第六章 鼓形齿轮的数控加工
6.1 概述
鼓形齿联轴器工作特性的好坏与许多因素有关,但鼓形齿轮的加工质量是一个非常重要的方面。在普通滚齿机上,不经改造或加上某些特殊的工艺装备,是无法加工鼓形齿轮的。正如第一章所分析,虽然有多种鼓形齿轮的加工方法,但是最佳的方法是数控改造普通滚齿机。它具有加工精度高、生产效率高、操作方便、调整周期短、适应各种批量生产、改造成本低、经济效益高等优点,并且能够较容易地实现各种非圆弧鼓度曲线的鼓形齿轮的加工。通过滚齿机的数控改造实践,充分证明了这一技术的先进性和实用性。本章介绍数控化改造普通滚齿机加工鼓形齿轮的设计研究。
6.2 加工原理及总体设计方案
在一般机械传动中,实际应用较多的鼓形齿联轴器通常模数在10mm以下,分度圆直径在800mm以下,也就是说用中型滚齿机就能满足大部分鼓形齿轮的加工要求。本设计针对中型普通滚齿机的数控改造,以满足鼓形齿轮的加工。
普通滚齿机具有主切削运动传动链、分齿运动传动链、进给运动传动链和差动运动传动链,通过调整,能够满足圆柱齿轮和蜗轮的加工要求。本改造的内容是要使其能够满足特定鼓度曲线的鼓形齿轮的加工要求,即在鼓形齿轮一定的轴向位置有一定的径向变位,这就需要增加一个加工运动的自由度。加工原理如图6-1所示。
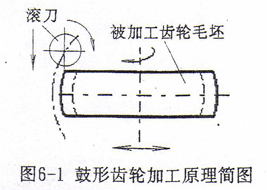
普通滚齿机的工作台是用丝杆螺母及其手动机构来实现径向进刀的,可以在其上加设驱动装置,实现刀架沿工件径向的相对运动要求。刀架的上下移动也可以用伺服机构驱动,实现刀架和工作台两轴驱动的数字控制。但是刀架有较大的自重,其驱动还要克服刀具切削力,因而需要较大的驱动力;另外,普通滚齿机的结构决定了刀架驱动数控伺服机构及减速机装置没有足够的安装空间,这将使机床的改造变得较为复杂。机床本身的刀架进给运动链设计完美,可以方便、平稳地实现进给运动。因此本设计采用工作台径向进给数控驱动、位移传感器检测刀架位移的准二轴数控方案。
系统的控制核心是计算机,目前采用较多的控制用计算机有工业控制微型计算机、Z80单板机和单片机等。工业控制微机具有强大的运算、控制功能和输入输出能力,具有非常好的抗干扰能力及很高的运动速度,并可用高级语言编程,数控程序的编程、调试方便,但是其价格较高。Z80单板机运用时间较长,价格较便宜,但它抗干扰能力较差。单片机是近年来应用较多的控制用计算机,它具有接点少、连线少、故障少、功耗小、接口简单、体积小、抗干扰能力强、性能价格比高等优点。例如,一片MCS-51系列的8031芯片相当于1片Z80CPU加上2片PIO、1片CTC和1片SIO,其指令系统也更为丰富。综合考虑性能要求及成本等因素,本设计采用MCS-51系列中,以8031为核心的单片单板机为控制系统,它既能满足加工控制的精度、速度等要求,又具有最低的硬件成本。
