3.3.3 输入输出轴的有限元模态分析
在结构动力学分析中,模态分析用于确定所设计的结构或机器部件的振动特性(固有频率和振型)。由于输入轴和输出轴直接与潜油电机及螺杆泵相连,其动力学表现直接影响它们的性能及寿命,所以应对输入、输出轴进行模态分析,确定其固有频率及振型,也为谐响应分析、随机振动分析奠定基础。
模型采用IGES格式导入,拓扑修补后选择单元为solid45,指定杨氏模量为2.06×1011N/m2,密度为7800kg/m2,泊松比为0.3。采用自由网格划分,划分精度为7 。划分网格并施加约束的输入轴见图3-14。选择Block Lanczos特征值求解器,指定扩展模态数为4,频率范围为O~8000Hz。求得输入轴的前四阶固有频率为2476Hz、2493Hz、3164Hz、3193Hz,对应的振型见图3-15。
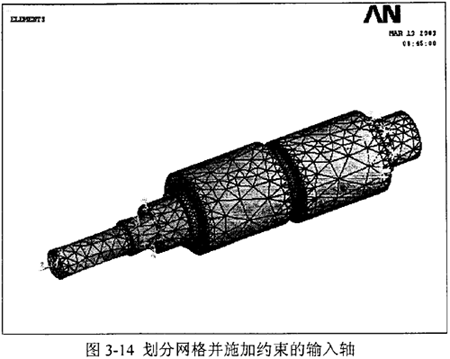
同样划分网格并施加约束的输出轴见图3-16。求得输出轴的前四阶固有频率为1584Hz、1585Hz、682lHz、6847Hz,对应的各振型见图3-17。
根据旋转轴转速与频率的关系:
n=60·f
式中n——转速,rpm;
f——频率,Hz。
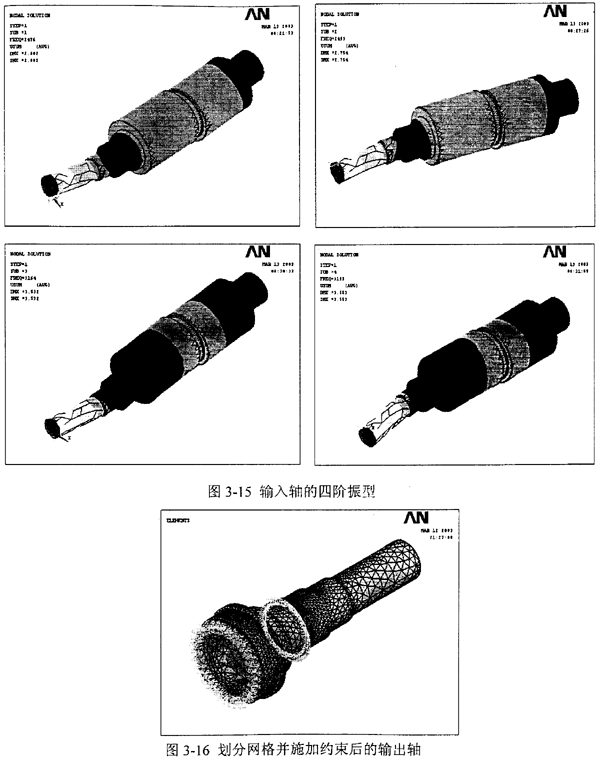
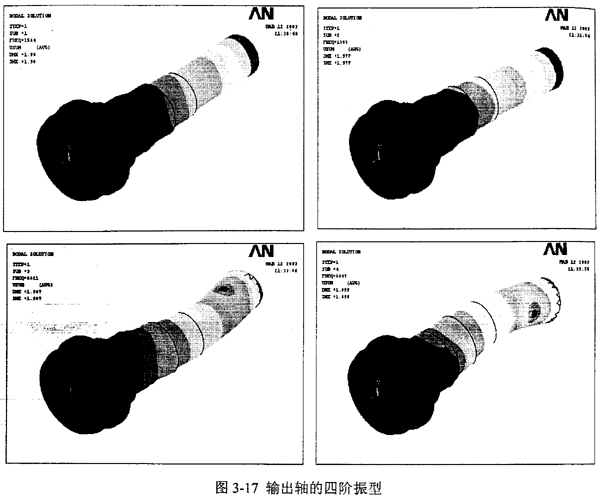
将输入、输出轴的固有频率转化为临界转速,所得结果见表3-2。
表3-2输入、输出轴的临界转速
|
输入轴 |
输出轴 |
阶次 |
1 |
2 |
3 |
4 |
1 |
2 |
3 |
4 |
转速 |
130560 |
149580 |
189840 |
191580 |
95040 |
95100 |
409260 |
410820 |
输入轴和输出轴的工作转速分别为2980rpm和330rpm,从表3-2中可以看出,两轴的工作转速均大大低于临界转速。
3.4 减速器虚拟样机仿真研究
在制造减速器样机前,根据设计参数对其进行虚拟样机的运动学仿真,目的在于检验是否存在运动干涉及验证结构设计参数的可行性。
3.4.1 虚拟样机技术简介
机械系统中的虚拟样机技术又称为机械系统动态仿真技术,是20世纪80年代随着计算机技术的发展而迅速发展起来的一项CAE技术。它可以使设计者在计算机上建立样机模型,对模型进行各种动态性能试验。从而可以简化机械产品的开发过程,缩减开发周期,减少开发费用和成本,明显提高产品质量,提高产品的系统级性能,获得最优化和创新的设计产品。
