第3章 滚柱活齿减速器的设计及计算机辅助分析
3.1引言
本章在活齿传动理论分析的基础上,针对井下驱动螺杆泵采油系统的实际技术要求,设计最大外径114mm、传动比为9、工作井深1000m的滚柱活齿减速器以满足油田生产需要。
首先,给出根据滚柱活齿传动的运动条件和强度条件设计减速器的方法,并根据这些约束条件初步确定减速器的参数。为准确验证所设计的减速器能否实现预定的设计要求,本章拟采用有限元分析的方法,针对减速器关键零件进行静力学分析和模态分析,以验算其强度是否满足要求,确定输入、输出轴正常工作时能否受激共振。
同时,为避免样机加工后发现问题而造成损失,缩短设计周期,在样机设计完成后,拟采用虚拟样机仿真技术对其进行运动学仿真,以验证其能否实现确定的相对运动。仿真成功后,绘制出全部零件图和装配图并加工样机。
3.2 减速器结构的设计
为简化样机结构,将波发生器与输入轴设计成一个零件,统称输入轴。将中心轮固定,选择输入轴和输出轴旋转方向相同。由于波发生器部分属偏心结构,工作时要承受很大的径向力,为改善支承的受力情况,采用双排相差为180°的滚柱活齿结构,不但使惯性力和惯性力矩完全平衡,而且保证整机的啮合力和啮合力矩平衡。
由于中心轮内齿面要同时与相差为180°的两排活齿啮合而且中心轮的齿形加工采用线切割工艺,所以中心轮沿轴线上各截面形状应保持一致。确定采用的结构后,根据运动条件和强度条件初步确定减速器的具体参数。
3.2.1 运动条件
3.2.1.1 中心轮理论齿廓曲线不顶切条件 由于中心轮理论齿廓曲线是滚柱活齿中心运动轨迹的等距线,所以当滚柱活齿中心运动轨迹的最小曲率半径ρmin≥r2时,活齿可以顺利地通过中心轮的齿顶;当ρmin≤r2时,中心轮的理论齿廓曲线要发生顶切现象,从而使传动终止,据此可写出中心轮理论齿廓曲线不顶切条件:
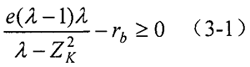
式中e——波发生器偏心圆的偏心距;
λ——激波系数,λ=(r1+r2)/e;
r1——波发生器半径;
ZK——中心轮齿数;
r2——滚柱活齿半径。
连续的齿廓曲线有传动平稳、参与啮合的齿数多等优点,所以设计活齿传动时,一般总是希望得到连续的齿廓曲线,即使之满足式(3-1)。
3.2.1.2 偏心距e和径向间隙c是活齿减速器的重要参数,减速器的结构形式和传动比不同,偏心距e和径向间隙c 的值也不同,其取值应按表3-1中的参数优先选取。
