第二章 三环减速器结构、工作原理及振动、噪声分析
§2-1 引言
三环减速器是90年获国家优秀专利的新型通用减速(或增速)装置,与其它类型的传动装置相比较,它具有体积小、重量轻、承载能力大、生产成本低等一系列优点,已开始在各工业部门得到应用,并已被列为国家重点推广应用的重大项目之一。但由于这种传动形式问世仅几年,对其的结构原理、运动学分析、动力学分析、材料、强度、动态性能及噪声分析、制造工艺及应用特点等方面还未能开展较全面的理论和实验分析与研究,本章的内容就是分析了三环减速器的结构及工作原理,并对其的振动机理和噪声问题进行了理论上的分析和研究。
§2-2 三环减速器的结构及工作原理
§2-2.1 三环减速器传动原理
齿轮传动是最常见的传动形式,由一系列相互啮合的齿轮组成传递运动的轮系,轮系可分这定轴轮系和动轴轮系两大类,行星齿轮传动属于动轴轮系中的一种,而少齿差行星齿轮传动机构实质上是一个由平面四杆机构和内啮合齿轮副组成的齿轮连杆组合传动机构。
三环减速器实质上就是一种双曲柄输入式、内齿轮作圆周平动而外齿轮用于输出的少齿差行星齿轮传动机构。原理如图2-1所示。双曲柄机构1-1以转速ω1输入运动,通过连杆2及与连杆相固连的内齿轮了将运动传给外齿轮4,并通过外齿轮4将运动传递给5ω2输出运动和动力,其传动比为:


图2-1
式中:Z1——外齿轮齿数;
Z2——内齿轮齿数。
众所周知,双曲柄机构的最大缺点就是存在死点位置,即当曲柄,与连杆共线时,机构处理运动不确定位置,其传动角为零,机械无法运动。为了克服死点位置,目前已出现了三种解决方法:其一是在同一行星轮上布置多套双曲柄机构的方法:其二是采用双曲柄动力输入式方法;基三是采用多相并列式双曲柄机构来克服死点的方法。三环减速器就是用三相并列双曲柄机构来克服死点位置,如图2-2所示。
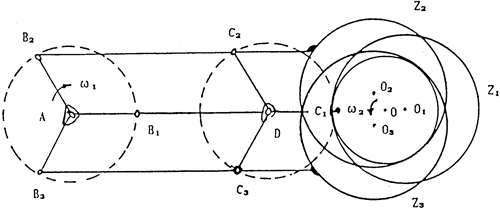
图2-2

§2-2.2 三环减速器类型
三环减速器通过增加高速轴和低速轴的数量或变更其相互位置,可以构成若干种类型,但其基本形只有两种,即输出轴位于输入轴和支承轴之间的101型和输出轴偏置的110型,110型适用于大中心距要求的场合。
110型三环减速器的基本构造如图2-3(a)(b)示,其支承轴3位于输入轴1和输出轴4之间,大中心距传动时,结构比较紧凑,但由于齿板上的啮合力的作用点位于两行星轴承之处,机构受力情况不太理想。
101型三环减速器基本构造如图2-4(a)(b)所示。其输出轴4位于输入轴1和支承轴3之间,受力情况要优于110型三环减速器。
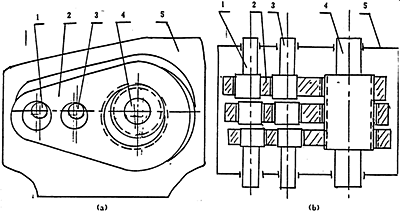
图2-3 110型三环减速器结构简图

