3 双环减速器环板内齿接触分析及齿轮系统模态分析
3.1 双环减速器环板内齿接触有限元分析
因为在少齿差内啮合中,不处于啮合位置的齿对在进入啮合之前以及在脱离啮合之后,其内、外齿廓间的间隙非常小,因此双环减速器环板内齿轮啮合传动在载荷作用下,因弹性变形实际接触齿对数远大于理论重合度,在传递载荷的过程中,轮齿的变形量要大于一部分齿对的间隙,这些齿对就要接触并同时分担载荷,这就大大提高了整个齿轮传动装置的承载能力。同时实际齿轮的接触对数及接触应力,随着载荷增大而相应增加。因而少齿差内啮合行星齿轮传动的实际接触齿对数的确定,对齿轮承载能力的估算以及齿轮模数的正确确定具有重要意义。对于齿轮的接触问题的,国内外学者对此已作了不少研究,取得一些研究成果。然而这些研究有的没有考虑误差的影响,有的仅考虑内外啮合齿轮副齿廓理论间隙,没有考虑轮齿制造误差和轮齿的弹性变形的影响。本文对于环板内齿轮接触问题进行了计算,计算时考虑内外啮合齿轮副齿廓理论间隙、制造误差及轮齿弹性变形的影响,在此基础上,建立了少齿差内啮合行星齿轮传动实际接触齿对数及各齿间载荷分配的理论分析计算的实体模型,利用I-DEAS软件进行了环板内齿轮接触有限元计算,并用该软件分析计算了在不同载荷工况下的实际接触齿对数、最大接触应力以及两环板上各接触齿的载荷分配情况。
3.1.1 误差对直齿内啮合传动重合度的影响分析
通常,内啮合渐开线齿轮的理论计算是按无侧隙的情况设计的,但要保证齿轮传动灵活,不发生卡滞,必须保留足够的齿侧间隙,在实际制造与安装中齿轮系统都必然存在尺寸误差,这些误差直接影响着齿轮传动的精度、齿轮的强度和振动噪声。
众所周知,内啮合直齿圆柱齿轮传动的理论重合度为:

设内齿直齿轮传动的齿轮模数为m,分度圆压力角为a,外齿轮齿数为Z1,内齿轮齿数为Z2,外、内齿轮变位系数分别为X1、X2,外、内齿轮变位系数分别为S1′、S2′,外、内齿轮节圆上的齿槽宽分别为e1′、e2′,两啮合齿轮节圆上的圆周侧隙为jt,两啮合齿轮非工作侧齿廓沿公法线方向的侧隙(法向侧隙)为jn。显然有
jn=jtcosα′=(e2′-s1′)cosα′ (3.2)
联系式3.6与式3.8,从两工中可以看出,计算中心距a′与啮合角α′是一一对应关系,这样式3.6可以表达为三种形式:
(1)由确定的齿侧间隙jn与齿轮变位系数X2-X1来求中心距a′;
(2)由确定的中心距a′与齿轮变位系数X2-X1来求齿侧间隙jn;
(3)由确定的齿侧间隙jn与中心距a′来求齿轮变位系数X2-X1。
当齿轮传动的几何设计参数确定后,影响实际传动的就只有制造和安装误差,对于中心距a′而言,影响它的因素是制造误差、安装误差,而不是齿侧间隙jn与齿轮变位系数X2-X1。齿轮设计是按无侧隙进行的,同时不考虑制造、安装误差,但加工时,齿轮齿厚公差都是负偏差,即齿轮厚公差都是负偏差,即齿轮必须减薄,这样实际传动存在齿侧隙。如果不考虑中心距的误差,由式3.6的第3种形式可知,齿侧隙的变化必然影响到齿轮变位系数的变化。显然,这样的变化也就会使齿轮的齿顶圆产生变化,相应的齿顶圆奢力角产生变化,进而影响齿轮啮合重合度。