表3-1 径向间隙c、偏心距e的优选值(mm)
偏心距 |
0.65 |
0.75 |
0.85 |
1 |
1.25 |
1.5 |
1.75 |
2 |
2.5 |
3 |
3.5 |
4 |
径向间隙 |
0.9 |
1.0 |
1.1 |
1.2 |
1.3 |
1.4 |
1.5 |
1.6 |
1.7 |
1.8 |
1.9 |
2 |
偏心距 |
4.5 |
5 |
5.5 |
6 |
6.5 |
7 |
7.5 |
8 |
9 |
10 |
11 |
12 |
径向间隙 |
2.1 |
2.2 |
2.3 |
2.4 |
2.5 |
2.6 |
2.7 |
2.8 |
2.9 |
3 |
3.1 |
3.2 |
3.2.1.3 滚柱活齿连续传动条件 为保证活齿在工作开始位置(中心轮齿顶)传动连续,活齿在与中心轮齿顶接触的同时,与活齿架应保持接触。由几何条件可知,活齿架内圆半径最大值即活齿工作起始位置连续传动条件为:
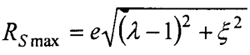
式中 ξ——活齿系数,ξ=rb/e;
RSmax——活齿架内圆半径最大值。
活齿架内表面和波发生器外轮廓面之间不应该发生运动干涉,不发生运动干涉的条件为:
RSmin=e(1+λ-ξ)
式中RSmin——活齿架内圆半径最小值。
上两式联立,可求出活齿架内圆半径RS的尺寸范围,见式(3-2)。

同样方法可得活齿工作结束位置(中心轮齿根)连续传动条件:

式中RMmin——活齿架外圆半径最小值。
活齿架外表面和中心轮的齿顶不发生运动干涉的条件:

式中RMmax——活齿架外圆半径最大值。
上两式联立,可求出活齿架外圆半径RM的尺寸范围,见式(3-3)。

3.2.1.4 活齿架的最小壁厚 联立活齿工作起始位置和结束位置时的连续传动条件,可得活齿架薄壁筒的最小壁厚为:

3.2.2 强度条件
3.2.2.1 活齿与波发生器间表面接触疲劳强度
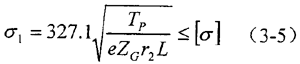
式中TP——波发生器的输入力矩,N·m;
ZG——活齿数;
L——活齿工作宽度,m;
[σ]——考虑寿命、载荷等因素的许用应力,[σ]=1423MPa。
3.2.2.2 中心轮接触疲劳强度