驱动部分设计主要考虑驱动力和驱动精度的要求。因为鼓度曲线的理论设计精度要求不高,盲目追求高的驱动精度是不必要的,本设计要求驱动精度为±0.01mm。因此采用步进电机驱动的开环控制就能满足加工精度要求。
整个系统由数控制计算机软硬件、步进电机伺服机构、位移传感器和机床四大部分组成。系统总体结构如图6-2所示。改造后的机床实物照片见附录。
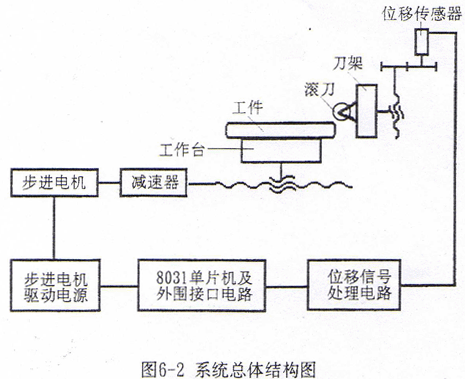
6.3 机床机械传动改造及位移传感器和步进电机伺服系统
机床的机械传动部分的改造设计与位移传感器的选用和步进电机伺服系统减速机构的减速比设计是密不可分的,以下分别论述。
6.3.1 位移传感器的选用
位移传感器根据运动的型式不同分为直线位移传感器和角度位移传感器,直线位移传感器常见的有光栅位移传感器、感应同步传感器等,它们可以直接安装在所测直线运动部件上,无传动误差影响,精度高。但是由于结构的原因,它们需要非常精确的安装基准和合适的安装空间,且通常情况下安装定位较困难。由于光栅的密封性较差,光栅材料较脆弱,所以它们的抗污染性能和抗振性能也较差,而且所需防护装置也较复杂,成本较高。角度位移传感器最常用的有光电编码器,它具有精度高,体积小,安装方便、密封性好、抗污染和抗振性能好等优点。本设计需测刀架的位移,在刀架上,切削冷却润滑油、切屑及粉尘的飞溅较严重,且不易设置防护装置。如果采用光电编码器需通过检测丝杆的角位移间接检测刀架的直线位移,但丝杆及传动机构具有的传动精度和位移检测精度是足够的。另外,加工鼓形齿轮时,形成鼓度曲线的实际切削位置通常在曲线较陡的范围,例如加工圆弧鼓度曲线,几何关系见图6-3,设位移圆半径rg=300mm,齿宽B=50mm,当Δy=0.01mm,则

可见由刀架位移的检测误差引起的鼓度曲线的误差是很小的。综合考虑诸因素,确定选用光电编码器为刀架位移传感器。
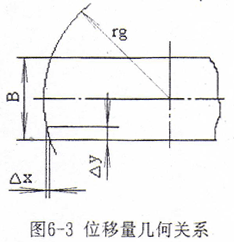
光电编码器的工作原理是利用光电效应,通过刻线盘的透光和遮光,使信号线上产生高电平和低电平,并由相位差90°的两个信号通过鉴相来判断位移方向。根据精度要求的不同,可以选择不同的刻线数,即光电编码器转一转所产生的脉冲数。
6.3.2 光电编码器至刀架丝杆的机械传动装置
由于机床的刀架进给丝杆的位置及结构关系,通常不能将光电编码器直接联接在刀架进给丝杆的端头,需将丝杆的旋转运动通过一对齿轮传至光电编码器。机械传动示意图如图6-4所示。
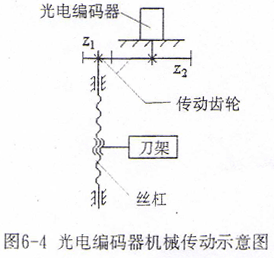
考虑安装位置的影响,要使光电编码器与机床其他零件无干涉,一般对传动齿轮有中心距的要求,以下推导丝杆导程T,光电编码器刻线数N,传动齿轮齿数z1、z2及脉冲当量δy之间的关系。设光电编码器转1转,则丝杆转过z2/z1转,刀架的位移为T·z2/z1。所以有