由式3.5变化为

本文实验样机的环板齿轮设计参数见表3.1所示,根据本文实验样机的环板齿轮设计参数,假定啮合角不变化,则对应齿侧隙的变化,应用MATLAB绘图分析,得到了齿轮变位系数随齿侧隙变化时的变化规律图,见图3.1所示。
表3.1 内啮合齿轮参数表
|
外齿轮 |
环板内齿 |
模数 |
2 |
齿数 |
56 |
58 |
啮合角 |
39.039° |
变位系数 |
1.37 |
1.685 |
齿顶高系数 |
0.7 |
中心距 |
2.42 |
齿顶圆直径 |
119.519 |
120.774 |
计算重合度 |
1.124 |
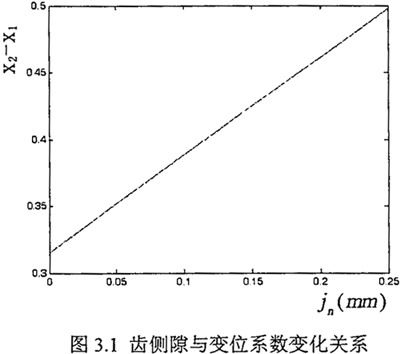

由3.2图可以看出,当齿侧隙jn由0变化至.25毫米时(查资料取较大最小侧隙参考值),齿轮变位系数差X2-X1的变化量由近0.32变化到0.50,变化了约0.18。
对于齿顶圆直径按德国工业标准DIN的简单方法有:
da1=m(z1+2ha*+2x1) (3.10)
da2=m(z2+2ha*+2x2) (3.11)
由式3.10、3.11可以看出,当总变位系数xΣ=x2-x1产生变化时,必然引起起啮合齿轮齿顶圆直径的变化。按X1、X2变化最小原则,有三种可能性,即X1不变,X2变化0~0.18;或X1变化0~0.18,X2不变;或X1变小,X2变大,变化范围0~0.09。假定齿轮啮合角不变,按本文实验样机参数,当齿轮变位系数发生变化时,其变化量对重合度的影响状况见图3.2所示。从图3.2所示可以看出,随外齿轮变位变小时,齿轮啮合重合度减小,随内齿轮变位变小时,齿轮啮合重合度增大,从图中的变化趋势为看,外齿轮变位系数的变化对重合度的影响程度与内齿轮变位系数的变化对重合度的影响程度大约是相同的,只是趋向是反向的。
对于中心距而言,查资料表35.2-60可知中心距的极限偏差为±0.011mm,假定外齿轮齿顶圆压力角不变,内齿轮齿顶圆压力角随变位系数变化,对于中心距变化对重合度的影响变化趋势及变位系数变化对重合度的影响的变化趋势比较情形见图3.3。假定内齿轮齿顶圆压力角不变,外齿轮齿顶圆压力角随变位系数变化,对于中心距变化对重合度的影响变化趋势及变位系数变化对重合度的影响的变化趋势比较情形见图3.4所示。

从图3.3、3.4明显看出中心距变化对重合度的影响程度明显小于变位系数变化对重合度的影响程度。
齿轮制造误差中对齿廓间隙影响较大的有最小齿侧间隙、基节偏差、齿形误差、齿距偏差、齿厚偏差等等,但这些因素相互关联、相互制约、相互影响,特别是基节偏差、齿形误差、齿距偏差、齿厚偏差等最终影响齿侧隙的变化,因此最终影响齿轮传动的主要因素仍是中心距和齿侧隙的变化。分析图3.2、3.3、3.4,在允许的制造误差范围内及最小齿侧隙的情况下,重合度的理论计算值变化不是很大。
