检测。
每转过一个齿距所发生的一齿综合偏差,有助于揭示齿廓偏差(常为齿廓倾斜偏差)。一个很大的个别的一齿综合偏差,表示有一个大的齿距偏差或受损伤的轮齿(见图6)。
对产品齿轮的装夹和检测方法作适当的校准后,此测量过程还可用来确定产品齿轮最小侧隙啮合的中心距,见GB/Z 18620.3关于轴中心距和轴线平行度的推荐意见,另外,这个步骤对检需要以最小侧隙运行的齿轮也是有用的,因为功能齿厚的范围可能很容易地从径向综合偏听偏信差上得到。
为了确定精度等级:
a)对直齿轮,产品齿轮要用一个测量齿轮进行检测,该测量齿轮能够与有效齿廓100%的接触。能见GB/T 10095.2-2001中5.5,在GB/T 10095.2中给出的径向综合总偏差及一齿径向综合偏差的公差值用以确定直齿轮精度等级。必须强调,因为峡谷两侧齿面的同时起作用,双面啮合检测得到的精度等级不能直接与用单项要素检测所得到的精度等级相关联。
b)对斜齿轮,虽然GB/T 10095.2中的公差是对直齿轮而言的,但如时采购方和供方都同意,也可用于评定斜齿轮,此时与齿轮相啮合时的重合度εβtest应符合4.1要求。
径向跳动
这是产品齿轮在一转中中心距的波动,在线图中表现在缓慢增加和减少的曲线(即齿轮的传动比变动) |
齿距偏差
在线图上显示出两个相邻齿之间记录笔以变化的幅度出现突然的和不规则的偏移。 |
齿廓偏差
在曲线上较小的波度表示齿廓与理论渐开线齿廓间的偏差,每一个波形相应于一个齿的接触周期。 |
压力角偏差(齿廓倾斜偏差)
它们在曲线图上表现为有规则的间隔和尖形的垂直偏移,而每一个偏移相应于一个齿的接触周期 |
图6 径向综合偏差的解释
5 径向跳动的测量、偏心量的确定
5.1 测量原理
轮齿的径向跳动Fr,是指一个适当的测头(球、砧、圆柱或棱柱体)在齿轮旋转时逐齿地放置于每个齿槽中,相对于齿轮的基准轴线的最大和最小径向位置之差(见图7)。
如果用球、圆柱或砧在齿槽中与齿的两侧都接触,则可应用GB/T 10095.2-2001中附录B所列的公差表。在有些情况下,要用一个骑架来与齿的两侧接触,公差表不是想要用于这种情况。
球的直径应选择得其能接触到齿槽的中间部位,并应置于齿宽的中央(见6.3球直径的计算)。
5.2 测量径向跳动用砧的尺寸
砧的尺寸应选择得使其在齿槽中大致在分度圆的位置接触齿面,棱柱的半角δyt可以用下面的近似方法来确定,此处δyt、ayt和ηyt为在测量圆上接触的各角(见图8)。
砧应在直径为dy的测量圆处于齿宽的中央与齿面接触。
图7 测量径向 跳动的原理

……………………(8)
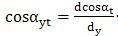
……………………(9)
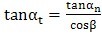
……………………(10)
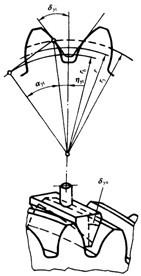
图8 测量径向跳动用砧的尺寸
dy=d+2mnx……………………(11)
η
yt=
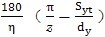
……………………(12)
对外齿轮: 对内齿轮:
s
t=
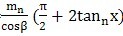
s
t=
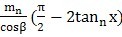
……………………(13)
s
yt=d
y(
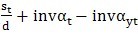
) s
yt=d
y(
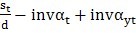
)…………………(14)
tabβ
y=

……………………(15)

