第4章滚柱活齿减速器扭振动力学分析
4.1 引言
随着现代科学技术的不断进步,人们对于机械设备的要求除了要满足静态设计目标外,还要具有良好的动态特性。而对并下驱动螺杆泵采油系统而言,减速器的振动不但会产生噪声、恶化传动件(活齿、轴承等)的工作条件,而且会破坏螺杆泵定子与转子之间的工作配合,降低螺杆泵使用寿命,从而影响整个采油系统工作寿命。所以对滚柱活齿减速器进行动力学分析,对于降低减速器的振动从而改善整个采油系统的动力学性能,具有重要意义。此外,目前对于滚柱活齿传动的研究还主要停留在静态设计阶段,而研究该传动形式的动态特性,给出其动态参数的一般计算方法,可以为其动态设计奠定基础,这对于改善该种传动的动态性能具有重要的理论意义。
研究传动系统的动态性能通常有两种方法,即试验法和计算法。一般情况下,试验法获得的结果比较准确,但其只适用于评定一个给定的实物或模型。而计算法通过建立动力学模型,在设计阶段就可获得系统的各种动态性能指标,并可根据分析结果改进设计或进行优化设计,从而在设计阶段就能得到具有良好动态特性的系统设计方案,因此计算法比试验法更实用、更经济,并可为同类系列产品设计计算奠定理论基础,但数学模型的建立具有一定的难度。用计算法对减速器系统进行动态分析时,其常用的数学模型有集中参数模型、连续分布模型和有限元模型三种。在这三种模型中,有限元法是一种比较成熟的方法,并有现成的商用程序软件可供用户使用,但它要求用户有相当高的分析与判断能力和丰富的实践经验。该方法建立的动力学模型虽然精度较高,但只能用来分析具体的某台减速器,如果该减速器改型或部分结构改进,则一切分析工作需要从头开始,非常费时费力。连续分布模型适用于连续质量分布的振动系统,而滚柱活齿传动的扭转振动属于有限个自由度的系统动力学问题,应该用集中参数模型描述。传递矩阵建模法是一种集中参数模型的建模方法,它主要用于研究轴类零件(机床主轴组件等)的弯曲振动和机械传动系统的扭转振动。由于该方法比较适用于传动系统的扭转振动分析,而且建模与求解合而为一,在数值求解时只涉及低阶次的传递矩阵和行列式,可以极大地节省计算工作量和计算时间,且计算结果完全可以满足工程实际的需要,因此,得到广泛的应用。
本章在分析该系统结构的基础上,拟采用适合系统扭转振动分析的以集中参数模型表示的传递矩阵法建立滚柱活齿传动的扭振动力学模型,并求解其动态参数和能量分布。并对减速器系统进行计算、分析和评价,找出其薄弱环节,为进一步提高动态特性提供理论依据。