式中ρ——综合曲率半径,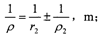
ρ2——取中心轮齿廓曲率半径最小值,m;
E——弹性模量,2.06×1011N/m2;
FKmax——活齿对中心轮的作用力,N。
在齿根附近(拐点以下)啮合时,综合曲率半径ρ中取减号,在齿顶附近(拐点以上)啮合时,综合曲率半径ρ中取加号。
3.2.2.3 活齿架接触疲劳强度和剪切强度 剪切强度为:
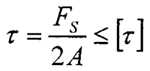
式中A——每个活齿槽的横截面积,A≈2r2(RM-RS);
FS——活齿对活齿架作用力,N;
[τ]——许用剪应力,MN/m2。
接触疲劳强度:
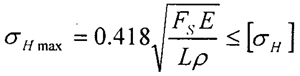
式中E——弹性模量,2.06×1011N/m2。
首先根据上述运动条件初步确定几何参数,然后采用强度条件校核。经分析可知,参数可行域很小,考虑到波发生器偏心距e、径向间隙c等参数需圆整为表3-1中的优选值,初步确定主要参数如下:波发生器偏心距e=1.5mm,波发生器半径r1= 30mm,r2=8mm,活齿数ZG=9,中心轮齿数ZK=8,活齿工作宽度L=60mm。
3.3 滚柱活齿减速器有限元强度分析和模态分析
有限元法(FEM)是一种采用计算机求解结构静、动态力学特性等问题的数值解法,现己广泛应用于结构、热、电磁场、流体等分析领域,成为现代机械产品设计中的一种重要工具。当前,国际上最权威的大型商用有限元分析软件是美国ANSYS公司的ANSYS软件。
进行有限元分析,首先要建立被研究对象的实体模型。ANSYS提供了三种方法创建实体模型:自下而上法(Bottom-up)、自上而下法(Top-down)和从其他CAD系统导入法。
自下而上法是先创建关键点,然后依次创建相关的线、面和体等图元。自顶而下法是可以直接创建最高级的图元,即几何体素。当用户定义了一个体素时,程序会自动定义相关的面、线和关键点。用户可以利用这些高级图元直接构造几何模型。在ANSYS建模过程中,自顶而下的建模方法和自底而上的建模方法是可以自由组合使用的,从而使模型的创建更加方便。
