三环减速器的振动及其实验研究
6.1引言
实际运用已经表明,SHQ40型三环减速器存在着比较严重的振动、并伴随温升、冲击等问题。在中高速、重载下更为突出,己成为该产品能否大规模生产及推广应用的严重障碍。本章提出三环减速器振动参数的理论计算,并对SHQ40型的振动进行分析。用理论及实验进行对比研究,验证本文提出的内齿行星传动理论的正确性。并为降低三环减速器振动冲击提出一些可以实施的方案。通过理论计算,这些方案的效果均显著。对进一步改进设计三环减速器,控制振动具有重要的指导意义。
6.2三环减速器的振动参数
三环减速器是由三套(三相)双曲柄连杆齿轮机构并列构成的相互约束的闭环机构。因此,各齿板(连杆)及偏心套庄转动过程中,将产生水平和垂直方向的交变质性力。该惯性力通过各轴及轴承转化为箱体轴承载荷传递给箱体,使其在垂直于齿板平面的两个坐标面内产生不平衡的交变力偶矩,从而使减速器产生振动。当机构存在变形或误差时,减速器的输入机构变成曲柄摇杆机构。此时,一套子机构过死点时,将由另两套子机构,强行推动其越过曲柄摇杆机构的死点位置,这势必造成死点位置的载荷冲击。该冲击载荷也将引起箱体的强烈振动。因此,三环减速器的振动是由机构的交变惯性力和过死点时产生的冲击载荷引起的。下面用振动速度、振动加速度等参数来描述三环减速器的振动问题。
6.2.1齿板的振动速度和振动加速度
无论是惯性力还是死点冲击力,都将使构件产生变形,使其质心产生位移。因此,可以用齿板质心位移对时间的导数一速度、加速度来描述齿板的振动或冲击。
齿板简图如图6-1所示。以齿板支承轴孔与偏心套的接触点为参考点,则齿板质心的位移为

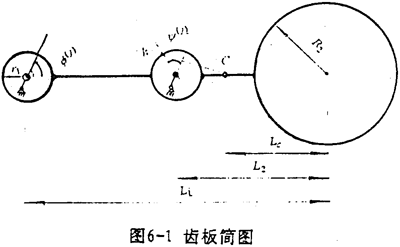
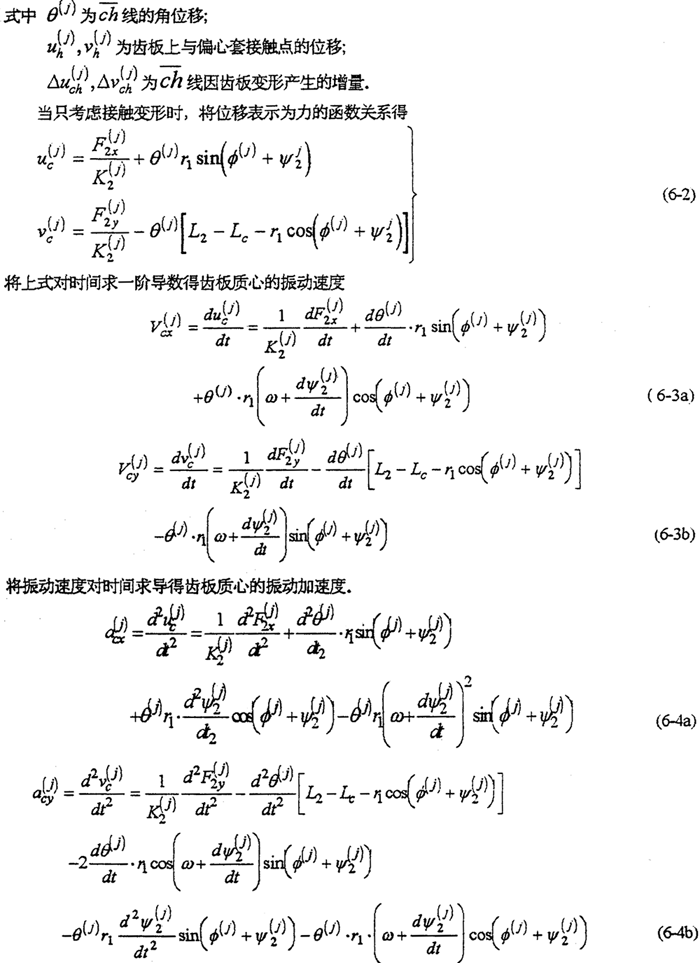