4.2 系统扭振动力学模型的建立
滚柱活齿减速器的结构简图如图4-1所示。为了分析该减速器的动态特性,首先需要根据其结构建立动力学模型。根据各种元件动力学作用的不同,可把组成系统的各元件分成两类,即惯性元件和弹性元件。惯性元件是指各轴及轴上的旋转质量。当传动系统发生扭转振动时,它们对系统的动力学作用,主要反映在转动惯量方面,所以称之为惯性元件,一个传动系统的自由度数,一般等于惯性元件数。弹性元件是指两惯性元件之间的轴段,它可以不计质量而只考虑扭转变形,它对振动系统的作用在于本身的扭转刚度。
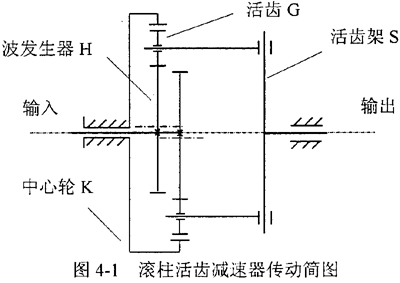
建立滚柱活齿减速器的扭振动力学模型时,将波发生器、活齿、活齿架作为只有惯性而无弹性的惯性元件。把同一轴上各惯性元件的转动惯量根据实际情况,转换到该轴的两端,形成两个等效刚性圆盘。计算两刚性圆盘之间所有轴段的扭转刚度和转动惯量,将各轴段的转动惯量迭加到该轴的两惯性元件上(一般可平均分配),各轴段的扭转刚度转换成一个弹性轴段的扭转刚度,其值应与两惯性元件之间实际轴段的扭转刚度相等。
对于图4-2a所表示的活齿与波发生器之间、活齿与中心轮之间、活齿与活齿架之间的啮合副而言,当啮合处的弹性变形不能忽略时,可以引入一个等级的弹性轴段,视为一个弹性元件,如图4-2b所示。
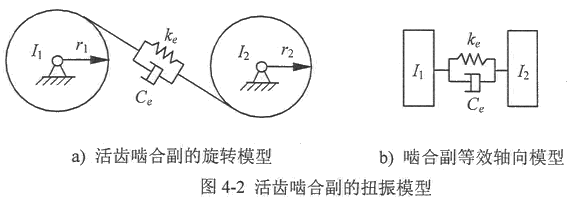
根据上述方法,可以初步建立起如图4-3所示的系统动力学模型,为了能够利用传递矩阵法对该系统进行动力学分析,需将各惯性元件和弹性元件向输入轴转换(也可向输出轴或中间任一轴转换,均不影响结果),构成单一轴线的当量圆盘系统的扭振动力学模型。转换中,按转换前后系统的动能和势能保持不变的原则,确定转换后动力学模型中各元件的参数。
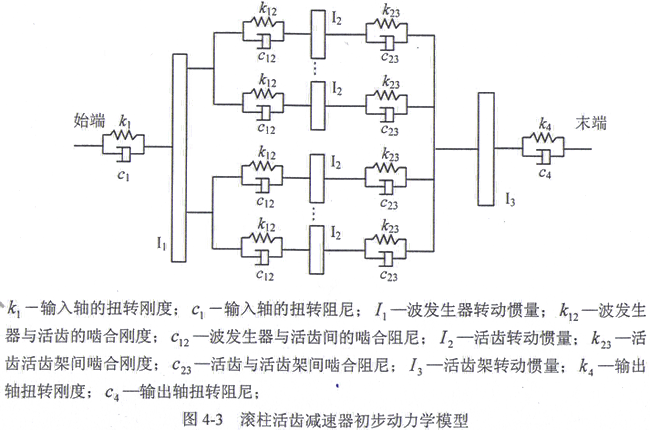
4.2.1 惯性元件等效转动惯量的确定
根据转换前后动能相等的原则,将各惯性元件的转动惯量统一向输入轴(波发生器)转换。
转换前活齿的总转动惯量为:
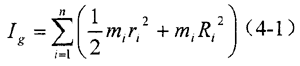
式中Ig——转换前活齿的转动惯量(kg·mm2);
mi——第i个活齿的质量(kg);
ri——第i个活齿的半径(mm);
Ri——第i个活齿中心到波发生器回转中心的距离(mm);
n——双排结构中同时参与啮合的活齿数。
向输入轴转化,根据转换前后动能相等的原则有:
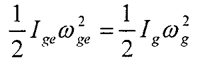
将ωge:ωg=r:R代入上式得

式中Ige——转换后n个活齿的等效转动惯量(kg·mm2);
ωge——转换后活齿的等效角速度(rad/s);
ωg——转换前活齿的角速度(rad/s);
同样,将活齿架的转动惯量向输入轴转换
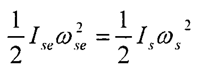
而ωse=iωs,所以
Is=i2Ise (4-3)
Ise―转换后活齿架等效转动惯量(kg·mm2)
ωse―转换后活齿架等效角速度(rad/s);
Is―转换前活齿架转动惯量(kg·mm2);
ωs―转换前活齿架角速度(rad/s)。
4.2.2 弹性元件等效扭转刚度的确定
由于弹性元件的存在而产生的刚度包括接触刚度和扭转刚度。现有文献提供的接触刚度算法一般都是线刚度,在扭振动力学分析中应将其换算成角刚度。应当指出的是,角刚度值与所选择的换算目标有关,必须明确换算的目标轴,才能保证分析结果的正确性。接触刚度转换到输入轴上的等效扭转刚度按式(4-4)进行:
k2=R2k1 (4-4)
式中R—所在圆周半径(mm);
k1—接触刚度(N/rad·mm);
k2—转换后的等效扭转刚度(N·mm/有rad)。
扭转刚度k的计算按式(4-5):

式中
G——剪切弹性模量(N/mm2);
Ip——极惯性矩(mm4);
l——轴长(mm)。
4.2.3 等效阻尼系数的确定
按照转换前、后系统的阻尼功不变的原则,对外阻尼有
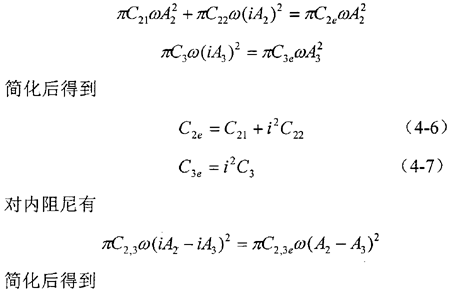
C2,3e=i2C2,3 (4-8)
在图4-3所示的动力学模型中,出现了具有并联结构的传动分支,应将其转换为等效的串联结构,以便应用传递矩阵法建模和求解。对波发生器而言,扭转刚度按式(4-9)计算。

式中ki—阶梯轴第i段扭转刚度。
支承处刚度不计,设两端均为自由端,按照上述公式将各轴上的惯量元件和弹性元件转换到输入轴上,可以得到转换后的系统扭振动力学模型如图4-4所示。
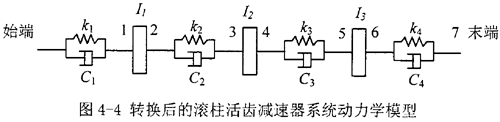
4.3 系统扭振数学模型的建立
从建立的动力学模型图4-4可以看出,该模型由惯性元件、弹性元件和阻尼元件组成,因此,只要获得了这几种元件的数学模型,就可以利用传递矩阵法建立起整个减速器系统的动力学模型。
4.3.1惯性元件的扭振数学模型