通常设计时需保证齿轮传动的中心距在某一范围之内,设为Amax和Amin,又设齿轮的模数为m,则应保证

将式(6-3-1)与(6-3-2)联立,则得到设计这对传动齿轮的公式

刻线数可根据光电编码器产品标准系列选取;δy的选取应根据精度要求,但其有效数应大于计算机处理的最小单位,例如计算机处理的最小单位为μm,则δy值的有效数应大于等于0.001mm。用试凑方法,就可以设计出光电编码器齿轮传动的齿数和模数,使其满足式(6-3-3)。
普通滚齿机具有刀架进给丝杆的消隙机构,因此丝杆正反转无间隙。齿轮的安装有侧隙存在,为了消除侧隙对位移检测影响,采用弹簧消隙机构,机构简图如图6-5所示。光电编码器安装在活动座上,其轴上装有齿轮2,齿轮1与刀架进给丝杆固连,活动支座在弹簧作用下绕销钉转动,压迫齿轮2与齿轮1使其无侧隙。由于光电编码器的驱动力矩非常小,因此所需的弹簧的拉力也很小,不会对光电编码的正常工作造成不良影响。
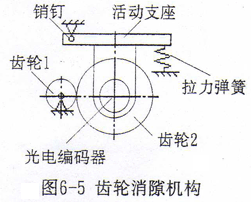
由于加工不同齿轮时,使用的夹具的高度不同,齿坯中截面的位置也不同,因此需设置高度位置标尺用以调整机械零点的位置,调定机械零点后按置零点键,用外部中断方式软件处理,使机械零点与电零点重合。
6.3.3 步进电机的选用及减速机构的减速比
步进电机种类很多,有旋转运动和直线运动的。从结构来看,它分为反应式和励磁式。励磁式又可以分为供电励磁和永磁两种。按定子数目可分为单相、两相及多相的步进电机。目前应用较多的是单段反应式步进电机[122]。
步进电机的主要参数有最大静转矩、步距角、相电流和相数等。最大静转矩是在静止状态下转子的锁定转矩,它反映步进电机驱动力的大小。步距角是步进电机每走一步所转过的角度,它反映步进电机走步的精细程度。

式中 δ——步距角
z——齿数
n——相数
k——分配方式系数
步进电机需要专门的驱动电源供电才能工作,驱动电源性能参数有最大静转矩,矩频特性等等,这里不作详述。
在选用步进电机时,最主要的参数是最大静转矩和步距角。对滚切加工而言,切削力的径向分量较小,垂直于工作台平面的切削力分量相对于工作台及被加工件的重量要小得多,而工作台径向进给驱动力的方向是平行于工作台平面的。因此,在确定工作台径向进给驱动力时,主要考虑工作台重量造成的静摩擦力。对于不同的机床,需首先测定径向进刀丝杆的驱动力矩。所选步进电机的力矩应在减速之后足以驱动工作台克服径向进给静摩擦力,即

式中TM——步进电机的最大静力矩
T——驱动工作台运动所需的驱动力矩
i——减速机构的减速比
η——传动链的机械效率
减速比的大小又是决定工作台驱动的脉冲当量的因子,因此,在确定减速比时,除考虑它对驱动力矩的影响,还要考虑对脉冲当量的影响。

式中δx——工作台径向进给驱动脉冲当量(mm)