以上各式中的F(j)2x,F(j)2y及θ(j),ψ(j)2等通过求解三环减速器的动力分析方程得到。
6.2.2箱体轴承座的振动速度、振动加速度
三环减速器内部机构运转时产生的动载荷及冲击载荷均通过各轴传递给箱体轴承,产生轴承载荷,作用于箱体轴承座,使箱体产生振动。因此,可以用箱体轴承座处理的轴中心的振动速度、加速度来描述轴承座处的振动。
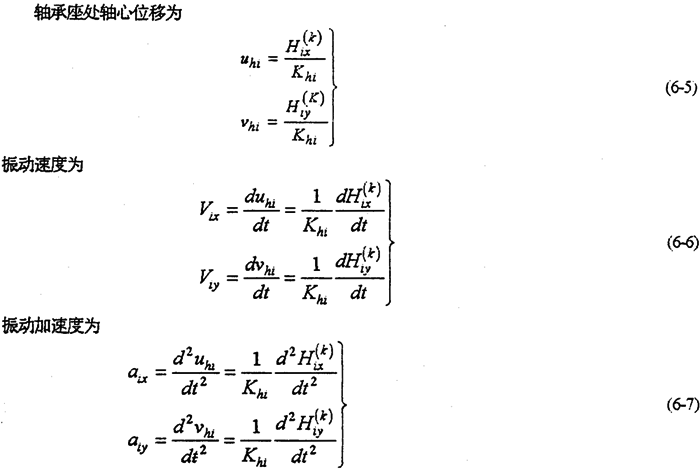
式中Khi是箱体轴承刚度;
H(k)ix,H(k)iy支承各轴的轴承载荷是转角φ=ωt函数。
6.2.3传动轴的冲击角速度及冲击角加速度
理想情下(机构无变形、无误差等),三环减速器的各传动轴之间无角速度冲击产生各轴之间相对角速度、角加速度为零,即
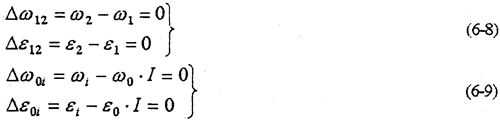
式中△ω12,△ε12是高速输入轴与高速支承轴之间的冲击速度及冲击角加速度;
△ω0i,△ε0i是输出轴与高速轴之间的冲击角速度及冲击角加速度;
ωi(i=1,2)是高速输入轴或支承轴的角速度;
εi(i=1,2)是高速输入轴或支承轴的角加速度;
ω0,ε0是输出轴的角速度及角加速度。
I是三环减速器的传动比。
由于减速器机构的变形及各构件的误差,使各传动轴的角速度及角加速度不再满足条件式(6-8)及式(6-9),亦在运转过程中各轴之间存在角速度及角加速度的冲击现象。该冲击将直接导致系统振动,使输出速度产生波动、降低其输出的稳定性,并产生冲击载荷。
设在某t时刻,各轴所转的角位移分别产φ1,φ2,φ0。如图6-2所示,则各轴的角速度为
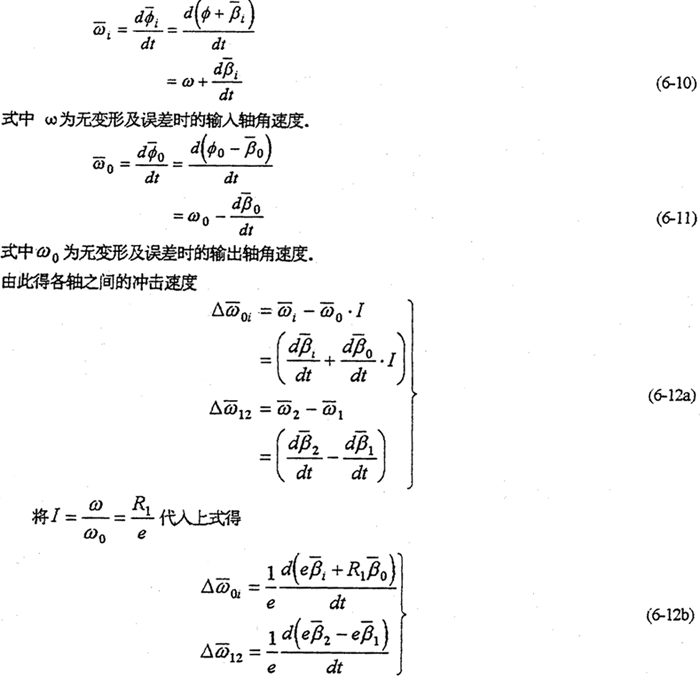