……………………(16)
5.3测量径向跳动
此测量方法简单易行,允许有很宽广的范围去选择测量设备和自动化程度,下面就使用的几种方法作简要的描述。
5.3.1 测量时产品齿轮间歇地转动定位。一种简单的方法即用手工对齿轮作间歇性的转动,此法常用于小型齿轮。被置于逐个齿槽中的测头,须调整得与测量的直线相一致,然后记录下逐个齿槽相对于一基准零位的径向位置偏听偏信差。当转动定位和成直线受转位装置的影响时,测量仪器必须有足够的侧向移动以抵消由于齿距和螺旋线偏差造成对准直线的影响。侧向移动的自由度是为保证测量头和齿两侧相接触所必须的。
多坐标数字控制(CNC)测量机也可用于这种测量方法,CNC的测量结果将受到测头接触点处螺旋角的影响。
5.3.2 测量时产品齿轮作连续旋转。砧形测头与齿槽两侧相接触,在齿轮旋转时也跟着一起移动,经历一个预先设定的弧长,径向偏差可以在弧长的量高点测量,也可以在沿弧长移动过程中在其他设定的点上测量。这是测量大型齿轮径向跳动的一种实用的方法。这种测量可以在测量机或展成切齿机床上进行,不过应注意在测量时,必须保证齿轮的基准轴线与机器的旋转轴线为同心,而且其弧长应足够以显示其最大偏差。
5.3.4 用坐标测量机测量。当应用坐标测量机时,径向跳动与齿距可同时进行测量,下面介绍两个方法。
a)两个齿面接触的测量法。将具有适当直径的球体测头在齿槽间移动,直到实现两个齿面接触时为止,按照所用装置的不同及齿轮参数,测量可以用一旋转工作台进行,也可以不同旋转工作台,可借助于一个平行轴测头,也可以用星形测头。当采用星形测头时,由于接触条件的需要,必须用8星形测头,见图9。
a) 用旋转工作台(4轴)与平行轴测头作径向跳动测试
b) 不用旋转工作台(3轴)与8星形测头作径向跳动测试
图9 用坐标测量机测量径向跳动
注:如果应用一个标准直径的测头,每个齿槽的径向跳动偏差需根据图纸给出的直径重新计算。考
虑齿槽中相同的齿距偏差,记录下来的径向跳动偏听偏信差却与所用的球体直径有关。由于在接触点处齿廓角的变动,一个较小的测头比一个大的测头具有更高的灵敏度,并得到较大的偏差。
b)一个齿面接触的测量法。将一个具有较小直径的测头在齿槽内移动,左侧和右侧齿面均在测量圆处测量。用此种测量法,计算出球体的位置,其直径如6.3中所给定的。按所用装置及齿轮的参数,此测量可以在旋转工作台或不用旋转工作台进行,也可用一个平行轴测头或一个8星形测头来进行。
5.4 测量结果的评价
5.4.1 径向跳动Fr。径向跳动Fr是以齿轮轴线为基准,其值等于径向偏差的最大和最小值的代数差,这里径向偏差是按5.3测得的。它大体上是由两倍偏心量fe组成,另外再添加上齿轮的齿距和齿廓偏差的影响(见图10)。
图10 一个16齿的齿轮的径向跳动曲线图
5.4.2 偏心量fe,图10表示测量径向跳动的曲线图。曲线的正弦成分右用手工粗略地画出来或可用最小二乘法计算出来,它表示(在测量的平面上)轮齿相对于基准轴线的偏心量为fe(见图10)。
5.5 测量径向跳动的用处
对于需要在最小侧隙下运行的齿轮及用于测量径向综合偏差的测量齿轮来说,控制齿轮的径向跳动是十分重要的。