δ——步进电机步距角(°)
t——工作台丝杆导程(mm)
i——减速机构的减速比
脉冲当量的确定,首先要满足驱动精度的要求,其次它必须是计算机处理最小单位的数值精度,否则会带来累积误差,给控制造成不必要的困难。
因此,必须综合考虑驱动力矩和脉冲当量两方面的影响,既要有足够的驱动力矩,又要满足脉冲当量的要求,即

6.4 数控计算机硬件配置
6.4.1 单片机概述[123][124]
单片机是国际上七十年代末、八十年代初发展起来的新型计算机,它广泛应用于机械设备改造、机电一体化技术、实时控制、自动检测和数据处理、仪器仪表、复杂控制等领域。Fairchild、Texas、Zilog、Motorola、Intel等计算机公司都开发了自己的机种,到85年已有50个系列373个机种。本设计采用Intel公司的MCS-51系列的高性能8位机8031作为控制核心。
6.4.2 硬件配置
数控硬件由8031、外扩一片程序存贮器芯片2764、外扩一片数据存贮器6264和外扩一片通用可编程并行输入/输出接口芯片8155、总线、片选择码电路、采用8279芯片的通用键盘显示电路和位移鉴相输入及驱动输出的接口电路组成。数控系统的现场抗干扰性能直接关系到整个系统的成败。在硬件方面,为了防止强电电网的电压尖峰和毛刺对系统的干扰,采用抗干扰能力强的工业用微机电源、超隔离变压器、片选法译码电路、光电隔离电路。
由于8031无程序存贮器,只有128字节的数据存贮器,因此扩展了8K字节的程序存贮器和8K字节的数据存贮器。8031的三个并行I/O部分用于扩展及作为总线,作为用户使用的接口不够。扩展的8155,PA口和PB口分别作为位移信号的输入和驱动信号的输出,键盘显示电路采用8279可编程的键盘显示芯片,不占CPU时间,自动完成扫描显示,编程方便,配备20个键、8位8段LED数码管。加工参数和控制命令通过键盘输入。显示器显示输入的加工参数和机床的加工状态信息,便于操作和监视加工过程。
位移信号是由光电编码器获得的相位差90°的一组脉冲信号,为了获得位移的加减数值信号,必须进行鉴相和计数。本设计采用可编程逻辑阵列芯片GAL16V8作为鉴相器,将光电编码器的脉冲信号转换成加计数或减计数脉冲信号;采用两片四位二进制计数器74LS193串接成一个八位的二进制计数器进行位移的计数。由于计数的脉冲数值范围超过256,因此必须用软件进行定时中断判断高8位的进位和借位。
加工过程还有工作台手动调整操作的要求,通常需设置三档手动速度,手动档位及自动的切换采用波段开关控制8031的并行口的位,采用软件查询口位的方法进行控制。
硬件系统总体框图及单片单板机原理图如图6-6、图6-7所示。
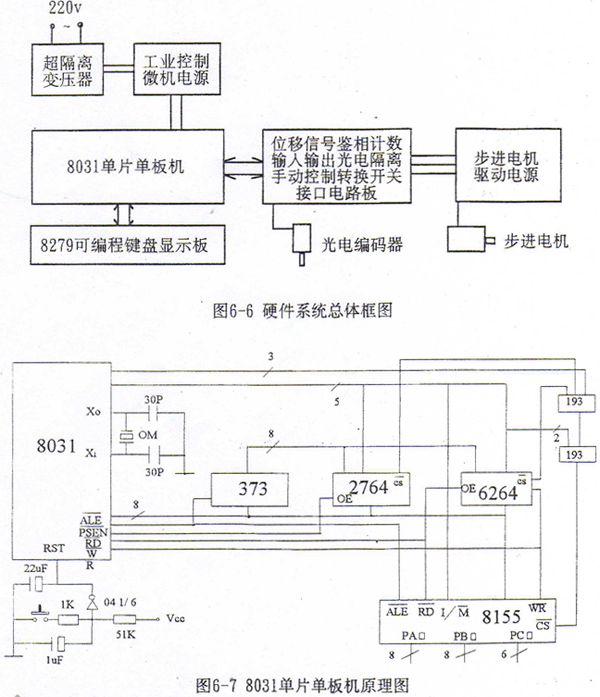
6.5 数控软件