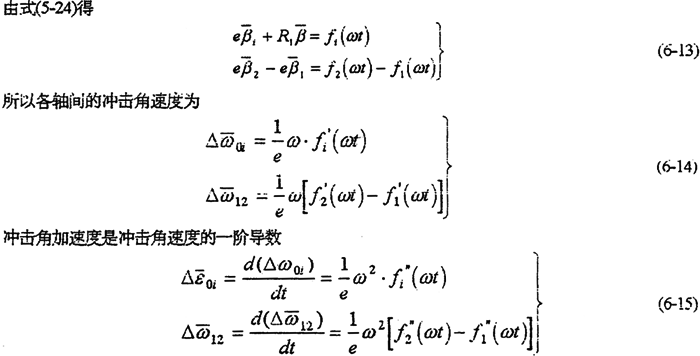
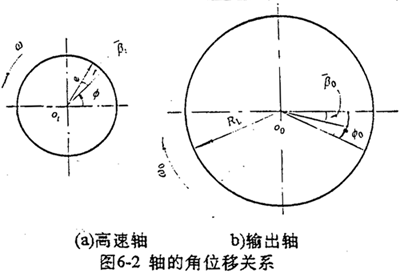
6.2.4转速、传动比及转矩的波动
轴间的冲击将引起输出的转速波动,并使三环减速器的传动比不再为恒定值。若输入轴的转速为n,则输出轴的转速可表示为
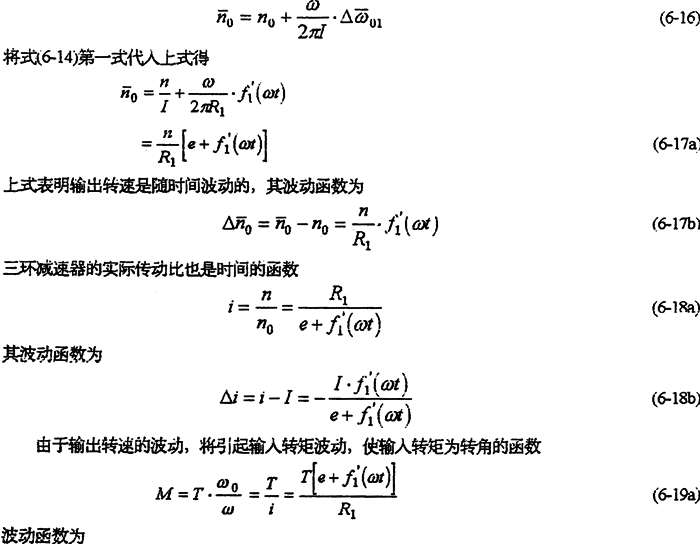

6.3SHQ40型三环减速器的振动分析
根据上一节导出的三环减速器的振动参数计算公式,可以对有误差和无误差时的三环减速器的振动参数进行计算。
6.3.1无误差时的冲击振动分析
在不考虑三环减速器机构运动副间隙、齿形误差,以及分度误差时,中间齿板的振动速度、加速度见图6-3所示。由图可看出:
1.无论振动速度还是振动加速度,沿水平方向的幅值均比铅垂方向的大,这一点与实测结果相吻合。
2.在齿板的振动时域曲线中存在其平动运动的稳态分量,在机构的两个死点位置即t=0.03S,0.06S附近出现两次幅值不等的速度及加速度冲击,说明三环减速器齿板的振动主要是由于双曲柄机构变成曲柄摇杆机构,在强行过“死点”时产生的载荷冲击引起的。
3.死点水平方向的冲击速度及加速度最大值为
vmax=15.69 mm/s
αmax=23539 mm/s
图6-4是支承轴轴承座及输出轴轴承座的振动速度及振动加速度时域图。图(c)中,一个周期内的三根较长的冲击棒线分别是三相机构因死点引起的啮合冲击。轴承座的振动速度比齿板的振动速度小,但振动加速度比齿板振动加速芳略大,最大值为
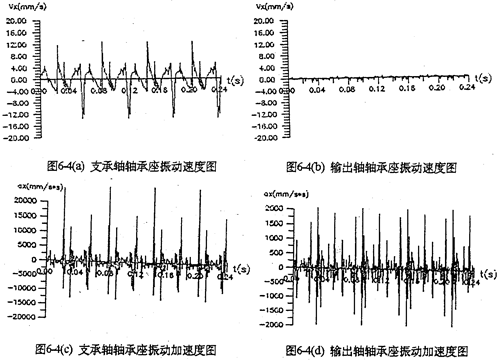
vmax=13.511 mm/s
αmax=24689.375 mm/s
