三环减速器的振动及其实验研究
6.1 引言
实际运用已经表明,SHQ40 型三环减速器存在着比较严重的振动、并伴随温升、冲击等问题。在中高速、重载下更为突出,己成为该产品能否大规模生产及推广应用的严重障碍。本章提出三环减速器振动参数的理论计算,并对SHQ40 型的振动进行分析。用理论及实验进行对比研究,验证本文提出的内齿行星传动理论的正确性。并为降低三环减速器振动冲击提出一些可以实施的方案。通过理论计算,这些方案的效果均显著。对进一步改进设计三环减速器,控制振动具有重要的指导意义。
6.2 三环减速器的振动参数
三环减速器是由三套(三相)双曲柄连杆齿轮机构并列构成的相互约束的闭环机构。因此,各齿板(连杆)及偏心套庄转动过程中,将产生水平和垂直方向的交变质性力。该惯性力通过各轴及轴承转化为箱体轴承载荷传递给箱体,使其在垂直于齿板平面的两个坐标面内产生不平衡的交变力偶矩,从而使减速器产生振动。当机构存在变形或误差时,减速器的输入机构变成曲
柄摇杆机构。此时,一套子机构过死点时,将由另两套子机构,强行推动其越过曲柄摇杆机构的死点位置,这势必造成死点位置的载荷冲击。该冲击载荷也将引起箱体的强烈振动。因此,三环减速器的振动是由机构的交变惯性力和过死点时产生的冲击载荷引起的。下面用振动速度、振动加速度等参数来描述三环减速器的振动问题。
6.2.1 齿板的振动速度和振动加速度
无论是惯性力还是死点冲击力,都将使构件产生变形,使其质心产生位移。因此,可以用齿板质心位移对时间的导数一速度、加速度来描述齿板的振动或冲击。
齿板简图如图6-1所示。以齿板支承轴孔与偏心套的接触点为参考点,则齿板质心的位移为
以上各式中的

等通过求解三环减速器的动力分析方程得到。
6.2.2箱体轴承座的振动速度、振动加速度
三环减速器内部机构运转时产生的动载荷及冲击载荷均通过各轴传递给箱体轴承,产生轴承载荷,作用于箱体轴承座,使箱体产生振动。因此,可以用箱体轴承座处理的轴中心的振动速度、加速度来描述轴承座处的振动。
式中 Khi是箱体轴承刚度;

支承各轴的轴承载荷是转角

函数。
6.2.3传动轴的冲击角速度及冲击角加速度
理想情下(机构无变形、无误差等),三环减速器的各传动轴之间无角速度冲击产生各轴之间相对角速度、角加速度为零,即
式中

是高速输入轴与高速支承轴之间的冲击速度及冲击角加速度;

是输出轴与高速轴之间的冲击角速度及冲击角加速度;

是高速输入轴或支承轴的角速度;

是高速输入轴或支承轴的角加速度;

是输出轴的角速度及角加速度。
I是三环减速器的传动比。
由于减速器机构的变形及各构件的误差,使各传动轴的角速度及角加速度不再满足条件式(6-8)及式(6-9),亦在运转过程中各轴之间存在角速度及角加速度的冲击现象。该冲击将直接导致系统振动,使输出速度产生波动、降低其输出的稳定性,并产生冲击载荷。
设在某t时刻,各轴所转的角位移分别产