虚拟样机技术的研究对象是机械系统,它可以视为由多个相互连接、彼此能够相对运动的构件的组合。核心是利用计算机辅助分析技术进行机械系统的运动学和动力学分析,以确定系统及其各构件在任意时刻的位置、速度和加速度,同时,通过求解代数方程组确定引起系统及其各构件运动所需的作用力及其反作用力。
目前,国际上己经出现虚拟样机技术的商业软件,其中最优秀的是美国MDI公司开发的ADAMS 软件。
3.4.2 减速器虚拟样机动态仿真
在虚拟样机的运动学分析中,系统中一个或多个构件的位置或相对位置与时间的关系是规定好的,其余构件的位置、速度和加速度与时间的关系,可以通过求解位置的非线性方程组和速度、加速度的非线性方程组来确定。它主要涉及系统及其各构件的运动分析,而与引起运动的力无关。
将Pro/ENGINEER建立起来的减速器三维装配实体模型通过Mechpro接口程序导入ADAMS,对其添加约束和作用力情况见图3-18,其中:
Revolute joint:输入轴(波发生器)、输出轴与机架之间;
Fixed joint:中心轮与机架、活齿架与输出轴之间;
Rotational joint motion:输入轴Revolutejoint上;
作用力:对每个滚柱活齿添加与中心轮和波发生器的作用力和摩擦力以及与活齿架的作用力。
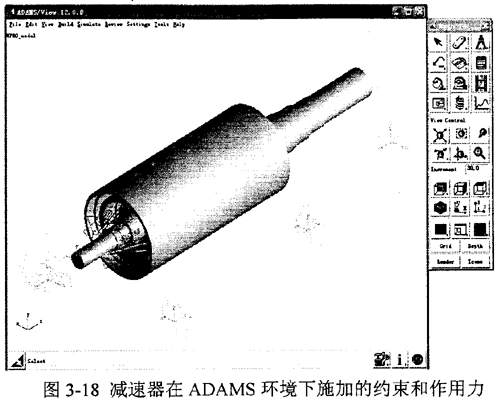
仿真开始后,ADAMS-View自动调用ADAMS-Solver进行求解,并实时地将每一帧显示在屏幕上,形成动画。仿真过程的部分关键帧见图3-19。
根据ADAMS仿真结果可知,按照前面确定的结构尺寸设计的减速器能够正常运行并实现预定的传动比,无运动干涉。
3.5 本章小结
1.首先根据减速器需要满足的几何条件、运动条件和强度条件初步确定出减速器的结构参数;
2.采用Pro/ENGINEER 建立起减速器的三维实体模型,利用有限元分析软件ANSYS对样机中的关键件进行了强度分析和模态分析。利用虚拟样机技术对设计的减速器进行运动学仿真研究,从而在静力学、运动学和动力学三方面全面验证了设计方案的可行性。
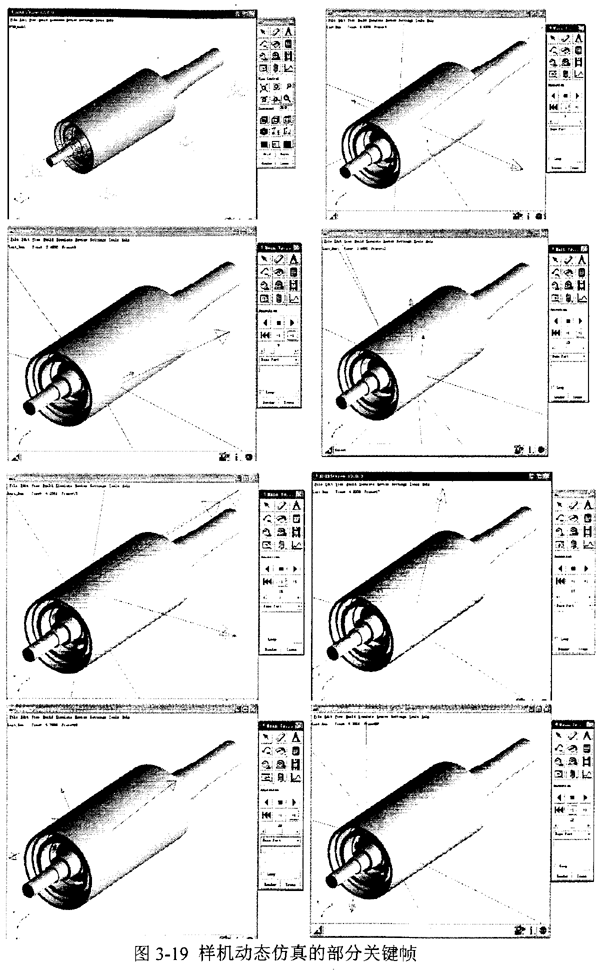
上一页
下一页
|