3.1.2 接触分析中制造安装误差的引入
从上述分析可知,齿轮的制造、安装误差对齿轮啮合的重合度有一定的影响,但就理论计算值而言,从上面的分析结果可以看出其影响程度是不大的,然而在少齿差内啮合齿轮副中,啮合线附近两相邻工作齿对齿侧间隙非常小。假设内齿轮固定,当轮齿承担载荷时,两接触轮齿将分别产生弹性变形,外齿轮将绕其轴线旋转一附加角,当这一附加转角足够大时,除原有接触齿对继续发生接触外,相邻工作齿对的齿侧间隙也会消失,这样就产生了多齿承载接触。
在本节中,引入制造、安装误差,用有限元方法计算内齿传动的接触对数,同时验证上节中讨论的影响重合度的关键参数。用I-DEAS软件计算环板内齿接触问题,其关键是齿轮轮齿的实体建模。对于相啮合的齿轮,因其两工作齿廓侧面相互位置误差的变化导致了实际齿廓间隙的变化,在啮合线附近只有少数几对齿在我们讨论范围内,这里我们只考虑对齿廓间隙影响较大的最小齿侧间隙、基节偏差、齿形误差、齿距偏差、齿厚偏差等。在用用I-DEAS软件进行齿轮轮齿的实体建模时,对轮齿而言,沿圆周是均匀分布的,因此,齿轮的制造误差在实体造型时,表现在齿轮轮齿的齿厚及基圆尺寸的误差上。而经多元回归分析,得出各变量对齿廓间隙的内在影响关系表明:齿轮的基节偏差是最主要的影响因素。
本文双环减速器齿轮加工精度为7级,根据资料,查得齿轮的基节极限偏差△fpb为±0.014,对于齿厚极限偏差,根据资料,查得齿轮齿厚的极限偏差△Es的上偏差为-128μm,下偏差为-192μm,将这些影响因素的极限偏差,通过几何关系的转换,换算到基节上,通过参数方程绘出齿轮单个轮齿的轮廓线,再由单个轮齿的齿廓沿圆周接齿轮齿数均匀复制,这样得到整个齿轮的齿廓线,由齿廓线延伸成齿轮实体模型。
由于零部件的制造误差,同时因装配原因,在进行整体装配时,产生零部件间的安装误差,这些误差直接影响齿轮间的啮合状态。对于双环减速器中的环板内齿轮啮合传动,由于环板内齿中心与输出齿轮中心之间的偏心距尺寸较小(本文双环减速器的偏心距为2.42mm),因此,偏心轴的偏心距制造误差及中心距制造安装误差是影响环板内齿啮合传动的关键。本文双环减速器两偏心轴偏心距的制造误差为±0.011。
综合以上误差分析,将环板与输出齿轮轴按极限偏差尺寸所定的位置进行轮齿啮合装配,然后进行有限元接触分析。
3.1.3 齿轮有限元模型的建立及边界条件的确定
环板内齿轮与输出轴齿轮之间的传动是直齿轮传动,为保证进行接触计算时,有较多的有较接触区域,齿轮轮齿部分的有限元网格采用映射网格划分法(Mapped Meshing)对齿轮进行有限元网格划分。同时,为保证两对啮合齿轮所划分的网格接触对相应的面能对应齐,因此齿轮啮合的接触面相应应当齐整。用输出轴齿轮的齿顶面所在的轮廓曲面对环板内齿进行划分(partition 命令),同理用环板内齿的齿顶面所在的轮廓曲面对输出轴齿轮进行划分,这样得到对应齐整的齿轮啮合的接触面,如图3.5所示。