图2-4 101型三环减速器结构简图
§2-2.3 三环减速器特点
一、传动比在,适用性强
由于采用了渐开线少齿差内啮合传动,可以获得较大的传动比,单级传动的传动比可达16~90;同时减速器的中心距与齿轮参数无关,可以根据需要设计,故其适用性较强。
二、结构简单、制造维修方便
由于齿板只做自转而不做公转,故没有一般行星齿轮传动的行星架或少齿差传动中的输出机构;同时,高速轴与低速轴位于同一平面上,各轴两端支承,减速器箱体可以采用水平分箱,上下组合形式。
三、承载能力高、轴承寿命长
内啮合齿轮副由于接触点处齿廓曲线方向相同,所以齿面接触强度较高,同时,当内、外齿轮的齿数差很少时,运转时由于轮齿的变形而形成多齿接触,使行三环减速器有较强的承载能力和过载能力;另外,行星轴承位于内齿圈外,其安装尺寸容许空间较大,轴承的计算寿命可达到2000小时以上。
四、制造成本低
三环减速器基本构件的材质要求不高,齿面采用的是软齿面,并经充分跑合后即可满足承载要求,不需淬火磨削,加工精度要求低,渐开线齿轮在普通齿轮机床上就可以进行加工,其成本仅为摆线针轮减速机的80%左右。
五、传动交率高
由于取消了输出机构,同时行星轴承受力较小,三环减速器的传动效率可达92%~96%左右。
§2-3 三环减速器的振动分析
§2-3.1 三环减速器振动激励分析
三环减速器是近年来出现的一种应用前景较为广泛的双曲柄输入式渐开线少齿差行星齿轮减速器,由图2-1、图2-2、图2-3可知,它实质上是由平面四杆机构和内啮合齿轮副组成的齿轮连杆组合传动机构,因此,引起三环减速器振动的原因除了有齿轮机构产生的外,还应考虑平面四杆机构所引起的振动。
造成三环减速器产生振动的激励频率有如下几个方面:
1、内啮合齿轮副产生的激励频率包括:
(1)内啮合频率:
如图2-5所示,轮齿的啮合频率ft为:

式中Z1、Z2分别为外齿轮、内齿轮的齿数,而N1、N2分别为各自转速,单位为转/分,i为传动比。

图2-5
(2)内啮合频率的各阶谐波频率。
(3)内啮合频率的各阶分谐波频率。
(4)转动轴频

式中N为转速,单位为转/分钟。
2.轴承等传动件产生的激励频率滚动轴承旋转频率为:
a.外圈频率:

b.内圈频率:

c.滚子元件频率:

d.保持架频率:

式中:d—滚动元件直径;
D—轴承的节径;
β—接触角;
n—滚动元件数量;
N—转速。
3.平面杆四杆机构产生的激励频率
a.机构不平衡重频率及其各阶谐波频率
fw=N/60(Hz) (2.8)
b.死点冲击频率及其各阶谐波频率
fsx=2N/60(Hz) (2.9)
fst=2ft (Hz) (2.9.b)
式中,N为输入轴转速,单位rad/min
§2-3.2 三环减速器振动机理分析
三环减速器的传动原理如图2-2及图2-3示。为了简化分析,作如下假设:
1.各种加工安装误差不计;
2.三环板啮合力交化规律相同,仅相差120°相位;
3.高速轴单轴输入;
4.匀速转动;
5.除死点位置及其邻域外,中间转臂轴偏心套构成的从动轴柄可简化为二力杆;
6.离心惯性力不计,重力不计(三环板离心惯性力相互抵消,残余惯性力极小)。
7.输入、输出扭矩为常数。
以下分析中,各符号定义如下:
FAr、FA、FB、FBr、Fn——环板受力;
F、Fn1——三环板当量啮合力及第i环板啮合力;
K1——第i环板啮合刚度;

Ma、Jo——环板质量与转动惯量;
ф——环板机构转角;
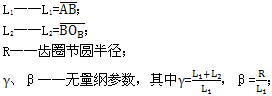
δ——啮合点切向变形量;
α——压力角。
一、力学模型
按上述假定,我们可仅取其中任一块环板进行受力分析,如图2-6所示。

由上式可以推出无量纲力:

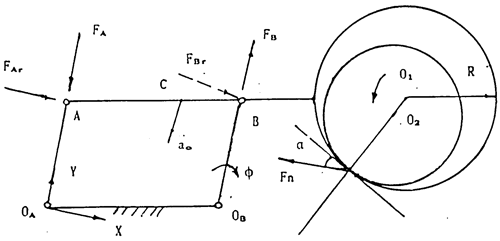
图2-6 环板受力模型
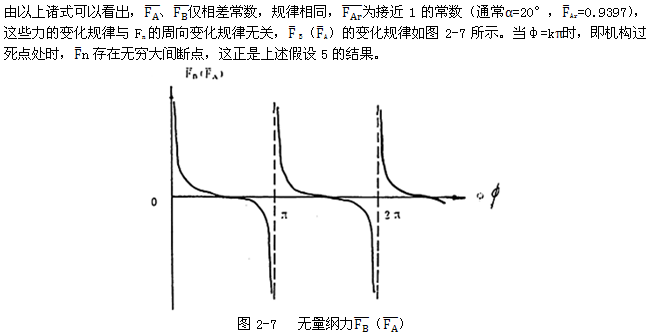