如图6-2所示,则各轴的角速度为
6.2.4转速、传动比及转矩的波动
轴间的冲击将引起输出的转速波动,并使三环减速器的传动比不再为恒定值。若输入轴的转速为n,则输出轴的转速可表示为
6.3SHQ40型三环减速器的振动分析
根据上一节导出的三环减速器的振动参数计算公式,可以对有误差和无误差时的三环减速器的振动参数进行计算。
6.3.1无误差时的冲击振动分析
在不考虑三环减速器机构运动副间隙、齿形误差,以及分度误差时,中间齿板的振动速度、加速度见图6-3所示。由图可看出:
1.无论振动速度还是振动加速度,沿水平方向的幅值均比铅垂方向的大,这一点与实测结果相吻合。
2.在齿板的振动时域曲线中存在其平动运动的稳态分量,在机构的两个死点位置即t=0.03S,0.06S附近出现两次幅值不等的速度及加速度冲击,说明三环减速器齿板的振动主要是由于双曲柄机构变成曲柄摇杆机构,在强行过“死点”时产生的载荷冲击引起的。
3.死点水平方向的冲击速度及加速度最大值为
Vmax=15.69 mm/s
amax=23539 mm/s
图6-4是支承轴轴承座及输出轴轴承座的振动速度及振动加速度时域图。图(c)中,一个周期内的三根较长的冲击棒线分别是三相机构因死点引起的啮合冲击。轴承座的振动速度比齿板的振动速度小,但振动加速度比齿板振动加速芳略大,最大值为
vmax=13.511 mm/s
amax=24689.375 mm/s
输出轴轴顾座的振动速度及加速度都比支承轴或输入轴轴承座的小10倍左右,其最大值为
vmax=1.2 mm/s
amax=2058.999 mm/s
由此可见三环减速器产生振动主要是由于高速轴冲击动载荷作用箱体轴承而引起的。
图6-5是输入轴与输出轴之间产生的角速度及角加速度冲击的时域曲线。从图可以看出两轴在机构死点位置,振动的冲击速度及冲击加速度均很大。
由以上分析说明了SHQ40型三环减速器在无误差时,产生振动的根源来自两方面:
1.由于各齿板作平动转动时因惯性力产生的稳态振动;
2.因双曲柄机构变形为摇杆机构后,强行通过死点而产生的死点冲击载荷引起的冲击振动。
在以上两点中,前者机构性质决定了的,是固有的。后者所占在重比前者大几倍甚至上十倍。因此,控制三环减速器的振动只有从后者入手。
6.3.2有误差时的冲击振动分析
当三环减速器各构件存在误差或运动副有较大的间隙时,产生的死点冲击振动更加大。
图6-6是输入轴上靠近输入端的偏心套旋转0.5°(分度误差)时,理论计算出的齿板振动及轴承座的速度及振动加速度。从图看出,冲击发生在过0°的死点位置,其幅值比无误差
时的冲击值大10倍左右。
图6-7是某相双曲柄机构在输入端具有0.03mm间隙时,齿板及轴承座的振动速度、振动加速度。图中表明,速度、加速度都在两个死点位置出现较大的冲击值。
由上述分析可知,误差引起减速器的死点冲击振动,比无误差时大许多倍,而有在水平方向明显大于垂直方向的。因此,在加工时,要尽可能减小误差、降低振动。
6.4SHQ40型三环减速器的振动实验
为了验证用本文提出的理论计算结果的正确性,我们对SHQ40型三环减速器做了振动测试实验。