根据图3.5所示,采用映射网格划分法( Mapped Meshing)进行网格划分的轮齿部分即是图中输出齿轮齿顶圆与环板内齿齿顶圆之间所划分的部分,而其余部分采用自由网格划分法(Free Meshing)进行划分,划分网格后的部分网格图见图3.6所示。考虑实际接触齿对数不会太多,所以每块环板上只给出6个轮齿进行接触计算。环板啮合的实际过程是环板齿轮带动输出齿轮运动,计算时为方便,假设环板固定不动,设定输出轴绕轴线转动,将减速器的输出功率换算为输出扭矩,加在输出轴的输出端。
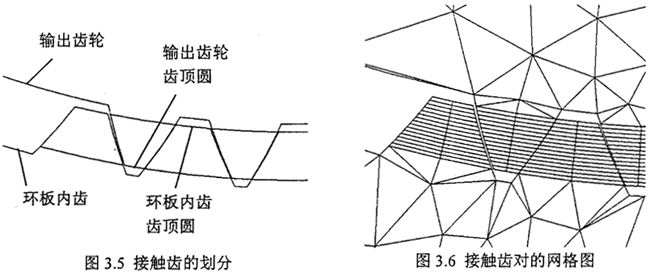
3.1.4 接触计算结果分析
按考虑偏心距误差影响及考虑齿厚误差影响的两个极限状态,组合为十种情况进行计算。十种计算工况见表3.2所示。考虑齿厚误差影响的两个极限状态分别是齿轮的轮齿最薄、最厚,偏心距误差的两个极限状态分别是偏心轴的偏心距最大、最小两种情况。种接触情况的计算结果分别由表3.3~3.7列出。
3.2计算工况列表
序号 |
工况说明 |
序号 |
工况说明 |
齿厚状态 |
偏心距状态 |
两环板状态 |
齿厚状态 |
偏心距状态 |
两环板状态 |
1 |
最厚 |
无误差 |
对称 |
6 |
最薄 |
最大正偏差 |
对称 |
2 |
最薄 |
无误差 |
对称 |
7 |
最厚 |
最大负偏差 |
不对称 |
3 |
最厚 |
最大负偏差 |
对称 |
8 |
最薄 |
最大负偏差 |
不对称 |
4 |
最薄 |
最大负偏差 |
对称 |
9 |
最厚 |
最大正偏差 |
不对称 |
5 |
最厚 |
最大负偏差 |
对称 |
10 |
最薄 |
最大正偏差 |
不对称 |
3.4工况一接触情况计算表
误差情况 |
载荷(N·m) |
接触齿对数 |
最大接触应力(MPa) |
环板1 |
环板2 |
工况一 |
200 |
1 |
1 |
75.2 |
160 |
1 |
1 |
66.8 |
120 |
1 |
1 |
56.1 |
80 |
1 |
1 |
41.1 |
40 |
1 |
1 |
28.0 |
3.5工况二接触情况计算表
误差情况 |
载荷(N·m) |
接触齿对数 |
最大接触应力(MPa) |
环板1 |
环板2 |
工况二 |
200 |
1 |
1 |
75.2 |
160 |
1 |
1 |
66.8 |
120 |
1 |
1 |
56.1 |
80 |
1 |
1 |
41.1 |
40 |
1 |
1 |
28.0 |
3.6工况三接触情况计算表
误差情况 |
载荷(N·m) |
接触齿对数 |
最大接触应力(MPa) |
环板1 |
环板2 |
工况三 |
200 |
1 |
1 |
68.2 |
160 |
1 |
1 |
62.6 |
120 |
1 |
1 |
55.1 |
80 |
1 |
1 |
40.2 |
40 |
1 |
1 |
25.3 |
3.7工况四接触情况计算表
误差情况 |
载荷(N·m) |
接触齿对数 |
最大接触应力(MPa) |
环板1 |