另外,ANSYS提供了与其他CAD系统的强大接口,用户也可以在擅长的CAD系统里建立实体模型,然后把该模型以某一种格式导入到ANSYS中,一旦模型成功导入后,就可以象在ANSYS 中创建的模型那样对此模型进行网格划分。这些接口程序是由ANSYS公司或CAD供应商编写的软件。由ANSYS公司可以得到下列软件的译码器;AutoCAD、CADAM、CADKEY和Pro/ENGINEER 。
其中值得注意的是ANSYS-Pro/ENGINEER接口,因为它提供了以执行部件为基础的参数化优化设计的功能。该功能允许由部件为基础的参数化Pro/ENGINEER模型开始,用ANSYS程序对其进行优化,并以一个优化的Pro/ENGINEER 模型结束,且仍是以部件为基础的参数化模型。
3.3.1 减速器三维实体模型的建立
无论进行有限元分析还是虚拟样机仿真,都要求首先建立减速器的三维实体模型。虽然ANSYS 在有限元分析方面技术领先,但其在三维实体建模方面并不比专业的CAD系统方便,甚至对于复杂的实体模型还要借助第三方软件才能完成。由于滚柱活齿减速器的中心轮和活齿架等零件的实体特征较复杂,故考虑采用第三方软件来完成。
工程用三维实体建模软件主要有Pro/ENGINEER、Ideas、UG等。其中美国PTC公司开发的Pro /ENGINEER 是世界上第一个基于特征的参数化实体建模软件,其在三维建模、尤其是复杂曲面的造型方面处于领先水平。所以减速器拟采用Pro/ENGINEER进行建模。
无论进行有限元分析还是虚拟样机仿真,我们只需研究与减速器工作直接相关的波发生器、活齿、活齿架和中心轮等关键零件,而忽略端盖、端套、轴承等辅助零件,据此建立减速器三维实体模型及其分解图见图3-1和图3-2。
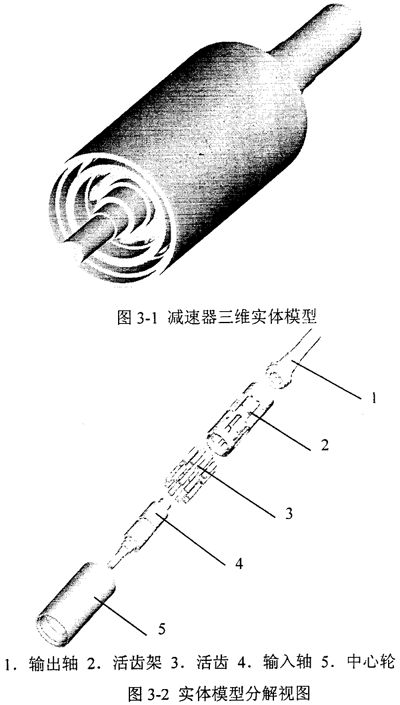
3.3.2 减速器关键件的有限元强度分析
3.3.2.1 活齿架的强度分析 采用平台为Pentium IV 1.7GHz CPU 、128MDDR SDRAM内存、NVIDIA Geforce2 MX/MX4OO显卡、Windows XP操作系统和ANSYS5.7 软件进行分析求解。
将Pro/ENGINEER中创建的活齿架模型以IGES格式导入ANSYS中,并作适当拓扑修补,以完成预处理中实体模型的建立。
