第6章 圆柱正弦活齿减速器的加工及试验研究
6.1圆柱正弦活齿减速器样机的加工制造
圆柱正弦活齿减速器是为适应航空航天、石油开采等特种工作环境的需要,而自行开发研制的一种微小型活齿传动装置。本文经过空间啮合理论、强度及动力学特性分析等一系列理论研究,对圆柱正弦活齿减速器进行了多目标动态优化设计,最终研制出一台最大外径为φ80mm,传动比为5,输出扭矩为20N·m的微小型减速器样机。
由圆柱正弦活齿减速器的结构组成可知,其中大部分结构都是常用的零件,故可用传统的加工方法及通用的加工设备进行加工制造。而壳体及主动轴的内、外空间正弦滚道的加工制造是该减速器制造的关键技术及难点,它们加工精度的高低及质量好坏直接影响着该活齿传动的传动性能。由于内、外正弦滚道为空间齿廓曲面,形状复杂,要求加工刀具不但要有x,y,z三个方向的进给运动而且还要求刀具主轴能绕y,z轴转动,因此无法在普通铣床上加工制造,需要依靠五轴数控(NC)机床来实现并保证滚道加工的精度和质量。
数控(NC)机床是装有程序控制系统的机床,该系统能够逻辑地处理具有使用编码或其他符号指令规定的程序。而同时具备自动换刀功能及自动判断被加工件上多个表面功能的NC机床,称为加工中心。数控机床具有如下特点:能加工复杂型面零件;加工精度高,加工过程中,能在一次装夹定位中加工多个表面,并能完成自动检测等工序,有效的提高了生产效率;自动化程度高;可以实现一机多用;采用数控机床,促进了单件、小批量生产自动化的发展,实现柔性自动化生产;只需更换程序,采用通用工夹具,就可适用不同品种及尺寸规格零件的自动化生产。基于以上特点,对于单件、中小批量生产,形状复杂、精度要求高的零件加工采用数控机床生产,可以提高产品质量,降低生产成本,获得较高的经济效益。
本课题利用瑞士米克朗公司生产的UCP1350五坐标数控加工中心进行空间正弦滚道的加工(如图6-1),瑞士米克朗公司于1908年成立于瑞士比尔,是世界著名的精密机床制造商,在机加工领域积累了数十年的经验。多年来,米克朗公司始终保持着在制造五轴联动加工中心方面的领先地位,并投入了大量的力量用于发展铣削技术,不断推出新型的高速高性能加工中心。其中五轴联动加工中心为复杂零件的加工提供了解决之道,一次装夹可实现多面加工以及一坐标联动加工,提高了加工精度和加工效率。加工中心主轴铣削加工时最高转速为12000rpm,磨削加工时为10000rpm。
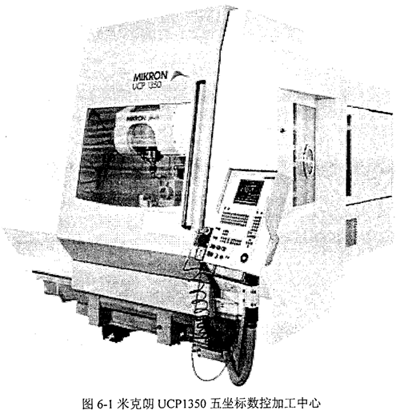
UCP1350采用了新的海登海因HeidenhainTNC426M数控系统。此系统支持海登海因纯文本和DIN或ISO语言进行车间现场编程,并支持并行模式,当机床在加工工件时,可进行其他程序的编制,通过“固有程序操作”功能,控制系统能对未经数控方式定义的工件进行编程工作。内外空间正弦滚疲道的数控加工程序参见附录。