当齿轮的径向综合偏差被测量时,并不需要上面所述的那样测量径向跳动。很明显,单侧齿面偏差,例如齿距或齿廓偏差是不可能用测量径向跳动的值来获得的。例如,有两个精度等级非常不同的齿轮(按GB/T 10095.1衡量),可能有相同的径向跳动值,这是因为一个齿轮相配对齿轮,只是在右侧或左侧齿面上接触,而径向跳动值则受右侧和左侧面齿面同时接触的影响,两侧齿面的偏差对于径向跳动值可能有相互抵消的影响,测量径向跳动所能获得的信息的程度,主要取决于切削过程中的知识和加工机床的特性。
然而,用某一种方法生产出来的第一批齿轮,为了掌握它是否符合所规定的精度等级需进行详细检测,以后,按此法接下去生产出来的齿轮有什么变化,就可用测量径向综合偏差来发现,而不必再重复进行详细检测。
5.6 径向跳动和齿距偏差之间的关系
当一个别处都很精确的齿轮却具有一个偏心的轴孔,其偏心量为fe如图11所示。它如围绕其孔的轴线旋转,则产生的径向跳动Fr大约等于2fe,偏心量导致沿齿轮圆周单个齿距偏差的最大值为fptmax=2fe[sin(180°/z )]/cosαyMt,其累积的齿距偏差也具有正弦的形门面,其最大值为Fpmax=2fe/cosαyMt,如图11所示。最大尺距累积偏差和“径向跳动”之间的角度约为90°在左侧齿面,此角度的近似值为90°-αt,由偏心造成的径向跳动,产生侧隙变化,由于齿距偏差而会产生加速度和减速度。
图11 一个偏心齿轮的径向跳动和齿距偏差
不过,当测量出的径向跳动很小或没和径向跳动时,这种情况下不能说明不存在齿距偏差。切齿加工时,如果采用单齿分度,很可能切出如图12所示的齿轮,此齿轮的所有齿槽均相等,从而没有径向跳动,但却存在着很明显的齿距和齿距累积偏差。图13用曲线图表示此情况,图14表示一个实际齿轮,它只有很小的径向跳动而却有相当大的齿距累积偏差。
这种情况发生于双面加工法,例如成形磨削或展成磨削(这两种方法都在磨削齿槽时采用单齿分度),磨削时齿轮的轴孔与机床工作台的轴是同心的,而分度机构产生一个正弦形齿距累积偏差,这个齿距累积偏差的根源可能是由于机床分度蜗轮的偏心造成的。
为了揭示齿轮的这种情况,可采用一种改进和径向跳动检测法,如图15中所示应用一个“骑架”作为测头,这种检测法能发现齿距偏差的理由,是因为在这里齿距偏差导致齿厚偏差。故当“骑架”接触两侧齿面检测时指示出径向位置的变化。
图12 齿轮无径向跳动,但有明显的齿距和齿距累积偏差(所有的齿槽宽度相等)
图13 齿轮具有齿距和齿距累积偏差无径向跳动
图14 实际齿轮只有很小的径向跳动,但有明显的齿距累积偏差
图15 当所有齿槽宽度相等,而存在齿距偏差时,用骑架进行径向跳动测量
6 齿厚、公法线长度和跨球(圆柱)尺寸的测量
测得的齿厚常被用来评价整个齿的尺寸或一个给定齿轮的全部齿尺寸。它可根据测头接触点间或两条很短的接触线间距离的少数几次测量来计值,这些接触点的状诚和位置是由测量法的类型(公法线、球、圆柱或轮齿卡尺)以及单个要素偏差的影响来确定的。习惯上常假设整个齿轮依靠一次或两次测量来表明其特性。
控制相配齿轮的齿厚是十分重要的,以保证它们在规定的侧隙下运行。有些情况下,由于齿顶高的变位,要在分度圆直径d处测量齿厚不太容易,故而用一个计算式给出在任何直径dy处齿厚s,见图16,推荐选取dy=d+2mnx。
图16 齿顶高和弦齿厚
6.1齿厚的测量
用齿厚游标卡尺测齿厚
syn=sytcosβy……………………(17)
s
ync=d
ynsin(