输出轴轴顾座的振动速度及加速度都比支承轴或输入轴轴承座的小10倍左右,其最大值为
vmax=1.2 mm/s
αmax=2058.999 mm/s
由此可见三环减速器产生振动主要是由于高速轴冲击动载荷作用箱体轴承而引起的。
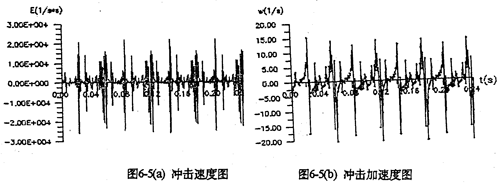
图6-5是输入轴与输出轴之间产生的角速度及角加速度冲击的时域曲线。从图可以看出两轴在机构死点位置,振动的冲击速度及冲击加速度均很大。
由以上分析说明了SHQ40型三环减速器在无误差时,产生振动的根源来自两方面:
1.由于各齿板作平动转动时因惯性力产生的稳态振动;
2.因双曲柄机构变形为摇杆机构后,强行通过死点而产生的死点冲击载荷引起的冲击振动。
在以上两点中,前者机构性质决定了的,是固有的。后者所占在重比前者大几倍甚至上十倍。因此,控制三环减速器的振动只有从后者入手。
6.3.2有误差时的冲击振动分析
当三环减速器各构件存在误差或运动副有较大的间隙时,产生的死点冲击振动更加大。
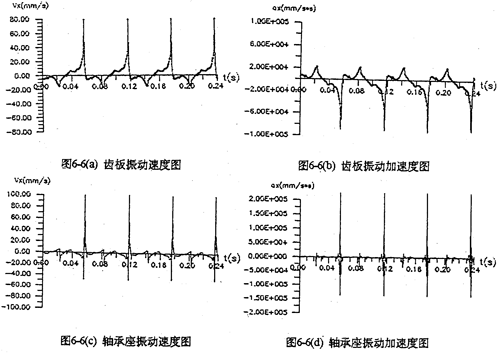
图6-6是输入轴上靠近输入端的偏心套旋转0.5°(分度误差)时,理论计算出的齿板振动及轴承座的速度及振动加速度。从图看出,冲击发生在过0°的死点位置,其幅值比无误差时的冲击值大10倍左右。
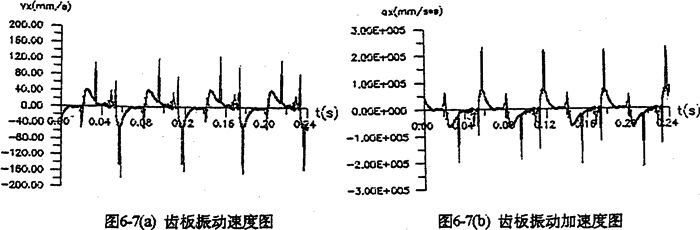
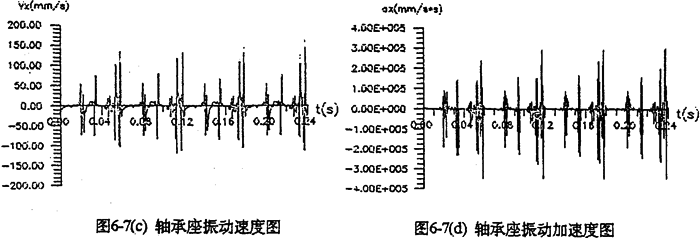
图6-7是某相双曲柄机构在输入端具有0.03mm间隙时,齿板及轴承座的振动速度、振动加速度。图中表明,速度、加速度都在两个死点位置出现较大的冲击值。
由上述分析可知,误差引起减速器的死点冲击振动,比无误差时大许多倍,而有在水平方向明显大于垂直方向的。因此,在加工时,要尽可能减小误差、降低振动。