环板2 |
工况四 |
200 |
2 |
2 |
74.6 |
160 |
2 |
2 |
62.1 |
120 |
2 |
2 |
49.0 |
80 |
2 |
2 |
41.8 |
40 |
1 |
1 |
26.6 |
3.8工况五接触情况计算表
误差情况 |
载荷(N·m) |
接触齿对数 |
最大接触应力(MPa) |
环板1 |
环板2 |
工况五 |
200 |
2 |
2 |
2.2 |
160 |
2 |
2 |
58.6 |
120 |
2 |
2 |
45.6 |
80 |
2 |
2 |
42.1 |
40 |
1 |
1 |
26.5 |
3.9工况六接触情况计算表
误差情况 |
载荷(N·m) |
接触齿对数 |
最大接触应力(MPa) |
环板1 |
环板2 |
工况六 |
200 |
1 |
1 |
76 |
160 |
1 |
1 |
63.2 |
120 |
1 |
1 |
49.7 |
80 |
1 |
1 |
40.5 |
40 |
1 |
1 |
28.5 |
3.10工况七接触情况计算表
误差情况 |
载荷(N·m) |
接触齿对数 |
最大接触应力(MPa) |
环板1 |
环板2 |
工况七 |
200 |
1 |
3 |
76 |
160 |
0 |
2 |
63.2 |
120 |
0 |
2 |
49.7 |
80 |
0 |
1 |
40.5 |
40 |
0 |
1 |
28.5 |
3.11工况八接触情况计算表
误差情况 |
载荷(N·m) |
接触齿对数 |
最大接触应力(MPa) |
环板1 |
环板2 |
工
况
八 |
200 |
1 |
2 |
130.0 |
160 |
0 |
2 |
114.0 |
120 |
0 |
2 |
93.4 |
80 |
0 |
2 |
70.2 |
40 |
0 |
2 |
39.0 |
3.12工况九接触情况计算表
误差情况 |
载荷(N·m) |
接触齿对数 |
最大接触应力(MPa) |
环板1 |
环板2 |
工
况
九 |
200 |
2 |
1 |
104.0 |
160 |
2 |
0 |
92.6 |
120 |
2 |
0 |
86.6 |
80 |
2 |
0 |
65.3 |
40 |
1 |
0 |
42.8 |
3.13工况十接触情况计算表
误差情况 |
载荷(N·m) |
接触齿对数 |
最大接触应力(MPa) |
环板1 |
环板2 |
工
况
十 |
200 |
2 |
1 |
136.0 |
160 |
2 |
0 |
117. |
120 |
2 |
0 |
102.0 |
80 |
2 |
0 |
77.4 |
40 |
2 |
0 |
47.6 |
由表3.2~3.13可以看出,无论有无制造、安装误差的影响,随着负荷的增加,齿轮实际啮合接触对数增加,但从计算结果分析证明,负荷对接触对的影响小于误差对接触对的影响。对比表中的接触对数和接触应力,数据表明当齿厚发生变化时,实际接触齿对数变化比较大,同时最大接触应力也有明显变化。从变化的趋势上看出与前面的理论推导变化趋势相同,这里只是更加明显。