6.4.1实验系统的配置
实验在重庆大学机械传动国家重点实验室电功率封闭式齿轮试验台上进行的,实验系统总配置如图6-8所示。
实验时,通过控制台操纵,交直流机组1发出直流电压设直流测功机1按恒定转速带动整个传动系统运转。SHQ-2及汽车变速箱将被测试件SHQ-1输出的转速升高后驱动直流测功机2发出直流电流,该电流经交直流机组2逆变为工频交流电返回电网,完成整个电功率封闭传动链。控制参通过控制交直流机组电压、电流、改变传动系统的转速转矩大小。被测信号由加速度传感器提取,经由电荷放大器放大后,进入磁带记录仪及CF-355频谱分析仪进行分析计算。电功率流封齿轮传动实验台如图6-9所示。
图6-9 电动率流封闭齿轮传动实验台(图略)
6.4.2多于SHQ40的测点布置
被测对象是用于起重行业的单级三环减速器。布置型式为110型,二高速轴位于低速轴同侧,转动中心共线。实物如图6-10所示。其主要参数为
图6-10SHQ40型三环减速器(图略)
传动比:i=16
额定转速:n=750rpm
额定功率:N=10KW
齿轮参数:Z1=48、Z2=51、e=6.392、m=4、B=30mm
轴间距:L1=190mm、L2=210mm
中心距:L=400mm
其他:S=55,d=34mm
为了将理论分析的结果与振动测试分析结果对比印证,将测点选在三个箱体轴承座及齿板支承轴孔的上边缘,如图6-11所示。
6.4.3 实验步骤
1.跑合试验
正式试验之间,减速器在试验台上分别以200rpm,300rpm,400rpm,500rpm,…1500rpm空转,进行20小时的跑合试验,跑合完毕后更换润滑油。
2.空载试验
分别在转速为800rpm,1000rpm,1500rpm三种空载工况下,测试记录SHQ40齿板及箱体轴承座上各测点的振动速度及加速度。
3.加载试验
分别在800rpm,1000rpm,1500rpm等转速下,测试齿板及箱体轴承座的振动速度及加速度。
6.5 理论计算与实验结果对比分析
测试结果经频谱分析处理后,将其与理论计算的结果进行对比分析如下。
1.齿板的振动
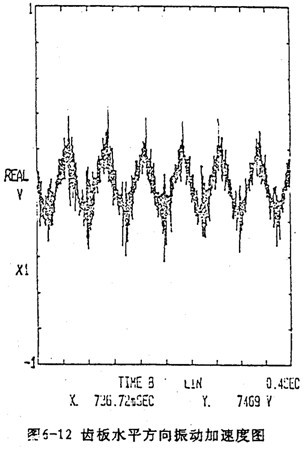
图6-12是齿板的实测振动加速度时域曲线图。从时域曲线图可知,SHQ40 型齿板的振动加速度中,存在稳态正弦分量,它是由于齿板作圆周平动运动产生。在其上迭加的每转两次冲击及其振动响应衰减信号,明显表现出齿板的加速度冲击信号,而且最大冲击发生在齿板过死点位置,每转两次非等幅冲击,恰好构成转频16.667Hz 的周期函数。
经转换计算后,加速度的最大冲击值为a
max 二21844mm/s
2。从加速度时或曲线规律发生死点的位置以及最大冲击值看均与理论计算结果(见图6-3 )相吻合。
2.箱体轴承座的振动
由于每片齿板都存在同样的周期性激励冲击函数,相位差120°,迭加后的总效果仍然是转频周期函数。因此对箱体轴承座的冲击也呈周期性。图6-13是支承轴箱体轴承座的振动速度及加速度的实测时域曲线图。其曲线图的变化规律及幅值与图6-4完全接近。速度及速度冲击值为