6.4SHQ40型三环减速器的振动实验
为了验证用本文提出的理论计算结果的正确性,我们对SHQ40型三环减速器做了振动测试实验。
6.4.1实验系统的配置
实验在重庆大学机械传动国家重点实验室电功率封闭式齿轮试验台上进行的,实验系统总配置如图6-8所示。
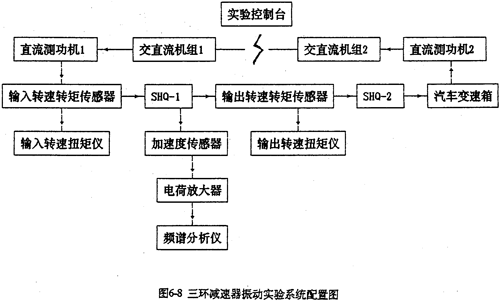
实验时,通过控制台操纵,交直流机组1发出直流电压设直流测功机1按恒定转速带动整个传动系统运转。SHQ-2及汽车变速箱将被测试件SHQ-1输出的转速升高后驱动直流测功机2发出直流电流,该电流经交直流机组2逆变为工频交流电返回电网,完成整个电功率封闭传动链。控制参通过控制交直流机组电压、电流、改变传动系统的转速转矩大小。被测信号由加速度传感器提取,经由电荷放大器放大后,进入磁带记录仪及CF-355频谱分析仪进行分析计算。电功率流封齿轮传动实验台如图6-9所示。
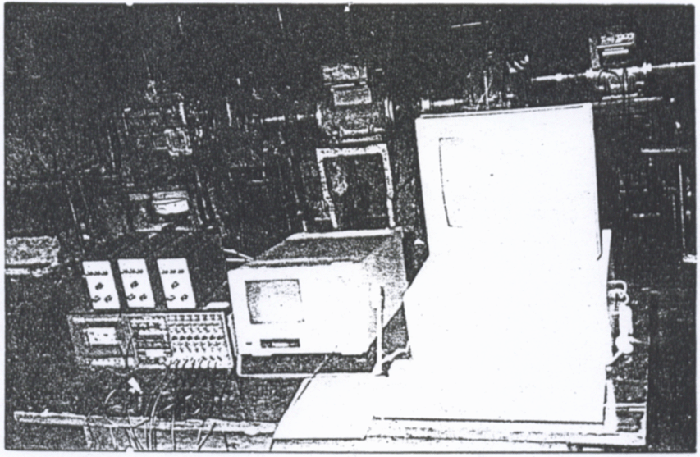
6-9 电动率流封闭齿轮传动实验台
6.4.2多于SHQ40的测点布置
被测对象是用于起重行业的单级三环减速器。布置型式为110型,二高速轴位于低速轴同侧,转动中心共线。实物如图6-10所示。其主要参数为
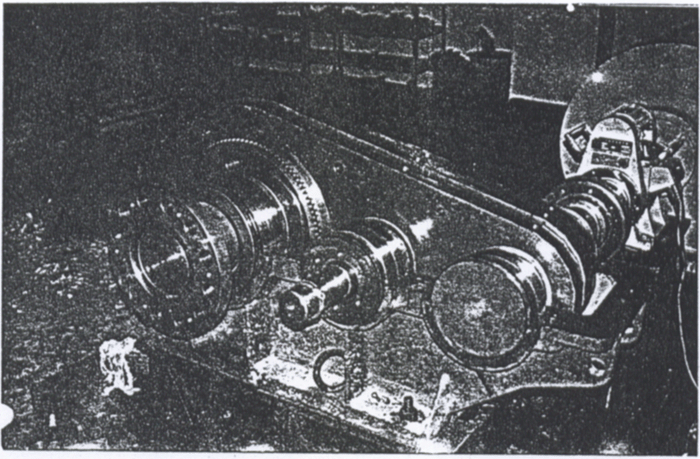
图6-10SHQ40型三环减速器
传动比:i=16
额定转速:n=750rpm
额定功率:N=10KW
齿轮参数:Z1=48、Z2=51、e=6.392、m=4、B=30mm
轴间距:L1=190mm、L2=210mm
中心距:L=400mm
其他:S=55,d=34mm
上一页
下一页