)……………………(18)
βy见5.2。
d
yn=d
y-d+

……………………(19)
sniβb=sinβcosαn……………………(20)
对外齿轮,syt按式14求得。
h
yc=h
y+
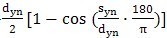
……………………(21)
这里: h
y=

……………………(22)
齿厚游标卡尺不能用于测量内齿轮。
侧隙的允许偏差没有包括在sync齿厚的公称值内,应从公称值减去上上偏差Esyns和下Esyni。
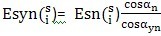
……………………(23)
式中Esns和Esni见7.2。

……………………(24)
式中ayt见5.2,产际的齿厚应该是
(sync+Esyni)≤Syncactuan≤(Sync+Esyns)……………………(25)
Esyni和Esyns应有正负号。
用齿厚游标卡尺测齿的弦齿厚的优点,是可以用一个手持的量具进行测量,携带方便和使用简便是其主要优点,见图17。
图17 用齿厚游标卡尺测量弦齿厚
测量弦齿厚也有其局限性,由于齿厚卡尺寸的两个测量腿与齿面只是在其顶尖角处接触而不是在其平面接触,故测量必须要由有经验的操作者进行。另一点是,由于齿顶圆柱面的精确度和同心度的不确定性,以及测量标尺分辨率很差,使测量不甚可靠。如果可能的话,应采用更可靠的公法线长度、圆柱销或球测量法来代替此法。
6.2 公法线长度的测量
公法线WK的长度是在基圆柱切平面(公法线平面)上跨K个齿(对外齿轮)或k个齿槽(对内齿轮)在接触到一个齿的右齿面和另一个齿的左齿面的两个平行平面之间测得的距离。这个距离在两个齿廓间沿所有法线都是常数(见图18和图19)。
图18 斜齿轮公法线测量
图19 在基圆柱切平面上的公法线测量的极限尺寸
在外齿轮的实际测量时,按规定作出的两内侧平行平面就是度量表面,以测量它们之间的距离。
度量表面间所跨的齿数k应这样来选择,即其接触线大体上位于齿高的中间,可按下面方法来计算(圆整到最近的整数):
k+
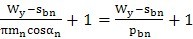
……………………(26)
式中:
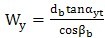
……………………(27)
式中βb见式20。

……………………(28)
式中αytt αt见式9和式10。
公法线长度尺寸由下列公式给出:
W
k=

……………………(29)
或Wk=(k-1)pbn+sbn……………………(30)
测隙的允许没有包括在Wk的公称值内,应从公称值减去公法线长度的上Ebns和下偏差Ebni的值(见图1),而对内齿轮则应增大。

……………………(31)
a) 对外齿轮:
Wk+Ebni≤Wkactual≤Wk+Ebns……………………(32)
b) 对内齿轮:
Wk-Ebni≤Wkactual≤Wk-Ebns……………………(33)
Ebni和Ebns应有适当的正负号。
公法线测量对内斜齿轮是不适当的。另外对斜齿轮而言,公法线测量受齿轮齿宽的限制,只有满足下式条件时才可能:
b>W
ksinβ
b+b
Mcosβ
b,这里b
M=5或b
M=

……………………(34)
或使
b>1.015Wksinβb……………………(35)
如果有齿廓或螺旋线修开,公法线测量应该在未经修形的齿面部分进行。对斜齿鼓形齿,斜齿公法线中的公称齿厚应予以修正。对直齿鼓形齿,应在鼓形的顶点测量。
6.3 用测定跨球(圆柱)尺寸来控制齿厚
当斜齿轮的齿宽太窄,不允许作公法线测量时,可以用间接地检测齿厚的方法,即把两个球或圆柱(销子)置于尽可能在直径上相对的齿槽内(图20),然后测量跨球(圆柱)尺寸。
图20 直齿轮的跨球(圆柱)尺寸Md
6.3.1 球或圆柱的尺寸DM
a)对外齿轮:
D
Mthe=
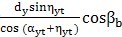
……………………(36)
b)对内齿轮:
D
Mthe=
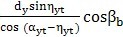
……………………(37)
关于αyt,dyηyt和βb见式9,11,12和20。
DM应根据优先数系R40选择较计算值大一点的直径,或选自可提供给齿轮制造商的标准圆柱销尺寸表,例如表1。参见图21。
表1 标准圆柱销的直径 mm
2 |
2.25 |
2.5 |
2.75 |
3 |
3.25 |
3.5 |
3.75 |
4 |
4.25 |
4.5 |
5 |
5.25 |
5.5 |
6 |
6.5 |
7 |
7.5 |
8 |
9 |
10 |
10.5 |
11 |
12 |
14 |
15 |
16 |
18 |
20 |
22 |
25 |
28 |
30 |
35 |
40 |
45 |
50 |
- |
- |
图21 球的尺寸
6.3.2 跨球(圆柱)尺寸Md
a)偶数齿的外齿轮:
M
d=
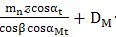
……………………(38)
b)奇数齿的外齿轮:
M
d=