。图6-14是输入轴轴承座的实测振动加速度时域曲线及其频谱分析图。从加速度谱图中看出,第一谱峰的频率值为33.75Hz,恰好是输入轴转频的二倍,也是死点冲击频率。死点冲击是一周两次,其频率为33.4Hz,这说明理论计算的结果完全可靠;第二谱峰的频率值为16.87Hz ,与齿板转频(输入轴频率)相近,是齿板的稳态振动频率;第三谱峰的频率值为49.55Hz ,是三环减速器的啮合频率(50Hz) ,第四谱峰的频率值为99.50Hz ,是死点的啮合冲击频率。图6-15是某单齿环内齿行星齿轮减速器的轴承座振动加速度的实测及理论计算曲线图。从图可以看出理论和测试的分布规律极为相似。图中一个周期有一次较大的加速度冲击峰,是由于行星齿板过180°死点时产生的啮合冲击。
从以上对轴承座的振动实测结果及频谱分析可知,激励三环减速器振动的载荷主要有:
(1)平面四杆机构因变形或误差,在过死点位置时对轴承座产生的冲击载荷;
(2)齿板作平动圆周运动时产生的稳态动载荷;
(3)齿板与外齿轮之间齿轮副的啮合冲击;
(4)平面四杆机构在死点位置时外齿轮造成的冲击载荷。
3.输出转速转动比
由于机构的变形及误差等原因,将使输出转速及传动比动变化,冲击箱体、产生振动。图6-16是对SHLEO15 型三环减速器实测及理论计算的转速和传动比随时间变化的波动曲线。输出转速对比为
实测结果 理论结果
最大转速 39.184(rpm) 39.95754(rpm)
最小转速 35.358(rpm) 36.40373(rpm)
波动量 3.837 3.55381
传动比对比为
实测结果 理论结果
设计传动比 17 17
最大传动比 17.556 17.580622
最小传动比 16.229 16.017
波动量 1.327 1.5036
可见,实测值与理论值相近,说明理论计算结果正确。
以上的理论和实验结果都表明,三环减速器的振动源于平行曲柄机构变形或因误差产生的死点冲击。冲击力大小与载荷成正比,冲击发生的时间与转速成反比。功率越大,啮合力也越大,冲击峰越高;转速越高冲击脉宽越小,激振动力带宽越宽。因此,减速器在高速重载时,产生的宽带与较强能量的激振源更容易激发减速器及其附联结沟的广泛共振,从而发生强烈振动。特别是推动环板死点的冲击力矩将可能造成箱体整体及附联结构的强烈振动。冲击力还将引起轴、轴承、键的较大交变动载,并可能引起键联接的松动、摩擦,发热等。
通过对SHQ40型三环减速器的理论计算结果及振动实验的对比研究,说明本文提出的内齿行星传动的动力分析理论完全正确,可以作为三环减速器等内齿行星传动装置的设计分析理论。
6.6 控制冲击振动的方案
前面已从理论和实验两方向论证了三环减速器产生振动的根本原因是机构变形及误差引起的死点冲击。因此,应从解决死点冲击出发控制其振动。
1.采用双轴输入降低死点冲击
采用双轴输人的齿板及箱体轴承座振动速度、加速度如图6-17所示。从图看出齿板速度及加速度值明显变小(为单轴输人时的0.3倍),而且无冲击,完全属于稳太振动。箱体的振动速度及加速度幅值只是单轴输人时的0.2倍。图6-18a是一轴的偏心套存在0.05度的分度误差时齿板的加速度曲线图,图中明显出现加速度冲击棒线。采用双轴输入后,死点冲击被彻底(见图6-18b) , 变成稳态振动曲线了。因此,为了减小三环减速器的振动,有必要加大三环减速器的横向尺寸,在箱体内增加一套双轴输入的齿轮功率分流机构,或者在箱体外另设计一套功率分流机构,以解决机构过死点的振动问题。
2.改变支承轴的位置
在上一章已经分析过,当三轴水平布置而且高速轴在输出轴的同侧时,载荷幅值最大,各相啮合力等都很不均衡(见图5-24)。图6-19是将支承轴布置在输入轴与输出轴间的150°位置时齿板的振动加速度。由图可知,因误差引起的冲击已被完全克服,而且原有的稳态幅值也降低了很多。
3.增加行星轴承刚度、降低内齿圈刚度
增大行星轴承刚度的目的在于减小双曲柄机构的变形,降低死点冲击幅值。并且使各相啮合力均衡化、减小啮合冲击。图6-20是分别将行星轴承刚度增加一个数量级和内齿圈降低一个数量级时齿板的振动加速度。两者加速度幅值均降低了1/4 倍左右。
4.减小支承轴或输出轴的箱体轴承刚度
降低箱体轴承刚度是为了吸收内部机构对箱体的冲击振动,减小冲击幅值。图6-21是转速为1500(rpm)即时分别将支承轴及输出轴的箱体轴承与轴之间加一3mm的弹性垫圈时,计算出的箱体振动加速度曲线。从图中看出,减小支承轴箱体轴承刚度比减小输出轴箱体轴承的效果更明显。
5.增加高速轴的刚度
增加高速轴的刚度是降低冲击载荷的重要途径。轴的刚度大(值径大),扭转、弯曲变形小,双曲柄机构变形也就小,这样既减小了冲击振动、又增加了轴的强度。图6-22将高速轴的直径由原来的45mm加到55mm后的,振动加速度图。
6.对各齿板的死点位置进行修形
由于机构过死点时,因变形要引起死点冲击,可以通过死点位置及其附近的轮齿(齿板)进行
修形,使三相载荷均衡化。图6-23是将死点位置轮齿修形后,轴承座的振动加速度图。与图6-21(a)比较,总体幅值明显下降。