本系统的软件采用模块化设计,主要包括系统初始化、数据输入和显示、插补运算和驱动控制、定时中断处理位移信号、自动与手动控制等功能模块。软件总体框图如图6-8所示。
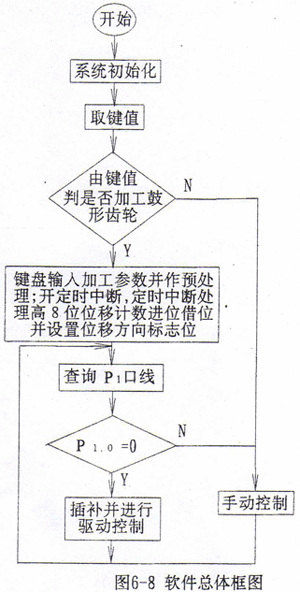
6.5.1 系统初始化
系统初始化的任务是将数据存贮器清零,设置中断向量表,确定堆栈区首地址,给定所使用的特殊功能寄存器初值和状态标志位初值,显示系统初始提示符等等。
本系统使用了一个外部中断和一个定时器溢出中断,因此,在外部中断O入口0003H放跳转指令,指向中断服务子程序的入口地址;在定时器O溢出中断入口000BH放跳转指令指向中断服务子程序。外部中断的目的是当机床调至机械零点后使机械零点与电零点重合或使手动坐标置零。定时器溢出中断的目的是定时查询位移信号的低8位,判断高8位的进位和借位并设置当前刀架运动方向的标志位和当前所处象限的标志位。
堆栈区要有足够大,否则有可能使所分配的数据存贮空间被堆栈占用或数据冲掉堆栈内容,造成系统混乱。因此,必须充分考虑堆栈空间,设置其首地址。
6.5.2 定时器中断服务子程序
为了使查询在两个位移计数脉冲之间进行,使高8位的进借位和标志得到及时处理,应根据刀架的最快速度计算两相邻位移脉冲的间隔时间,作为定时器溢出的间隔时间,由此计算出定时器的初值。设刀架的最快移动速度由机床说明书查得为vmax(mm/s);所取的脉冲当量为δy(mm),则间隔时间T=δy/vmax(s),设定时器以TMOD方式1工作,则
T=(216-T0)×机器周期
式中 T——定时时间
T0——定时器初值
8031的机器周期为2×10-6,所以
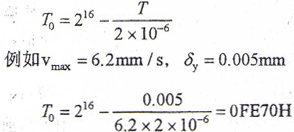
则定时器初值(TH0)=0FEH,(TL0)=70H。
位移脉冲计数的高8位的处理采用差值法,设前后两次的低8位二进制数为X1、X2,高8位二进制数为B1、B2,先求差值△=X2-X1,若△的最高位为1,则此时整个16位计数的十六进制数为B1X1+FF△;若△的最高位为0,则为B1X1+0△。相应的,若△的最高位为1时,当前刀架向Y坐标负方向运动;若△的最高位为0时,当前刀架向Y坐标正方向运动。而高8位由FFH变为00H时,当前刀架位置在Y坐标大于零;高8位由00H变为FFH时,当前刀架位置在Y坐标小于零,此时应取Y坐标补码进行插补运算。定时中断服务子程序框图见图6-9。
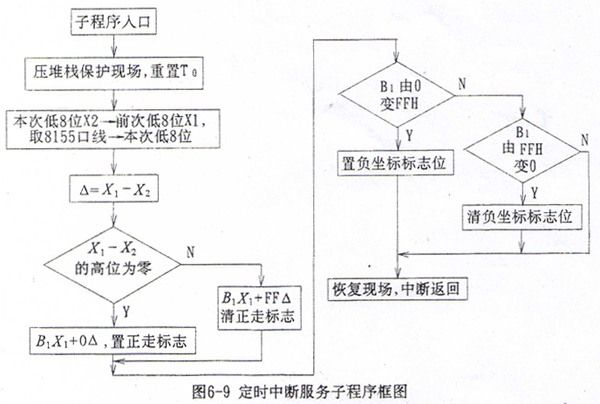
6.5.3 插补运算及驱动控制程序
输入参数时,若是加工圆弧鼓度曲线的鼓形齿轮,则输入鼓度半径值,若是其他曲线的鼓度曲线,则输入相应的参数值。当零点确定之后,其控制点的位置坐标就确定了,由于x、y坐标的脉冲当量可能不相同,因此需采用将脉冲换算成坐标进行插补运算。不同的鼓度曲线采用不同的软件插补计算公式。计算采用整型运算子程序,包括若干个多字节的加、减、乘、除运算供运算时调用。