由于圆柱正弦活齿减速器径向尺寸小,在现有国产铣刀的条件下,加工壳体的内空间正弦滚道具有很大的难度,本文提出一种加工方案,较好的解决了这个难题。采用五坐标数控加工中心,将球状铣刀倾斜一定角度,斜插进壳体内圆柱面进行铣削加工,其加工位置示意图如图6-2。
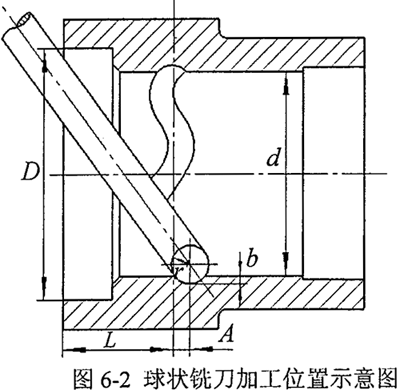
由于球状铣刀的刀刃部分为半球头形状,为避免球头铣刀的刀柄与壳体内壁发生干涉,导致内空间正弦滚道被铣削出平面,则空间正弦曲线的平衡位置到壳体端面的距离L应满足一定的条件,由图6-2中各参数的关系,可以得到

根据空间正弦滚道的形成原理,铣刀中心沿空间正弦轨迹曲线运动的同时,刀具自身作旋转运动,并沿径向方向进给运动加工出滚道槽深,则铣刀的刀刃包络出内外空间正弦滚道的齿廓曲面,也即完成了空间正弦滚道的铣削工艺。
为保证空间正弦滚道的加工精度,工件经过车削、铣削及高频淬火等工艺流程后,必须对空间正弦滚道进行精磨。对内空间正弦滚道的磨削是比较困难的工艺流程,本文根据滚道及壳体内圆柱面的形状尺寸,进行了非标球头磨具的设计。该非标球头磨具的材质选用金属基立方氮化硼(CBN),CBN浓度为100%,粒度为80目。其制造的工艺流程为:将立方氮化硼颗粒溶入液化的金属基(铜)中,浇注在特定的模具中,冷却凝固后,将金属基CBN球头与钢质刀柄用银焊接在一起,最后采用电火花工艺将球头按一定精度加工成型,由此更好的保证了球头磨具的型位公差。为防止磨削时产生的积屑降低磨具的磨削硬度及精度,在磨具的球头部位还设计有排屑槽。加工成型后的金属基CBN球头磨具见图6-3。最终加工成型的主动轴、导架、壳体、其它关键件及装配后的减速器样机见图6-4~图6-8。
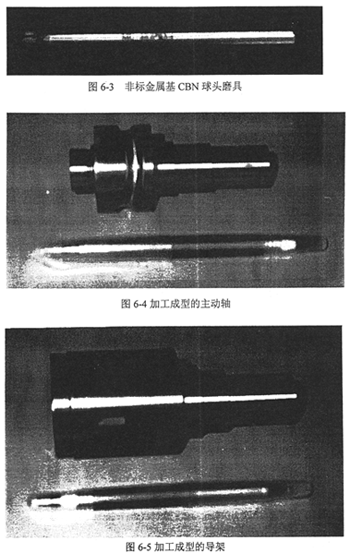
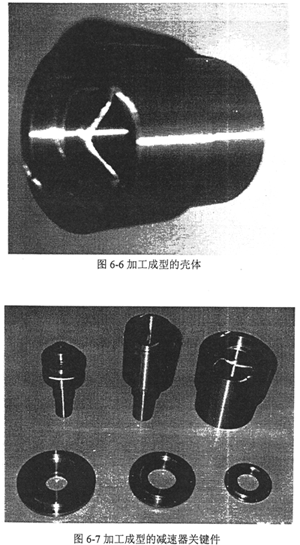
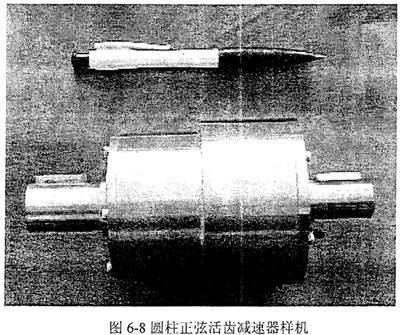
6.2传动效率试验研究
6.2.1试验原理
机械传动件的性能是工程界十分重视的一个问题,它直接影响产品成本及能源消耗,每个设计师都希望自己设计的机器是一台高效率,噪声低,振动小,温升低的机械。但是,由于机器结构等因素的影响,实际机器很难达到理想的计算效率及其它设计参数,实际机器效率受加工精度和装配精度及使用条件等因素影响将低于计算效率,这就需要进行试验研究,以测量实际机器的效率值和与其相关的参数,给传动装置的选择及改进设计提供数据。为此,本文对圆柱正弦活齿减速器样机进行了传动比及传动效率试验研究,试验装置的工乍原理如图6-9所示。试验台的实物照片如图6-10所示。