……………………(39)
式中: invα
Mt= invα
t+
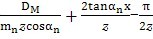
……………………(40)
c) 偶数齿的内齿轮:
M
d=
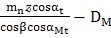
……………………(41)
d) 奇数齿的内齿轮:
M
d=

……………………(42)
式中:
invα
Mt= invα
t-
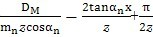
……………………(43)
6.3.3 计入侧隙允许偏差的跨球(圆柱)尺寸测量
Md的公称值中不包括侧隙的允许偏差,应从公称值减去上偏差Eyns和下偏差Eyns,Eyns和Eyni由下列方程式转换(见7.2)。
偶数齿时:

……………………(44)
奇数齿时:

……………………(45)
因而,跨球(圆柱)尺寸应为:
a)对外齿轮:
Md+Eyni≤Mdactual≤Md+Eyns……………………(46)
b对内齿轮:
Md-Eyns≤Mdactual≤Md -Eyni……………………(47)
Eyni和Eyns应有正负号。
对于内斜齿轮,只能用球测量。常用球形测头内径千分表来测量,测得端平面上两个置于直径两端的齿槽中球之间的最小尺寸,这是真实的尺寸,当测量奇数齿的斜齿轮时,需要考虑用适当的方法使球定位于端平面上。
6.4 用径向综合检测作齿厚测量
用径向综合检测测量齿厚有其优点,测得的是功充齿厚,包括齿的所有偏差的影响。如果工件的尺寸允许,所需工装也适用,则径向综合检测,即半径方向的测量,是检测齿厚的最好的方法。径向综合检测在一次操作中对产品齿轮的每一个齿都进行了检测,比用其他方法进行多次测量要快得多。
然而,这个方法仅适用于中型和小型齿轮,因为中心距大于500mm的测试仪器是很稀少的,在特定情况下,可以在切削机床上进行测度。
应特别注意被测齿轮的安装面,以保证所进行的测试,能代表齿轮实际运行时的安装情况。对内齿轮需要用专用的仪器或附件。
测量仪器必须经过仔细标定,特别是对小模数和高精度的齿轮。
6.5 径向综合啮合测试的计算
下面的方法适用于外齿轮。
必须校核测量齿轮的尺寸,以使其与产品齿轮作正确的啮合,并保证其接触能达到齿顶附近及真实的渐开线的直径处而不产生干涉。
测量齿轮通常在其上标记着检测半径,所谓检测半径,是指在此半径处测量齿轮与标准齿轮相啮合,该标准齿轮在分度圆直径d2处的齿厚为:
s
t2=

……………………(48)
对非标准尺寸的直齿轮,常常需要特殊的测量齿轮。斜齿轮通常需要特殊的测量齿轮。
测量齿轮应该做的非常精确,因为测量齿轮的任何偏差,将在检测结果中添加到产品齿轮的偏差上去。
6.5.1 最大检测半径
最大检测半径是以最大实效齿厚为基础计算的。计算方法中假设测量齿轮的误差是极小的,不会影响检测的结果。这就需要一个十分精确的测量齿轮,特别是在测量精密齿轮时。
如果两个齿轮是紧密相啮合,它们在工作节圆上齿厚之和等于在此圆上的齿距(圆弧上度量的),另外,两个齿轮的工作节圆直径与其齿数成正比。这些关系加上齿厚基本方程式就得联立方程式,从它们可得到工作端面压力角。
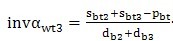
……………………(49)
式中:sbt2——产品齿轮的最大端面基圆齿厚,mm;
sbt3——测量齿轮的端面基圆齿厚,mm;
db2——产品齿轮的基圆直径,mm;
db3——测量齿轮的基圆直径,mm;
αwt3——紧密啮合时端面工作压力角,°
pbt——端面基圆齿距,mm。
αwt3也可用下式计算:
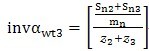
+invα
t……………………(50)
式中:

——产品齿轮在分度圆直径蓰的法向齿厚,mm;

——测量齿轮在分度圆直径处的法向齿厚, mm;

——产品齿轮的齿数;

——测量齿轮的齿数。
产品齿轮在分度圆上的最大齿厚的尺寸,等于公称齿厚减去齿厚上偏差。
所有的测量均在端平面上进行。
最大中心距值αmax(mm)可由下式计算
α
max=

……………………(51)
最大检测半径r2max是:
r2max=αmax-r3……………………(52)
式中:r3——测量齿轮检测半径,mm。
6.5.2 最小检测半径
图22表明一个典型的径向综合啮合检测的图,“最大齿轮迹线”表示一个齿轮,它有一个最大实效齿厚swtmax的齿,对于径向综合啮合测试或检测中心距的公差带,必须包括由径向综合总公差加上齿厚公差的全部偏差。两个组成部分都随产品齿轮的尺寸和精度不同而变化。
图22 径向综合啮合检测测量齿厚
在下面求αmin的公式中,用αwt3作为最小压力角是一个近似的方法,如时需要更为精确的结果,可用式49或工50和αmin重新计算,取得最后的数值。
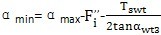
……………………(53)
式中:αmin——最小中心距;

——与测量齿轮啮合的工作节圆直径处的端面齿厚公差。
r
2min=

……………………(54)