非圆弧曲线插补运算时,首先根据当前的Y坐标值及插补曲线f(x,y)=0,求解出x坐标理论值xt,设当前的实际x坐标为xr,令误差函数F=xr-xt。对圆弧曲线,根据当前的x、y坐标,计算x2+y2值,令误差函数F=x2+y2-R2。根据当前点在不同象限、当前刀架的运动方向及误差函数的正负,共有8种情况出现(如图6-10所示),应根据它们的状态进行不同的处理。①、⑥两种情况应使当前点向x坐标负方向走步;③、⑦两种情况应使当前点向x坐标正方向走步;②、④、⑤、⑧四种情况无需在x坐标方向走步。由于在切齿过程中刀架的进给速度较低,最高一般不超过30毫米/分钟,两次y坐标计数脉冲间隔时间可达几十毫秒,而插补运算的时间不超过1毫秒,因此插补速度足够。在刀架快速运动时,插补有滞后,但此时不切削,这种滞后不影响加工。在插补过程中,显示器轮流显示当前的x、y坐标值,以利于操作者监视加工情况,因此还需进行显示BCD码的转换和轮换的控制。插补运算及驱动控制程序框图见图6-11。
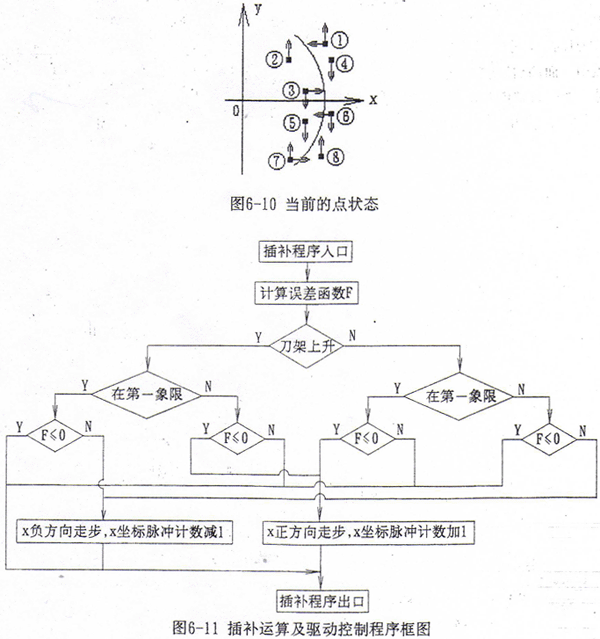
6.5.4 手动控制程序
手动控制程序采用查8031I/O口线方式进行控制。当按下手动键时,连接该键的口线为低电平,同时,由波段开关设定的某一档位连接的8031相应的I/O口线也为低电平。程序根据这两个低电平出现的I/O口的位置进行控制。手动速度的大小由两次输出驱动脉冲的时间间隔决定,延时量根据所需手动速度计算,设驱动脉冲当量为δx,手动速度为v,则延时△T=δx/v。确定手动速度的大小,一方面要有利于操作,另一方面要考虑驱动步进电机的频率不应超过所选用的步进电机允许的超动频率,若所确定的频率较高,应设计提速台阶,逐步提高驱动频率,直至达到最高速度。一般情况下,为了实现大距离快速移动和小距离刀具趋近工件进行对刀、进刀的操作,设置快速、低速和点动三档手动速度。
6.5.5 其他软件处理
工作台是由步时电机通过减速机和工作台径向进给丝杆螺母来驱动的,这中间存在着一定的传动间隙,在切齿过程中,当滚刀中心越过鼓形齿轮中截面时,要改变驱动的方向,这就需要在反向时加入一定的转角以消除反向间隙。这一综合间隙包含了丝杆螺母的间隙、减速机齿轮侧隙和轴承间隙。综合间隙的测定应在机械部件安装调整完成后进行。在切削过程中由于振动的影响,光电编码器有可能出现微小的正反转动,如果直接反应在驱动控制中,则会出现丝杆正反消除间隙的往复转动,这会导致驱动坐标的混乱。因此,必须用软件作反向延迟处理,即当反向脉冲出现若干次后才对标志位作置位或清零处理,这样就避免了因机械振动引起的驱动摆振。
为了提高系统的抗干扰能力,软件方面采取了若干措施,主要有软件环形分配、指令冗余、输入数据判别和输出多次重复。