试验台采用直流电动机驱动,磁粉制动器作为加载装置,电动机通过调节稳流电源电流控制磁粉制动器加载转矩的大小。为了方便准确的测定减速器的传动效率,在试验台的输入端与输出端各安装一台磁电式转矩转速传感器,传感器将输入输出轴上的转矩和转速变成电信号,并由转矩转速测量仪显示出输入轴转矩M1、转速n1、功率P1及输出轴的转矩M2、转速n2、功率P2的测量值。则被测减速器的传动效率为
η=P2/P1 (6-2)
式中 P1——输入、输出功率
。
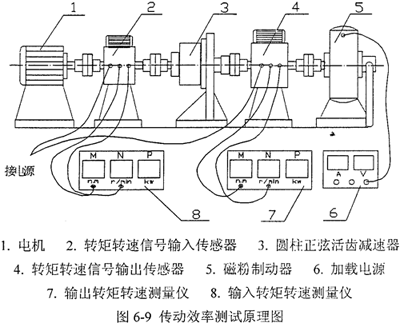

6.2.2扭矩转速测量装置
试验台为了同时测量转矩和转速,需使用可同时测量两种物理量的传感器。目前常用磁电式传感器来同时测量转速转矩,其根据磁电转换和相位差原理,将转矩,转速机械量转换成两路有一定相位的电压讯号,能直接测量各种动力机械的转矩与转速,具有测量精度高(误差±0.2%),操作简便,显示直观,测量范围广等优点,可以测量轴静止状态至额定转速范围的转矩,它输出功率大且性能稳定,具有一定的工作带宽,因而得到普遍应用。
图6-11为磁电式相位差型转矩转速传感器的结构示意图,它由机座、端盖、扭力轴、内齿轮、外齿轮、磁钢、线圈轴承等组成。内齿轮、磁钢固定在套筒上,线圈固定在端盖上,外齿轮固定在扭力轴上,当内外齿轮发生相对转动时,由于磁通不断变化,在线圈中便感应出近似正弦波的感应电势ul、u2,两感应电势的初始相位差是恒定的,考虑到正反加载,φ0设计在大约180°位置上,当加上扭力时,扭力轴发生扭转变形,在弹性范围内外加扭矩与机械扭转角成正比,这时ul、u2讯号的相位差要发生变化,即
φ=φ0±△φ (6-3)

当传感受器的扭矩增加到额定值时,变化的相位△φ大约为90°。因此,测量出φ就等于间接测量出轴上的外加转矩,这样,传感器就实现了把机械量的扭角变化转化成电子量的相位差变化的过程。
6.2.3试验加载装置
采用磁粉制动器作为试验的加载装置。磁粉制动器由转子、机壳、激磁线圈、磁粉组成,其结构如图6-12所示。在激磁线圈不通电流时,不产生磁通,磁粉呈自由状态。当轴转动时,由于离心力的作用,使磁粉散布在转动件与机壳之间,若此时激磁线圈通电流,则在线圈周围产生磁场,转动件与机壳间的磁粉沿磁通方向连接成链状,由于磁粉间的结合力,使工作面之间产生摩擦力,从而形成制动力矩,起到加载的作用。该力矩与激磁电流的大小基本成正比,故通过调节激磁线圈的电流大小可在一定范围内改变制动力矩的大小。
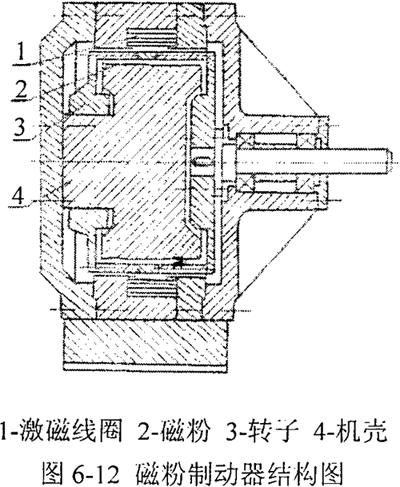
6.2.4试验结果分析
进行减速器效率试验前,首先让减速器在输入转速为500rpm的条件下,空载跑合4个小时,观察运转正常后,进入试验的准备阶段。为测得准确试验数据必项对转矩转速测量仪进行常数输入和转矩调零设置,一切准备完毕后,开始对减速器进行试验测试。当输入轴转速取不同值时计算出减速器样机的传动比及样机总评传动比如表6-1所示,通过分析测试数据可知,经实测最大的传动比误差为-0.0148,平均传动比误差为-0.0078。表明样机的传动比准确,传动精度高。经分析可知,正弦滚道的加工精度是造成整机传动误差的主要原因。