……………………(55)
7 齿轮的公差和配合
7.1概述
装配如的齿是相匹配的产品。为了保证它们无障碍也运转,需要适当的侧隙配合。决定配合的齿轮副要素有(图23):
s1——小齿轮的齿厚;
s2——大齿轮的齿厚;
a——箱体的轴中心距。
图23 齿轮轮齿的配合
除了上述这些要素的尺寸外,齿轮的配合也受到齿轮的形状和位置偏差以及轴线平行度的影响。
小齿轮和大齿轮的齿厚(实际)尺寸和轴的中心距尺寸加上相应齿轮要素的偏差,确定定了齿轮轮齿的侧隙j,即在工作直径处非工作齿面间的间隙。
通常,最大侧隙并不影响传递运动的性能和平稳性,同时,实效齿厚偏听偏信差也不是在选择齿轮的精度等级时的主要考虑因素。在这些情况下,选择齿厚及其测量方法并非关键,可以用最方便的方法。在很多应用场合,允许用较宽的齿厚公差或工作侧隙,这样做不会影响齿轮的性能了承载能力,却可以获得较经济的制造成本。除非十分必要,不应该采用很紧的齿厚公差,因为这对于制造成本有很大的影响。当最大侧隙必须严格控制的情况下,对各影响因素必须仔细地研究,有关齿轮的精度等级、中心距公差和测量方法,必须仔细地予以规定。
很可能需要规定一个更为精密的精度等级,以便保持量大侧隙在要求的极限范围之内。
最小工作侧隙不应当成为零或负值。由于工作侧隙是由装配侧隙和工作状态确定的,它们包括挠度、安装误差、轴承的径向跳动、温度以及其他未知因素的影响,因而必须区别开:
——装配侧隙,和
——工作侧隙。
侧隙不是一个固定值,由于制造公差和工作状态等原因,它在不同的轮齿位置上是变动的。
本指导性技术文件只限于有关装配侧隙和齿厚。有关轴中心距和轴线平行度的测量,包含在GB/Z 18620.3中。
齿轮诸要素的形状和位置偏差,包含在GB/T10095.1和GB/T 1095.2中。
关于适当的检测方法方面的意见,已在第6章中提出,关于计算工作侧隙的导则,在附录A(标准的附录)中给出。
7.2 齿厚公差
轮齿的给定尺寸公差的影响,取决于装配。另处,尺寸的测量取决于所用的方法及轮齿的几何偏差,如在GB/T 10095.1和GB/Z 186020.1中所论述的。为了确定这些影响,计算应在端平面上进行,因为最终的齿轮传动运动和侧隙,常常是在圆周上测得的值。
齿厚与侧隙的给定值,是由设计人员按其使用情况选定的,在分度圆上垂直于齿线方向来规定和测量其值,可能是方便的。
7.2.1 齿厚上偏差Esns
齿厚上偏差取决于分度圆直径和允许差,其选择大体上与轮齿精度无关。
7.2.2 齿厚下偏差Esni
齿厚下偏差是综合了齿厚上偏差及齿厚公差所获得的,由于上、下偏差都使齿厚减薄,从齿厚上偏差中应减去公差值。
Esni=Esns-Tsn……………………(56)
Esni 和Esns应有正负号
注意:
Tsn=Tstcosβ……………………(57)
7.2.3 法向齿厚公差Tsn
法向齿厚公差的选择,基本上与轮齿的精度无关,它主要应由制造设备来控制。如果出于工作运行的原因必须控制最大侧隙时,就必须用附录A中所提供的方法进行计算。必须注意太小的齿厚公差对制造成本和保持轮齿的精度方面是不利的,因为它们在制造中不必要地限制了校正的可能性。
附录A
(标准的附录)
侧隙和齿厚公差
A1 目的
这个附录对选择齿轮的齿厚公差和最小侧隙提供一个合理的方法。一对相啮齿轮,利用最小侧隙、齿厚公差、中心距公差及轮齿的精度公差,还提供一个计算其最大期望侧隙的方法。本附录还包括推荐的最小侧隙值。
A2 侧隙
在一对装配好的齿轮副中,侧隙j是相啮齿轮齿间的间隙,它是在节圆上齿槽宽度超过相啮合的轮齿齿厚的量。侧隙可以在法向平面上或沿啮合线(见图A1)测量,但是它是在端平面上或啮合平面(基圆切平面)上计算和规定的。
图A1 用塞尺测最侧隙(法向平面)
单个齿轮并没有侧隙,它只有齿厚,相啮齿的侧隙是由一对齿轮运行时的中心距以及每个齿轮的实效齿厚所控制。
所有相啮的齿轮必定要有些侧隙。必须要保证非工作齿面不会相互接触,在一个已定的啮合中,侧隙在运行中由于受速度、温度、负载等变动而变化。在静态可测量的条件下,必须有足够的侧隙,以保证在带负载运行于最不利的工作条件下仍有足够的侧隙。
侧隙需要的量与齿轮的大小、精度、安装和应用情况有关。
A3最大齿厚
齿轮的最大齿厚是这样确定的,即假定齿轮在最小中心距时与一个理想的相配齿轮啮合,能存在所需的量小侧隙。齿厚偏差使最大齿厚从其最大值减小,从而增加了侧隙。
对于X=0的齿轮,理论齿厚或公称齿厚通常等于分度圆上的齿距的一半。除非有专门的规定,一个未装配的齿轮其实际最大齿厚常常比理论值要小,因为制造者常常以减小齿厚来实现侧隙。
A4 最小侧隙
最小侧隙jbmmin是当一个齿轮的齿以最大允许实效齿厚与一个也具有最大允许实效齿厚的相配齿在最紧的允许中心距相啮合时,在静态条件下存在的最小允许侧隙。这是设计者所提供的传统“允许侧隙”,又防备下列所述情况:
a) 箱体、轴和轴承的偏斜;
b) 由于箱体的偏差和轴承的间隙导致齿轮轴线的不对准;
c) 由于箱体的偏差和轴承的间隙导致齿轮轴线的歪斜;
d) 安装误差,例如轴的偏心;
e) 轴承径向跳动;
f) 温度影响(箱体与齿轮零件的温度差、中心距和材料差异所致);
g) 旋转零件的离心胀大;
h) 其他因素,例如由于润滑剂的允许污染以及非金属齿轮材料的溶胀。
如果上述因素能很好的控制,则量小侧隙值可能很小,每一个因素均可用分析其公差来进行估计,然后可计算出最小的要求量,在估计最小期望要求值时,也需要用判断和经验,因为在最坏情况时的公差,不大可能都叠加起来。
表A1列出了对工业传动装置推荐的最小侧隙,这传动装置是用黑色金属齿轮和黑色金属的箱体制造的,工作时节圆线速度小于15m/s,其箱体、轴和轴承都采用常用的商业制造公差。
表A1 对于中、大模数齿轮最小侧隙jbnmin的推荐数据
mn |
最小中心距ai |
50 |
100 |
200 |
400 |
800 |
1600 |
1.5 |
0.09 |
0.11 |
- |
- |
- |
- |
2 |
0.12 |
0.12 |
0.15 |
- |
- |
- |
3 |
0.12 |
0.14 |
0.17 |
0.24 |
- |
- |
5 |
- |
0.18 |
0.21 |
0.28 |
- |
- |
8 |
- |
0.24 |
0.27 |
0.34 |
0.47 |
- |
12 |
- |
- |
0.35 |
0.42 |
0.55 |
- |
18 |
- |
- |
- |
0.54 |
0.67 |
0.94 |
表A1中的数值,也可用公式A1进行计算:
j
bnmin=