软件环形分配是由软件根据输出转动方向要求及当前步进电机的通电状态,直接在输出口线上输出下一步的步进电机通电状态,而不用硬件环行分配器。这样就减少了硬件可能受到的干扰,使输出稳定可靠。在程序中有许多转移指令、子程序调用指令和返回指令,这些指令直接影响到程序的流程,为了确保这些指令能正常执行,避免因前面取指令的混乱给这些指令造成的误操作,通常在这些指令前面加入两个空操作NOP指令,这样就能截断取指令错误,使程序运行在正常流程,这就是指令冗余。如果输入数据口线因干扰造成的错误恰好被采入系统,就会给控制造成误操作,为了避免这一情况发生,在软件中加入了输入数据判别的程序,将口线数据若干次采入,判断是否一致,如不一致则重新采入,直至一致时才将其输入该数据的存贮单元。在输出时,重复执行若干次输出语句,可避免输出口线因干扰造成的输出错误。
6.6 系统特点
本系统较好地解决了鼓形齿轮的加工问题。改造后的机床运行稳定可靠,鼓形齿轮的加工质量得到保证,生产效率提高。
总体结构上,采用准二轴开环控制,适应了滚齿机结构特点,易于实现。对原机床的结构无大的改变,机床的机械传动装置基本不变,机械改造部分的成本较低。最大限度地利用原机床的功能,节省数控驱动的成本。系统功能满足鼓形齿轮加工要求,而且机床保持原有的所有加工功能。
数控硬件在满足系统功能要求的前提下尽可能地简单,数控装置成本低,维护方便,装置小巧,占空间少,可尽量靠近机床便于操作。
在硬件和软件两个方面采取了抗干扰措施,很好地解决了现场抗干扰的问题,即使在环境条件较差的大车间运行,系统未出现因现场干扰而引起的系统失控现象,运行稳定。
本系统无须操作者编程,只需在键盘上输入加工参数。因此对于不同的鼓形齿轮产品可以很方便地实现调整,调整周期短。更换不同的鼓形齿轮加工品种,其机床调整量主要是机床传动链的调整和被加工件的安装调整,产品批量适应性强。
系统不仅可以加工圆弧鼓度曲线的鼓形齿轮,还可加工优化鼓度曲线的鼓形齿轮,这是其他鼓形齿轮加工机床改造所不具备的。部分修改程序存储器EPROM或EEPROM内容,可方便地实现其它各种不同鼓度曲线的鼓形齿轮加工或有齿向修形齿轮的加工。
数控改造后的机床,操作简单,易于掌握。
本系统已成功地应用于Y38-1和Y3180滚齿机的数控改造。两台滚齿机的数控改造略有不同之处,Y3180滚齿机的加工范围比Y38-1滚齿机更大,传动链参数不相同,因此数控改造的结构参数及控制参数也不相同。对Y3180滚齿机的数控改造还实现了优化鼓度曲线的鼓形齿轮加工,其使用环境也较差,对抗干扰性能要求更高。用户单位反映,设备使用情况良好,已获得了一定的经济效益。验收证明见附录。
实践证明,这是一种经济有效地扩大普通滚齿机加工鼓形齿轮功能的数控改造方法,适合现阶段国内鼓形齿轮加工的要求,具有较高的推广应用价值。
上一页
下一页