图2-8 三环板静不定系统简化模型
实际上,环板的受力与Fn(ф)有关,因为三块环板共同受载时彼此约束,构成静不定系统,如简化模型图2-8所示。
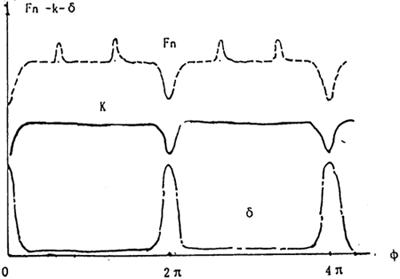
图2-9 啮合点切向位移、综合刚度与啮合力
根据有限元分析结果,啮合点受单向载荷时,齿圈啮合点切向位移有如图2-9所示的规律,且各环板受力应满足变形协调条件:
F=Fn1+Fn2+Fn3

因此对应的综合刚度K(φ)与啮合力Fn(φ)也相应地如图2-9所示。
二、环板受力分析
因Fn(Kπ)≠0,则当环板机构过死点位置时,该双轴柄机构将在啮合力Fn与输入轴驱动力FAr的作用下产生反转力矩,有可能在机构的该运动状态的不确定位置ф=Kπ处由正向双曲柄机构变成反向双曲柄机构,而在此时,另两套双曲柄机构将通过转臂轴与偏心套的键联接处产生推动该环板过死点位置的作用力,克服其反转,从而产生冲击力FBr,否则FB、FA将趋向于无穷大,其物理意义为机构不可能通过死点。显然,在ф=Kπ的死点位置的微小领域内,转臂轴的二力杆假设不在再成产。冲击力FBr的峰值由该时刻的动力学方程(2-10)可导出为:
FBrmax=Fn(γ+β)cosα (2.13)
理论上,该力仅在ф=Kπ点产生,而FA、FB将在此点处趋于无穷大。考虑实际结构的弹性变形等因素,FBr应在ф=Kπ的一转角领域内ф=Kπ±△ф产生,而FB、FA在该邻域内由正(或负)向峰值过零转变为负(正)向峰值,如图2-10所示。这是因为FB、FA在死点位置附近迅速增大产生的弹性变形也会使环板产生微小反转角度,而导致FBr的产生,显然该微小角度领域的大小以及FB、FA所能达到的峰值决于环板的刚度。刚度越大,该领域越小,FB、FA峰值越大,FBr的大小与啮合力及无量纲参数(γ+β)成正比。一般情况下,高速重载的三环减速器、环板机构的刚度啮合力等均较大,因此死点处受到的冲击越大,且冲击脉冲宽度小(反比于角速度),激振频率更宽,更易激起广泛的共振。
因此任何导致环板间承载不均的误差因素都将引起冲击力,因高速轴同侧布置与双侧布置相比γ+β约大3位,在同等条件下,双侧布置所受的冲击力小。
同理,对于齿轮副来说,在ф=Kπ的某一转角领域ф=Kπ±△ф内,啮合力也将由Fn趋于零然后又增大到Fn而产生冲击,而且在啮合点处的冲击力要大于支承轴处的冲击力FBr。
这一节也解释了式(2.9)的由来。

图2-10 转臂轴在死点位置附近受力
三、箱体受力分析
三环板间彼此构成约束,因此一板过死点时产生的冲击力FA、FB之反力将相向作用于两根高速轴上,它们本质上构成平衡内力,但作用于不同位置,将引起各部件的振动,但不令引起箱体的整体振动。
另一方面,在ф=Kπ处的环板受力及两高速轴的受力分析表明,由冲击力FBr以有FAr在ф=Kπ处的变化将在箱体上产生不平衡的冲击力矩为:

这一冲击力显然将会引起箱体的摆振并将引起基础的振动。
以上的有关三环减速器的振动理的分析的有关结论,我们将通过后续章节的试验予以分析并验证。
§2-4 三环减速器的噪声分析
§2-4.1 三环减速器噪声的产生及传播
运动着的机械必然产生振动,而机械噪声大部分是由于工程机械的振动而辐射的。机械噪声的类型很多,按声强随时音质变化情况主要可以分为三种:稳态噪声、周期噪声和脉冲噪声。稳态噪声是由于随机力或稳态力的作用下而产和噪声;周期性噪声是在周期力作用下产生的噪声;脉冲(冲击)噪声是由机械冲击力产生的噪声。在实际的机械噪声中,这三种噪声不会单独存在,而往往同时存在,互相迭加而形成混合噪声,这振动的机械或部件就是产生噪声的噪声源。
三环减速器中各传动部件,如内啮合齿轮副、轴、轴承、环板、润滑等都是减速器产生机械噪声的噪声源,各噪声源发出的声波,在箱内遇到箱壁和其它结构时,一部分被反射,重新回到箱体内,另一部分被箱体或其它部件吸收,还有一部分透过箱壁产生折射或穿过箱体缝隙及开口处发射到箱体外面。同时,由于减速器箱体内各部件的振动激励(详见§2-3节),经轴承座传递到箱体,造成箱体振动而辐射出机械噪声。
三环减速器向外副射的噪声按其传播途径大致可分为两类:固体传播噪声和空气传播噪声。
其传播途径如图2-11所示。

图2-11 三环减速器噪声传播途径
从图中可知,固体传播噪声是由传递中的振动激励引起的,环板冲击及轮齿啮合振动通过轴、轴承、轴承座传向箱体和机座;引起振动而辐射的噪声通过箱壁向外辐射,此外,由轴的振动引起的噪声的一部分直接向箱体外辐射。
当三环减速器内部的各种振动激励源的频率与箱体的固有频率接近或一致时,将产生共振,此时,箱体将辐射出较大的机械噪声。
§2-4.2 三环减速器噪声的研究方法
三环减速器是一种双曲柄输入式渐开线少齿差行星齿轮减速器,当它传递运动和动力时,各种振动激励源激起箱体振动而辐射出机械噪声,这种机械噪声为固体传达室播噪声,具有关研究资料表明,固体传播噪声的输出能量是噪声发出能量的95%以上,因此,我们在对三环减速器进行噪声分析研究时,把工作重点放在箱体受激励振动而辐射出的固体传播噪声上。
三环减速器受激而使箱体产生振动,进而辐射出噪声,这里受激励作用是箱体产生振动的原因所在,而振动又是箱体辐射出噪声的原因之所在,换句话说,三环减速器振动系统由于受到激励作用后,而产生的效果有两种表现形式,一是振动,二是噪声,二是是相互紧密相连的,它们之间必然存在着一种确定的定量关系,一般而言,振动大,噪声也大,但其噪声的量值,却不仅与振动量大小有关,而且与各频率下的辐射效率等许多因素有关。对于某一确定的齿轮箱体及某一单频率噪声,箱壁辐射声能的大小与箱壁表面振动速成度及表面积大小正比,且可认为体现该比例的辐射系数在整个噪声频域内,是一个仅与噪声频率、箱体材料特性、几何形状有关的确定函数。这样,我们就能通过测试箱壁振动来求出齿轮箱的辐射噪声。
对三环减速器的噪声问题进行较完整系统地研究,就必须从理及实验两个角度来进行。
一、三环减速器噪声问题理论研究
所谓的三环减速器噪声问题的理论研究就是噪声予估问题的研究,对箱体而言,若能在它尚处于设计蓝图阶段时,即能根据其结构参数、精度等级、预定工况等条件,预估其将来的噪声水平,并进一步以此为根据,找出齿轮箱各组成零部件的最佳结构、精品,加速设计制造进程,并能提供主动的振动与噪声的控制手段。
在本研究中,我们首先SUN工作站上对三环减速器箱体进行建模动态分析计算,然后从实际工况中识别出激励载荷,然后加到模型上进行计算,算出其发射噪声的预估值,为三环减速器的设计,制造、生产提供理论依据。
二、三环减速器噪声问题的实验研究
设计试验方案,对三环减速器进行噪声及振动试验,通过试验可以测出箱体表面的振动状态及其噪声发射值——声强的值及规律,对预估值进行验证其正确性,为噪声控制提供必要的依据。
上一页
下一页