工况六至工况十这四和情况,是指两环板之间不对称,即偏心轴的两个偏心拐的尺寸误差不一致,这里考虑的是特殊状况,从表3.10-3.13看出,当两环板不对称时,将产生严重的载荷不均现象,载荷偏向中心距小的环板内齿上,甚至只有一个环板承受载荷。由此说明,对于双环减速器偏心轴有加工,应特别注意两曲捌的制造误差,应尽量使安装好的两环板具有较好的对称性。图3.7~图3.12为六种工况下环板内齿的接触齿对的应力云图。
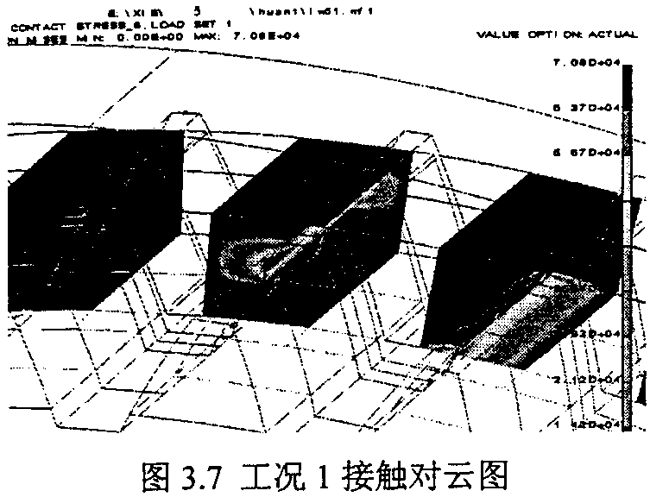
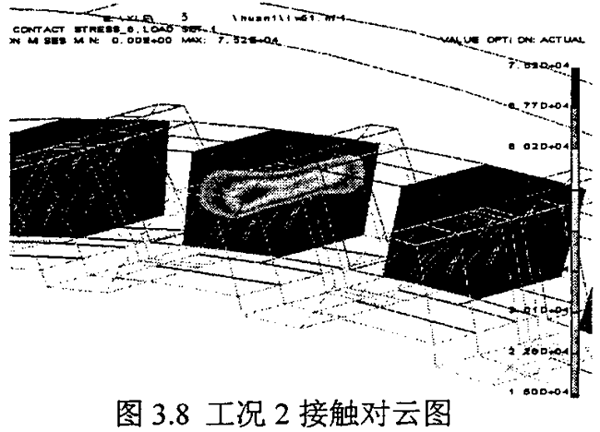
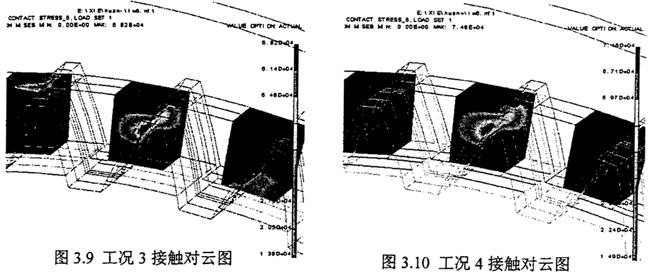

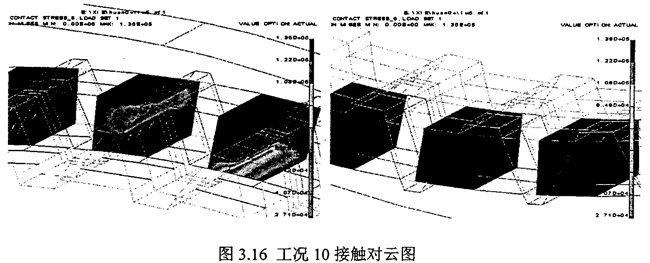
3.2 双环减速器有限元模型建立及模态分析
近年来,随着齿轮振动噪声研究的不断深入,不仅需要考虑齿轮系统及其啮合过程,还必须考虑动态啮合力在整个齿轮系统中的传递,以及系统中各零部件的固有特性和动态响应的性质,因此,必须以整个齿轮系统为研究对象,建立同时包括传动系统和结构系统的完整系统的分析模型。本节将在双环减速器运动特性分析的基础上,以整个双环减速器齿轮系统为对象,建立有限元动力分析模型,全面分析该系统的固有特性和动态响应。
齿轮系统的固有特性一般指系统的固有频率和固有振型,是齿轮系统的动态特性之一,它对系统的动态响应,动载荷的产生与传递,以及系统振动的形式等都具有重要意义。此外,固有特性还是用振型叠加法求解系统响应的基础。由于系统的固有特性表明了在哪些频率下结构会产生共振以及在各阶频率下结构的相对变形,因此对于改善结构动态特性具有重要意义。通常,研究齿轮系统固有特性有理论计算法和实验测试法两种。实验测试将在以后的章节中研究,本章将利用数值计算法计算双环减速器齿轮系统的固有特性。结构系统固有特性的数值计算通常采用有限元模态分析方法。在有限元分析中,结构的动力学特征用微分方程组表征,则结构的固有频率和固有振型相应地由动力学方程的特征值和特征向量所确定。所以可以说,求系统的固有频率和固有振型即为求系统的特征值和特征向量。特征值问题的解法很多,主要有多项式割线迭代法、矢量逆迭代法、广义雅可比法、子空间迭代法和行列式收缩法。动力问题有限元法是求解复杂结构的大型动力学方程组的特征值问题的有效方法。本章将用动力有限元法对双环减速器齿轮系统进行特征值分析,计算其固有频率和固有振型。
本文建立了齿轮系统的有限元动力学模型,用I-Deas 集成化软件的固有模态求解模块求解了齿轮系统的固有频率和振型,并用响应动力(Response Dynamios)分析模块研究了齿轮传动系统的动态响应特性。要进行有限元模态分析,必须先建立齿轮系统的有限元力学模型。
上一页
下一页