……………………(A1)
注意:

必须是一个绝对值/
jbn=|(Esns1+Esns2)|cosαn……………………(A2)
如果Esns1和Esns2相等,则jbn=2Esnscosαn,小齿轮和大齿轮的切削深度和根部间隙相等,且重合度为最大。
A5齿厚测量中的规定
对于任何检测方法所规定的最大齿厚必须减小,以便确保径向跳动及其他切齿时变化对检测结果的影响,不致增加最大实效齿厚,规定的最小齿厚也必须减小,以便使所选择的齿厚公差能实现经济的齿轮制造,且不会被来源于精度等级的其他公差所耗尽。
A6 最大侧隙
一对齿轮副中的最大侧隙jbnmax,是齿厚公差、中心距变动和轮齿几何形状变异的影响之和。理论的最大侧隙发生于两个理想的齿轮按最小齿厚的规定制成,且在最松的允许中心距条件下啮合,最松的中心距对外齿轮是指最大的,对内齿轮是指最小的。
最大的理论侧隙也可发生于当两个齿轮都按最小实效齿厚swtmin制成,且运行于最松中心距条件下碰在一起时。在实践中,那种情况不大可能发生。
swtmin的值,计算方法如下:
s
wtmin=s
wt-E
sni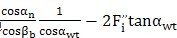
……………………(A3)
jwtmax= pwt - swtmin1- swtmin2-(αmax-αmin)2tanαwt……………………(A4)
式中:swt——在工作直径处的理论端面齿厚;
pwt——工作节圆的齿距。
在工作直径处侧隙的值,可以按下面方法转换成塞尺测得的侧隙jbn:
p
wt=

……………………(A5)
j
bn=j
wt 
……………………(A6)
j
bn= j
wn
……………………(A7)
最大期望侧隙是jbnmax及轮齿的单个要素和中心距变动的统计分布的函数。由于制造上的原因而造成轮齿的任何偏差将减速少最大期望侧隙,需要用经验和判断来估计一个合理的数值。
如果必须控制最大侧隙的话,应该对最大侧隙的每个要素作仔细的分析,然后选择一个精度等级,以求按需要去限制轮齿的偏差。
对于一个装配好的齿轮传动装置,特别是多级传动,如果用最大侧隙作为验收合格准则时,其最大合格值必须很小心的选择,以求总成的每个部分都能有合理的制造公差。
附录B
(提示的附录)
文献目录
1) GB/T 2821-1992 齿轮几何代号
2) GB/T 3374-1992 齿轮基本术语
3) ISO/TR 10063: 圆柱齿轮 功能组,检验组,公差族(正在制订中)
4) GB/Z 18620.4-2002 圆柱齿轮 检验实施规范 第4部分:表面结构和轮齿接触斑点的检验