根据问题的性质和模型的复杂程度,选用Solid95单元(见图3-3)。该单元是三维的20个节点的结构单元,可以在保证计算精度的前提下允许实体中不规则的形状存在。每个节点存在三个自由度:X、Y和Z方向的移动,可应用于塑性、脆性、大变形和大应变等问题。

设定材料属性为线性各向同性、杨氏模量为2.06×1011N/m2、泊松比为0.3,采用自由网格划分并设定划分网格精度为7。在每个工作活齿所在活齿槽中分别加载4400N,限制输出端节点的全部自由度,划分网格并加载后的有限元模型见图3-4。求解后,在后处理中各节点的总位移等值图见图3-5,最大位移在节点688处,值为0.71μm。各节点的综合应力等值图见图3-6,其中最大综合应力在节点69处,大小为599846N/m2,小于许用应力。
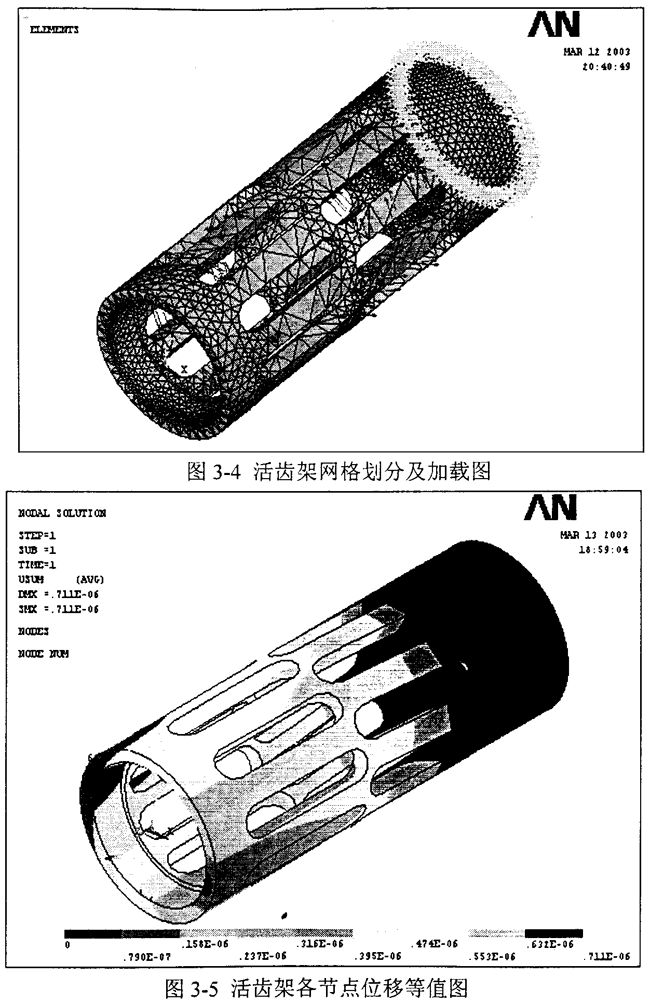
3.3.2.2输入输出轴的强度分析 同样将Pro/ENGINEER中创建的输入轴和输出轴模型以IGES格式导入ANSYS中,并作适当拓扑修补,完成预处理中实体模型的建立。
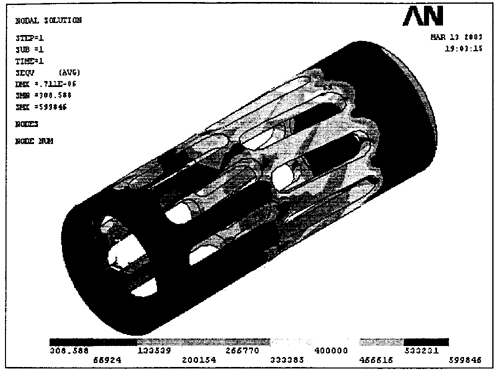
全面考虑计算精度与计算机资源,选用Soild45单元(图3-7 ),该单元有8个节点,每个节点有X、Y和Z三个方向的自由度。同样设定材料属性,采用自由网格划分并设定划分网格精度为9。对输入轴限制输入端节点的全部自由度,在另一端施加工作扭矩,划分网格并加载后的有限元模型见图3-8。求解后,得各节点的总位移等值图见图3-9,最大位移在节点420处,值为0.254mm。
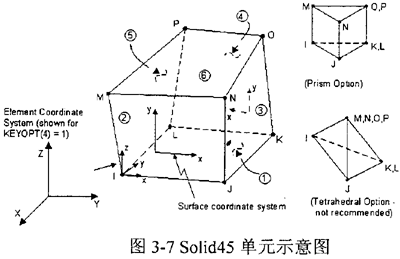
各节点的综合能力等值图见图3-10,其中平均综合应力为75043N/mm2,远小于材料的许用应力。
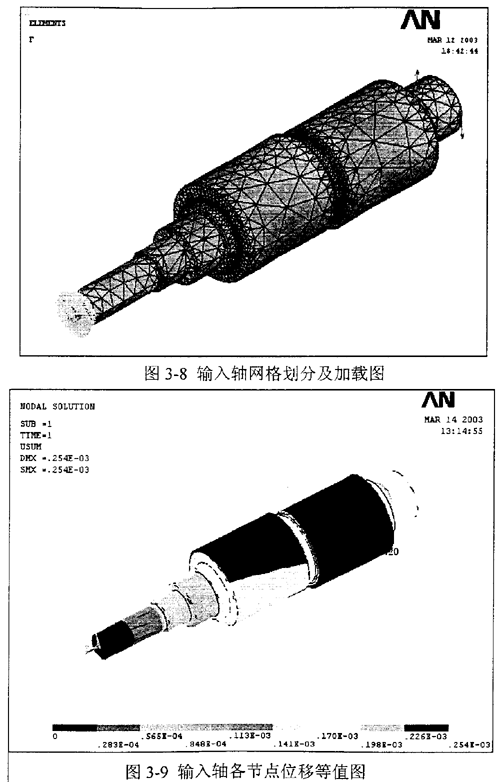
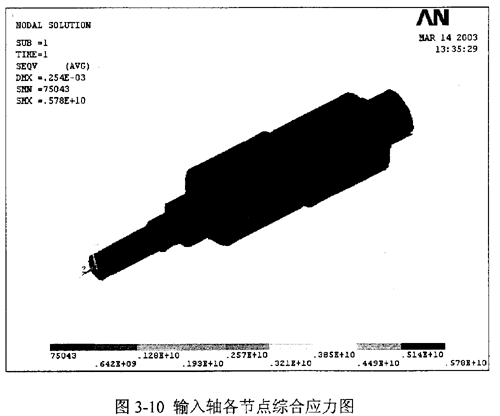
同样,输出轴划分网格并加载后见图3-11,各节点位移图和综合应力图分别见图3-12和图3-13。查询可知输出轴了大位移在节点49处,位移值为0.333mm。平均综合应力为1.5MN/mm2,远小于许用应力。
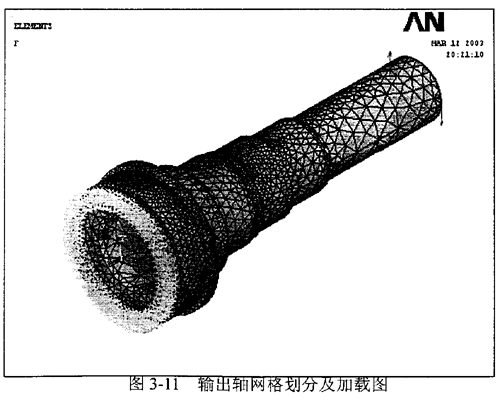
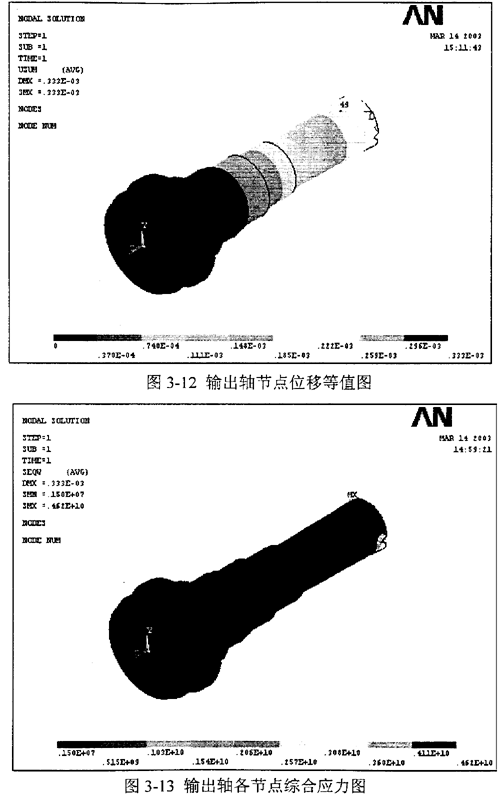
上一页
下一页
|