如图4-5 所示,第j个惯性元件的转动惯量为Ij,所受到的激振力矩为wj(t),旋转阻尼为Cj。元件左侧的状态矢量为转角θLj和扭矩mLj,右侧的状态矢量为转角θRj和扭矩mRj。元件动态载荷为惯性力矩Ijθ&&j和外阻尼力矩Vjθ&j。根据力平衡关系可得
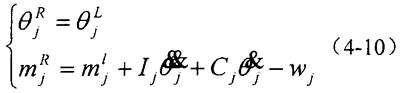
若激振力矩是频率为ω的简谐函数,即
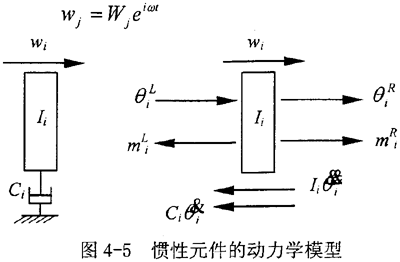
式中ω——激振频率(rad/s);
Wj——激振扭矩幅值(复常数)(N·mm)。
则作为响应的状态变量也是与激振力矩具有相同频率的简谐函数。即
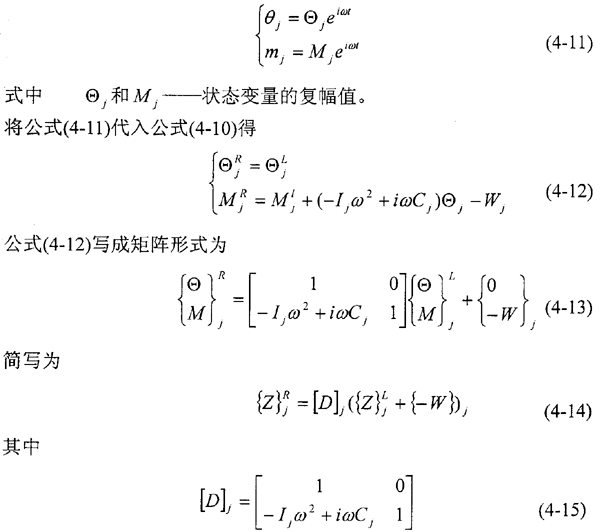
式中
[D]j——第j个惯性元件的传递矩阵;
{Z}Rj——第j个惯性元件右侧的状态矢量;
{z}jL——第j个惯性元件左侧的状态矢量。
4.3.2弹尾元件的扭振数学模型
如图4-6所示,第j个弹性元件的扭转刚度为kj,扭转阻尼为Cj,元件的左右两侧各连接一个惯性元件,左侧惯性元件的右端状态矢量等于弹性元件的左端状态矢量,即θLj=θRj-1,mjL=mj-1R。右侧惯性元件左端的状态矢量等于弹性元件右端的状态矢量,即θRj=θLj+1,mjR=mj+1L。弹性元件的内力为弹性恢复力矩kj(θRj-θLj)和阻尼力矩Cj(θ&&j-θ&j)。根据力平衡关系可得
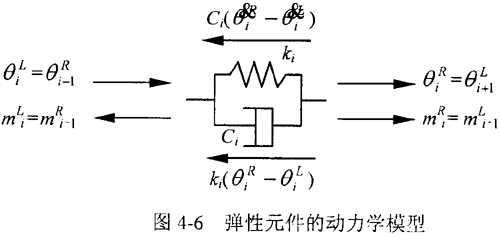
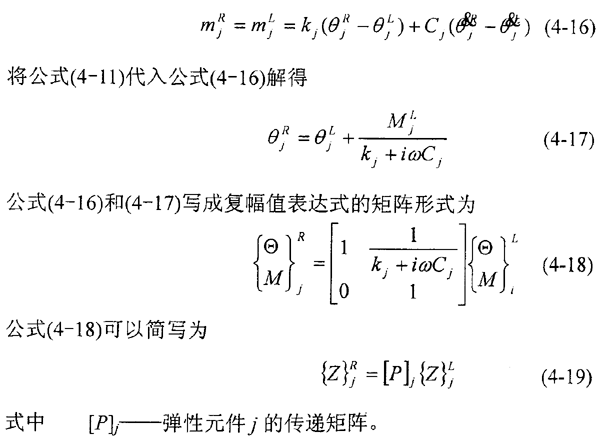
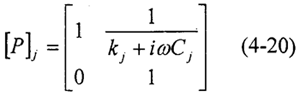
4.3.3弹性元件和惯性元件组成单元的数学模型
组合式(4-14)和(4-19),可建立第j-1个刚性圆盘右侧和第j个刚性圆盘右侧状态矢量间的关系。
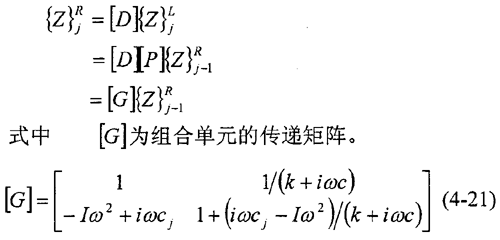
4.3.4减速器系统状态传递方程和传递矩阵
当元件数学模型建立后,尤其是得到各个元件的传递矩阵后,根据传递扭矩法就可行到整个系统的数学模型。假设整个系统共有n个元件,则根据上述原理,可以逐步计算各个元件两端的状态矢量。
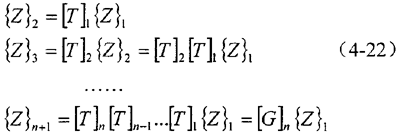
式中[T]j——弹性或者惯性元件的传递矩阵;
[G]n——n个元件传递矩阵的累积矩阵。
上一页
下一页
|