表6-1 传动比测试结果
输入转速(rpm) |
400 |
500 |
600 |
700 |
800 |
900 |
1000 |
1200 |
1500 |
传动比平均值 |
输出转速(rpm) |
81.2 |
100.5 |
120.2 |
140.7 |
161.1 |
182.3 |
202 |
241.8 |
305 |
4.961 |
传动比 |
4.926 |
4.975 |
4.99 |
4.965 |
4.969 |
4.945 |
4.95 |
4.963 |
4.967 |
当输入转速为500rpm时,通过磁粉制动器对减速器施加不同的载荷值,得到一系列输入输出转矩、输入输出功率及效率如表6-2所示。
表6-2 传动效率测试结果
输入转矩(N·m) |
0.325 |
0.426 |
0.52 |
0.628 |
0.712 |
0.81 |
0.923 |
效率平均值 |
输入功率(w) |
17 |
22.3 |
27.2 |
32.9 |
37.3 |
42.4 |
48.3 |
输入转矩(N·m) |
1.493 |
1.975 |
2.423 |
2.933 |
3.336 |
3.811 |
4.352 |
输入功率(w) |
15.6 |
20.7 |
25.4 |
30.7 |
34.9 |
39.9 |
45.6 |
效率η |
0.919 |
0.927 |
0.932 |
0.934 |
0.937 |
0.941 |
0.943 |
0.933 |
同样方式测得当输入转速分别为700rpm、900 rpm、1100 rpm、1300 rpm、1500 rpm时,减速吕样机的平均效率随输入转速变化曲线如图6-13。通过测试结果表明,在低中速情况下,减速器的传动效率受其转速的影响不明显,由于此时润滑脂温度较低,随着转速的增加,减速器的传动效率略有提高,其平均值在93%以上,由引说明本文设计的减速器具有较高的传动效率。
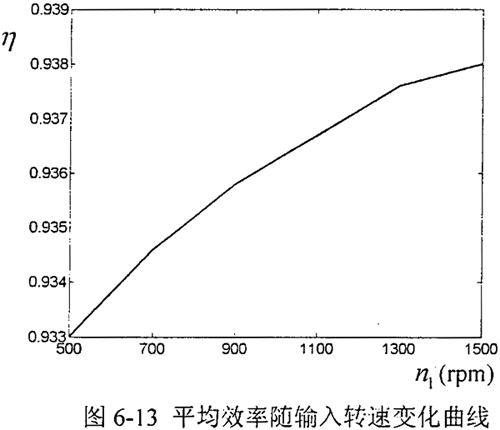
6.3本章小结
1.在理论分析的基础上,经过多目标优化设计,最终确定减速器的结构参数,并绘制出减速器的装配图和零件图。与哈尔滨建成集团合作加工制造出一台样机;
2.提出在小半径内圆柱面上加工空间正弦滚道的方法,为提高加工精度,设计并制造出非标CBN球头磨具;
3.设计了试验方案,设计、加工了与该减速器配套的试验辅助装置,验装了试验台。通过试验结果表明,该减速器具有较高的传动精度和传动效率。
上一页
下一页